LaLaLand Production & Design, California’s largest shoe manufacturer, known for working with brands like LVMH, Gap and Amiri, has partnered with Elastium, a Los Angeles-based 3D-printing start-up that created the world’s first fully 3D-printed foam shoes.
Together, they aim to revolutionise the footwear industry with a new Hybrid production model that combines cutting-edge 3D-printing technology with traditional mass manufacturing.
This innovative collaboration offers footwear brands a faster, scalable and sustainable solution – no minimum or maximum order quantities, faster concept-to-market timelines and reduced initial investment costs by up to 80 per cent. Their first product, the Orca sneaker by ELSTM, debuts this week from LaLaLand’s Los Angeles factory.
The partnership addresses major challenges in the footwear industry, such as complex supply chains, high upfront investments and the need for more localised, sustainable production.
Robert Karklinsh, Founder of Elastium, explains why his start-up decided to empower traditional manufacturing instead of declaring war on it. He says, “For years, there has been a belief that 3D printing and other advanced technologies would revolutionize footwear by replacing traditional manufacturing.,” adding, “For me as an engineer and designer, the idea of 3D-printed shoes grown like potatoes in 3D printer farms is fascinating. But the market doesn’t move on what engineers or designers think – it moves on what consumers demand. And consumers demand far beyond fully 3D printed “potato shoes”, which are seen just as another trend rather than a revolution.”
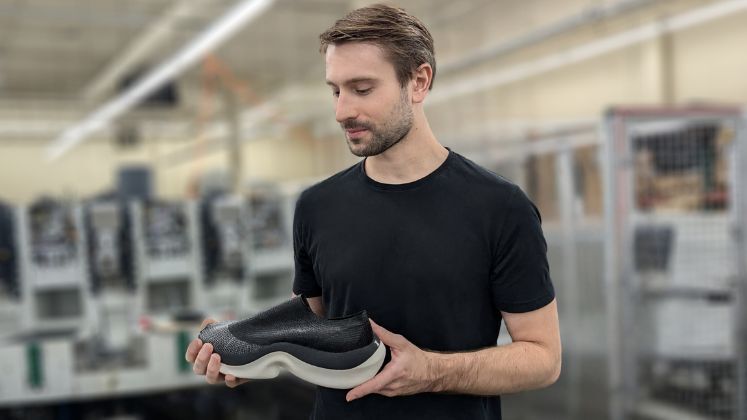
He further averred that the actual revolution towards localised production can be only achieved by putting the consumer in the center of it and integrating all kinds of technologies and craftsmanship into breakthrough products that fascinate consumers rather than designers.
It’s pertinent to mention here that the No-Minimum-and-Maximum-Order-Quantity (No-MMOQ) Hybrid production model allows brands to launch new designs with as few as one pair, utilising advanced 3D printing technology, while seamlessly transitioning to mass production if needed.
Elastium’s proprietary 3D-printed foam, with over 75 per cent energy return, offers superior cushioning and performance compared to traditional materials like EVA. This model enables brands to innovate faster while maintaining quality and cost efficiency, positioning the partnership as a game-changer for the industry.