Much effort is expended in garment factories in moving work from machine to machine and department to department. This is an additional work for which the customer does not pay! How the work moves through the factory is, of course, to a large degree dictated by the building in which it is housed. In this article, Paul Collyer discusses the pros and cons of multi-storey factory as a part of a two article series. He emphasizes here on floor-to-floor workflow, information flow and movement of people for ease of production.
The single storey high roof industrial shed type of building and layout are by far the best as long as factories are made in sprawling acres of lands. Where rolls of fabric arrived at one end of the unit, progressed through warehousing, cutting, sewing, finishing, on to the finished goods and despatch either in a straight line or a U-shaped flow and then left through the same door or one sited at the opposite end. Most of the single storey buildings also have mezzanine floors built in to give additional floor space commonly used by managers to keep a hawk’s eye over the entire production floor below. But as many of the factories in developing countries are in metro cities where land cost is high, factories are made in multi-storied buildings (a good example can be seen in India too). While industrial sheds offer advantages towards layout of steam and/or compressed air line to every workstation without interrupting environment and workers manoeuvrability (using the vertical space due to high ceiling), the multi-storied buildings offer compactness, security, use of gravity for intelligent material movement.
Strangely many companies prefer to use the ground floor for office space and then place additional machines or materials on the upper levels. In my experience people can walk and move up the stairs much easily than machines and materials. Whereas it is no coincidence that the best laid out factories I have seen are new builds I do not wish to dwell on their usage as few managers have the luxury of laying out a factory from the beginning in a purpose built unit. Most have to arrange the best compromise they can in a multi-storey building erected for any number of uses.
It is, not always possible to give an optimum layout for a multi-storey factory as there are too many variables. However, we can discuss a few options and examples. The first and the foremost concern in a multi-storey factory is the workflow side.
Should the workflow up or down?
Should we place the cutting room on the top floor and move the material to a warehouse located on the ground floor?
Or should we reverse the order and start from the bottom and finish with completed goods on the top floor?
Finishing and washing departments are often preferred in top floor to use the sun drying facility Often, maximum populated departments are kept in basement, so they don’t have access to other departments
The dilemma between cutting and finishing site
Historically the most commonly used option is to site the cutting room at the top and flow work downwards. This system needs recommendation because of the fact that mostly finished garments need pressing. Presses, particularly modern carousel units, are heavy and bulky and it is not necessary that all buildings will have the structure and the required strength to accommodate heavy equipments on interim floors. Additionally, the steam and vacuum generation plants ideally should be sited on the ground floor, nearer to the fuel supplies, with minimum pipe runs.
Cutting rooms have traditionally been placed on the top floor allowing the flow of cut panels downwards. However there is no hard and fast rule as different circumstances dictate different solutions. The change from hand fabric spreading and cutting by straight and band knife to computerized laying and cutting in which heavy equipment is moved from table to table has forced many companies to locate cutting rooms on the ground floor.
Additionally many companies use a central cutting facility to feed satellite make-up units and locating cutting anywhere other than a lower floor involving extra work.
Why ground floor is preferred by all ?
However when other units are being serviced it is not uncommon for garments to be returned for finishing and packing. So several departments vye for the preferential ground floor space. Again there is no set rule as garments from outside factories are often placed into the workflow for finishing etc. Managers should work with simple flow charts and approximated times for moving materials to determine the optimum layout for their factory and not rely on convention or “gut feeling”.
Talking of knitted fabric, should it be taken out of the premises for brushing or dyeing or can the floors handle the weight of the knitting machines? Such queries need to be pre-planned thoroughly.
Thus we can conclude that there is no perfect factory layout for the smooth flow of work, and that a practical compromise is the best the manager can achieve. As long as the flow of work is sensible and does not move up and down between the floors, we can allow the material to flow through the sewing floors.
Advantages of single floor layout
A key area where the single storey building proves to be a better option over the multi-storey is that it requires far fewer support walls and pillars, no central staircase and emergency stairs. The manager therefore has the freedom to layout the sections or departments to the best advantage and to accommodate whichever work transport system is utilized.

