Despite being a key player in the global market, India’s denim industry has recently been bogged down by challenges such as fluctuating demand, supply chain issues and market volatility. These challenges are reflected in the balance sheet of several major denim players as they witness revenue decline in FY ‘24.
For example, Arvind Ltd., a US $ 3 billion group, saw its denim segment revenue dip from Rs.1,586 crore
(US $ 191.08 million) in FY ’23 to Rs.1,257 crore (US $ 151.45 million) in FY ’24. The group produces 50 million metres of denim, 200 million metres of woven fabrics, 74 million garments and 12,000 MT of knits every year.
Similarly, Jindal Worldwide’s revenue plunged from Rs. 2,070 crore (US $ 249.40 million) in FY ’23 to
Rs. 1,824 crore (US $ 219.76 million) in FY ’24. The company with an annual capacity of 140 million metres of denim fabric generates 98 per cent of its revenue from the domestic market.
Nandan Denim, with an annual capacity of around 110 million metres of denim, saw a slight dip in annual revenue from Rs. 2,027 crore (US $ 244.22 million) in 2023 to Rs. 2,010 crore (US $ 242.17 million) in 2024.
Another key player, Vishal Fabrics, too saw its revenue decline from Rs. 1,547 crore (US $ 186.39 million) in FY ’23 to Rs. 1,450 crore (US $ 174.70 million) in FY ’24. The company has an annual dyeing capacity of 80 million metres and a processing capacity of 105 million metres.
Raymond UCO, a 50:50 joint venture between Raymond Limited and Belgian denim giant UCO NV, also felt the effects of sluggish market growth, with revenue from its Indian operations declining to Rs. 790 crore (US $ 95.18 million) in FY ’24, from Rs. 973 crore (US $ 117.23 million) in the previous year. The company’s denim manufacturing facilities are located in Yavatmal (Maharashtra) and Romania, with a combined annual capacity of 47 million metres. In addition to meeting domestic demand, Raymond UCO exports to over 30 countries.
Siyaram’s, one of India’s leading men’s textile and fashion conglomerates, saw its revenue decline from Rs. 2,229 crore (US $ 268.55 million) in FY ’23 to Rs. 2,087.2 crore (US $ 251.47 million) in FY ’24. The group entered the denim mill segment with its Den-Knit brand in 2019.
However, RSWM Limited of LNJ Bhilwara Group reported mixed numbers. Its total revenue rose from
Rs. 3,788 crore (US $ 456.49 million) in FY ’23 to Rs. 4,057 crore (US $ 488.82 million) in FY ’24, but its EBITDA dropped from Rs. 339 crore (US $ 40.84 million) to Rs. 131 crore (US $ 15.78 million) in the same period. RSWM manufactures denim fabric under LNJ Denim, with a manufacturing capacity of 25 million metres annually.
Whereas, Aarvee Denims experienced the largest revenue decline, dropping by 65.4 per cent, from Rs. 263 crore (US $ 31 million) in FY ’23 to Rs. 91 crore (US $11 million) in FY ’24. Based in Ahmedabad, Aarvee has annual production capabilities of 39,000 metric tonnes of yarn, 85 million metres of denim fabric and 18 million metres of non-denim bottomwear.
Factors behind the setback
The Indian denim industry is facing several issues with most of the players citing external factors as the key reasons for the slow growth. Extra pressure was felt last year as major economies like Japan and the UK slipped into technical recessions (defined as two successive quarters of GDP contraction) during the September-December quarter of 2023. Additionally, Ireland and Finland faced similar downturns in the fourth quarter and at least 14 other countries saw shrinking GDPs in the July-September quarter. These global disruptions, alongside ongoing conflicts such as the Russia-Ukraine war and the Israel-Hamas conflict, have complicated the trade landscape for Indian exporters.
