Have you ever wondered why the sewing machine is positioned on a table that is 21” X 42”? The answer is, probably, that the sewing machine factories had a consultant who suggested it. But do the factories realize the importance of right size and inclination of the table. Team StitchWorld along with inputs from Peter Pinder Browne discusses how a sewing table can be re-engineered into a more effective workplace.
The earlier article by Peter Pinder Browne titled “Material Movement-from Central Table to Bundle Trolley” in the StitchWorld June 2009 issue discussed how a transport table is an obstacle to effective workplace organization whereas Bundle trolleys are a better alternative to the central table as they provide ease of operation, workplace engineering options and many more advantages. It need not be emphasized that we require to convert a sewing table into a sewing workstation with the help of work aids and disposal equipments to make it more productive and efficient.
The shape and size of worktable plays an important role in workplace engineering. Even though more than 95% of the sewing machines used in factories are rectangular in shape and of standard size of 42” X 21”, there have been instances of lockstitch and overlock sewing machines being of 47” X 22” and 54” X 28” dimensions. As a usual practice, the motor is suspended under the table and has its gravitational centre within the four legs of the table, leaving just enough space for the machine head to be inserted and have about 8” distance from the front edge to the needle. Many factories accept this situation as unchangeable and normal.
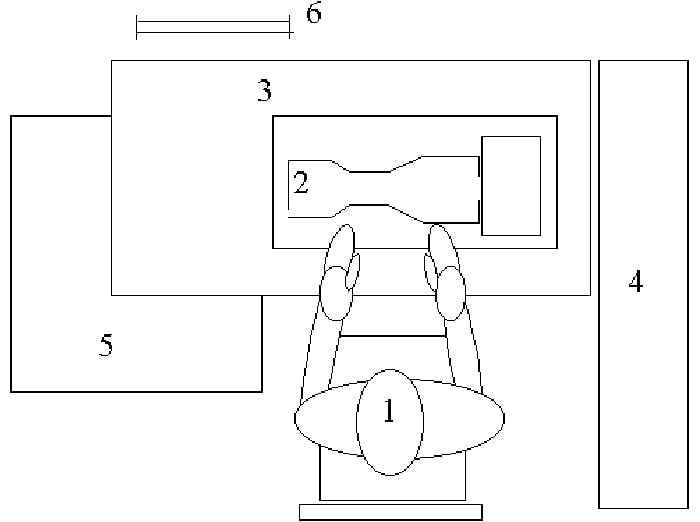
1. Denotes the Operator (hand position, height) and the Operator’s seat (height, width, back rest, width).
2. Denotes the machine type (folder position, knee lift position, needle positioning).
3. Denotes the machine bed (flat, submerged, raised, width, length, surface).
4. Denotes the centre bench (material pick-up position, distance from operator).
5. Denotes work aid provided (extensions, carousels, trolleys, clamp, stands, trays, etc).
6. Denotes disposal equipments (stackers, stands, bins).
On the contrary the 8” distance in front of needle is too short for efficient production. This space may be increased to 12” to allow the garment parts to be positioned effectively and allow longer bursts of sewing at one time. The space in front of the needle is also used to prepare and position the parts to be joined. The 12” limitation is because of the bobbin changing; it becomes very difficult for the seamstress if the table is too wide.
However, there is no standard convention that 12” space should be in front of needle. It can vary from product to product and should be directly co-related to length of seam sewn in a single burst. Suppose the sewn product is a bed sheet then we can have larger extension in front of needle but care should be taken that paddle is also moved as per extensions made on sewing table. Similarly the space required at the left of needle varies as per product being sewn. In some cases the sewing machine can be aligned at angle to the edge of table at certain degree to facilitate the operator in sewing faster especially when there are large straight seam lengths involved.