In Figure 1, all production is based on one floor. Incoming goods arrive at one end of the factory, travel through all processes and finished goods exit at the far end. The sewing layout is a traditional version in that jacket components are completed as subassemblies and then collated prior to loading onto assembly. Optimum transport would be components on trolleys (not collars which can be worked from block) assembly on an overhead transport system that continues into pressing. Trouser production is separate and trolleys used throughout.
Let us take few examples of multi-storey operations of specialized as well asfashion garments.
Multi-storey factory layout plan
It is of course possible to work in a multi-storey building with even the most complex of garments but as it is unlikely that all operations can be fitted onto one floor, the manager has to decide at what point in assembly the production moves from floor to floor or indeed what format the production sequence has to follow. Many garments have operations common to most styles and it is desirable for productivity reasons to form specialist sections to deal with them primarily as they are often of a very short cycle (e.g. manufacturing looping for trousers or jeans with a folder) or they need specialist equipment (e.g. automatic pocket setting using Duerkopp etc.). With the majority of small cycle operations it is desirable, to minimize handling to work “in block” straight from the cutting room and then at some point collate components into bundles onto trolleys or bags. Where does the manager site these operations? If the factory has more than one floor producing the same product then each floor needs to be given its own specialist section thereby doubling or trebling equipment need and producing poor equipment utilization.
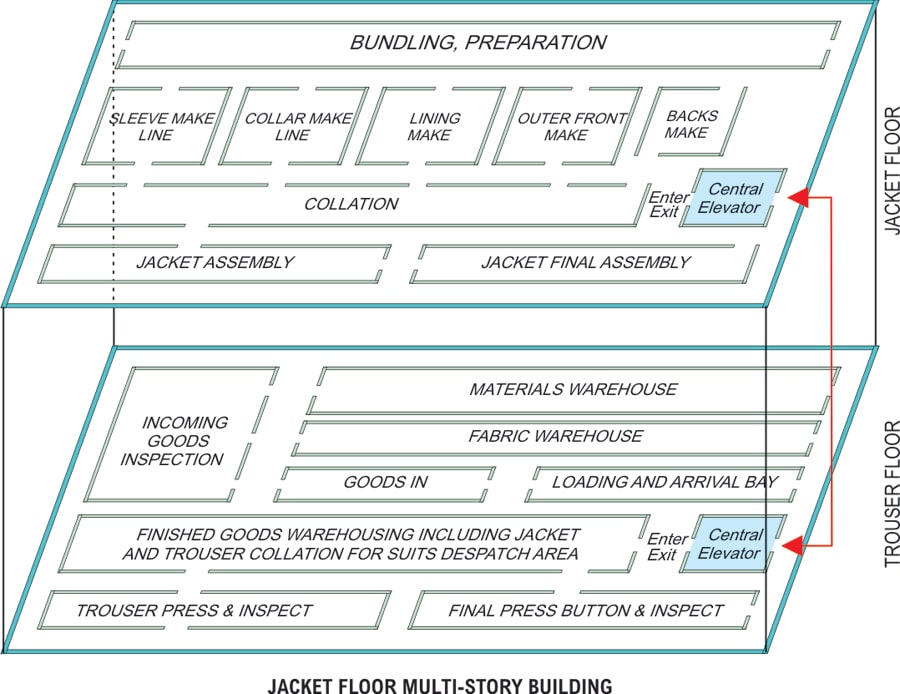
In Figure 2, the jacket sewing lines occupy first floor of a multi-storey building. As in previous example the work flows through sub assembly sections on trolleys (not collars) and is collated prior to assembly cutting, whereas, warehousing, pressing and despatch are on other floors. Obviously, it is not as effective a layout as the one floor option. The ground floor is divided into two functions: acceptance and storage of fabric and components; and finishing and despatch of completed suits. All services such as steam generation, vacuum, generator, etc. are not shown as they should be housed externally and not in the working areas.
The ideal way to make jackets is to work in bundles on trolleys to prepare subassemblies, e.g. patch pockets, fronts, sleeves, collars, backs, linings, etc. It is usual for each subassembly to travel through a specialist section independent of others to reduce throughput time and to be collated into garments when necessary. Ideally when the subassemblies need to be joined together, individual garments should be put onto an overhead delivery system. This handling system dictates the layout of the factory. In a multi-storey building the subassemblies may be made on one floor, passed down to an assembly floor and then on to a ground floor pressing department. Additionally most men’s wear factories also make trousers and these will usually be allocated separate floors.
