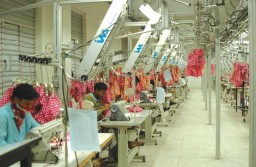
Apparel manufacturers are perennially striving to cut down costs and improve productivity. It can be achieved by the use of efficient material handling processes. Unit Production System provides for improved efficiency, by eliminating highly unproductive material handling procedures. A survey by Clemson Apparel Research, USA, reveals that the implementation of UPS of as a percentage of total sewing capacity varies from a low of 9% of total capacity to a high of 92%. In a polo-shirt manufacturing plant, approximately 90% of the sewing operations are achievable on a UPS workstation.
At a time, when competition between clothing manufacturers has never been greater in terms not only of price but also of flexibility, turnaround time, quality, quick response etc, there is a need to review the production sections, individual workstations and the deployment of associated garment handling and control systems, which are all very fundamental to the efficient running of a production unit.
Development of Unit Production System (UPS) System
[bleft]Unit Production Systems leads to a reduction in direct labour content of 9.7% by completely eliminating bundle handling costs, the pulling of piecework tickets and the associated clerical duties[/bleft]
Studies showed that in garment manufacturing industries, material handling and other associated non-value added activities accounted for 80% of operator’s time, leaving only 20% of the time for adding value and for actually sewing the garment. It was evident that efficiency in the apparel industry could be improved upon by eliminating the highly unproductive material handling procedures. It could be achieved by developing systems to convey garment parts from one workstation to another, in a coordinated manner. The underlying theme was to create a smooth workflow and effectively utilise both the workers and equipment.
The history of UPS can be traced to the early 60s.
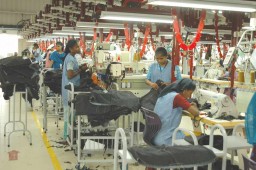
At that time the Swedish apparel industry was experiencing a number of cost related problems; throughput times were too high and as a result, demands for quicker delivery times could not be met; garment workers were forced to waste time handling and transporting material instead of sewing, and capital was needlessly tied up in work-in-process (WIP).
The result was development of an ingenious material handling system called Unit Production System (UPS) by Eton Systems. The UPS didn’t waste valuable floor space and required no major modification to the existing machines. The system eliminated ‘bundle handing’ (tying and un-tying of bundles) and allowed all the material needed for a specific garment to be transported as a unit directly to the sewing machine of any workstation. When an operation was completed at one workstation, the system would automatically send the unit on to the next.
These days, Eton Systems from Sweden, INA Systems from Singapore and SMART-MRT from Japan are some of the popular manufacturers providing fully automated systems. Additionally, Switchtrack from the UK provides manual systems.
Salient Features of the Unit Production Systems
[bleft]UPS can result in improved operator’s productivity by an average of 18.4%. This figure represents an actual increase of garments produced per hour for the entire plant versus the production levels achieved in a traditional bundle system for that plant[/bleft]
The Unit Production System is basically an overhead conveyor, which moves the single product between workstations. With every UPS workstation, comes the unique chain and multiple rail system, which helps to maximise the productivity and ergonomics. Systems and floors are also linked with bridges and elevators. In addition to an easier pick-up and a free disposal at each workstation, the UPS reduces the time the garment is normally idle between workstations. Most importantly, Unit Production Systems address the weakness of imported goods: long delivery and customer response times. UPS requires a reduction in work-in-process levels and a change in the management philosophy of a sewn product plant from “high work-in-process is efficient” to “low work-in-process levels allow quick response”.
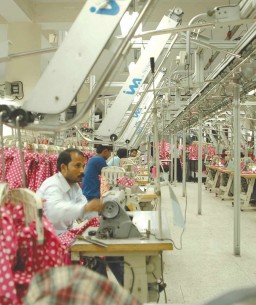
The modern Unit Production Systems are modular, which makes it very easy to adjust for every customer’s specific needs. There are no fixed design or welding of parts. Individual stations, or even entire systems, can be moved and reconfigured as circumstances change.
The varying needs of both the apparel and textile industry are met by two system platforms; one designed for lighter products of the apparel/textile segment such as shirts, jeans, ladies’ blouses, bathrobes and bed sheets and the other for heavier and bulkier products such as quilts, large rugs, mattresses, office seating, etc.
Computerisation of UPS & Real Time Production
These days automatic loading devices, pick-ups and work delivery robots are included, and real time production control software provided, for immediate up to the minute accurate production, quality and labour cost information.
