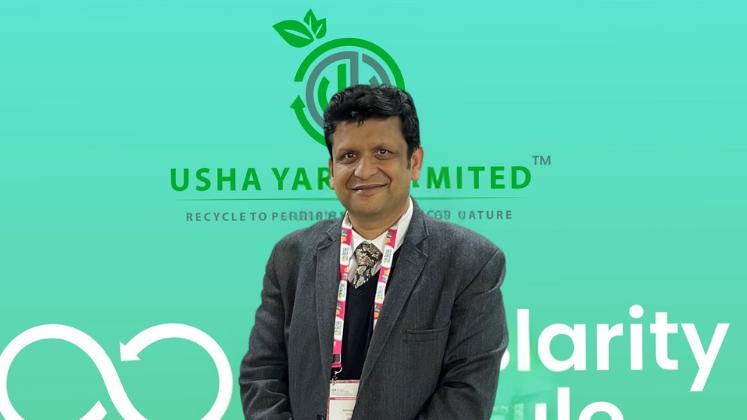
As the consumer demand for sustainable textiles is increasing, fashion brands are discovering the competitive advantage by choosing more recycled content for their garments to help the environment and improve their bottom line. Despite progress, there’s still ample room for improvement, with less than one per cent of textile waste currently being recycled. In this landscape, Usha Yarns stands out as a key player making a significant difference.
With four modern facilities spread across 28 acres near Chandigarh, Usha Yarns annually produces over 18,000 metric tonnes of recycled yarns for global apparel brands. According to Anurag Gupta, Managing Director, Usha Yarns Limited, ‘What is good for the planet is also good for your business.’ With certifications including GRS, RCS, OCS, ISO 14001, ISO 45001, IGBC, Higg FEM, Higg FSLM, SLCP, Intertek Green Leaf, Green Leaf and OEKO, Usha Yarns uses pre-consumer garment cutting waste and polyester made from recycled PET bottles to produce quality-recycled, pre-dyed yarn. Each manufacturing unit features advanced set-up for recycled yarn production tailored to handle specific colour and fibre blends.
Usha Yarns caters to a diverse clientele comprising prominent global apparel retailers across various segments, from mass retail to high fashion, all sharing a common goal of integrating recycled materials into their products. In an exclusive interview with Apparel Resources, Anurag Gupta shares insights into the company’s unique offerings, strategic partnerships and the future trajectory of sustainability.
AR: What sets Usha Yarns apart from its competitors? What is your USP?
AG: As pioneers in the recycled yarn industry, we’ve set the gold standard for quality in India. Our commitment to excellence means we deliver larger lot sizes and higher volumes, offering an extensive array of colours, blends and consistently high quality with 100 per cent recycled content.
Today, our customers rely on us for more than just yarn. They trust that we uphold the highest standards in quality, traceability, chemical compliance, social responsibility and environmental sustainability. With an abundance of verified claims and certifications, we’re proud to exceed expectations and lead the way in sustainable textile manufacturing.
AR: Tell us about some of your unique products and how they contribute to industry’s growth?
AG: Our recycled yarns, branded as Puneh (derived from Sanskrit, meaning ‘again’) include blends of pre-consumer cotton fibres with sustainable fibres like Circulose/Liva Reviva, Recycled Postconsumer Cotton, BCI Cotton, Organic Cotton and Recycled Polyester suitable for knitting and weaving fabrics for garments and home textiles. Our fourth facility commenced operations in November 2023 and this cutting-edge facility is specifically tailored for the development of our latest series of Puneh material blends.
Let me take you through some of our crowd favourites, kicking off with Puneh Popular, a sought-after blend made from 60 per cent post-industrial cotton and 40 per cent post-consumer poly. It’s highly favoured due to its exceptional recycled content of over 98 per cent, certified by the Global Recycled Standard (GRS). With a vibrant palette of more than 120 colours, it eliminates the need for additional dyeing processes, offering versatility in spinning options from coarse to fine counts.
Puneh Signature represents our latest collaboration with Birla Cellulose, featuring a blend of 60 per cent post-industrial cotton and 40 per cent Liva Reviva (from Birla Cellulose). This blend, made from a mix of chemically and mechanically recycled materials, sets new sustainability standards with its mono-material characteristic. Puneh Iconic is another innovative blend resulting from our partnership with Birla Cellulose. It comprises 60 per cent post-industrial cotton and 40 per cent virgin viscose, introducing new sustainability benchmarks with its mono-material characteristic.
Puneh Vintage presents our range of recycled denim yarns, meticulously designed to minimise environmental impact. Crafted from up to 80 per cent reclaimed cotton sourced from discarded denim waste and a minimum of 20 per cent recycled polyester from plastic bottle
waste or virgin cotton/viscose, it offers a rich spectrum of natural denim-like colours.
Puneh Natural embodies conscious creation within the Usha Yarns lineage, blending 60 per cent pre-consumer recycled cotton materials with 40 per cent natural cotton. Lastly, Puneh Exclusive is a collection of bespoke yarns crafted with recycled fibres intertwined with premium materials like fine acrylic, sumptuous wool and the iridescent Angelina fibre. We also offer coloured yarn shade.
AR: Could you share details of your partnership with Birla Cellulose and its objectives?
AG: We’re excited about our partnership with Birla Cellulose. Together, we’re diving into the world of recycled yarns, using a blend of pre-and post-consumer textile waste to make yarns that pack in over 50 per cent textile waste. It’s all about sustainability you see and this recycled yarn blend is a perfect example—it’s a mix of chemically and mechanically recycled textile waste, keeping energy, water and chemical usage to a minimum.
