The key aim of every layout is to maximize utilization of available space in order to optimize the material flow, maintaining visibility or ease of supervision. The other benefits of a good layout may be improving on other productivity factors such as manpower, machine and lesser defects. Different production setups have different arrangements of resources depending on a number of factors such as product, process, and space availability, and of course mindset of the management.
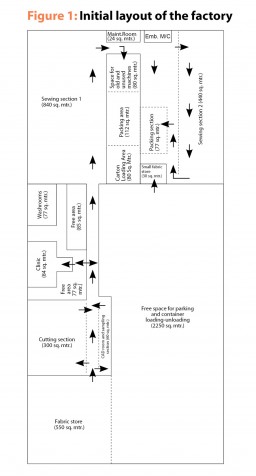
We observe a number of variations in the machine layouts having its own pros and cons. And we always starve for better layouts aiming for maximizing unidirectional material movement optimum handling and storage of cut parts, half-finished parts and complete garment for easy retrieval.
Manoj Tiwari, Associate Professor, NIFT Jodhpur and Dr. Prabir Jana, NIFT Delhi discuss various aspects of an effective layout with actual shop floor cases, observing significant and visible improvements.
Layout plays a critical role in making the IE practices effective and significantly visible. An effective machine arrangement may help in smoothening various kinds of flows (man, material etc.). This also helps in improving on quality issues, throughput time and very importantly making the problems visible. Many a times, we observe machine arrangements in a very haphazard and unorganized manner where it’s very difficult to even understand the flow. This kind of situation makes operators confuse and supervisor couldn’t channelize his attention to his many activities.
The layout planning should be as simple as possible and able to link the different departments and processes seamlessly. The activities should be arranged in a logical sequence making the control effective and result in minimum man, material and equipment movement. Such layout also has a number of other benefits such as effective control of WIP, efficient space utilization, minimum time consumed in transportation, improved cleanliness, effective man and machine utilization and last but not the least making the problems visible. [For further understanding refer to Apparel Plant Layout: Basics in SW May 2009 and Improve Factory Layout to Boost Productivity in SW September 2010].
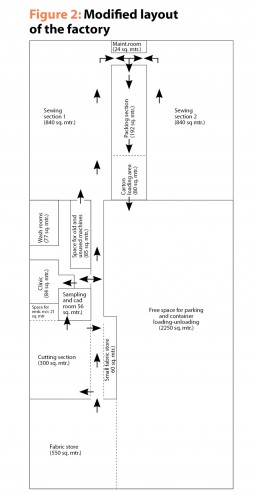
There are two levels of layout planning done by industrial engineers: in macro level it is the factory layout and in micro level it is the layout of sewing machines in a sewing line. The macro level factory layout is done once during factory setup or during expansion, major re-planning and not on daily basis. The micro level machine layout is done during every new style planning. The sewing machine layout planning depends on long term factors like style changeover system and storage and movement of semi-finished material within sewing line (read SW, May 2009). These systems or policies generally remain unchanged for a factory, and an industrial engineer generally plans the machine location and their sequence based on the operation breakdown flow chart to minimize the flow path of semi-finished parts. Often the material handling system and equipment is also changed based on style change which will be discussed in the next article. The sewing machine position within a layout can be facing unidirectional, reverse directional, straight or angular and each layout has its own advantages and disadvantages (read SW, May 2009). An IE has to choose the most appropriate layout for his overall factory settings. We will discuss the factory layout (macro level) planning as well as machine layout (micro level) planning with case example each.
Case -1 – Case of a factory
Like the sewing lines sequential arrangement of machines is critical, such arrangement is equally important while deciding the factory layout. Many a times, we observe that various sections are located without any logical thinking. It is very important to keep all the related departments/processes near to each other. This results not only into minimized material and manpower movement but improved control and ease of supervision. Just by using a little common sense and understanding the process flow, significant visible improvements can be done. This is also very important that the changes should make the process smooth, that too without much disturbance; besides other important things to consider that any such changes should be done with minimum possible investment to avoid financial burden on the factory management.
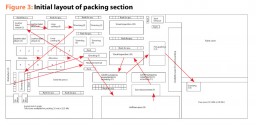
Let’s understand this with a case of a factory whose layout was modified. The old layout of the factory is shown in Figure 1. Few points can be easily observed from this layout as below:
1. Packing activity is happening at different places which may make the control difficult and may as well hamper the space utilization.
