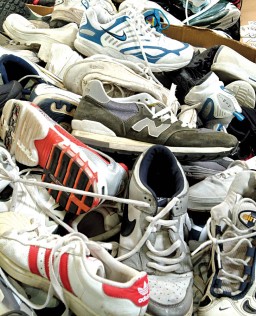
As more and more people across the world take to a healthy lifestyle the market for athletic shoes is on the increase, more so as the segment which was earlier just about sports now has a growing segment of ‘active’ and ‘fashion’ wearers. In fact, according to NPD, in the $ 19.4 billion athletic footwear market, running shoes is the largest selling category with $ 4.9 billion, closely followed by low-performance footwear designed for fashion and comfort at $ 4.8 billion.
In the year 2007-08, India exported an estimated $ 900 million worth of footwear to Europe, where UK was the top market with export of $ 215 million, followed by Germany with $ 205 million worth of exports. Surprisingly, USA comes much down in the list with India exporting $ 162 million worth of leather shoes, and the balance $ 148 million worth of exports going to the rest of the world. (Source: CLE & US Customs).
As per the Indian Footwear Components Manufacturer’s Association (IFCOMA), India has a large untapped domestic market with consumption presently estimated to be over 100 million pairs. Interestingly, the estimated production capacities indicate a larger share for the non-leather footwear (1056 million pairs) in comparison to leather footwear (909 million pairs). Though India has traditional footwear industry centered in Tamil Nadu, Agra, Kanpur and Delhi, it is only recently that international brands have started using the country as a manufacturing base for athletic shoes.
Footwear giants Nike, adidas, Puma, Reebok, Fila and New Balance are using India as a production centre through outsourcing contracts with domestic companies such as Lakhani Arman Group and M&B Footwear. Besides these athletic brands, international shoemakers like Florsheim, Clarks, Salamander and St. Micheal’s for formal leather shoes, and domestic players like Bata, Liberty, Mirza, and Woodland also have major presence in footwear market.
[bleft]The role of technical textiles is fast becoming more acceptable. The choice of fabrics for the uppers is many depending on their functionality. The fibres chosen are mostly polyester or polyamide. Laminated foils are being used to keep water out[/bleft]
The athletic segment in shoes is dominated by innovations for greater comfort, performance and look. Research has reached a stage where efforts are on to transform footwear into a dynamic and active foot-device capable of adapting to the users environmental conditions for better foot health. Adidas alone spends up to $ 100 million in sports shoe research every year. The fast growing global footwear market supports the magnitude of research going into athletic footwear. Estimated footwear industry worldwide by 2010 is pegged at US $ 192.4 billion with a projected consumption of 13.9 billion pairs of shoes. While China exports close to a billion pairs a year, India exports just 100 million pairs annually.
Sport shoes offer a multitude of choices to a manufacturer to experiment with fabrics. An ‘upper’ made of improved water-repellent rip-stop soft shell material, perforated foam; breathable… the options are many. In fact, any kind of woven fabric could be used as outer shell if it is strong enough to resist abrasion and tearing forces. Thus whereas, for the outer shell, flat fabrics with linen weave or twill are most popular, for trimming, fake furs and plush make an interesting choice. The lining is popularly of woven or knitted fabrics, which are sleek in the case of sport shoes. Some manufacturers also use terry type fabrics for the rim of the ankle.
But the role of technical textiles is fast becoming more acceptable. In technical textiles, choice of fabrics for the uppers is many depending on their functionality. The fibres for the textile materials are mostly polyester or polyamide. Laminated foils are being used to keep water out. Next to the classic brands like Gore Tex, USA and Sympatex, Germany, which launched its PUR (polyurethane) membrane in 2007, there are many other products available, which allow moisture transportation from inside out and prevent wetness to come in from outside. A new development is a fully recyclable membrane with Oeko Tex-Standard 100 certificate.
Today, outer fabrics made of spacer warp knits are in fashion and used for airy summer sport shoes. These warp knit spacer fabrics are known for their thickness, which varies from 2 to 16 mm. The top surface often shows an open wafer structure while the inner surface is neat and plain with the ability to decompress. These fabrics give a rather bulky look to the shoes.
Indian production capabilities in footwear has seen impetus with many new projects involving international players and dedicated SEZs. IndKunz Shoe Last Development (India) Pvt. Ltd., a wholly owned subsidiary of Formas Kunz, Brazil, is setting up a shoe last manufacturing unit at Irrungattukottai, about 40 km west of Chennai for the domestic and export markets.
Apache Footwear Ltd., a China-based company and the largest manufacturer of adidas shoes worldwide, last year signed an agreement with the Andhra Pradesh Government to set up a manufacturing facility on a 314-acre site, which has been accorded SEZ status. The company, which has since then begun manufacturing has said it plans to eventually manufacture one million pairs of shoes at the facility.
According to the Asia Footwear Association, rising costs have forced 15% of shoe manufacturers in Guangdong province of South China to shut down or relocate in the past year. The development of three exclusive footwear SEZs – Apache SEZ Development India Pvt. Ltd. (Andhra Pradesh), Cheyyar SEZ (Thiruvannamalai, Tamil Nadu) and State Industrial Promotion Corp. of Tamil Nadu (Sriperumbudur) at a time when the Chinese shoe industry might actually be showing a slowdown is exciting news for the Indian industry, providing a new opportunity for growth.