Real time production control goes hand in hand with the UPS concept as all relevant management and performance information is automatically generated and presented through the software. It helps the customers make better decisions on a real time basis, thereby conquering their next hurdle even faster. The computerisation of UPS has two significant benefits: firstly, the opportunity for human error is reduced, and secondly, the data collection is automatic and does not consume productive operator time.
However, the main benefits that accrue from a UPS come from an in-depth knowledge of how to handle it. Operators need to be provided professional training in handling of both hardware and software. Current UPS software is available to allow a company to link several UPS lines together, and also to tie in to off-line operations. There is also a historical link to each product after it has been completed. All combinations need to be firmly linked in the software to make the UPS concept completely unbeatable.
Advantages and Disadvantages of a Modern-day UPS
A study by Clemson Apparel Research, Clemson University, USA, confirms the inherent benefits of UPS. The key advantages of UPS are increased productivity and efficiency, improved quality, reduction in direct and indirect costs, reduced WIP inventories, as well as a reduction in operator fatigue due to the ergonomic advantages. The ‘one-piece’ (one unit per carrier/hangar) flow makes it easier to process smaller batches and still get an economically efficient manufacturing process. The Unit Production System also offers substantial reduction in throughput time, turnover, attendance and space utilisation.
The factory’s efficiency increases immediately and work-in-process radically reduces. Probably the most striking advantage of the UPS is the drastic improvement in throughput time to the extent that reduction in total cycle time from 14.9 days to an average of 5.9 days is possible. The shortening of throughput times enables any quality problems to be identified much quicker; operators can concentrate on sewing, and with all parts hanging, the amount of in-process creasing is reduced drastically resulting in less final pressing. Faster throughput also results in accelerated invoicing since there is faster conversion of piece goods to finished product. This obviously improves the manufacturing cash flow. Not only does the productivity improve, but also production can be planned and controlled down to each individual garment.
Unit Production System causes a reduction in direct labour content (9.7%) through ergonomic garment handling by the operator and its automatic removal upon completion of the sewing cycle. Further, there is a complete elimination of bundle handling costs, pulling piecework tickets and completing clerical duties.
UPS leads to a significant improvement in quality of product (by an average of 60.4%), mainly because of the drastic reduction of work-in-process. Problems are not ‘hidden’ in bundles and tend to show up quickly. Also, this improvement in quality, directly affects operator productivity since more garments are sewn correctly the first time and fewer defects must be corrected. The reduction in defects (by 11.1%) results in a savings in the number of off-line repair people, mender carriers, etc. There is a better overall appearance of the products due to garments being hung versus tied in bundles and stored. These garments tend to require less inspection, cleaning and pressing. All of this results in a better quality product.
The use of UPS leads to improved operator’s productivity (by an average of 18.4%) and less fatigue, since operators neither have to pick up heavy bundles nor stretch to pick up and dispose of garments. The UPS also helps to pace operators by automatically positioning the next garment. Additionally, there is no bundle handling, which tends to break the operator’s rhythm. Another added benefit of UPS is that it has a positive effect on operator annual labour turnover rate, which has been seen to reduce by 29.5%.
A UPS line is seen to improve the operator’s satisfaction and morale. The combination of a high-tech environment, the potential for increased earnings, and increased team feeling seems to contribute to higher morale. Operator earnings (gross pay) were seen to increase by 8.7% (productivity increase of 18.4% less direct labour cost reduction of 9.7%). Because the distribution of work is accomplished by a computerised sorting system, all claims of “favouritism” are eliminated. Many of the computerised systems also offer semi-automatic line balancing, because the supply of work is given to the faster operators automatically. The sorting of work can be accomplished automatically by size, style, and/or colour, which lead to a reduction in operator method changes and thread changes.
On an average, Unit Production
Systems result in a reduction in floor space of 40.3%. Most of this reduction is due to less storage space required for work-in-process. In a UPS unit, most of the work-in-process is stored on the system above the operator and machines are normally located closer together than machines in typical Progressive Bundle System (PBS) units.
Depending on how one likes to look at it; one ‘disadvantage’ could be that the demand on the attention and hands-on activity of the supervisor is increased. With the dramatic reduction of WIP levels, errors and imbalances are revealed quicker. While these challenges exist in any manufacturing system, large levels of WIP often hide their impact. Automated and computerised UPS calls for active supervisors who are called upon to focus on these challenges in order to accomplish more. A commitment to education and training is necessary for customers to get the most out of their UPS investment.
Conclusion
The global sewn-products manufacturing situation has changed dramatically during the last few years. It has resulted in a marked growth in the demand for UPS mainly because the system focuses on speed, variety, and value.