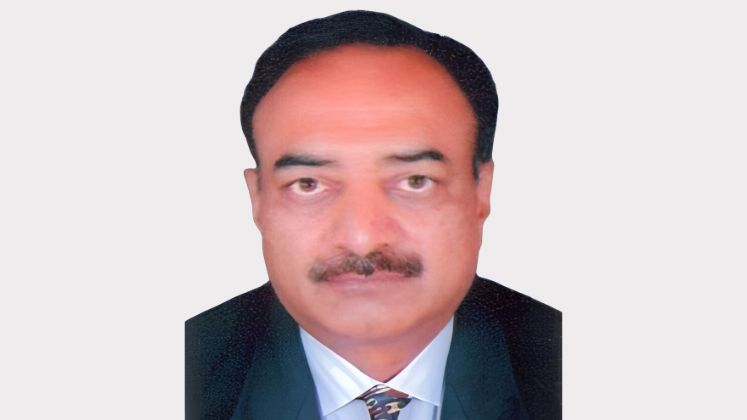
One of the most significant hurdles has been the Red Sea shipping crisis, where Houthi rebel attacks have disrupted operations through the Suez Canal, a critical global trade route. According to a JP Morgan report, with 30 per cent of global container trade passing through this canal, supply chains have become strained and shipping costs have surged nearly fivefold on certain routes, particularly between Asia and Europe. CRISIL has warned that these prolonged disruptions could further erode profit margins and extend the working capital cycles of textile manufacturers.
Highlighting the impact of the crisis, Vinod Mittal, Director, Vinod Denim, which boasts a production capacity of 50 million metres and a turnover exceeding US $ 361 million, stressed, “The Red Sea issue is a major challenge for the industry, leading to increased container prices. In contrast, China is better positioned due to government subsidies on freight costs.” He added that domestic hurdles, such as the 45-day MSME payment rule, election-induced policy paralysis and monsoon disruptions have further stunted market growth. Echoing these concerns, Vishal Fabrics, in its annual report, noted that FY 2024 faced export challenges stemming from the Red Sea crisis, alongside increased competition from lower-cost fabric imports from Bangladesh, which negatively affected domestic players.
“Almost all nations felt the effects of global economic uncertainty, including higher energy and food prices, inflation rates and volatile markets,” remarked Gautam Hari Singhania, Chairman and MD, Raymond Limited in a statement. Whereas, Brij Mohan Sharma, Joint Managing Director, RSWM Limited, noted in the company’s annual report, “As the Russia-Ukraine conflict entered the third year, its negative impact weighed heavily on the European nations – demand for apparel nosedived. Latin American markets remained tepid owing to the political instability.” He also pointed out that, despite operating at 90 per cent capacity, pricing pressures drove their margins south, a struggle shared by many competitors.
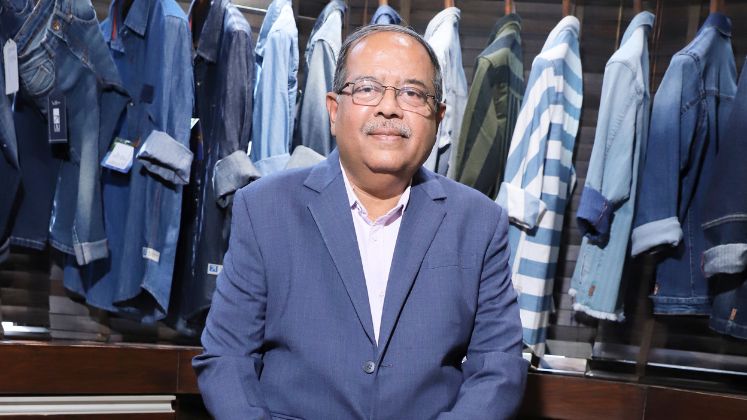
Although India’s GDP has been performing relatively well, no country is entirely immune to the effects of globalisation. External headwinds have also affected India’s economy. It’s no surprise that experts observed subdued demand in the Indian textile market, even during the typically high-demand festive season.
Unfazed by the challenges
“Despite the setback, the denim players are upbeat about the future. The visible positives are that the US market is stabilising, inflation in the UK has dropped and Central Bank interest rate stability in Europe has worked well in building consumer confidence. If these factors continue into FY ’25, we should see better days,” claimed Suketu Shah, CEO, LNJ Denim. Suketu highlighted a key achievement for the company: reclaiming its status as the largest supplier to Levi’s. Additionally, RSWM plans to slightly increase its supplies to Levi’s to meet their growing demand. The company has also welcomed a US-based brand to its customer roster, enhancing revenue visibility for the upcoming months and into the first half of FY ’25. Furthermore, the company is exploring the possibility of venturing into garment manufacturing to create a more streamlined and integrated supply chain for its clients.