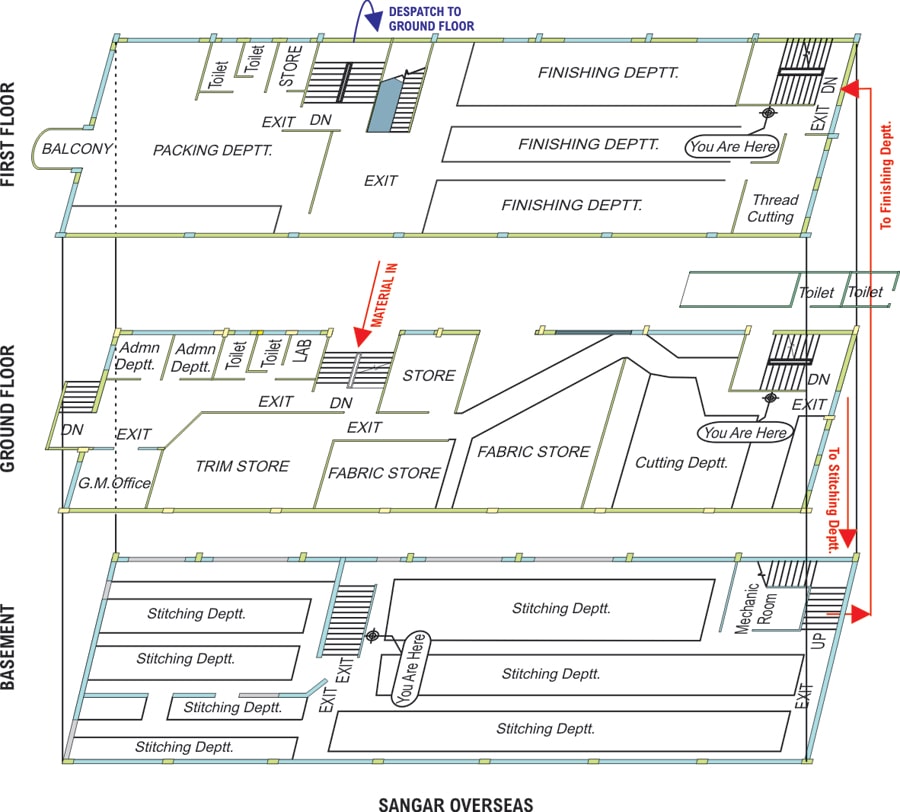
In Figure 3, the factory in NCR, India basement area is used for sewing room, which is not really common (a quick check with rules and regulations reveals that there are no restraints in having sewing activity in basement). The logic here is that maximum populated departments are kept in basement, so they don’t have access to other departments. The factory doesn’t want to show the rest of the factory to the operators.
The generator is on the ground floor and is on the outside of the main building. The finishing department at the top floor necessitated having steam boiler installed on this floor. PERC dry cleaning machine generally causes vibration and that is why it is preferred on the ground floor. But in this example it is located on the additional floor on the top of the building (not shown in the diagram); the additional floor has been created with shock absorption facility to minimize effect of vibrations. Finishing and washing departments are often preferred on top floor to use the sun drying facility. Fabric storage at ground floor although simplifies the raw material entry but cut parts first go down to basement for sewing, followed by travelling to the top floor for finishing and again back to ground floor for dispatch.
