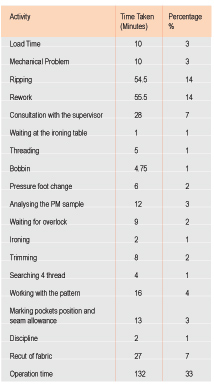
Several time-wasting and invaluable activities are involved in the manufacturing of a garment, which require immediate removal. They reduce the percentage of cycle time of Work in Progress (WIP) in sampling department. These activities are defined as Non Value Added Activities. Parul Singh & Nipun Goyal, B.F.Tech (Apparel Production), under the guidance of Archana Gandhi, Associate Professor, NIFT, Delhi discuss them.
The ultimate goal of any organisation is to increase productivity, pay good wages to employees, provide satisfactory dividends to their investors and sell products and services at a competitive price. Amongst the activities involved to increase productivity is cutting down on wastage. A very important principle of waste elimination is the standardization of workers’ actions. Standardized work basically ensures that each job is organised and is carried out in the most effective manner. There are three different activities that exist in almost all apparel industries:
1) Value Added Activities : These include such activities that the customer envisions as valuable either in a product or as a service, for example: sewing operation.
2) Necessary Non Value Added Activities : Activities which do not make a product or service more valuable, but are necessary under the current operating conditions. Such waste is difficult to remove immediately but cannot be ignored. Instead, it should be targeted for long-term changes. Example: walking to the ironing table.
3) Unnecessary Non Value Added Activities : These activities are neither valuable for a product nor for its service. They are sheer waste and should be targeted for immediate removal. Example: waiting at the ironing table, searching for attachments, etc.
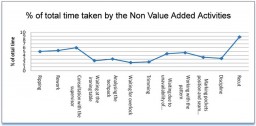
Chart 1 explains the methodology (with percentage) followed while performing the above three activities. Around 20 samples were tracked and activities enlisted against them. The main focus during the project was to enlist the third kind of activity, i.e. Unnecessary Non Value Added Activity, and suggest ways to eliminate them.
On comparing the Value Added and Non Value Added Activity time from the samples, the conclusion reached was that only an average of 53% of the total time is Value Added Activity, and 37.54% of time is the Non Value Added Activity. The average percentage time taken by each of the Non Value Added Activities is explained in Chart 2.
The following solutions could help in reducing the Non Value Added Activities and maximize production:
1. On a standard sample sheet, sketch the sample and write down the construction details. This will avoid getting into frequent arguments with the Supervisors.
2. Use work aids wherever feasible in order to avoid excessive ripping and rework problems; thus saving time.
3. Have a proper job distribution for smooth flow of the sampling department.
4. Inculcate a culture to improve discipline, cut down on unproductive activities by the operator such as trimming of excess fabric, and reduce waiting time for out of line processes such as pressing table.