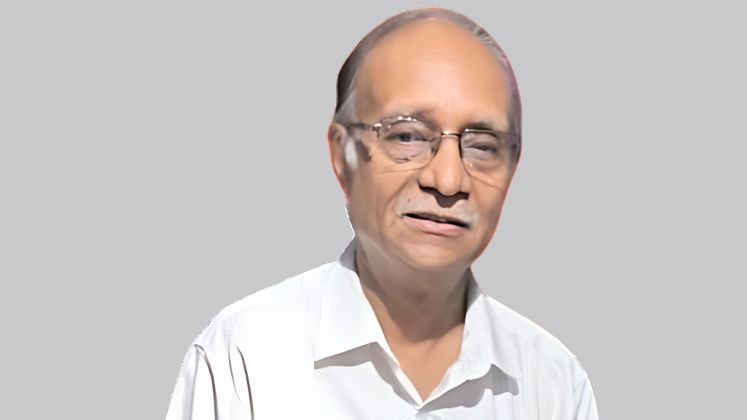
Meanwhile, Raymond plans to continue focusing on cost efficiencies and product re-engineering to provide customers with value-based solutions. The group will also pursue ‘asset-light’ expansion in garmenting to efficiently increase capacity. Similarly, Arvind has proposed a new investment strategy set for the next three financial years, including an expected total investment of US $ 48 million to US $ 55 million through FY ’25. This investment will be applied to a variety of needs such as upgrading its fabric base and other matters to ensure it leverages the market effectively.
Experts highlight the robust growth potential of the Indian economy, which is expected to sustain its positive momentum in the coming years, supported by a steady decline in inflation. India is on track to become the world’s third-largest economy, with its GDP projected to surpass Japan and Germany, reaching US $ 5 trillion by 2027.
“I believe the worst is behind us. We’ve gained momentum and our mills are now operating at nearly 100 per cent capacity,” stated Vinod Mittal.
“We see tremendous potential in expanding our sustainable product offerings and tapping into new markets. Our focus will be on agility, innovation and sustainability to navigate these challenges effectively. We would also strengthen our distribution network,” stated Avinash Patel, President of Marketing, Jindal Textiles. Having said that, companies are not shying away from exploring non-traditional avenues for growth. Arvind Mills has already ventured into real estate, while Raymond Realty, the real estate arm of the Raymond Group, was established in 2019. Jindal Worldwide has also forayed into the electric vehicle space.
1,600
India’s denim production is over 1,600 million metres per annum, making it the second largest producer of denim fabric globally, after China. According to an AO survey, about 65 per cent of this fabric is used domestically, including for jeans that are exported, while the remaining 35 per cent are exported to countries like Bangladesh, Colombia, Venezuela, Egypt, Sri Lanka and the UAE. Amongst these, Bangladesh stands out as a key destination, accounting for 35 per cent of India’s denim exports. |
“It makes sense to explore non-traditional avenues to prepare for the future. You can’t keep all your eggs in one basket as the market is becoming more competitive. Last year, many players had to sell at prices below market rates. Once buyers get accustomed to a certain price, it becomes challenging to ask for a fairer one,” said DK Jain, Director and Head of Export Marketing, Nandan Denim. He mentioned that Nandan Denim is diversifying by manufacturing BOPP (Biaxially-Oriented Polypropylene) film for the FMCG sector, having set up a manufacturing facility in Ahmedabad. For those unfamiliar, BOPP is a type of plastic film widely used in packaging, labelling and laminating applications.
When it comes to market trends, industry experts agree that clients have been increasingly prioritising comfort and stretchability for the past couple of years. “I haven’t seen anything groundbreaking in terms of colour. Clients are leaning heavily towards blends. The demand for 100 per cent cotton is declining; instead, there is a growing interest in four-way stretchable fabrics. Even for shirts, more customers are seeking stretchable options,” Avinash explained. Suketu added, “We offer single-ring core-spun yarns with LYCRA/spandex and dual-ring core-spun yarns featuring T400/LYCRA or polyester/spandex fibre combinations at the core.” In line with modern trends, Aarvee’s textiles now incorporate LYCRA dualFX technology, which enables tight-fit jeans to adapt to various body types and postures through the flexing of the dual core yarns.
Experts agree that the resilience and proactive strategies of denim mills position them well for a strong recovery in the coming years.