- The Group identifies Human Resource Development as a Strategic Goal.
- Sets up ‘Village Cluster Adoption Project’ to improve cause of the cotton.
- Takes up ‘Mission White’ to enhance productivity of cotton.
- President Abdul Kalam visited one of its adopted village in 2006.
- Farmers’ Field Schools opened in the adopted villages.
- Nimbua Greenfield Project set up to counter industrial pollution.
- Company trains SC, ST and OBC college students at its training centre.
- Sri Aurobindo College of Commerce and Management and a school opened.
- Eevery factory has a Manav Vikas Kendra for training workforce.
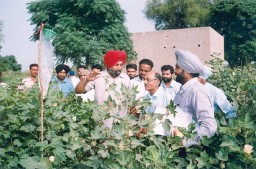
Integrated textile conglomerate, Vardhman was established in Ludhiana in North India in1965, and is involved in the manufacturing and marketing of yarns, fabrics, sewing threads, acrylic fibre and special alloy steel. The group has the largest manufacturing capacity of yarn in the country with over 6,00,000 spindles, and one of the largest fabric weaving plants in India. Vardhman has 19 units all over India; five of these are in Punjab, nine in Baddi in Himachal Pradesh and three in Madhya Pradesh. The company employs 20,000 people in its plants.
“Corporate Social Responsibility (CSR) is embedded in our work culture and has been an integrated part of our philosophy,” indicates D.L. Sharma, MD of the group. “It covers several segments – from the training of potential managers and administrators, to the welfare of cotton growing farmers to concerns about the environment,” he adds. Although the Group is involved in multifarious activities, its main initiatives are towards enhancing employability through technical, attitudinal and cultural training; imparting education; helping farmers by providing them training and R&D support for cotton cultivation; working to improve industrial safety and health; assisting the community with environment protection measures and creating skills in the rural unskilled workforce.
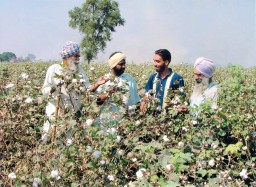
The Group’s most striking social intervention for development has been towards improving the cause of the cotton growing farmers in Punjab. Called the ‘Village Cluster Adoption Project’ (VCAP), this endeavour essentially helped farmers improve the yields of their crops by empowering them with knowledge and information and by providing them with better methods of production.
This was done because it was noticed that till 1999, cotton yield in the State was very low at 286 kgs per acre. This was less than the Indian average of 301 kgs and almost half of the world average at 591 kgs. Cotton crop was, therefore, considered to be a high-cost, high-risk activity plagued with frequent failures, which had thrust the community into a debt trap and led to several cases of suicide by farmers. At this stage, the Vardhman Group, along with other textile companies and some banks took on the task of enhancing productivity of cotton and launched an initiative called ‘Mission White’.
[bleft]An important initiative by the company has been the Nimbua Greenfield Project, which aims to counter industrial pollution when chemical wastes get released into water channels, thrown in the open air or buried to avoid visibility[/bleft]
VCAP began with one village called Nava-Pind in 2003-04. The next year, it adopted another 10 villages. Subsequently 25, 50 and 70 villages were adopted in 2005-06, 2006-07 and 2007-08, respectively. The programme, carried out with the help of specialists from the Punjab Agricultural University and the Department of Agriculture, Government of Punjab, led to encouraging results, with the average yield in the villages increasing to 800 kg of cotton per hectare in 2003-04, while the average yield in Punjab was 400 kg of cotton per hectare, that year.
“VCAP also got a boost when former President Abdul Kalam’s visited one of the adopted villages called ‘Gheri Butter’ at the end of 2006, and his mention of the project on Technology Day,” points out Sharma.
