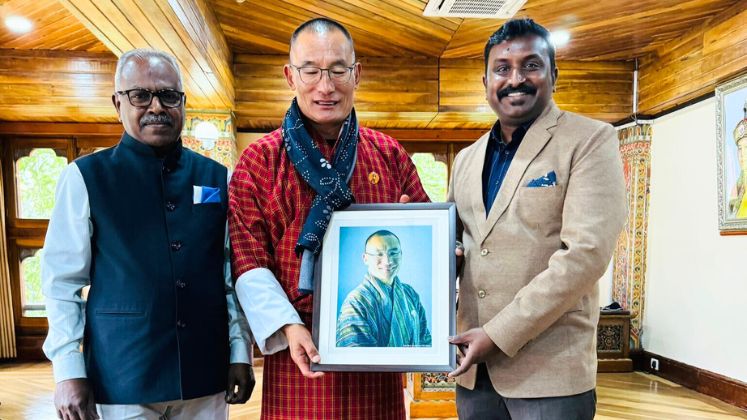
Shree Renga Polymers came into limelight in 2023 when Prime Minister Narendra Modi wore a Blue Sadri Jacket made of material recycled from PET bottles in the Parliament, which instantly became viral. The jacket was produced by Ecoline Clothing, a sustainable fashion brand of Shree Renga Polymers, a frontrunner in pet bottle recycling and sustainable textiles in India.
“Daily, we produce up to 25 tonnes of fibre involving recycling of over 30 tonnes of plastic PET bottle waste,” said Senthil Sankar, Owner, Shree Renga Polymers. Based in Karur, Tamil Nadu, the company has an annual turnover of Rs. 100-110 crore and specialises in dope-dyed colours and specialty recycled polyester fibres.
Senthil shared that since the company’s founding in 2008 by his father K. Sankar, they have developed more than 50 colours in a short span of time and have capabilities to produce flame retardant, anti-microbial, trilobal and hollow fibres. “Our Unique Selling Proposition is the ability to manufacture colourants and masterbatches in-house for the dope dyed processing. We have the unmatched ability to match the precise colour requirements of our customers,” he added. Driven by his passion for polymer products and green field projects, K. Sankar pursued Post Graduate studies in Polymer Technology at the Indian Institute of Technology, New Delhi. Over the years, he gained extensive hands-on experience in a wide array of polymer products, including PET fibres, FRP products, synthetic marble, plastic components for white goods and textiles, nylon compounds and PET engineering plastics. Senthil Sankar, his son, joined the family business in 2011 after leaving his position at Tata Consultancy Services, where he worked for three years. Today, Senthil is a successful entrepreneur, industrialist and angel investor, with over 14 years of industry experience.
In an exclusive chat with Apparel Resources, Senthil reveals why going green doesn’t have to break the bank and walks us through his innovative business process.
AR: How do you turn discarded PET bottles into valuable products while championing both social responsibility and environmental sustainability?
SS: We have nearly 20,000 ragpickers across Tamil Nadu, Kerala, Pondicherry, Andhra Pradesh and Karnataka involved in this effort. These ragpickers collect PET bottles from trash, events, hotels, restaurants and other places. Our suppliers purchase these bottles from the ragpickers and crush them at high speed to form flakes. These flakes then go through a detailed 10-step process to produce clear, premium-quality PET flakes. The recycled polyester fibres that we produce using pet bottles are used as the primary component in producing recycled yarns. The fibres are subject to Ring Spinning Process to convert them into yarns. This activity involves exclusive machines where the fibres are oriented, carded and finally spun into yarns. Being dope-dyed in the previous phase of production, the yarns eliminate the process of separate dyeing at this juncture.
The Recycled Polyester Yarns we produce are of types including 4s, 6s, 10s, 16s, 20s, 24s, 30s, 36s, 40s, etc. These have various applications in making polyester, blended fabrics, knitting, shawls, woollen materials, etc.
AR: How do you make sustainability affordable without compromising on quality or raising costs?
SS: We keep our products priced very reasonably because we handle everything in-house—from recycling the bottles to creating the final brand. Unlike larger brands that source fabrics from others and add their own margins, we’ve mastered the art of producing affordable, sustainable fabrics.
We have proved that sustainability is possible without the high price tag, but achieving this requires robust technology and expertise, which we’ve got. Not all entrepreneurs can pull this off easily, but with the right approach, it’s possible. As demand for sustainable products grows, prices will naturally drop due to increased volume.
AR: As a champion of sustainability, what initiatives have you implemented to support this cause?
SS: The process of producing polyester from PET bottles is in itself sustainable. Unlike the traditional method using virgin materials like Purified Terephthalic Acid and MEG (Monoethylene Glycol) — which releases harmful CO2 emissions—our process is eco-friendly. By recycling PET bottles, we create a durable polyester fabric with a higher intrinsic viscosity, reducing environmental impact.
In addition, we perform a Life Cycle Assessment (LCA) to compare the carbon emissions of producing virgin polyester versus recycled polyester. From our analysis, we’ve found that every T-shirt we sell helps save about 4 kg of CO2 from being emitted into the atmosphere compared to making it from virgin polyester. Similarly, each ‘MODI’ jacket we produce saves over 8 kg of CO2. We are also proud to be part of the Siachen project, where we transform PET bottle waste from the Siachen Glacier into sustainable Sadri jackets. The proceeds from this initiative support the local Ladakhi tribes for their upliftment and development. This innovative idea came from an Army Brigadier who wanted to tackle waste management creatively and we teamed up to make it happen.
The army handles the crushing of these bottles in Ladakh and then sends the flakes to us. We recycle these flakes into jackets and send them back to Ladakh.
Since launching our D2C sustainable brand, Ecoline Clothing, in 2021, we are offering a wide range of contemporary designs for men, women and kids, including casualwear, sportswear, nightwear, winterwear and coats. We’re also doing well in the corporate segment by offering customised, sustainable corporatewear and we provide CO2 and water savings certificates to our clients.
We’re also certified by GRS, TUV SUD, OEKO-TEX, Ocean Bound Plastic and ZED.
AR: What exciting new innovations have you been working on lately?
SS: Innovation drives us and we’re constantly pushing the envelope. Every month, we hold ‘Innovation Meet-ups’ where we dive into new ideas and strategies to keep our brand leading the way. We’re not just about keeping up; we’re about breaking new ground.
Take, for example, our latest projects: we’ve started turning PET bottle caps and rings into vegetable trays—stuff that would otherwise go to waste. We’re also creating bricks from sludge discarded by our Effluent Treatment Plant, mixing it with mud, paper and special construction materials. We’re recycling ash from our wood fire boiler and using recycled water from our plant to make these bricks even more sustainable. On top of that, we’re diving into biodegradable polyester and experimenting with plant-based and bacteria-based dyeing for our organic cotton products. We’re all about finding new ways to make our processes greener and more efficient.
We have nearly 20,000 ragpickers across Tamil Nadu, Kerala, Pondicherry, Andhra Pradesh and Karnataka involved in this effort. These ragpickers collect PET bottles from trash, events, hotels, restaurants and other places.