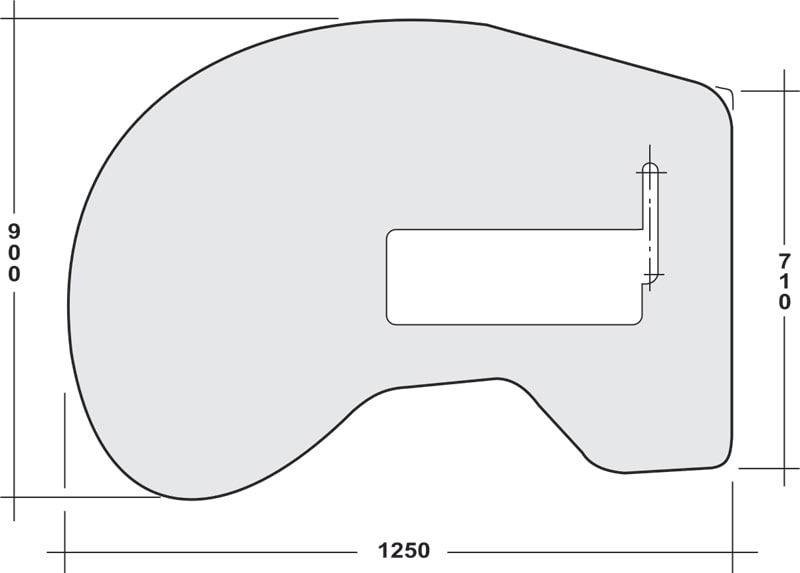
Handling Large Garments
A lot of space is required on the left in the workplace that requires lot of handling space to support a large garment. For example attaching sleeves to men’s jackets and coats using trolleys as means of transport.
When working on an overlock machine, this distance can be increased to up to 15”. The wider the table, the less the tendencies to have the garment fall off the table at the start of the seam.
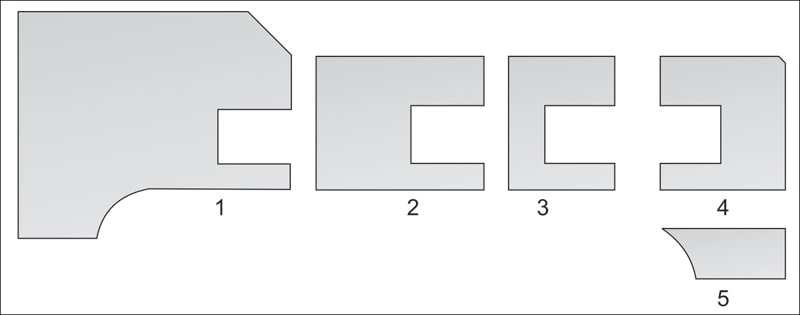
Table-tops – Shapes
There are a multitude of different shapes that could be thought out and implemented.
In the figure below, Table-top #4 is the basic part that remains fixed to the workplace, while #1-2-3 and #5 are interchangeable. The advantages, especially in fashionable exclusive lady’s wear are high. When the quantities increase, we can use fixed table-tops that have been designed for the standard operation, to great advantage.
The distance to the left of the needle is normally about 18”, which may be sufficient for some garments, such as pants and children’s clothing, but when sewing jackets and shirts, an additional 10” is an advantage, but this process also has its drawbacks. The increase in the work area increases the total space requirements of a factory. Whereas the front extension is more acceptable as it requires no additional space as the operator’s chair is not moved, he/she just has to sit a little closer to the table.
