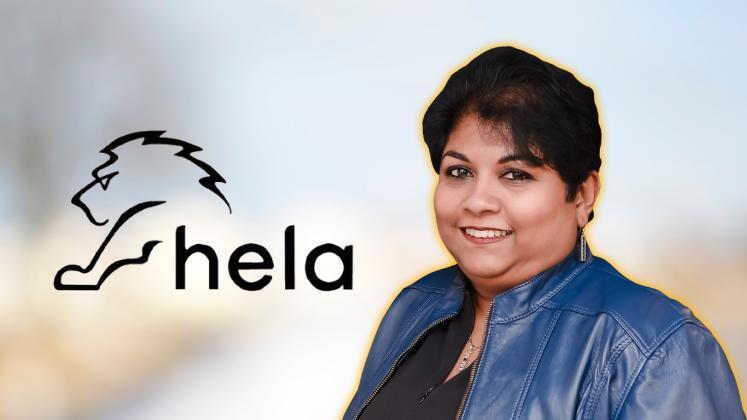
The apparel manufacturing industry is an ever-evolving landscape, constantly shaped by various forces—technological advancements, geopolitical shifts and global events.
In my journey, which began in programming, I’ve embraced change as a constant. This inclination originated from my early days exploring various programming languages and courses, reflecting the dynamic nature of the apparel industry. I believe that adaptability is crucial, especially when geopolitical shifts demand swift and strategic adjustments.
Looking five years ahead, the industry will likely undergo significant regional and global shifts due to political advancements, economic trends and evolving consumer preferences. While these fluctuations may spur industry revival, they shouldn’t be mistaken for enduring expansions. Despite the Covid-induced growth bubble, projected industry growth rates range from 2 per cent to 4 per cent (McKinsey & Company – The State of Fashion 2024), with luxury items showing higher percentages of growth.
During these periods of significant industry shifts and changes, it’s imperative for manufacturing companies to remain steady and not be swayed by temporary market bubbles. The future I envision for the industry revolves around a collaborative and regulated supply chain ecosystem. This future is deeply intertwined with product innovation, particularly in integrating sustainability measures and wearable technology.
Enterprise Resource Planning (ERP) systems form the bedrock of this transformation. We’ve termed our initiative as the ‘Digital Core’ project because, to us, an ERP serves as the foundational pillar.
The implementation of this project was a significant milestone for Hela as it greatly enhanced our operational efficiency and cohesion. It was also the first SAP S/4 HANA fashion implementation in Sri Lanka. The project spanned across an 18-month period, marked by staggered rollouts across different clusters of plants within and outside Sri Lanka:
Initial Phase – October 2022:
- Kids Cluster Go-Live: This phase encompassed the onboarding of three plants in Sri Lanka and one in Egypt, constituting the kids’ cluster. It involved four distinct legal entities within Hela.
Follow-up Phase – April 2023:
- Intimates and KinetiX Clusters Go-Live: The second phase of rollout, occurring six months after the initial kids’ cluster implementation, included the onboarding of three additional plants in Sri Lanka, two in Ethiopia and one in Kenya. Additionally, this phase involved the integration of a sizeable subcontracting plant and five legal entities within Hela.
The transition from a fragmented system landscape to a singular integrated solution proved transformative. The entire process—from receiving confirmed sales orders to dispatching finished goods—was streamlined and standardised.
A key integration was the development of a state-of-the-art Manufacturing Execution System (MES) solution that replaced multiple versions of the previous shopfloor systems. This new solution was seamlessly integrated with SAP, leveraging QR codes on tablets and a Wi-Fi network within plant flow areas for real-time monitoring of production, data capture and analytics, accessible via mobile devices and digital displays.
Moreover, our HR function underwent an extensive digital transformation by consolidating six separate systems into a unified platform. This involved integrating with MiHCM to streamline payroll, time and attendance and a comprehensive talent management suite. Additionally, we synchronised employee IDs with the MES for real-time data capture, connecting to SAP and our planning system. This ensured precise adjustments to planned consumption as operations unfolded on the plant floor. This complex integration entailed a four-way link between SAP S/4 HANA, the MES system, our MiHCM HR system and the Coats Digital Fast React System.
A notable capability introduced through this integration was the ability to seamlessly receive orders across multiple legal entities and geographies within Hela and manufacture based on the business requirement within our global network of manufacturing facilities. Previously, this process was burdened by multiple systems, whereas now, the streamlined approach within a single system ensures enhanced decision-making and efficiency.
