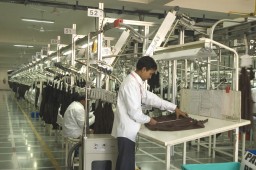
Quality Control, Quality Assurance and Quality Management are the concepts which have assumed increased importance for the Indian garment export industry currently reeling under the threat of decreasing margins due to several factors. Bringing down costs and improving quality of products at the same time to meet the emerging competition from our neighbouring countries is staring the industry in its face. Pradip V Mehta, a Fellow of the American Society for Quality (ASQ) having 32 years of quality management experience, discusses here the concepts and advises how these concepts can be implemented successfully in the Organisation depending upon the activities undertaken.
A well known quality management expert, Philip B. Crosby spelled out the difference between quality control, quality assurance and quality management by suggesting to think of an organization as an automobile, with the driver as management. Quality control would be the car’s measurement features: dials on the dashboard tell how much fuel the car has, how fast it is going and the oil pressure or engine temperature status, etc. Upscale autos have computer packages that offer drivers all kinds of data, including trip, range and miles per gallon. They can use this data to see if everything is operating well and if they are going in the right direction.
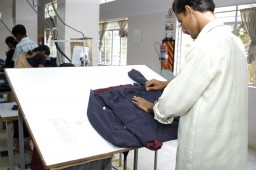
Quality assurance is the car owner’s manual. It describes the entire vehicle’s components, discusses maintenance, gives direction on how to turn the lights on and has many useful procedures for keeping the car running well. Quality management is the vehicle’s operating philosophy. Driving style relates to an organization’s operating procedures. If a driver chooses to meet telephone poles or icebergs straight on, that has nothing to do with quality control or quality assurance. Both serve only as information; they do not operate the vehicle.
Now let us understand quality control, quality assurance, and quality management in some detail so that one can implement any one of them effectively in order to be able to manage quality of whatever one is producing.
Quality Control (QC)
Control simply means controlling operations or processes in a manufacturing or service environment so that the quality requirements for a product or service will be met. Therefore, quality control means operational techniques implemented to control operations or processes.
ISO defines quality control (QC) as “the operational techniques and activities needed to fulfill requirements for quality.”
Under QC, actual performance of a product or service is evaluated and compared against requirements (quality goals), and action is taken on the differences, if any. Following steps are necessary under QC for each product or process:
a. Choose what to control – This refers to a characteristic or property such as shrinkage, colorfastness and/or a process such as a sewing operation that need to be controlled or kept within certain limits.
b. Choose units of measurement – Decide in what units such as %, pounds/grams, inches/centimeters, etc., the characteristic or property to be controlled will be measured. Sometimes the characteristic or property to be controlled may be appearance of an operation such as certain seam finishing or pocket placement.
[bleft]Pradip V. Mehta, a Fellow of the American Society for Quality (ASQ) has 32 years of quality management experience. He worked for a $ 8.9 billion, multi-national retail and service organization for 30 years in quality assurance, retiring as the Director of Quality Assurance. Mehta has written three books on quality management and is a member of the Consumer Advisory Council of the Underwriters Laboratories (UL), Inc. and Consumer Interest Forum of the American National Standards Institute (ANSI). Also on the Editorial Review Board of Quality Progress, a monthly published by the American Society for Quality, he teaches quality management on a visiting basis at several institutions in India as well as two ASQ Certification refresher courses in the U.S.[/bleft]
c. Establish frequency and number of measurements – Decide how often the measurements will be taken such as hourly, once during the shift, once a week, once from each lot or batch, etc. and decide how many samples will be either inspected or tested. When there are no measurements involved but an item or a process is evaluated by observation and judgment, it is called “inspection.” When a characteristic or property is determined by subjecting an item or a product to a set of physical, chemical, environmental, or operational action and conditions, it is called “testing.” If testing is called for, a test method to be used should also be specified.
d. Establish standards of performance –These could be the specifications, customer requirements, etc., which will help determine whether the characteristic under consideration is acceptable or not. Specifications or customer requirements can be in the form of numbers, sketches, photographs, etc. For appearance related requirements, it is best to have photographs of what is acceptable and what is not.
e. Interpret the differences – This means comparing the characteristic or property measured or observed with the requirements, and deciding if there is a difference between the two and whether that difference is acceptable or not. If the difference is not acceptable, move on to the next step.
f. Take action on the difference – Decide what to do if the difference between what is produced and what is required is not acceptable. This decision could be reject, rework, scrap, or simply ship hoping that the customer does not find out this unacceptable difference!
QC focuses on meeting customer requirements that are clearly spelled out, typically through specifications, or satisfying customer needs that are understood by the organization. The control system focuses on achieving sufficient conformity to ensure that the product is saleable or merchantable. The organizations that focus only on QC are characterized by rework, redo, remake, etc. Emphasis is more on ‘corrective’ actions rather than ‘preventive’ actions. The focus is to get the final product ‘right.’ Data analysis tends to be a day-to-day activity with little attention to trends.
Quality Assurance (QA)
Assurance means the act of giving confidence, the state of being certain or the act of making certain. Therefore ‘Quality Assurance’ means assuring through planned and systematic activities that quality requirements for a product or service will be met.
ISO defines quality assurance as “all planned and systematic activities implemented within quality system that can be demonstrated to provide confidence that a product or service will fulfill requirements for quality.” Quality assurance builds on quality control by activities such as developing specifications and performance standards, performing QC activities, addressing customer complaints, etc. Quality assurance typically does not address quality improvement. As the name suggests, under quality assurance, the emphasis is on assurance that the quality requirements will be met. There is more focus on prevention and correction of defects rather than quality improvement. Information gained from customer complaints, customer feedback, quality audits, etc., is used for defect prevention and correction rather than quality improvement.