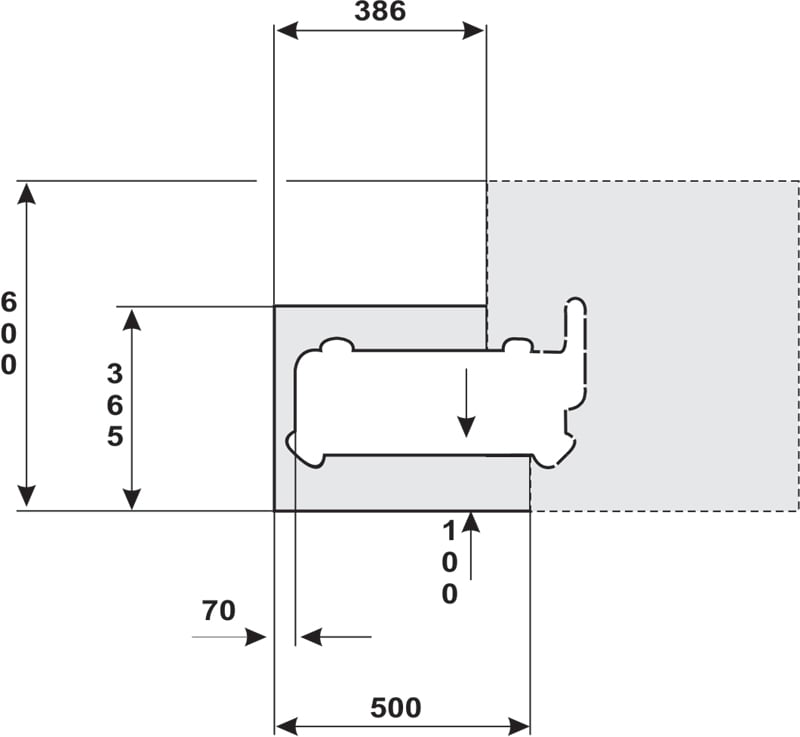
Workplace for Hemming Operations in Modular System
The figure below shows a raised, shortened table, where skirt or blouse hems are sewn in an overhead hanging material handling system. It is important to have the edges on the left hand side of the shortened table rounded to avoid pieces from getting jammed and damaged while passing.
The modular system can normally be recommended if the machine head is required intermittently at different operations. The difference between the modular, flexible system and the fixed tables lies in the requirements of the factory and the production quantities. The fixed system requires continuity without constant changes in the operation.
The product to be sewn should ideally determine the size of the machine table. Sewing small parts requires table of standard dimension, i.e. 1’9” plus 4” in front of the needle. Whereas, when sewing jackets or overcoats, then the table should be extended to the left by 8” and behind the needle by another 4”. On the other hand, in production units using a hanging system, the tables are far too large on the left and should be reduced to a maximum of about 10”.
The table height is important when using a hanging system. The standard height of sewing table is around 30 inches. But the height of table should be adjustable as per height of the operator. While increasing or decreasing the height of the table, the height of paddle and the height of chair should be taken into consideration. In most cases the height must be set to 3’ so that the waterfall principle can be used without the parts falling onto the floor. The machines are generally adjustable in height, but when used in the fixed transport table system, the height is dictated by the height of the transport table.
In Europe, some factories have their machine tables tilted. The tilt allows the larger pieces to be drawn away to the back by gravity, a better solution is to use air-jets set into the table top, to do the same job, but with more effect as one can direct the garments to the side as well as forwards but still require the 12” in front of the needle.
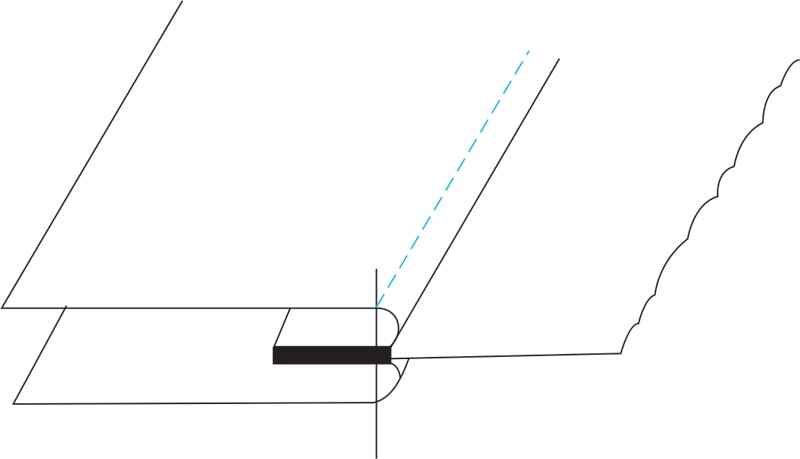
Workplace Engineering
Methods are dependent on the degree of investment in a workstation. Generally, it is expected that more automated and sophisticated a workstation is, simpler is the sewing method. This may not always be the case as we continuously seek new and better methods either for operation simplicity, with more work-aid, or befitting a highly skilled operator.
