Fabric accounts for around 50-60 per cent of the total garment cost, making it very critical to the entire process of garment manufacturing. Garment rejection/alteration due to weaving or knitting defects in the fabric can lead to a huge value loss to the company. Not only the defect identification process, but also the location marking of the defect on the fabric and avoidance of the defect while marker making and subsequently in cutting, is of immense significance so as to offer a defect-free garment.
Pallavi Chaudhary, MF Tech from NIFT and Professor Prabir Jana, Chairperson, Dept. of Fashion Technology, NIFT analyse the operation of dart sewing and the technology involved at the basic and highest levels. discuss different levels of technology solutions available for fabric inspection
Basic level of technology: Manual Fabric Inspection
At the very basic level one can visually inspect fabric on Horizontal or Slanting Inspection tables illuminated from the top and bottom. In this very simple entry level machine, which is usually low cost, a fabric inspector pulls the fabric over the lighted inspection table and the defects are located, marked and recorded on an inspection form manually. For easy flow of fabric, a top fabric guide roll is provided, with an option of adding edge guide and a metre counter. The rolls of fabric are mounted behind the inspection table under adequate light and re-rolled as they leave the table, the mechanical length counter measures the length of fabric inspected. Usually a tray is provided to keep the loose fabric for inspection. In the mechanically driven version, the fabric movement is generally from the bottom to the top, while it is reverse in the case of manually driven ones with standard width of the fabric to be inspected varying between 60 to 75 inches.
The Checkmate by Paramount and Table Type Fabric Inspection machine by Konsan are some of the best options available.

Intermediate level of technology: Mechanical/Semi-automatic fabric Inspection
The intermediate level of fabric inspection machines are power driven with variable frequency drive inverter for precise speed control and proximity sensors to control the uniformity of edges, with an auto-stop option. The machine speed can vary between 12 metres/minute to 60 metres/minute and some models have provision for option to inspect delicate fabrics at zero tension to avoid damage to the structure of the fabric.
Another advantage of semi-automatic inspection machines is the electronic wheel type encoder provided to measure length of the inspected fabric as well as monitor the width of the fabric. While the length measurement is helpful in defining the number and length of lays, even width of the fabric maximizes fabric utilization. The mechanism is such that the fabric runs smoothly through the roller systems (with tensioning adjustments) and then under a metre counter, on to a holding pipe. Fabric speed on inspection machine must not be more than 15 yards per minute, that being the ideal speed at which an operator can comfortably detect faults.
The two-way lighting provision, at the top and bottom, and safety sensors and emergency stop function support better control over the fabric inspection. The machine comes fitted with a metre counter to keep a check on the quantity of fabric being inspected as well as a fabric holding tray to ease out the fabric handling.
This is the most widely used technology for fabric inspection and helps in achieving better and faster inspection, the results are still dependent on the roving inspector’s skill and expertise. RF 101 E by Ramsons and check MASTERIITM by Paramount are some of the best examples available in this category.
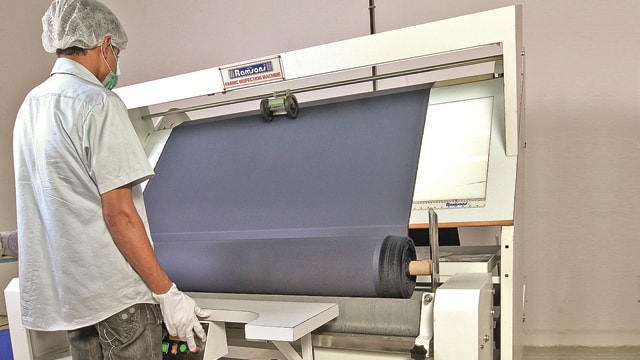
Software add-ons for defect documentation
To document defect pattern for analysis and decision making, ‘fabric inspection defect analysis software’ (FIDAS) is available in the market which can be installed on every fabric inspection machine of any brand and make. It is used for defect entry through a touch screen monitor and performs automatic fabric gradation based on number of defects, providing aid in choosing appropriate fabric roll with less defects and can be easily integrated with all the existing CAD and ERP software in the unit to obtain efficient marker and cutting plan. The software works on the 4-point system for fabric inspection as per ASTM standards, the most commonly used system for inspection.
