Editor note: Managing cost is one of the most important priorities for garment exporters today to meet the increased pressure on global apparel prices. In its Feb. 2007 edition, StitchWorld carried a research article on how manufacturers of jeans could meet production cost at less than Rs 199 and still make a profit. We are reproducing an abridged version of the article for our Apparel Online readers in a special arrangement with StitchWorld as the issue is critical not only to the production floor, but also at the merchandise and management level. I invite the industry provide a clue on how shirts could be manufactured at Rs 99 ….any takers?
Finally Reliance made an entry into the Indian clothing arena, and that too with its usual hype, with newspaper articles flashing their proposed plan to retail Jeans at INR 199 creating a flutter and increased pressure on manufacturers. In the wake of the hype, with presumably no Indian manufacturer committing to supply at the announced price, marketing honchos have already branded this merchandise as a ‘loss leader’. Can jeans be profitably made and sold at Rs 199? Prabir Jana works out the methodology that could clinch the deal…
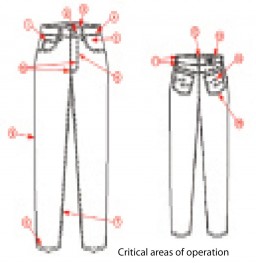
Henry Ford once said mass manufactured products should be affordable to masses. The logic holds true for cars as well as for clothing. The secret of mass manufacturing is ‘division of labour’ as the cost of manufacturing in mass production is lesser in comparison to ‘bespoke manufacturing’ -tailoring in case of apparel- primarily due to three reasons:
- Reduced work content (through repetitive and/or specialised operation, methods improvement and use of specialised machines): thus reduced labour cost.
- Savings in raw material consumption (primarily fabric savings through optimised marker layout): thus reduced raw material cost
- Scientific management (production planning and control, quality management systems, etc): optimised use of man and machine; thus more output per rupee invested in infrastructure.
If the above mentioned parameters are achieved, then there is no reason why mass manufactured goods should be costlier than tailored goods. Even though the retail price of fashion merchandise is nearly three times the manufacturing cost, in domestic retail 20% – 30% add-on to factory cost (sourcing cost) is common for commodity merchandise like jeans. Thus manufacturing jeans at Rs 150 – 160 ex-factory is what anyone should target for. While this article does not prescribe a recipe to make jeans at Rs 150, it reviews the manufacturing process, pinpoints possible areas of improvement and raises hope for manufacturers that, with scientific control of man, machine and material, one organisation may be able to profitably manufacture jeans at Rs 150.
There are three angles to savings: savings in raw material, reduced work content and better asset management. With success on these fronts, INR 199 is definitely achievable
There are three angles to savings: Savings in raw material, reduced work content and better asset management. With success on these fronts, INR 199 is definitely achievable.
Savings in raw material
In raw material savings there are again different angles; firstly, reducing consumption of fabric per jeans at a given cost and secondly, reducing the cost of the denim fabric itself. According to experts, typical marker efficiency for a five-pocket jeans can be anywhere between 88-92% depending upon the shape of jeans; skinny jeans have better efficiency, more belt loops can add to this. Average consumption of jeans was calculated at 1.3 metres apiece, whereas 1.15 to 1.18 metre consumption is common among domestic regional branded manufacturers, where 2-3 way markers are generally made. Depending on size ranges, marker combinations and fabric widths, it can be decreased further. Accounting for 3-5% waste due to end bits, total consumption can be pegged at 1.2 metre per piece.
Currently there are only one-length jeans available in retail, inseam of 34 inches. Obviously that’s the longest length sold. Generally, the extra length is trimmed and folded at the retail cash point. That trimmed length at the cash point is ‘value-added loss’ of raw material, the saving of which can reduce the crucial consumption of fabric. With more and more customer data available with retailers now, can we not offer multiple inseams for jeans? Additional savings will definitely accrue then. Denim fabrics are generally manufactured in air jet looms and 62” (58-60” working) width is common. Experts feel that, with bulk orders, fabric cost for 60” denim can be brought down to INR 55-60. If the above is implemented, we have untapped fabric savings potential up to 5-7%.
We need to assume that the working day will be 8 hrs, or 480 minutes long. Granting the worker a little ‘ time out’, it would be quite acceptable that a conscientious worker will spend 450-460 minutes at his post.
Depending on the level of automation being used the work content for a five pocket basic jeans varies from 20 standard minutes to 11 standard minutes! A reliable source confirms Levi’s most automated plant in Belgium used to make jeans at 9 standard minutes! Most of the sewing operations in jeans can be automated to a large extent, thanks to dimensionally stable and stiff denim fabric.
While the manual and semi-automatic machines require 1:1 machine to operator ratio, the automats like decorative stitch to hip pocket, hip pocket attach, etc. can work with 2:1 machine to operator ratio. In sequential cycle sewing workstations like hip pocket crease and hip pocket attach, a single operator can operate both the workstations proficiently in sequence, thus boosting labour productivity also.
It should be kept in mind that, apart from using workstations, there is another way productivity can be increased- by complete re-engineering of the operation from batch processing (conventional method) to continuous processing. For example, in batch processing, zip attach to right and left fly will take approx. half a minute thus producing, at the end of the working cycle, around 900-950 flys. In this method, zippers are pre-cut and stopper/slider attached. Alternately if we attach zipper from continuous roll to separate fly and then cut and attach stopper and slider we can improve productivity considerably.
Scientific management
How do you keep your cost down to the minimum? What is the running cost per machine per shift of eight hours? How many jeans you need to produce per shift? A highly automated plant can sew jeans in 9 to 11 minutes, but most importantly, you have to run such plants to full capacity to manufacture jeans at least cost. The question is, at what rate in terms of minutes and at what capacity? An 11-minute jean can peak at 40 pieces per machine per shift of 8 hours at 90% efficiency in the utilisation of the sewing line.
Cost heads | Existing Price in INR | New Price in INR |
Cost of fabric (1.3 mtr @ INR 70) | 91 | 80 |
Tailoring charges | 30 | 20 |
Trims (Zipper, thread, rivet, labels, etc.) | 25-30 | 25 |
Rinse wash | 10-12 | 10-12 |
Cost of Retail | +30% | +10% |
Manufacturer’s margin | +10% | |
Final cost of manufacturing | = 240 | = 150 |
The daily (shift of 8 hours) operating cost for some of the better-organised factories in India in a multi-style environment is around Rs 800-1000 per machine. [In highly automated factories, sewing machines to operator ratio is less, as operators can now handle more than one automat. The general manpower and merchandising cost also goes down due to less co-ordination required. On the other hand, capital expenses increase due to the high cost of automats]. At a conservative estimate we can take the figure of Rs 800. If the running cost per machine per shift of eight hours is Rs 800 then Rs 20 (800/40=20) is the CM (cut make) cost per jeans. The cost break up for a five pocket jeans as published in the newspaper and the newly worked out rates are:
Assuming the washing and trims cost remains the same, we can recalculate to arrive at a manufacturing cost of Rs 150 per jeans. We have discussed about only labour cost reduction in sewing; it must not be forgotten that the scope of savings in large-scale production is aplenty in the pre-sewing section also. For example while spreading denim for 5 metre length of lay, the use of an automatic spreader can increase speed by six times over manual spreading. On an average, CAM is twice as fast as manual cutting. All theses savings brings down the running cost per machine per shift further.
All the suggested cost effective methods may not be as easily implemented as written, but they are certainly feasible and the industry can work towards achieving the benchmark created for greater productivity and better profits.