Quality Management
ISO defines quality management (QM) as “coordinated activities to direct and control an organization with regard to quality.” Direction with regard to quality generally includes establishment of quality policy and quality objectives, quality planning, quality control, quality assurance, and quality improvement.
Dr. Juran, a world renowned quality management expert, puts quality management in business perspective by comparing it to financial management as shown in Exhibit 1.
Exhibit 1
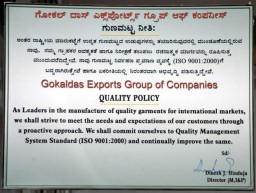
There is hardly a company that operates without a budget, i.e. estimating expenditure, allocating resources, etc. Even with sound and realistic budgets, most companies would be constantly looking out for opportunities to save money by cost and expense control. Even with effective cost and expense controls, most companies put in place various steps to reduce costs and increase profits as the time goes by. Yet, there are companies that operate without quality management, i.e. quality planning, quality control and quality improvement, and wonder why they are not able to compete.
Effective quality management (QM) starts with a quality policy. A quality policy is overall intention and direction of an organization related to quality as formally expressed by the top management. Quality policy should reflect company’s vision and mission. Dr. Juran suggests top management consider the following questions while formulating quality policy.
“What markets do we intend to serve? Within these markets, how does quality affect income? What standards do we need to establish – quality leadership, competitiveness, or adequacy? Shall we go for quality leadership, for a respectable grade, or for what we can get by? Shall we go for building a well-known image around our quality performance? What internal standards shall we set for conduct of the quality function? How shall we divide up the work of achieving fitness for use among the various company departments, among the various levels of supervision, between line and staff, between supervisors and non-supervisors, between the company and its vendors?”
Only after crystallizing the discussion of the above questions can top management establish quality policy, objectives and plans to make the dreams come true.
In order to implement quality policy, it should be translated into quality goals.
Exhibit 2 shows examples of some quality goals.
Exhibit 2
Quality goals should be measurable and achievable (realistic). If quality goals are not achievable or are unrealistic, employees will get frustrated and will quit trying to achieve quality goals. Quality goals may be linked to product performance (such as shrinkage, colorfastness, seam strength, etc.), service performance (on time delivery, complete delivery, size and color breakdown as ordered, packaging as requested, etc.), customer satisfaction, quality improvement, or cost of quality.
In order to achieve quality goals, quality planning is necessary. Quality planning is the process for preparing to meet quality goals. Quality planning refers to allocating resources, defining quality procedures, and selecting quality standards pertaining to a specific product, service or project. Outcome of quality planning is a quality plan. A quality plan is a document or a set of documents that describe the standards (quality requirements); quality procedures (inspection, testing, etc.); resources (types of fabrics and accessories, types of equipment, such as sewing machines, etc.) needed and processes (operations, types of seam and stitches, etc.) to be used pertinent to a product. The standards can be related to workmanship, such as how a finished garment is supposed to look like and/or product performance, such as colorfastness, shrinkage in laundering, seam strength, etc.
Quality improvement is very much a part of quality management. According to Dr. Juran quality improvement projects provide a higher return on investment than virtually any other investment activity. Quality improvement involves either reducing or eliminating things that are wrong with products resulting in customer dissatisfaction and waste (high cost of poor quality). Quality improvement may also mean improving or raising quality level, i.e. reducing % defective level from 5% to 2%.
Typical quality improvement steps are:
(a) Identification of quality improvement project.
(b) Preparing a problem statement – as someone has said “a problem well defined is a problem half-solved.”
(c) Analyzing the symptoms of deficiency or quality problems.
(d) Identifying the root causes – diagnosing the problem.
(e) Addressing the root causes – solving the problem, and
(f) Putting controls in place to hold the improvements.
Those companies that practise quality management treat quality as a strategic issue. Goal/target setting in quality area and management review by top management are on-going activities. The focus is on improving productivity while eliminating waste and rework and enhancing market value. There is an emphasis on continuous improvement. The top management establishes goals against key measures of customer satisfaction and internal performance. The top management provides necessary resources for continuous improvement. The top management involves suppliers very early in defining requirements for joint development. Companies work with suppliers to develop mutual trust, respect, and commitment to customer satisfaction.
While the responsibility for quality management belongs to top management, the attainment of desired quality requires the commitment and participation of all members of the organization.
Choosing an Approach to Managing Quality
Based on a company’s activities, the management can decide whether QC, QA or QM is appropriate.
For example, if you are a contract manufacturer, QC may be quite sufficient because there is no product design and specification development taking place in your company. This is all done by your customer. The customer also defines quality level desired. You are simply cutting and sewing as per the requirements of your customer. Therefore, the emphasis is on meeting customer requirements. A sound inspection system based on statistical sampling and appropriate product testing will be more than adequate. Any quality improvement you might undertake would be related to reducing number of rejects and waste. Typically, under quality control, quality improvement efforts will not relate to product performance improvement, such as shrinkage, colorfastness or strength because the focus is on meeting customer requirements through control of those properties by controlling respective processes and operations.
If you are a contract manufacturer and also make products based on your own designs, then you may want to consider having either QA or QM for your own products and QC for the contract manufacturing products.
If you are a company where you design, develop, manufacture and market under your own brand name, then QM is for you. Zara is a good example of a company having a QM system in place. For a company like Zara, QC or QA will simply not be effective in today’s highly competitive market place.