The traditional method adapted by majority of factories for bottom/sleeve hemming operations includes picking up component, placing, aligning, manipulating, positioning, sewing followed by manipulating and guiding to complete the operation. Practically only one machine can be assigned to one operator.
Both sleeve hemming and bottom hemming can be done either at the flat (prior to stitching) or tubular stage. Flat bottom hemming is necessary for T-shirts with side slits, while circular bottom hemming is done on T-shirts without side slits. Sleeves can be hemmed first using automated workstation followed by side seam operation thereby increasing hemming efficiency, but manufacturer should keep in mind that backlatch device should be used for such side seam operation. If side seam is done first, followed by sleeve hemming in circular shape, then no workstation can be used for sleeve hemming operation.
Integrated automatic hemming units drastically improve production and help in deskilling difficult hemming operations, wherein the operator’s task is limited to feeding/loading. It also ensures consistent lap joint by minimizing human intervention.
In addition, integrated work units offer opportunity for hemming to be designed as ‘external task’ as against ‘internal task’ in sewing line, which can help to minimize set-up time. Global brands like Pegasus, Sahl International, Sicama and Atlantic Attachment Company (AAC) have products in their portfolio for such operations.
Exhibit 1.1: Total cycle time and production rate for integrated bottom hemming units along with manual process time |
||||||||||
Bottom Hemming Operation | ||||||||||
Sl. No. | Brand | Machine serial No. | “Pick, fold & align (in secs.)” | Sewing (in secs.) | Dispose (in secs.) | Total actual time taken (in secs.) | Average single cycle time with allowance | Prod/hr. | “Prod./hr . X No. of machines manned” | “Prod./shift” |
1 | Pegasus | MHG 140 | 6 | 6.2 | 2.5 | 14.7 | 17.64 | 204 | 204 | 1633 |
2 | Pegasus | 342 | 3 | 3 | 2.7 | 3 | 3.6 | 1000 | 1000 | 8000 |
3 | AAC | 213 | 3 | 3 | 2.9 | 3 | 3.6 | 1000 | 1000 | 8000 |
4 | Sahl Int | BSA 920 | 4 | 16 | 1 | 17 | 20.4 | 176 | 529 | 4235 |
5 | Manual operation time (Pick + Fold + Sew + Dispose) | 29 | 34.8 | 103 | 103 | 824 |
A conventional bottom hemming machine comes in a two or three needle version of a flat or cylindrical bed interlock machine. They are completely manual in operation, where almost all tasks viz. picking up, place, align, manipulate, position, guide, dispose are manually performed, thus necessitating the use of skilled manpower. In addition, since one machine is manned by a single operator, it leads to poor manpower utilization.
All sewing operations can be broken up into three steps, such as loading, sewing and unloading. Loading involves picking up the fabric components by one hand/two hands, placing/aligning/folding/matching and sliding below the presser foot. Sewing involves sewing needle movement and occasional stopping of needle movement for guiding/aligning/matching/measuring/pivoting till the sewing cycle is complete. Unloading is the disposing of the sewn piece by sliding/flipping/folding to arrange the pieces in order once the thread is cut. Picking up one ply of fabric component from a stack of cut pieces is the most difficult while considering automating the process. Therefore, most of the sewing automats follow manual loading by operator and sewing and unloading steps are completely automated without any human intervention.
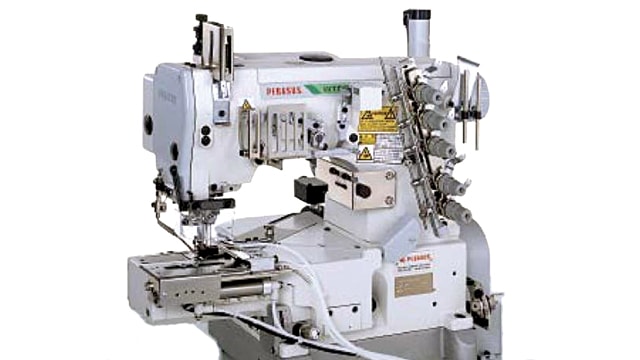
On the other hand, newer machines have direct or servo drive system against the traditional V belt transmission. They are also equipped with electronic or pneumatic bottom and top trimmer and oiling can be eliminated by adapting dry head technology. With the use of control panel, in-built resistance to voltage fluctuations, noise and vibrations are made possible. These machines are also equipped with differential feed, wherein it is possible to finely adjust the differential feed amount to a best-suited value for the material being used.
