Making dress shirts with 100% cotton fabrics with finer counts is very different from making casual shirts, which invariably poses a challenge for manufacturers. Special precautions need to be taken during the making of collars and cuffs. One is often not aware about the rationale behind this need nor is one clear about related technological possibilities. As cutting operations can be automated to a reasonable extent, selection of right interlining, fusing machine and correct operating procedures is the key to success, as also the selection of appropriate sewing and ancillary equipment. In a two-part series, Apparel Online inter-acted with some world-renowned experts in this area to collate glimpses of technologies available and ‘best practices’ followed the world over.
In the first part, three experts will discuss about the pattern engineering, the interlining and fusing process and second part two experts will discuss the sewing technology and processes. While the idea is to provide knowledge and information to our readers, the brand and model numbers are only indicative.
Pattern Engineering
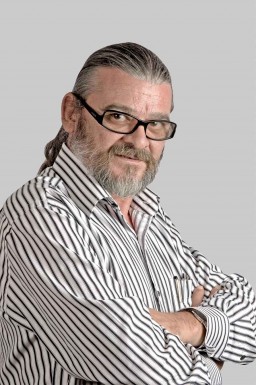
When we talk about a classic shirt with irremovable collar bone, the collar making process becomes a bit technical compared to the casual shirts. The collar making process begins at the pattern stage, in order to get a correct position on the body. The appropriate collar-band shape gives the collar a perfect look, which is why it is important to understand the anatomy of the human body.
The heart shape is ideal for the neck of this kind of shirt. Diagram 1 clearly demonstrates this fact. To get the appropriate design of collar-band, the two curbs between the collar-band and front neck shape (E zone) must have the same shape in order to create a consistent traction of collar on collar-band. The same effect must apply between the band and the neck shape on the front area (D-F/N-M) as well as on the back though far less prominent (G zone, refer Diagram 1). Another critical point is the shoulder, where the curve of the band collar changes direction and converges in the opposite direction.
The aspect of folding a shirt and avoidance of twisting effect is also dependant on the shoulder point. In general we identify the shoulder point at a degree of neck circumference. It is important to match the collar-band shoulder point with body (F-M) during the sewing process.
The fabric and interlining are the most important points which one should look at before starting the fusing and sewing process. In most factories we see block collar cutting, and after fusing and sewing the extra fabric is cut off, which is loss of both material and production.
It is strongly recommended to cut the fabric perfectly according to one’s own pattern. The pinning table is one of the most efficient methods in order to get perfect matching, but one must identify and choose the matching point according to the fabric repeat.
Fusing Process
Fusing collar and cuffs have two different but important technical aspects:
1. Type of Fusing Machine
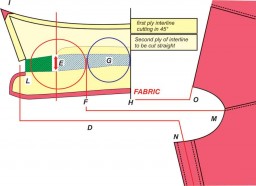
The choice of the fusing machine is important; after identifying the production need, one should decide between a machine with belt or by vertical pressure, which, is the best method in order to avoid elongation. Unfortunately this kind of machine has a small working space and the bigger ones have inconsistent pressure over the various portions of the fusing area.
A machine that has continuous input by belt is recommended, but the collar must be positioned across the belt in order to avoid elongation.
Very few brands of fusing machines have a solution to this kind of work, but some of them are excellent and technically upgrade their machines constantly.
2. Quality of Fusing Interlining
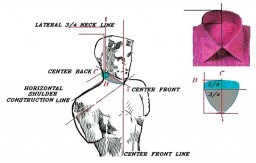
The quality of the interlining is as important as the quality of the fusing machine. The supplier must give you all the technical information regarding temperature, pressure and time for different types of interlinings. Testing the interlining is absolutely important on each type of fabric.
It must be tested for the filling aspect; but one should also check the quality of glue and its uniformity. The major defect in this matter is bubbling, but this is not always visible on the finished garment as it appears only after a wash.
Selection of Interlining
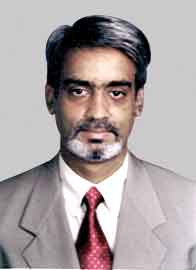
Generally, men’s premium dress shirts use superfine fabrics like 100% combed cotton-2/100’s, gassed and mercerized yarn using superior cotton like Egyptian Giza or American Supima, etc. It gives a very soft, smooth and shiny look to the fabric. One has to be very cautious while selecting the interlining for this fabric.
The moisture content of approx. 8% in 100% cotton fabric will influence fusing temperature setting and adhesive selection. The temperature to be set is approx. 15-20 degrees Celsius higher than the glue line temperature recommended by the interlining supplier. HDPE (High Density Polyethylene) adhesives are used which have nil or very little affinity for water and are least affected by the steam formed during fusing. The washing conditions to which these shirts are subjected to as well as the life expectancy of an expensive shirt, influence selection of the HDPE adhesive for strong bond strength.
The yarn count (or diameter of yarn), its density and twist decide the dot size of adhesive and the fusing pressure. This also gives an idea about the softness, or bending properties of shell fabric. This helps in deciding the weight (GSM) of base fabric of interlining, its construction – i.e. woven, knitted or non-woven and surface texture (handfeel). Woven interlining always gives stiff handfeel, which goes against the basic nature of shell fabric. Hence, to retain or enhance the softer and fuller handfeel, non-woven interlining is better than the popularly used woven interlining.
Recommendation: Vilene 85-100% Polyester fibre based 85 GSM waterjet bonded interlining with very good volume/handfeel for extra bounce/body.
HDPE adhesive – 180 dots/sq. cm. calendared finish gives very smooth surface and there is no impression of any glue dots visible on fine fabrics. At the same time it gives very strong bond strength.