2. A small fabric store is located near to Sewing Section 2, which is far from the main fabric store. This is resulting into an increased fabric movement while fabric is carried for cutting.
3. Embroidery section is located near to Sewing Section 2; due to this cut panels which are going to be embroidered have to travel comparatively more distance from cutting section before coming back for bundling.
4. A good space is occupied by the old and unused machines.
While observing the old layout critically, we find that there are few spaces which are not utilized properly; such spaces are areas available near to clinic and space occupied by old and unused machines.
A logical re-arrangement may result into seamless linking of process and an improved space utilization as shown in the modified layout (refer Figure 2). Few modifications can be observed in the modified layout:
1. Embroidery section, CAD and sampling room have been moved near to the cutting section. This may bring improved control and less distance travelled in material movement.
2. Old and unused machines have been relocated to the area near to clinic with a provision of gate opening towards Sewing Section 1. This has resulted in free space between Sewing Section 1 and Sewing Section 2.
3. Small fabric store has been relocated from Sewing Section 2 (in the area earlier occupied by CAD and sampling room), near to fabric store and cutting section. This will result into an easy fabric transaction while cutting as well as effective supervision.
4. Packing which was happening at different places has been arranged to be at one place, between Sewing Section 1 and Sewing Section 2 with only 1 entry and exit points.
5. The modifications done (as mentioned in point No. 1 to 4) have resulted into an increased space availability in the Sewing Section 2 which can accommodate at least 90 additional sewing machines and makes Sewing Section 1 and Sewing Section 2 equal in terms of number of sewing machines accommodated.
The rearrangement of layout (Case Study 1) resulted into improved space utilization, better (minimized) flow of material, seamless linking of fabric store, CAD & Sampling and Cutting Department. Other visible improvement is an exclusive packing section with no disturbance or interference of other sections. The same has been done with no or minimum investment and disturbance to the regular activities.
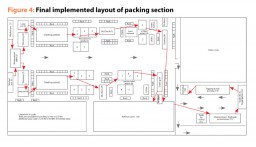
Case – 2 – Case of a packing section layout modification
A jeans manufacturing setup with a daily packing capacity of 4,000 units/8 hours has to deal with two kinds of jeans product orders where one is high-end with smaller order quantities while the other product is for masses with bulk quantities.
The layout of the packing section is such that many a times one product needs to wait as other product is in the section. Many a times, high value garments couldn’t be packed as mass order of other product is in packing and small quantities (yet high value) got delayed. In other times, mass quantities had to wait as an extreme care is required in packing of high-value garments and entry of other styles may create chaos. Management tried to execute packing of both the products parallel but it resulted into serious quality issues as workers got confused and packing trims (price tags, leather patches etc.) were interchanged.
The task was to redesign the packing section with the available resources that both styles could run smoothly and waiting time can be avoided.
First of all the existing layout of the packing section was studied and it was revealed that the flow was not smooth (refer Figure 3, Initial layout of packing section).
Table 1: Code and operations (for old layout) | |
Code | Location/Operation |
1 | Table for washed pieces |
2 | Measurement table |
3 | Leather patch attach |
4 | Belt loop cutting |
5 | Thread trimming |
6 | Dusting |
7 | Checking |
8 | Hoffman Press |
9 | Size measurement |
10 | Visual inspection |
11 | Labelling and tagging |
12 | Poly bagging/packing |
13 | Scanning |
It can be observed from the Figure 3 that the initial layout of packing section had a clumsy arrangement of resources and making the flow complex. The sequence of the activities is shown in Table 1 and while following the activities using arrows in the figure, it can be seen that products had to travel a longer zigzag path.
Table 2: Code and operations (for modified layout) | |
Code | Location/Operation |
1 | Table for washed pieces |
2 | Measurement table |
3 | Thread trimming |
4 | Loop cutting |
5 | Checking |
6 | Alteration |
7 | Alteration checking |
8 | Leather label attach |
9 | Dusting |
10 | Hoffman press |
11 | Measurement, folding and Preparation |
12 | Shade segregation |
13 | Poly bagging/packing |
14 | Scanning |
The challenge is do re-design this layout in such a manner (in the given area and without any additional resources). The objective is to enable this facility run both the styles at a time that too without any interference.