Exhibit 1.2: Total cycle time and production rate for integrated sleeve hemming units along with manual process time |
||||||||||
Sleeve Hemming Operation | ||||||||||
Sl. No. | Brand | Machine serial No. | “Pick, fold & align (in secs.) (Processing Time)” | Sewing (in secs.) | Dispose (in secs.) | Total actual time taken (in secs.) | Average single cycle time with allowance | Prod./hr. | “Prod./hr. X No of machine manned” | “Prod./shift” |
1 | Pegasus | SOH-541 _x000D_ W/o Stacker | 3 | 2.5 | 2 | 5 | 6 | 600 | 600 | 4800 |
2 | Pegasus | SOH-342 _x000D_ W/t Stacker | 2.5 | 2.5 | 1 | 2.5 | 3 | 1200 | 1200 | 9600 |
3 | AAC | 211 M | 2.7 | 2.5 | 1 | 2.7 | 3.24 | 1111 | 1111 | 8889 |
4 | Sicama | SAS _x000D_ W/o Stacker | 3 | 3 | 2 | 5 | 6 | 600 | 600 | 4800 |
5 | Manual operation time (Pick & Fold & Sew) (For Single Sleeve) | 15 | 18 | 200 | 200 | 1600 |
Technology behind automated bottom hemmer
Automates for bottom and sleeve hemming operations are available in three variants: semi-automatic units for hemming operation on tubular and flat components; integrated sewing units for hemming flat components and tubular components. Features of all three variants have been discussed in detail below.
w Semi-automatic units for hemming operation on tubular and flat components
Following MHG series from Pegasus cater to the above requirements
a. MHG-111 : Bottom feed type (3 Needle)
b. MHG-131 : Variable top feed type (2/3 needle)
c. MHG-140/141 : Variable top feed with fabric trimmer type (2/3 needle)
These are semi-automatic units targeted at deskilling difficult hemming operations and also help in improving workforce utilization. Essentially they are cylinder bed, interlock stitch machines with fabric trimmer. The feed type can be selected from bottom feed & variable top as per the requirement. These machines are useful for hemming tubular components (bottoms) and flat sleeves made of light to medium weight fabrics, such as T-shirts, polo shirts and similar garments. The machine is equipped with automatic open-close pneumatic hemming guide which eliminates the need to fold the fabric. The unit folds and hems the fabric, hence operator’s task is limited to hold the fabric. The guide automatically opens and closes during sewing. This easy to use unit significantly reduces the work performed by the operator. The machine is therefore claimed to provide consistent quality of overlap joint. The guide can be easily removed to be used for other operations. The machine permits hem widths from 15 mm to 40 mm. Tubular goods with circumference up to 360 mm can be hemmed.
One of the common problems with bottom hemming of tubular materials is inconsistent amount and accuracy of overlap stitch which depends on the skill of the sewing operator. The automated workstation detects the beginning of stitch and stops automatically with pre-determined overlap amount.
Integrated sewing units for hemming flat components
These are fully automatic integrated units designed for flat hemming operation that help in automating the manual task and de-skilling a difficult operation such as hemming flat sleeves or hemming bottoms of T-shirts, polo shirts and similar garments. The machines help in producing products with consistent quality and improve labour utilization. The operator’s task is limited to loading the fabric component on the guide/feeder. The unit completes sewing and stacking while forming a clean finished hem. Following major global brands cater to this segment:
Exhibit 1.3: Improvement in bottom hemming operation with respect to conventional manual bottom hemming operation |
||||
Bottom Hemming Operation | ||||
Sl. No. | Machine name | Machine serial No. | % improvement in average cycle time | Average production/hr. x No. of m/c manned |
1 | Pegasus | MHG 140 | 49% | 204 |
2 | Pegasus | 342 | 90% | 1000 |
3 | AAC | 213 | 90% | 1000 |
4 | Sahl | BSA 920 | 52% | 643 |
Pegasus-SOH-342, an integrated sewing unit for hemming flat sleeves and bottoms: The unit is equipped with 2/3 needles, and is a flat bed, interlock stitch machine. It has a variable feed system with thread watcher system and the operator’s task is restricted to loading the fabric component on the feeding guide. The unit automatically performs the hemming operation followed by trimming and stacking of hemmed panels. The unit ensures a significant improvement in production.
Exhibit 1.4: Improvement in sleeve hemming operation with respect to conventional manual sleeve hemming operation |
||||
Sleeve Hemming Operation | ||||
Serial No. | Machine name | Machine serial No. | % improvement in average cycle time | Average production/hr. x No. of m/c manned |
1 | Pegasus | SOH-541 | 67% | 600 |
2 | Pegasus | 342 | 83% | 1200 |
3 | AAC | 211 M | 82% | 1111 |
4 | Sicama | SAS | 67% | 600 |
Pegasus SOH series of integrated sewing units for hemming
Pegasus-SOH-531(3 needles)/SOH-541(2/3 needles), an integrated sewing unit for hemming flat sleeve
The unit is equipped with variable top feed, flat bed interlock stitch machine. It performs hemming operation on flat sleeves of T-shirts, underwear and similar garments. The equipment automates and deskills difficult hemming operations. The operator’s task is restricted to loading the fabric component on feeding guide. The unit automatically performs the hemming operation followed by trimming and stacking of hemmed panels. It ensures a significant improvement in production. The variable top feed interlock stitch machine is claimed to ensure positive and neat feeding of fabric, which prevents twisting during hemming operation. Hem width varying from 20-30 mm is possible.

