Formulated way back in 1947 by a network of the national standards institutes of 137 countries, the International Organization for Standardization or ISO, as it is popularly known, has over the years created an ISO 9000 family of standards to benchmark quality management that improve customer satisfaction by preventing defects or non-conformities in products and services. Pradip V. Mehta works with Team StitchWorld to conduct the first ever survey of the companies with ISO Certification to understand their motivations and to share their success stories.
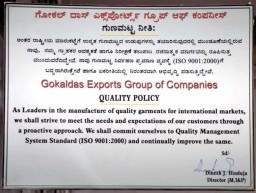
Introduction to ISO 9000 The ISO 9000 standards which broadly make up the current list includes ISO 9000:2005 Quality management system on fundamentals, ISO 9001:2008 Quality management system to assess an organization’s ability to meet customer and regulatory requirements, and ISO 9004:2000 Quality management system guidelines for performance improvement. ISO 9001 was introduced in 1987 and has been revised three times since then: in 1994, 2000 and 2008. The new edition of ISO 9001 is expected to be available in Oct.-Nov. 2008. Even as all ISO standards get reviewed every five years, the objective is to review and reaffirm the same as per current international market requirements.
A company/unit that is going for either registration or certification must show how it addresses the requirements of each clause of ISO 9001. Ultimately, it is up to the company to decide if it wants to seek ISO Certification for the entire company, a particular plant, or a particular product line. Being registered to ISO 9001 means having an accredited independent third party, i.e. a registrar, conduct an on-site audit of a company’s quality management system against the requirements of ISO 9001. Upon successful completion of this audit, the company receives a registration certificate that identifies that the company’s quality systems are in compliance with ISO 9001 standards.
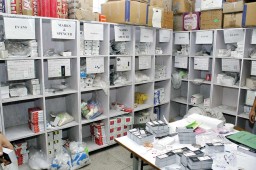
Registration is good for three years from the date it is granted. During this time the registrar can carry out surprise checks once or twice a year, and continued registration depends on the findings of these audits. At the end of three years a renewal audit is performed before the registration is continued.
The ISO 9001 registration process provides a company not only with the opportunity to better understand and anticipate customer requirements, but also improve its understanding of business processes and control them in a logical, systematic way. In addition, it fosters internal discipline leading to streamlined production, reduced cycle times, and quality improvements and reduces paperwork by doing away with forms and reports that do not add any value to the processes or products.
Motivation for ISO 9001 Registration
[bleft]It was indeed heartening to learn that buyer pressure was the least of the concerns for most companies when opting for Certification.[/bleft]
Though many industries have been using the ISO standards as a management tool for a long time, the Apparel industry embraced the concept only in the early 1990s when Delhi-based Opera House and ISEX Fashion in Chennai applied for the Certification in 1993-94 and 1996, respectively. Since then the players in the industry have increasingly shown confidence in the ISO process to manage their companies more effectively.
StitchWorld surveyed industry players that have already been certified on three critical areas – Why, How and Benefits accrued. The findings from the survey covering 20 companies in the Apparel industry has brought forth some very interesting facets of the Certifications and while each company had varied experiences and motivations for seeking ISO Certification, there was unanimity on the results – ‘Systems do improve for better efficiencies’, how much, is different from company to company.
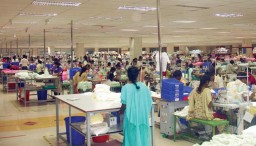
There is no doubt that the motivation to certify for ISO is primarily to achieve quality management system, which is the basis of the Certification. In fact 85% of the respondents indicated the same as top priority in opting for ISO. Interestingly, most companies have opted for Certification of the whole company, though there are some that have chosen to get only the Apparel manufacturing unit or the integrated plant certified.
The finding is not surprising, as the root to any growing organization must have quality management systems in place. There has to be a standard quality policy, quality manual with quality plans and procedures, as also process to monitor quality of products and an organizational structure with responsibilities of individuals defined, as well as adequate resources to implement the quality system.
[bleft]A company should be able to demonstrate that it is not only willing but also prepared to abide by the management principles that determine ISO benchmarks.[/bleft]
Interestingly, the desire for a distinct Effective Tool for Measurement, Analysis and Improvement and Resource and Inventory Management were ranked second and third with 57% and 70% companies opting for each respectively as the motivators to apply for ISO. Other motivators include ‘Corporate image’, ‘Marketing advantages’ and ‘Buyer pressure’ in that order. It was indeed heartening to learn that buyer pressure was the least of the concerns for most companies when opting for Certification.
This clearly indicates that companies are self-motivated to achieve global standards. “ISO Certification does not have direct impact on our business with buyers,” says Vinod Saraogi MD Meridian Apparels, “ISO deals with documented procedures, whereas buyers are looking for Certifications that address social responsibilities. But working by well defined procedures and rules does result in quality standard product,” he adds.
