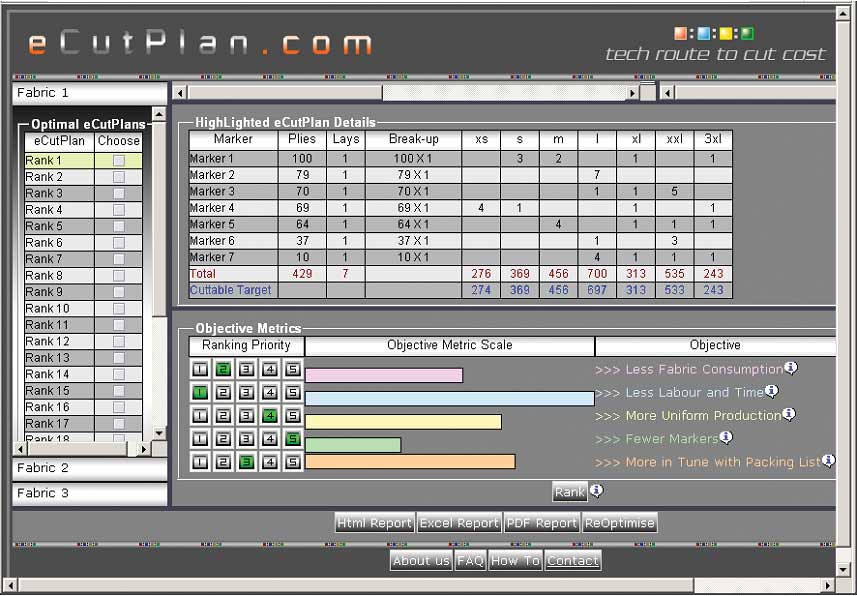
One of the most crucial activities that takes place in cutting room is Cut Order Plan. This activity is also termed as ‘lay plan’, ‘cut plan’, ‘lay lot plan’, etc. Cut Order Plan is basically optimizing the cutting process under certain constraints by following certain parameters.
Marker efficiency, a subset of Cut Order Planning, is much hyped, as it is easily quantifiable in terms of percentage of fabric consumption. There are many facets to Cut Order Planning, reducing fabric consumption being just one of them. It demands mathematical optimisation of competing objectives.
The web-service www.eCutPlan.com for Cut Order Planning developed by Tanya Geometrik Pvt. Ltd. simultaneously maximises meeting these objectives. Prabir Jana, Professor NIFT, assesses this solution.
Cut Order Plan is a very crucial activity. Which sizes to combine and row much to cut are really very confuisng. Keeping the size in mind, the ‘cutting master’ or the CAD supposedly decides it.
It is interesting to note that ‘size mix’ (how many and which sizes should be combined) in a marker is a mind-boggling permutation and combination but actually decided by the CAD operator or “cutting master” hypothetically (of course keeping the size ratio in mind) and not through any scientific process.
For example an order with S/M/L size and maximum 3-garment marker allowed, there are 10 different options for 3-garment marker, 6 different options for two-garment marker and 3 different options for single garment marker. While 3L marker is a theoretical option, practically 3L marker may not be advisable for exorbitant consumption.
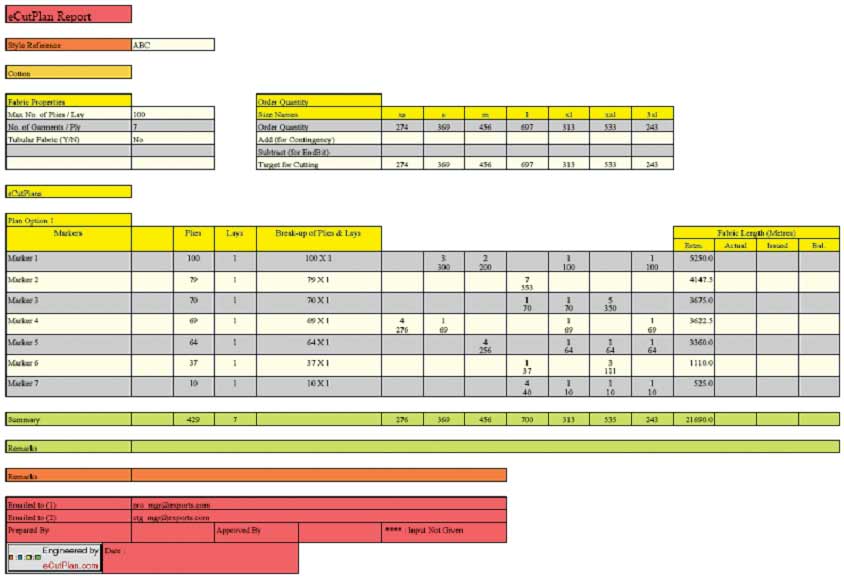
Generally the ‘size mix’ and marker combinations (how many different types of markers are needed for a given order quantity) are generated based on factors like size and colour ratio. Even the spreading and cutting process have infrastructural constraints like lay height (maximum number of ply that can be cut using available straight knife cutting machine), lay length (working length of table available), etc. and working out the most optimum cutting plan under all these factors and constraints is a challenge.