Birla Cellulose is really leading the charge here. It has introduced Reviva fibre, a man-made cellulosic fibre that’s 30 per cent textile waste and 70 per cent wood pulp from FSC-certified forests. What’s appreciable is they’ve got this unique ‘reverse logistics’ chain going on, maximising value addition and really pushing the boundaries of circular fashion. Birla Cellulose has set its sights on supplying 100,000 tonnes of recycled fibre by 2024! As for us, we’re constantly striving to deliver the best in regenerated yarns. With our top-notch in-house research, quality control and production facilities, we’re all about maintaining those consistent global standards of excellence.
Puneh Signature represents our latest collaboration with Birla Cellulose, featuring a blend of 60 per cent post-industrial cotton and 40 per cent Liva Reviva (from Birla Cellulose). This blend, made from a mix of chemically and mechanically recycled materials, sets new sustainability standards with its mono-material characteristic. |
Teaming up with Grasim Industries means we’re in a great position to offer brands, serious about sustainability and circular fashion, the solutions they need. It’s about making a positive impact while staying stylishly eco-conscious and we’re thrilled to be a part of it.
AR: How do you source PET bottles for your production process?
AG: We responsibly procure fibres from PET bottles through certified third-party suppliers and collaborate with garment manufacturers across India who are part of our circularity partnership. This ensures adherence to sustainability standards and traceability in our supply chain.
But it doesn’t stop there. We also recycle cotton fabric waste right in our own facilities using our advanced processes. Of course, tackling challenges like proper waste segregation, maintaining quality and consistency and ensuring traceability are no easy feat. That’s why we’ve partnered with dedicated supply chain experts who are trained to collect and sort waste materials meticulously. Plus, we’re constantly testing and refining our processes to ensure they meet our stringent standards.
AR: How do you ensure the quality and purity of recycled yarns while separating blended fibres? What specific technology is used for this process?
AG: At Usha Yarns, ensuring quality and purity during the recycling process is paramount. We use cutting-edge technology to achieve this goal. Our process begins with advanced digital scanning devices, which meticulously test blends to identify different materials and colours.
To separate colours and blends effectively, we rely on state-of-the-art machinery from known brands such as Rieter, Trutzschler and Schlafhorst. These machines are specifically designed to handle various types of blends and ensure efficient separation.
We’ve collaborated with leading spinning and recycling machine manufacturers to create machines tailored for recycling purposes. Proudly, we’re the first spinner worldwide acknowledged for our utilisation of Rieter’s COM4RECYCLING ROTOR technology and Truetzschler’s TRUCYCLED system. These cutting-edge technologies highlight our dedication to sustainability and superior quality.
In addition to these advanced technologies, our in-house testing facility plays a crucial role. Here, we conduct rigorous quality control checks at every stage of the recycling process. This ensures consistency and maintains the high quality of our recycled yarns across different material colours and blends.
AR: As a sustainable business, what specific initiatives have you undertaken to minimise environmental impact?
AG: Sustainability beats at the heart of our ethos. As a Science Based Target (SBTi) committed company, we diligently monitor our scope 1, 2 and 3 emissions, working towards decarbonisation to achieve net zero by 2050. Joining the Business Ambition for 1.5°C campaign underscores our commitment to halving global emissions by 2030, aligning with the world’s largest and fastest-growing group of companies on this vital mission.
In 2023, our total GHG emissions (Scope 1 + 2) experienced a notable 7.6 per cent reduction. Moreover, we achieved significant progress in reducing the intensity of GHG emissions per tonne of yarn, which dropped by 2.24 per cent. The intensity of CO2 emissions per crore of revenue also decreased substantially by 47.69 per cent.
Our commitment extends to optimising energy usage in our day-to-day operations. At Usha Yarns, energy conservation is an ongoing process. From installing LED lights to fixing air leakages and utilising solar panels, we employ practical methods to minimise energy consumption. Over the past three years, our efforts have led to a remarkable reduction in energy by over 44 per cent and energy per tonne of production by 17 per cent.
We ensure the legitimacy of our recycled materials through the Global Recycling Certificate, maintaining compliance across various aspects. Employing tools like the Higg MSI and conducting Life Cycle Assessments (LCAs), we integrate Usha recycled fibre into the Higg Index materials library, allowing brands to assess its environmental impact. Additionally, we’ve transitioned to a resource-efficient dry process for producing dyed yarns, eliminating water and chemical usage entirely.
Our commitment to sustainability also encompasses the well-being of our workers. Through systems like Hazard Identification and Risk Assessment (HIRA) and robust fire prevention measures, we prioritise the safety and security of our workforce.
AR: What is your perspective on the sustainable products market in India and where do you foresee its trajectory?
AG: The sustainable products market in India is experiencing a significant upswing and the outlook is incredibly promising. This growth is fuelled by a multitude of factors, including heightened consumer awareness regarding environmental issues, proactive government initiatives promoting sustainable practices, the increasing emphasis on corporate social responsibility, ongoing innovations in eco-friendly technologies and the surging international demand for sustainable products.
As these forces continue to converge, India is poised to emerge as a frontrunner in the global sustainable fashion and textiles arena. With its rich history in textile production and a growing ecosystem of sustainability-focused businesses, India has the potential to play a big role in shaping the future of the industry. By capitalising on its strengths and embracing sustainable practices across the entire value chain, India can not only meet the growing demand for eco-conscious products but also set new standards for sustainability worldwide.
We’re also working on new sustainable material blends and collaborating with innovators in traceability and chemical recycling to process blended and post-consumer waste and even complex waste streams more efficiently.