Companies need to consider investing in UPS to strategically improve their manufacturing capabilities.
Excerpts from the Interview:
Eton Systems, an ingenious hanging conveyor system, was designed and developed by Inge Davidson, technician and co-owner of the Eton Shirt Factory in 1967. Today, with nearly 4000 customers and over several hundred thousands installations in 60 countries, the Eton UPS concept has gained recognition as the industry standard for precise and comprehensive production control by leading global manufacturers. StitchWorld talks to Claude Kehren, who has been working with the company for the more than 22 years, about the marketing strategy of the company for the Indian market.
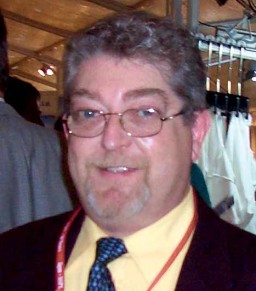
What advantages do you believe a UPS has over other quick response, low work-in-process manufacturing systems such as team manufacturing processes?
Claude: Team manufacturing processes are good and are not contradictory to the use of the UPS. In fact, team and modular initiatives are sometimes incorporated within the Eton System. However, UPS consistently provides superior overall improvements in productivity, efficiency and quality together with total control. Companies require much more training of the operators with a manual team working system than with an UPS system. This is an advantage in countries like China, as they change staff very often.
How modular is the hardware in terms of adjustment of height? Is the installation from the roof or floor or both? Can it be dismantled and re-assembled when a factory moves or relocates, and if so, with how much percentage of recovery?
Claude: All the hardware of the Eton system is modular. The height of a system can go from 2.30 m or less to 4.50 m or more; this depends on the need for the type of production and on the possibilities in the studied factory. A line for a bed set production will be installed as high version (3.50 to 4.50 m) due to the length of the products. A garment production is generally installed 2.50 to 2.70 m high. In general, the systems are floor mounted but any system can be hung from the roof, if the structure from where to hang it, is adapted. Every Eton system can be dismantled, re-assembled or moved or extended, etc. with nearly 100% recovery.
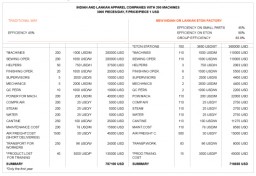
What is the installation time per workstation? How many days will the company require to start functioning, especially in case of companies changing from the PBU to the UPS system?
Claude: The installation time per workstation depends a bit on the configuration, but on an average, a few hours are enough. To start functioning from PBU to UPS takes just a few hours; the production starts immediately after installation, but the customers are assisted, trained and educated until the Eton team feels that they are confident with our systems and with their new environment.
What is the cost per workstation?
Claude: The cost per workstation is variable depending on the configuration of the system, the type of stations, the type of clamps, the need of flexibility for the production and the amount of workstations which are ordered. On an average, a station price will be between 3000 USD and 4000 USD per workstation.
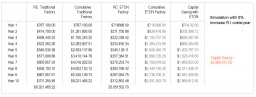
What is the ideal number of workstations for the best ROI?
Claude: There is no ideal number for the best ROI; this depends on the actual situation, the type of production and adherence to Eton’s instructions by
the customers. You will have excellent ROI in Polo shirt production for lines of 35 stations, in trousers for 50 stations, in made-ups for 37 stations, etc. The ROI, in general, is between 6 months and less than 2 years. For a new factory, it could be immediately when making the right choice between a traditional production and an Eton UPS production.
What kind of layout would you suggest – Straight or ‘U’ shaped?
Claude: A system could have different layouts (U, L, E, I, combined lines, etc.). It all depends on the need for the given production, the planned production per day or shift, the configuration of the sewing room, the available space, the height, the pillars, etc. But any configuration is possible with Eton.
If you are suggesting different layouts for different products, please explain with examples.
Claude: The layout given by Eton will always be the best alternative after considering the best use of the space, the best solution for the type of production and for improving the production. We follow only one rule “Give the best solution and the best service for the best possible price! In other words- the best satisfaction for our customers!” Eton has progressed for more than 40 years only because of its success stories!
Established in 1977 in Singapore, Singapore Machinery Co Pte Ltd is one of the premier providers of solutions to the manufacturing requirements of garment industry. In 1998, the company developed the fully computerised SMART MRT Unit Production Systems, which was claimed to be the first in South East Asia. StitchWorld talks to Richard, President, Smart MRT about the specialities of the company’s new Smart UPS system
What are the advantages of your UPS system over Bundle System?