Capacity study may be done for each operation required for packing the different styles and resources may be allocated to meet the individual style requirements. Further resources can be re-arranged following the packing operation sequence. Figure 4 shows the re-designed arrangement of operations and resources meeting individual style requirements.
Table 3: Tentative area allocation in a garment manufacturing setup | |
Section Name | Tentative Area share (%) |
Fabric store | 10 -15% |
Spreading & cutting | 10 -15% |
Sewing | 35 – 40 % |
Finishing & packing | 15 – 20 % |
Others (Admin offices, Maintenance deptt., Offices for production personnel, IE, quality, etc. | 10 – 15 % |
The re-engineered layout as shown in Figure 4 shows a sequential arrangement with smooth flow. Other noticeable things in the modified layout are 2 clearly visible packing setups, capable to handling packing of 2 different products at a time. In order to utilize the available area, free area (as shown in Figure 3) has been utilized while designing the modified layout.
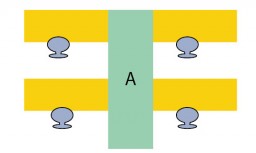
There are little modifications in the sequence, as leather label attach was activity number 3 in previous layout; the same is placed as activity number 8 in the improved layout. Also provision of sewing machines for lather label attach is kept in one line only depending on the requirement. Resources of these two packing setups may be shared in case of only one style in packing.
What should be an ideal area given to a particular process? This is one of the frequently asked questions by the factory owners and managers while developing layouts and facility design. There is no clear cut answer to this but based on our observation on a number of existing layouts for various products, a macro level area allotment may be as mentioned in Table 3. As far as layout for entire production process (from fabric stores and cutting to finishing & packing) is concerned, the area of a section depends on various factors such as product type, process and space availability. We observe a varied proportion of area allotted to different sections in different production setups. For example, in a home textile setup generally cutting sections are bigger compared to other setups as cutting sections require handling of high fabric volumes. While in a jeans manufacturing setup, sewing section requires more area.
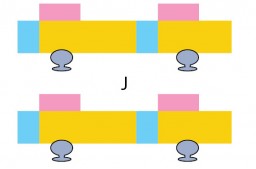
Let’s try to understand the same with an example. Assuming the total area of a garment manufacturing setup is 10,000 sq. mt., considering that after following the bylaws area available for manufacturing activities is 60% of total area. Now we have 6,000 sq. mt. of area available where sections such as fabric store, cutting, sewing and finishing & packing may be planned. Following the distribution mentioned in the Table 3, area of sewing section may be roughly 2,400 sq. mt., while fabric store, spreading & cutting may be of approximately 900 sq. mt. each. Assuming on an average a sewing work station requires 4.5 sq. mt. area (including all the aisles and areas for loading & receiving material on the sewing floor), as much as 530 sewing machines may be accommodated in the available space.
It is worth mentioning that the above estimates are purely based on our experience of various plants and there are no standards available on the same. Still it may be used as a ready reference while planning for plant setup, of course the area allocation may vary depending on the specific requirements.
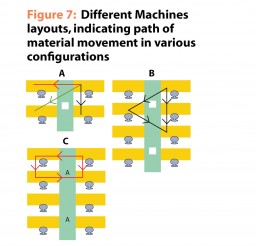
Case – 3 – Sewing Line
The machine layout in a line either has two rows of sewing machines with centre table (Figure 5) or with individual pick up and disposal bins for each sewing machine (Figure 6).
For common centre table layout, the machines are arranged in such sequence so that the flow of semi-finished components flows from one machine to another in shortest path. In Figure 7A, if the components move diagonally to next operation, it will cover maximum distance (green line) than moving sideways (red line) or forward/backward (black line). In an operation flow of jeans manufacturing, suppose one operator is making belt loops and feeding two operators for the operation of loop attach to waistband. After belt loop attach, the pieces are moving to one operator who is bottom-hemming it. The several options of machine arrangement of the four machines are shown in Figure 7B and 7C; while Figure 7C involves lesser length of movement than Figure 7B. Similarly, there will be numerous options while mapping the complete flow of semi-finished pieces in a complete line and IE has to weigh all options before deciding the preferred option.
Conclusion
There is no clear-cut answer or ready recipe to design a layout. Different kinds of solutions are suggested in different work environments. A solution which is working well with one setup may or may not fit with others. Sticking to basics can only help in an effective layout in a particular setup. A good layout solution should be able to establish seamless interaction among resources (man, material and machine) and processes without compromising safety.