Creating specialised and engineered garments like knitwear, activewear, swimwear, outerwear jackets, sportswear, rainwear and hikingwear requires a high level of expertise and the seamless integration of technology. This is where Fortis Group, a leading RMG manufacturing organisation in Bangladesh, excels. The group operates factories including Habitus Fashion, KA Design, Quattro Fashion, Fortis Garments and Arrow Fabrics, collectively generating export revenue of US $ 200 million. In an exclusive conversation with Indika Wanigabaduge, CEO of Fortis Group, Team AR delves into the company’s progressive approach to embrace automation and cutting-edge technologies in its garment manufacturing processes. Here are excerpts that discover how Fortis Group has strategically incorporated advanced tools and systems to enhance efficiency, streamline workflows and position itself as an industry leader.
AR: How has Fortis Group incorporated automation in its production processes and what specific benefits has the company observed?
Indika: There are two areas of tech interventions on shopfloor. Automation of sewing process and digitalisation is in our DNA and it’s an ongoing process. We are using it to improve productivity, enhancing line efficiencies. This strategic integration has resulted in streamlined workflows, reduced production timelines, minimised errors and ultimately improved overall productivity. We are one of the few companies in Bangladesh to have implemented highly advanced seam sealing machines and fusing machines (Martin Group) to produce high-end garments such as activewear, sportswear, swimwear and hiking apparel. Our denim unit is studded with sewing automats (Vibemac) such as pocket setters, automatic serging units and side seamers etc. In our product development process, we have been using CAD and CAM since the beginning and now we have switched to 3D which saves at least one month in sample approval process and also helps in huge raw material and manpower saving. The implementation of cutting edge technologies has positioned us at the forefront of innovation, ensuring increased competitiveness. Real-time monitoring software plays a crucial role in helping our production floors across factories make data-driven decisions by providing immediate insights into various aspects of production. AI-driven production software systems track machine uptime, downtime and overall equipment efficiency (OEE). To give you an example, our average OEE has increased by 10 per cent through real-time monitoring, resulting in production efficiency increase of 15 per cent. These systems have also helped us in identifying defects or issues in the production process promptly. Let’s say the defect rate decreases by 40 per cent due to early detection which means our defect rate hovered around 5 per cent before the implementation of real-time monitoring that has decreased to under 3 per cent now. We have also been able to improve our inventory turnover by 25 per cent. Our machine downtime has reduced by 30 per cent ever since we implemented IoT-enabled tools in our factories.
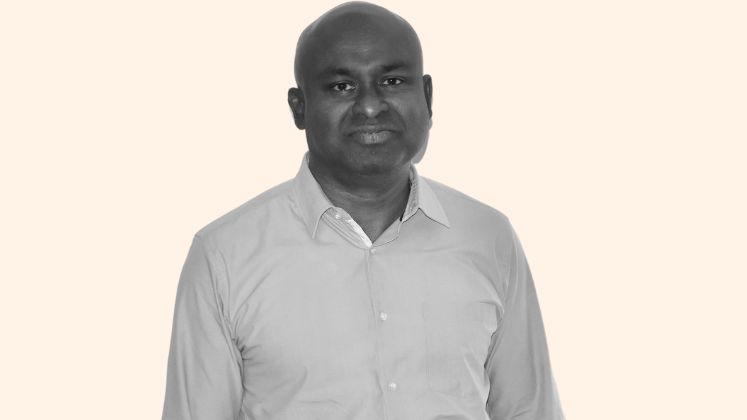
AR: How have the challenges in adopting new technologies been addressed?
Indika: Challenges are many such as ensuring a smooth transition for the workforce, integrating diverse systems and managing the initial investment costs. Implementing such technologies at root level is a long-drawn process.
Ensuring a smooth transition for our workforce during the introduction of new technologies involves investing in robust training programs. We provide comprehensive training sessions to familiarise employees with Indika Wanigabaduge CEO of Fortis Group new technologies, emphasising their benefits and practical applications.
Additionally, we encourage open communication and feedback to address any concerns, fostering a collaborative environment that supports a seamless integration of technology into our production processes. The phased implementation aims to minimise disruptions and aids in strategic financial planning to optimise the return on investment over time.
AR: How do you ensure the quality of the engineered products?
Indika: Implementing a dual-focused approach to worker training is the key. We combine hands-on technical training with a strong emphasis on soft skills development. First, our workers undergo specialised technical training to enhance their expertise in handling critical and high-end products. Simultaneously, we prioritise soft skills such as communication, problem-solving and teamwork to ensure a well-rounded workforce. This comprehensive training approach equips our workers with the technical know-how and interpersonal skills necessary to excel in producing intricate and high-quality garments.
AR: Fortis Group’s factories are LEED certified. How so?
Indika: Three out of our six factories are LEED PLATINUM-certified and we are proud of our achievement. This is achieved through the implementation of various ‘Green’ technologies. Notable initiatives include the adoption of energy-efficient lighting systems, harnessing solar power, implementing waste recycling programs and incorporating water conservation measures. These sustainable practices not only contribute to environmental responsibility but also align with our commitment to operating eco friendly and resource-efficient manufacturing facilities.
The tangible impact of these efforts is evident in the cost savings achieved to date, totalling BDT 11,595,234 Taka (US $ 105,653). One of our significant green initiatives involves solar panels, with a total capacity of 428 kWh. The total energy generated stands at an impressive 210,958 kWh, contributing to a significant carbon avoidance of 788 tonnes. Since 2019, we have consistently demonstrated our commitment by saving equivalent of 1 lakh gallons of water per month.
AR: What are the upcoming technological trends or innovations that Fortis Group is considering for future investments in garment manufacturing?
Indika: Adoption of newer technologies is an ongoing process and we are actively exploring the integration of industry technologies such as lean manufacturing, IoT devices, advanced data analytics and automation, to enhance our garment manufacturing processes. These innovations align with our commitment to stay at the forefront of technological trends, promoting efficiency and ensuring a sustainable and competitive future of the industry.