The software can be customized to develop user defined reports such as fabric batch or roll wise inspection report to determine the number of defects in each roll, daily production report – to keep a check on the productivity in terms of meeting daily targets; fabric realization report – for calculation of actual fabric that can be utilized; and department wise defect report which is helpful in tracking the particular department responsible for the defect such as dyeing and printing department for any colour defect. These reports are instrumental in planning the consecutive processes as well as to maintain a library of the defects occurred for future reference.
Some of the advantages of using the software are increased production rate due to faster process, reduced dependency on manpower, achieving process transparency between interrelated departments and increased profits through improved fabric realization.
Some of the service providers who are selling this software in India are Almac Group, Gayatri Engineers and Amith Garment Services; they also manufacturer and provide fabric inspection machines.
Advanced level of technology: Automated Visual Inspection
The textile industry world-wide has experienced dramatic technological changes during the last decade. Automated visual inspection system is an example of such advancement in fabric inspection process. The most important change is switch over from dependency on human eye to scan by CMOS/CCD camera. The process is such that the location, size and image of the defects are recorded in the system. After the inspection, the product is graded in terms of severity and the detailed report gets printed. The aim is to obtain saving of manpower and time, as well as increased accuracy in the inspection process.
At the first level of processing, the image of the fabric is transformed into a threshold image which is a digital image in grey shades, this helps the software to read and differentiate between the image of the defect and the fabric. Post the conversion, the software marks the region with defects in the form of a window and the location of each defect is stored into the data. The defect window is further probed at the secondary level of image processing based on five attributes, namely, height and width of the defect window; the ratio of total defect area to the overall window area; total number of defects in the overall defects window and finally the ratio of the smallest defect area over the largest defect area. Based on the above mentioned attributes, data regarding each defect is generated, which helps in the recognition and classification of defects based on standard inspecting systems such as 4-point system. The system utilizes high resolution colour line scan technology and enhanced Defect Sorting Algorithms (DSA) to achieve defect detection and interpretation.
The WebSPECTOR by Shelton Vision Systems and IQ-TEX 4 by Elbit Vision Systems (EVS) are two such products which can perform full inspection automatically.

IQ-TEX 4 by EVS is a fully integrated image acquisition and processing system, built on Smart Vision Camera (SVC) platform. The system has the capability to detect defects less than 0.1 mm in size, at speeds of up to 1,000 metres per minute. The solution can be used at many stages starting from the weaving of the fabric to the final of finished products. Some of the features which help in better identification of the defects are real time process monitoring and alarm, defect data for documentation, synchronization with marking and cutting software, and proprietary defect sorting algorithms.
The WebSPECTOR by Shelton, uses line scan camera, often in two or three planes of view, each with a different lighting position for better defect detection and these are back light transmission, diffuse top light and low angle top light. As the defects are detected, an image of each defect is stored along with all the identified data that allows the factory to classify the ‘defect by type’ in real time. An electronic defect map is created which helps in implementing the most efficient cut plan. The WebSPECTOR has been automated to cope with large style and/or product ranges.
Automatic inspection systems are designed to increase the accuracy, consistency and speed of the detection of defects not only in the inspection but also the manufacturing processes of fabrics. There are more advantages in using automated technology for inspection system since it is faster, and also eliminates high inspection error due to human frailty. More importantly, it can save the labour cost by reducing the demand for highly skilled inspectors. It takes years to train a good human inspector, and these automated systems can be installed and “trained” in a matter of weeks.
On-loom Fabric Inspection using Cyclops
To check fabric directly at the weaving stage, few textile mills use the On-loom Fabric Inspection System, which communicates with the microprocessor of the weaving machine and in case a running defect is detected, the On-loom Fabric Inspection System stops and holds the loom, preventing continuation of production of defective fabric. Before the loom can be put back in production, the weaver has to make a declaration, confirming that the defect cause has been eliminated. The weaver’s declaration also allows further specification of the nature of the defect for which the loom has been stopped by the Cyclops On-loom Fabric Inspection System, offered by Barco.
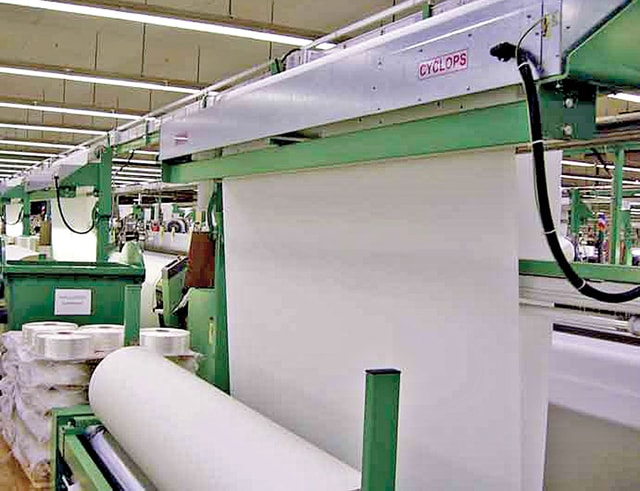
The Cyclops scanning head includes a camera and illumination system. The measuring head travels at a scanning speed of 1.08 metres per minute and has an option of backlight illumination for detection of starting marks in high density fabrics.