Fusing Conditions: Dial
temp setting – 160-165
degrees Celsius
Glueline temp: 145 degrees Celsius
(tested and set by thermo papers)
Pressure: 2-3 kg/sq. cm.
TIME: 12-13 sec
Construction
Single layer fused top collar and neck band – the lining is cut length-wise and never in the bias direction. The lining is cut by direct or band knife by using a pattern 1-2 mm smaller than the shell fabric pattern. The collar point is reinforced by using an additional patch-as shown in the picture. The interlining components are placed properly on the back side of the fabric and fixed temporarily by the tip of a hand iron at regular intervals. This is also referred to as spot welding.
Fusing Preparation: The fusing machine is thoroughly cleaned before starting, particularly the belt, pressure rolls and scraper blade. The machine is heated to around 100 degrees Celsius and a belt cleaning spray is used to clean any glue stains on the belt and pressure rolls. The pressure supply line is checked for any accumulated liquid. The pressure rolls are checked for any unevenness or gaps in the roller nip. The machine is set at 3 kg/sq. cm. and a belt running speed (dwell time) of about 13 sec. The temp on the dial is set at 160-165 degrees Celsius. These preparatory steps are very important for ensuring good fusing result.
Non-woven interlinings are justifiably the best suited for premium dress shirts.
Non-woven interlinings are very light and soft as compared to wovens. Hence it retains the light and soft texture/handfeel of shell fabric. It does not add to the thickness or stiffness of outer fabric. Vilene 855 recommended for dress shirts are bonded together by water jet, hence it has very soft handfeel and body. It adds more bounce to the fused fabric.
Woven interlinings on the other hand are heavier, thicker and rigid. After fusing, they add thickness and stiffness to the fused component. Due to this added thickness on the collar point it is never as sharp as one gets in non-woven interlinings.
HDPE adhesive has a high melting point hence the glue is unaffected by higher washing conditions.
Roller fusing press gives better penetration than any flat bed press. Pneumatic pressure gives very uniform pressure precluding delamination.
Fusing ‘The Right Way’
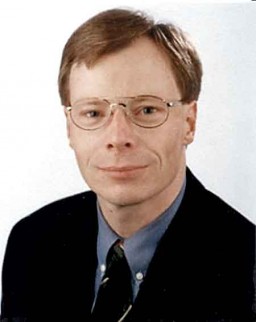
Correct fusing can only be achieved by the following rules:
Absolutely reliable fusing equipment regarding temperature, pressure and speed.
Fabric-friendly fusing by avoiding shrinkage, shading effect or damage of the fabric surface structure.
Individual heating & pressure concepts.
50/50 glue penetration between interlining and shell fabric for utmost bonding.
Continuous fusing machines have lot of advantages as they allow continuous loading of the machine by a number of operators’ independent from each other.
Beside collars and cuffs, front placket can also be fused. By intelligent pressure systems, a similar high-pressure level as given by hydraulic systems can be achieved.
The output of continuous machines is normally higher than hydraulic presses. Today, chemicals used for glue are not made for double passing; one time fusing must be enough to lead to a good result. The glue and its ingredients are really high-tech and react very fast and reliably in case the fusing machine provides the correct temperature and pressure.
Continuous Fusing Machine Temperature
The heating concept is most important, with the possibility for individual temperatures for the interlining and fabric sides, as the thickness of the interlining and fabric has different temperature demands. A clearly defined upper and lower heat zone, in a curved design, to assure a good heat transfer allows control of the glue dot penetration into the shell fabric. A lower temperature from the top, i.e. the interlining side and a higher temperature from the bottom, i.e. the shell fabric side to assure utmost glue spread is recommended.
The allowance of temperature difference between set and actual temperature should not be more than +5 degrees Celsius. This is important to avoid strike through or strike back to the conveyor belts. One should use unique heat technology which allows an even temperature all over the heat zone, to avoid a cool down of the glue causing a spread of the glue dot which leads to a hard handle and low bonding, as the glue, instead of diving into the fabric is spread on the surface of the shell fabric. Fast reaction of the thermostat of the fusing equipment is a must, as temperature swinging will lead to weak bonding and bubbles after washing. Usually the fusing temperature should be the highest applied during the shirt manufacturing process. In case of longer duration high temperature supply while fusing, re-melting of the glue is likely and this will have a negative impact on the bonding.
Pressure
Pressure is the most underestimated factor when it comes to fusing. A large number of tests together with the world leading interlining suppliers offer three concepts of pressure systems.
Standard pressure system is good for all applications of average fabric and interlining, the so called “work horse” among the pressure systems can be used for all major shell fabric and interlining types.
– Double pressure system has two independent working and adjustable pressure systems that allow a pressure supply according to any requirements of the shell fabric and interlining. The first pressure system is the so-called “hard pressure system”, good for all applications where a higher specific pressure is needed, for example dress shirts US $ 100 or US $ 150 (high spun yarn).
The second pressure system is the “soft system”, good for casual shirts with a non-woven interlining, or sensitive fabrics where the specific pressure should be low. Both systems can be used in combination or alone. Fully independent pressure can be set between the systems from zero to maximum.
– FLEXO pressure system is the first pressure system and which is an air-inflated roller and works independent from fabric thickness. Thick and thin fabric can be fused at the same time with the same pressure supply. Specially recommended for ladies outerwear and high sensitivity fabrics. Single and sandwich parts can be fused at the same time too.
Control functions
As we know, fusing operations fall in the category known as “bottle neck” operations on the factory floor. It is very important that any technical problem is indicated by the machine itself. We do that within the control panel using a built-in diagnostic system. Audio and visual signals can indicate problems and allow the technician to keep downtimes as short as possible.