Apparel Industry Experience
Having decided that efficiencies have to be built into the management, a company should be able to demonstrate that it is not only willing but also prepared to abide by the management principles that determine ISO benchmarks. They must continually upgrade on customer requirements and based on that, remain committed to quality with quality objectives and policy in place for customer focus. In addition, it must clearly define responsibilities of its work force, ensure communication and flow of information, hold regular reviews of quality results and base decisions on fact and analysis of data. It must also demonstrate that there is continuous monitoring, measurement, and analysis of processes that have impact on quality.
Once implemented, companies have been seeing good results in areas of manpower utilization, stock/inventory control, rejections and customer satisfaction. While the improvements were in all desired areas listed above the maximum changes were observed in the attitude of the company with increased focus on a positive mindset of the leadership and better teamwork to achieve set goals.
[1] Positive Mindset of Decision Makers/Leaders:
Leaders establish unity of purpose and direction of the organization. They should create and maintain the internal environment in which people can become fully involved in achieving the organization’s objectives. Thirukkumaran, CEO of Esstee Exports (certified in 2003), talking about the change in the mindset of the decision makers said, “Responsibilities and authorities are defined for executives and employees. They know their duties and limits. This has increased the transparency in the organization and has moulded the leadership to take easy and quick decision-making. Consequently, due to the systematic approach and working, employee mindset has also changed and employee turnover reduced from 65% to 35% in the last 4 years.”
[2] Increased Systems Approach by Management:
“Identifying, understanding and managing interrelated processes as a system contributes to a company’s effectiveness and efficiency in achieving its objectives”, says Vinod Saraogi, MD Meridian Apparels (certified in 2001). “We are now doing management review meetings at least twice in a year to discuss effectiveness of implemented quality management system through internal audits and also audit by the Certification body. Directors attend the review meeting so that areas of improvements can be discussed and procedures set for continual improvement.” Manish Mandhana, MD Mandhana Industries (certified in 2006) adds, “Post Certification, the systems are now ‘in place’. Information is available off hand thus making it easier to track orders.”
[3] Improved Employee Turnover and Mindset:
People at all levels are the essence of an organization and their full involvement enables their abilities to be used for the organization’s benefit. As the company begins to implement ISO 9001 standard, it forces all the employees to review the current practices in all areas of operations and improve them. Subsequently, consistency in procedures and practices brings discipline in operations, resulting in reduced variability, which is the key to process improvement. As a company goes through the process, quality and productivity improves. Greater awareness of quality is created at various levels as areas get identified for reducing errors.
T. Chelvi, Management Representative from SP Apparels (certified in 2002) observes, “Clear understanding of responsibilities of individual employees has helped in faster execution of duties. This has subsequently resulted in effective utilization of manpower and other resources such as machinery and materials.”
GM Quality Assurance for Pratibha Syntex (certified in 1999), R.S. Sandhu highlights, “We have noticed better focus in existing employee mindset and increased awareness amongst them. Further, we have also seen noticeable improvements in departments such as housekeeping and internal transport, besides better co-ordination amongst workers who now display an amazing team spirit.”
[4] Systemized Process Approach:
A desired result is achieved more efficiently when activities and related resources are managed as a process. CEO Dhanpal of NSP Tex and Kandhan Knits (certified in 2003) while talking about the changes observed, “Raw material purchases are now being done as per requirement only and so over-booking is avoided. Stocks are now updated and so whenever there is requirement; it is checked against the stock first before the material is ordered.”
“We have achieved planned results in all processes after effectively implementing the PDCA process,” reveals Chelvi. “PDCA means plan, to establish the objectives: Do, to implement, Check, to monitor and measure, and Act for continual improvement.” Thirukkumaran confides, “Due to systematic planning for production, lead time has reduced from 90 to 70 days.” Ravi Dhingra, MD Orient Clothing (certified in 2003) adds, “Correct process approach has resulted in wastage control, less rejection in trims and fabric and more productivity due to uninterrupted supply of material”. S.K. Gupta, GM Cheer Sagar, also shares, “All the concerned staff is maintaining records of each and every piece. Subsequently, this has reduced shortage of garments whilst packing the shipment. After maintaining OCR/FCR reports and cost sheet, we are able to easily find out the stage of rejection.”
[5] Improved Product Quality:
Proper planning is essential to ensure that quality product is produced as per internationally set standards. Improvement in product quality reflects in minimized inspection failures and rework. “Our rejection has reduced by 4%,” says Sandhu. Thirukkumaran adds, “The quality team has been separated from the production team. From raw materials to finished goods, ready to be dispatched through this QA control so that product quality is ensured.” Adds Vinod Saraogi, “The product quality acceptance criterion is defined and procedures are established to achieve quality standards. Quality objectives are defined and monitoring is done regularly to achieve the objectives.”