In order to help the weaver, a lamp in the loom’s light tree is activated indicating the stop and a message on the loom’s display panel informs the weaver about the nature and location of the fabric defect. The loom will be stopped for any detected running warp defect as well as for a too high concentration of weft or filling defects in a set length of fabric.
The Cyclops scanners cost US $ 5,000 each and can be used for fabric widths up to 260 cm for single panel looms using a single camera and 500 cm for double panel looms using two cameras for scanning. There is also the cost of a one-time vision software license of US $ 25,000. Thus the investment for an installation of 100 looms is about US $ 5,25,000. The company estimates the annual savings for a typical application to be US $ 2,00,000, giving a payback of roughly 2½ years.
Working formulas
• Finishing cost = 0.20 x CM of the garment
• CM price per Operation = Finishing cost x (SAM for single operation/Total SAM)
• Production per day (shift of 8 hours) = 480/SAM value for single operation (min)
• Production per annum = Production per day x Working days/month x No. of months/year
• Cost output/annum = Production per annum x CM price per garment inspected
• No. of machines required = Roundup (Production Target/Production per day, 0)
• Cost of total machine (Rs.), T = No. of machines required x Cost of one machine
• Depreciated value of machine after one year (Z) = Cost of total machine x [1 – Annual Depreciation (%)]
• Total operators salary (Y) @ 12 months = Cost of one operator per month x No. of operators x 12
• CM price from total machine (X) = Cost output per annum x No. of machines required
• Total kWh consumption = kWh consumption of one day (8 hour) x 26 x 12 x No. of machines; 1 kWh = 1 unit
• Total electricity consumption (W) = Total No. of units x 5 (price of one unit)
• Cash Inflow (I) = X – Y
• ROI for the first year = (X-Y-W)/Z = I/Z
• Payback Period = T/I
ROI for technology in Fabric inspection |
||
CM price of the garment (Rs.) Assumed | 100 | |
Cost for (Fabric inspection + spreading + cutting + fusing) Rs. | 10 | |
CM price of fabric inspection per garment (Rs.) | 1 | |
Fabric consumption per garment (in metre) | 2.5 | |
Intermediate Level of Technology | Advanced Level of Technology | |
Fabric inspection rate (metres per minute) | 30 | 1,000.00 |
SAM value for fabric inspection of single garment (minute) | 0.0833 | 0.0025 |
Production per day (shift of 8 hours) | 5,760.00 | 192,000.00 |
Working days in a month | 26.00 | 26.00 |
Months in a year | 12.00 | 12.00 |
Production per annum (pieces) | 1,797,120.00 | 59,904,000.00 |
CM price per garment inspected (Rs.) | 1.00 | 1.00 |
Cost output/annum (Rs.) | 1,797,120.00 | 59,904,000.00 |
Production target (pieces per day) | 80,000.00 | 80,000.00 |
No. of machines required | 13.89 | 0.42 |
Cost of one machine (Rs.) | 250,000.00 | 2,000,000.00 |
Cost of total machine (Rs.) (T) | 10,500,000.00 | 833,333.33 |
Annual depreciation (%) | 15.00 | 15.00 |
Depreciated value of m/c after one year (Z) | 8,925,000.00 | 708,333.33 |
Cost of one operator per month (minimum wage) | 5,500.00 | 4,800.00 |
Total operators salary (Y) @ 12 months | 916,666.67 | 24,000.00 |
Total KwH consumption per year | 209,664.00 | 5,391.00 |
Electricity cost per year (Rs.) (W) | 1,048,320.00 | 26,955.00 |
CM price from total machines (X) | 24,960,000.00 | 24,960,000.00 |
Cash Inflow (I = X-Y-W) (Rs.) | 22,995,013.33 | 24,909,045.00 |
ROI for the first year (I)/Z (%) | 257.65 | 3,516.57 |
Approx, Payback Period (T/I) | 6 months | 12 days |