To attach yokes to shirt back with single needle machine, there could be a better and re-engineered workplace design.
Figure 2 shows what an optimized workstation could look after reorganization. The basis is the seam which is a necessary part of the construction (Figure 1).
The emphasis while designing such a workplace is on the optimal space/area utilization, assuming that maximum quantity of shirts is getting produced to warrant the investment.
The sewing table initially used to be 10 degree tilted towards front or back to facilitate smooth flow of garments being sewn. But garment manufacturers did not use it optimally; therefore these surfaces were done away with. A sewing table tilted at 10° to 25° towards the operator, improves visibility of the task and helps to keep the neck in a more upright position. Ensure that the table top is very smooth for consistent flow of fabric.
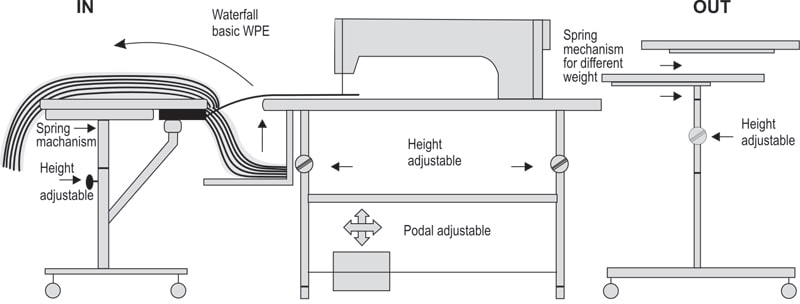
How the system works?
To the left of the operator, we find a height adjustable pickup shelf with a clamping mechanism. The pickup and disposal follow the waterfall principles, in this particular case from top to bottom. (The disposal direction is indicated by the curved arrow.) The pickup shelf can be spring controlled so that a fully trained operator can pick up from the same spot without looking, as the height is automatically adjusted by the weight. The same applies to the pickup shelf on the right side where the yokes are stored. The shelf under the left side of the machine table should also be adjustable in height. By doing this we can cater for various thicknesses and weights of cloth. When compared to simple solutions for the same operation in the industry, we can save up to 30%. If the previous method was attach, turn and topstitch, then the savings are nearer 50%.
Work aids help improve productivity
While there is a lot of emphasis on sewing, loading and unloading consumes maximum time and labour. Stackers are used to organize and make the unloading activity efficient whereas clamps predominantly used for loading. Some of the stackers and clamps that are commonly used are small part stacker, large part stacker, flip stacker, multi position rotary stacker, bundle clamps, etc. Some of these work aids have been able to cut down the operator fatigue level, measured by distance moved up to 18%. These work aids have proven to be widely used throughout the industry effecting savings in material handling reduction and minimum operator displacement. There are no work aids which fit well under all conditions. They need to be engineered to suit the purpose.
With the prevalent practices in a factory, one just needs to ask few basic questions about workplace design – height, length, width and shape of worktable and position the pieces such that they fit into the workstation without any strenuous motion by the operators, and the productivity is sure to increase.
How sewing table-tops can be made more efficient?
- The table should be rounded from all sides to prevent any damages or tearing of fabric.
- The surface should be non slippery.
- The surface can have matt/velvet finish.
- The matt finish helps to prevent scratches on surface and provides optimum grip to the fabric while stitching.
- Nowadays the table- top surfaces are post form laminated till the bottom to ensure smooth and scratch free surface.
- To keep the fabric to pass over easily sewing table Air Floatation Techniques can be used.
- The sewing table surface should be heavy to ensure that vibrations from motor are not transferred to the machine while stitching.