These integrations represent just a few examples of the transformative advantages realised through our Digital Core implementation. However, it did have its share of challenges.
Firstly, data migration emerged as a significant hurdle. Legacy data posed compatibility issues with our SAP migration strategy. Anticipating this during the cutover, we proactively engaged additional resources to rectify data discrepancies post-migration.
Additionally, data quality presented a formidable challenge. While the migration process was meticulously structured, weak data quality amplified corrective efforts post-migration.
Moreover, operational changes within Hela and geographical challenges added complexity to the project. The conventional approach of freezing operational changes during IT projects became impractical in this dynamic landscape.
Employee training and adoption, particularly in a post-Covid context, posed another challenge. Remote training, while cost-effective, proved inadequate for language-specific training requirements in certain geographical locations.
Despite encountering these obstacles, the rollout of our Digital Core brought many meaningful outcomes and benefits.
Enhanced Visibility: The transition to the Digital Core and HR360 programmes facilitated heightened visibility across operations. Plant floor data, including piece count (the number of garments produced) and efficiency on an hourly basis, is now readily accessible to plant workers, management and even the CEO through mobile apps and dashboards. Integration with SAP extended this visibility beyond planners to various levels within the organisation, fostering a deeper understanding of operational metrics.
Improved Performance Metrics: The increased visibility enabled by the Digital Core allowed us to track and compare planned versus actual metrics daily. This comparison serves as a foundational tool for enhancing operational efficiencies. It sets the stage for elevating performance standards by leveraging real-time data insights to improve processes continually.
Future-Proofing Digital Foundation: The implementation has laid a robust digital foundation for Hela, positioning the company to build upon this framework. In the current digital era, this foundation serves as a launchpad for advancing into the next wave of digital transformations, particularly in utilising Artificial Intelligence (AI) for data-driven decision-making while leveraging APIs for integration with customers and suppliers.
KPI Dashboards and Metrics: We have identified 66 priority key performance indicators (KPIs) leveraging data from the Digital Core and HR360 programmes. Plans are in motion to utilise this data to create digital dashboards, providing a comprehensive overview of these KPIs. While this is a future endeavour, it represents a significant step toward data-driven decision-making and performance tracking.
Recognition and Awards: The transformation of the manufacturing execution system using tablets and QR codes was acknowledged and celebrated within the industry. We received an Industry 4.0 award from SAP at their Dare to Dream event, underscoring the innovation and excellence achieved through this digital transformation.
I’m grateful to the Digital Core and HR360 project teams whose unwavering commitment, dedicated teamwork, relentless perseverance and eagerness to learn and innovate were instrumental. Their dedication, combined with strong support from the board and group management, ensured the timely deployment of these projects within Hela.
If there’s one crucial takeaway in today’s uncertain world, it’s the indispensable role of technology adoption coupled with robust process integration. Amidst global uncertainties, especially within the apparel industry, CEOs and leaders must prioritise technology deployment and ensure process adoption is given due importance.
Investing in technology, working with sound partners and continual upskilling of resources should be at the forefront of any company’s strategy. This proactive approach fortifies businesses, ensuring resilience against unforeseen disruptions and fostering adaptability in the face of an ever-evolving landscape. Ultimately, it’s the harmony between technology and process adoption that forms the bedrock of survival and sustainability in today’s uncertain world of business.
Ruwanthi Fernando, Group Chief Information and Process Officer at Hela Apparel Holdings PLC
Group Chief Information and Process Officer at Hela Apparel Holdings, Ruwanthi Fernando has three decades of expertise, steering digital revolution for organisations such as Prima, Associated Motorways, Camoplast Solideal (Michelin), Expo Freight (EFL) and driving customer’s digitalisation through N-Able and Microsoft.While she drives Hela’s technological future through innovative processes and digital transformations, she also spearheads transformative initiatives, including the seamless integration of SAP S/4 HANA across global operations. In this role, she bears responsibility for managing organisational change, fostering a culture of innovation, process improvement and driving the adoption of new technologies amongst employees. In recognition of her unwavering dedication and contribution to the technology sphere in Sri Lanka, she was recently featured on the inaugural National CIO List 2023 of the Computer Society of Sri Lanka. A devoted mother, caring wife, singer, animal enthusiast and also the Chief Culinary Creator for Roo’s Deli, she thrives on embracing change both professionally and personally. |