Richard: The Smart UPS requires only 1/3 ~1/5 production time to that of a progressive bundle. It carries less WIP (work in process) – more than 50% less, comparatively. It can increase productivity by 25~50%.
How modular is the hardware in terms of adjustment of height? Is the installation from the roof or floor or both? Can it be dismantled and re-assembled when a factory moves or relocates, and if so, with how much percentage of recovery?
Richard: It brings the sewing parts close to the sewing needle -as close as 10 inches- to minimise the body movement of the sewing operators. There is no necessity to adjust the height. Our system requires a ceiling height of only 2.8 m. It does not require roof/ceiling mount as there are no centre pillar/supports for our ‘new’ system (but both can be apply).
The Smart MRT System is in modular form. It can be dismantled and modified to suit a new factory layout.
What is the installation time per workstation? How many days will the company require to start functioning, especially in case of companies changing from the PBU to the UPS system?
Richard: Average assembly time for one line of 30~60 workstations will take between 4~7 days to install.
What is the cost per workstation? What is the ROI? What is the ideal number of workstations for the best ROI?
Richard: RSP is approximately USD 3200. ROI is normally within 2~3 years. Ideal number or workstation would depend on the type of products and factory floor shape & size.
What kind of layout would you suggest – Straight or “U” shaped? If you are suggesting different layouts for different products, please explain with examples.
Richard: We would usually recommend straightline, as the setup is neat and requires less travelling time. But according to the factory floor availability, we design the layout & shape of the system that is best suited for the application.
Swtichtrack Systems has been improving the production lines of garment exporters for sewn products for over 20 years. Till now, the company has increased its clientele list further and has an installation of more than 100,000 Stitchtrack systems installed in 27 countries. The system delivers most of the benefits of a powered system for just 25% of the cost. To ensure improvement in productivity, the company offers a layout design service for the garment manufacturers and also provides technical and operational support. Steve Mogford describes the unique features of the Switchtrack Systems to StitchWorld.
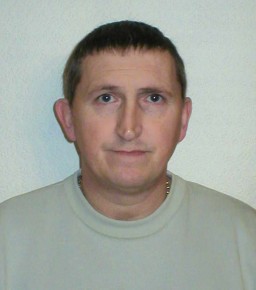
How modular is the hardware in terms of adjustment of height? Is the installation from the roof or floor or both? Can it be dismantled and re-assembled when a factory moves or relocates, and if so, with how much percentage of recovery?
Steve: A completely modular UPS can be moved very easily and reassembled at a new area.
What is the installation time per workstation? How many days will the company require to start functioning, especially in case of companies changing from the PBU to the UPS system?
Steve: It is less than 1 day. Most factories I have dealt with, stop work on Friday and start functioning on the new system (Switchtrack) on Monday. It takes only 3 days to get back to the previous output, and normally on the 4th day, the output increases.
What is the per workstation cost? What is the ROI ? What is the ideal number of work stations for the best ROI?
Steve: The cost per station depends on quantity ordered and the type of system. In general, it is $570/stn for 1 line of say 30 stations. This amount reduces as the number of stations increase.
ROI depends on starting point. It depends on how good the company is at production management before installation of Switchtrack. The biggest improvement is at workstations with poor Production Management! The improvement is less at a site with good management. In general terms, the improvement is between 15% and 40%.
There is no ideal number of stations for best ROI. The number of stations depends on garments being made and methods of manufacturing being used.
Example ROI ….If a company is making 750 polo shirts on a line and achieves a minimum 15% increase, it gets 113 extra garments /day or 675/week (113 x 6) or 33,750/year (675 x 50).
If it receives say $4 a shirt, it works out to an extra $135,000 ( $4×33,750) in increased turnover. The extra cost for this increased turnover is labour (if piecework) and fabric and trimmings. If labour is salary, there is no extra cost; if labour is piecework, it’s minimal; and fabric and trim is normally 65% of the turnover.
Therefore fabric and trim cost would be $87750. If we take this away from our increased turnover this leaves $47250. This is increased contribution to overheads and profit.
If we say that with our existing manufacturing, we are paying for our overheads then this amount must be regarded as increased profit.
The cost for 1 line of 30 machines which would make this number of Polo shirts would be approx $20,000. Therefore the ROI is less than 6 months. (47,250/87750).
What kind of layout would you suggest – Straight or “U” shaped ? If you are suggesting different layouts for different products, please explain with examples?
Steve: I wouldn’t suggest any layout. The layout is one that suits the company in terms of its products, staff, buyers, and methods. Generalisation in this industry is unprofessional; every company is different.
I suggest a layout only after finding out about all aspects of the production in the company.