Along with optimizing lay plan, one should also calculate fabric utilization based on fabric roll length available. To maximize fabric utilization, roll length should be numeral multiple of lay length. The roll allocation to lay is best done using mathematical algorithm subject to fabric is defect free. For example:
Lay length of the marker in hand: 6.5 m Fabric roll in hand:
Roll A……………….. 15 m …………….. remainder fabric 2 m [(i.e.15-(6.5×2)]
Roll B……………… 16 m …………….. remainder fabric 3 m [(i.e.16-(6.5×2)]
In this case it is advisable to go for the 15 m roll because the end-bit is less.
The ultimate goal for a business organisation is neither minimizing number of lays nor maximizing use of fabrics, but rather to optimize the “total process cost”. This is complexing; what-if situation, and can only be solved by scientific operational research tools. The total process cost includes various factors like marker making cost, spreading cost, cutting cost, cost of fabric end loss, bundling and ticketing cost, etc. The irony is while you try to decrease your spreading cost you might actually increase cutting cost and vice versa. One cannot minimize all factors at a time; ideally one should prioritise each factor and try to optimize the “total process cost”. For example sometimes the priority is to minimise the fabric consumption (when fabric is costly or in short supply), whereas sometimes the priority is to finish cutting as soon as possible (when fabric arrives late or order is running late), and so on.
Let’s take a simple example. You have received an order of 1200 pieces as under:
Colour/size | Small | Medium | Large |
Red | 66 | 200 | 133 |
Blue | 100 | 300 | 200 |
Green | 34 | 100 | 67 |
Suppose your existing cutting table length will allow you to make maximum three-garment marker and you can cut maximum up to 150 layers by your straight knife machine.
First Option
Lay1 : 100 layers (red 66 + green 34) : marker S : M : L
Lay2 : 100 layers (blue 100) : marker S : M : L
Lay3 : 100 layers (red 67 + green 33) : marker 2M : L
Lay4 : 100 layers (blue 100) : marker 2M
In first option your “cutting master” decides to cut the total order in four lays using three different types of marker. Second option has saved both making time and cutting time while your spreading time may remain almost same.
Second Option
Lay1 : 100 layers (red 33 + blue 50+green 17) : marker 2S : L
Lay2 : 150 layers (red 100 + green 50) : marker 2M : L
Lay3 : 150 layers (blue 150) : marker 2M : L
The Computerized Solution
Cut Plan is a multi-optimality problem. In mathematical parlance it is known as Pareto Optimality Problem. There are many optimal Cut Plan solutions, induced by interplay of many dimensions. The different, but often conflicting, dimensions are:
Less Fabric – Maximising the extreme size mixing. This is emphasized upon when the order quantity is high and the fabric is also expensive.
Less Labour & Time – Minimising the number of lays, leading to saving in spreading cost.
Fewer Markers – Minimizing distinct ratio, i.e. minimising the number of markers to be prepared manually or through CAD software. This is especially useful when you need to commit constant number of sewing machines and workmen for the completion of the order.
More Balanced Production – Minimizing deviation in layer height across lays. This needs to be addressed when the order quantity is low and the time and cost involved in marker making process is relatively more compared to spreading and cutting.
More Balanced Packing – Simultaneous production of garments of all sizes. At times of urgency, interim lots can be sent to the purchaser without waiting till the whole order is complete.
The procedure is simple – Input size details, order quantity, number of plies possible for the fabric and the number of garments possible in a lay, to the dot com. and get alternative Cut Order Plans to choose from.
In a Cut Order Plan, each marker is represented with its corresponding layers, lays and size details. Each Cut Plan is tagged with objective attainment scale. The tool also gives a handle to optimize the objective attainment scales and pull out a customized Cut Plan.
There are many objectives to be attained by a Cut Plan. Not all the objectives can be achieved to the same extent. For a given Cut Plan, in a scale of 100, say one would stand at 75%, the other at 25% and so on. For another Cut Plan, the former objective could be at 40% and the latter 30% and so on.
www.eCutPlan.com also outputs spread-sheet of the selected Cut Plans in excel format, pdf format and html format. The output may be appended with fabric roll and end bit information to issue cutting slip to the cutting department.
Comparing previously executed cut plans with those outputs by www.eCutPlan.com for identical data, you can make an interesting case study. The difference in the total number of plies will be revealing. Also changing the input for ‘ply height’ and ‘number of garments per lay’ will give forth interesting results. www.eCutPlan.com takes you one step closer to scientific management. All it takes is a mouse-click.