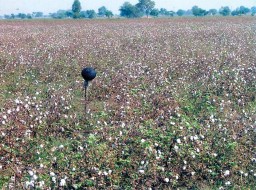
He attributes VCAP’s success to the approach which was based on reaching out to farmers through agriculture experts and trained village scouts, besides educating them about the latest modern techniques and practices for cotton crop. “Farmers’ Field Schools were opened in the adopted villages which gave further impetus to this drive. Free testing of water and soil and inputs for better production also helped. Above all, children were also educated about the benefits of scientific cotton farming by holding camps in their village schools. The various methods that were used paid off; and within six years, the farmers in Punjab rose from the 6th position as a cotton grower in 1999 to the 1st position in 2006-07,” notes Sharma.
The other important initiative by the company has been the Nimbua Greenfield Project, which aims to counter industrial pollution when chemical wastes get released into water channels, thrown in the open air or buried to avoid visibility. Gujarat and Maharashtra have been two States, which have worked to protect the environment. And, Punjab became the next through S.P. Oswal, CMD, Vardhman Group, who volunteered to organize disposal systems in the State and develop a common ‘Hazardous Waste Treatment and Storage Facility’.
“Nimbua in Dera Bassi in Punjab, was selected as the project site for its implementation. And, a company called Nimbua Green Field Punjab Limited (NGPL) was incorporated, which drew its Board of Directors from Punjab’s industrialists, and representatives of the State and Central Governments,” says Sharma. “This private-public partnership works on a ‘no profit no loss’ principle. All secretarial services, including maintenance and audit of accounts, initiation and registration of NGPL as a company, arranging loans from banks and providing commercial and engineering know-how for procurement of equipment were provided by the Vardhman Group,” he further added.
Besides these two major projects, which involved many stakeholders and coordination between many agencies, there has been a focus on training and education of workers as well in the company. “One of our main areas of focus is on training the underprivileged to empower them with skills that can make them employable,” stresses Sharma and adds that the company trains college students from Scheduled Castes, Scheduled Tribes and Other Backward Castes at its training centre in Ludhiana.
In the latest training programme of this kind held in May 2008, it trained about 50 such students during a 35-day training module, which involved skills in public speaking, preparing for interviews, writing CVs, and insights into management principles, the basic tenets of communication and the finer aspects of finance and accounting. This Capability Enhancement Training Programme, organized by the Vardhman Training and Development Centre and the “Affirmative Action Campaign” of the Confederation of Indian Industry, helped about 44 of the 50 students who were trained and got jobs in the industry.
The Vardhman Group’s thrust towards education and training has also led to the setting up of the Sri Aurobindo College of Commerce and Management (SACCM) in Ludhiana, which is affiliated to the Punjab University. “This was done to create a human resource pool for administrative and management positions in enterprises or those who could set up their own businesses as entrepreneurs,” indicates Sharma. The college, spread in over 9.5 acres, has classrooms fitted with modern teaching aids; a computer laboratory with 35 PC stations; internet facility and a library. It also has a career management and placement cell that works closely with the students and prepares them for their careers.
The Group’s social interventions have also spread outside Punjab and reached Himachal Pradesh. When Vardhman first landed up at Baddi in Himachal Pradesh in 1989 for its first plant – Auro Spinning Mills, it found that the village needed a good primary school. So, it opened the Sri Aurobindo Public School in 1996, which became a secondary school in 2005 and is today, a co-educational English medium school affiliated to the CBSE. About 60% of the students are wards of employees working in various factories covering Pinjore, Baroliwala, Baddi and Nalagarh.
“Besides having initiated schemes like Total Productive Maintenance (TPM), Kaizen and Quality Circles for upgrading working conditions, we have also provided our workers with residential colonies along with community centres, ration shops and ‘Play-Way’ schools,” indicates Sharma. The Group has ‘Manav Vikas Kendras’ in every unit where trained faculty members conduct attitudinal programmes for employees in addition to giving them functional inputs.
Various camps, workshops and training sessions addressing social issues like aids, drinking and smoking, savings, hygiene and health are also organized from time to time for workers and their families. These are a part of the on-going initiatives at the group, which lays a lot of emphasis on Human Resource Development, concludes Sharma.