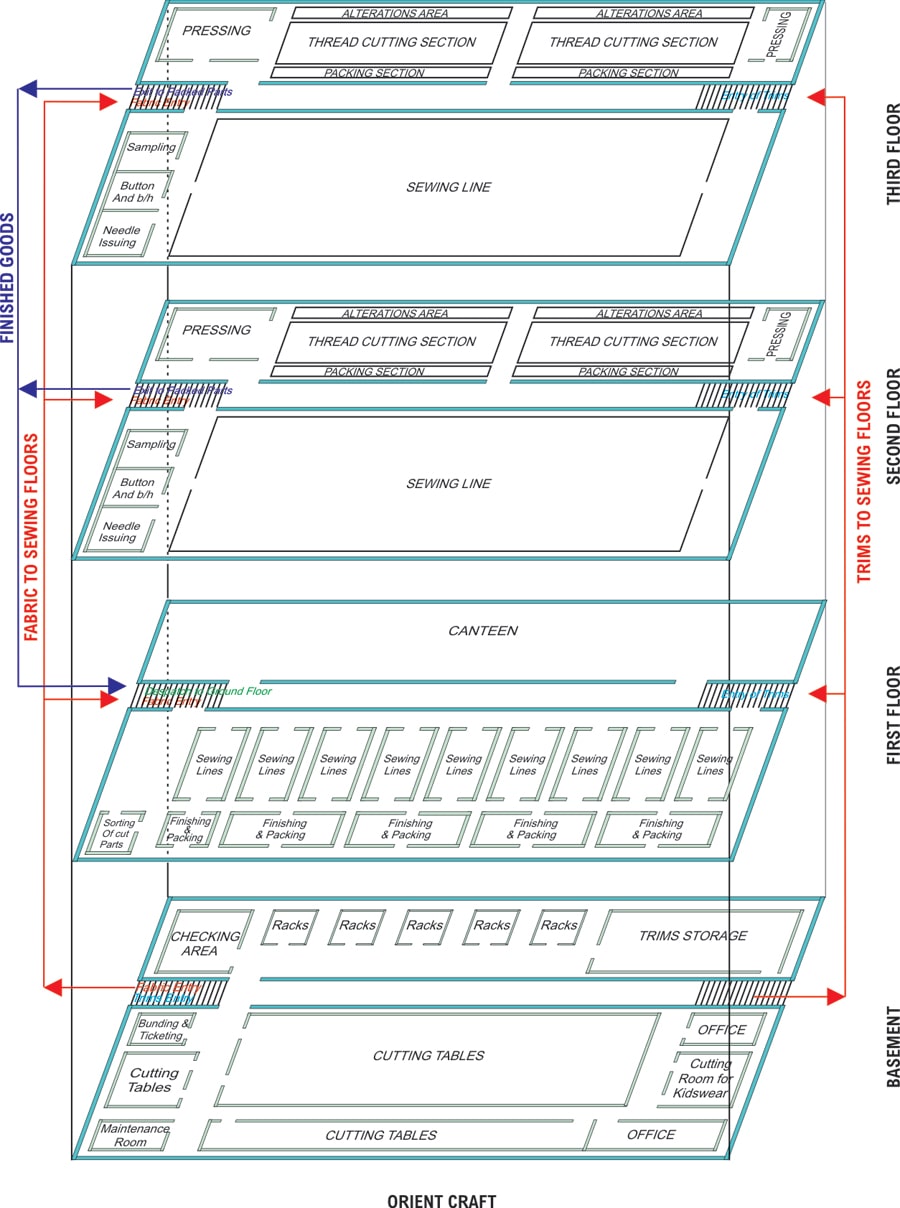
In Figure 4, again of a factory in NCR, India, the basement is used for cutting and fabric storage enabling fast cutting and distribution of cut parts than having cutting at top floor. The company produces 50% women’s wear, 30% kids wear, rest men’s wear. It manufactures primarily tops and with a lower percentage of bottoms – 10% trouser and 5% skirts. Sewing is divided into multiple floors style wise and one can trace back in case of bad quality. The cut parts and trims are having unidirectional flow upwards to each floor while finished goods have unidirectional flow downwards to ground floor for dispatch. Ground floor has a boiler and a generator outside the main building area besides office space and reception (not shown in the figure). Steam distribution pipeline has to go to all the floors resulting in energy loss in the topmost floor.
Conclusion
While main emphasis remains on the material flow between floors, other non technical reasons often become decisive in designing layout. Whether to allow operators and the management staff to use same staircase and elevator or allowing sewing work force to interact with cutting and finishing work force (where sewing work force may be contract labour and rest in company payroll), may lead to labour unrest. Also the sewing operators on the ground floor may get distracted by outside activities; and most importantly vaastu (feng sui) often influence in deciding the actual layout. Many companies will have access to software enabling them to plot the path of garments through a number of potential solutions. Those who are less fortunate can, of course resort to the tried and tested string diagram to measure the distances work will have to travel; a combination of graph paper, pins, thread and a ruler still works!