Atlanta Attachment Co. Inc. – Model 213, an automatic 2 needles hemming unit for sleeves and bottoms
The Atlanta Attachment Company’s high speed automatic two-needle cover stitch hemming workstation is a versatile unit for hemming sleeves and bodies. It is equipped with two stackers, return conveyor and fold in half stacker. It is an electronically controlled workstation consisting of a conveyorized downturn hemming apparatus with two-needle bottom and/or top cover stitch sewing head. It is equipped with electronic motor, automatic edge trimmer and self-contained waste disposal unit. The operator’s task is limited to loading parts on edge guide/conveyor and initiating sewing. The unit continues sewing as long as parts are placed on the conveyor within a specific distance. The sew cycle stops as soon as the machine detects an empty feeder. Rated output for sleeves is approximately 1,950 pieces per hour, and for bottoms, it is approximately 1,260 pieces per hour, depending on material and size of parts.
Sleeves can be hemmed first using automated workstation followed by side seam operation thereby increasing hemming efficiency, but manufacturer should keep in mind that backlatch device should be used for such side seam operation.
Atlanta Attachment Co. Inc. – Model 211M, an automatic 2/3 needles hemming unit for sleeves
The Atlanta Attachment Company’s high speed semi-automatic cover stitch hemming workstation is a versatile unit for hemming sleeves that can be equipped with either two or three-needle sewing head. It is equipped with automatic trimmer and stacker. It is equipped with electronic motor, automatic edge trimmer and self-contained waste disposal unit. The operator’s task is limited to loading parts on edge guide and initiate sewing. The unit continues sewing as long as parts are placed on the conveyor within a specific distance. The sew cycle stops as soon as the machine detects an empty feeder. Rated output for sleeves is approximately 1,125 pieces per hour, depending on material and size of parts.
SICAMA-SAS, an automatic/de-skilling workstation for hemming flat sleeves
SAS is an automatic hemming guide for flat sleeves of T-shirts, polo-shirts and similar products. It is suitable for light to medium weight fabrics. The operator simply places the fabric on the feeder and the unit automatically performs hemming producing consistent uniform high quality products. For better performance, SAS is recommended to be installed on the flat interlock machine with the upper feed function.
Integrated sewing units for hemming tubular components
These are fully automatic integrated units designed for hemming tubular products. They help in automating and de-skilling difficult hemming operations for tubular goods. The operator’s task is limited to loading the fabric component on the guide/feeder. The unit completes sewing and disposing while forming a clean finished hem. They offer unique advantage wherein multiple work units can be assigned to a single operator. This significantly improves productivity and manpower utilization. Sahl International is one such brand which caters to this market.
Sahl International BSA 920 SA Automatic circular hemmer
Sahl International, BSA 920 SA Automatic circular hemmer: The BSA 920-SA automatic circular hemmer is especially developed for automatic hemming of tubular articles such as bottoms of T-shirts, underwear and sportswear. The machine is equipped for twin needle hemming, and can be adjusted for hem widths between 15 and 32 mm. The equipment is available with or without stacker. It is equipped with top feed sewing head with 200 – programme functions, thread break sensors and height adjustable stand. The EKF electronic edge guiding system from SAHL-ISM ensures fully automated sewing including the end of ‘seam cycle’ facility (sewing-over and thread-trimming). The company’s rated output is 3,600-4,200 pieces for a single operator manning two machines with a stacker for eight hours shift.
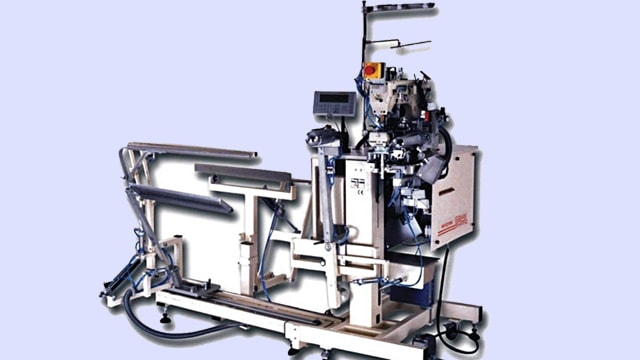
Conclusion
Use of integrated automats for sleeve and bottom hemming operations help in deskilling the difficult operations and minimize human interference. The experiment has demonstrated the improvement in cycle time and productivity with respect to conventional sleeve and bottom hemming operations. The high production rates permit assigning the operator other activities/tasks, thereby improving manpower utilization. Integrated automats are beneficial for bulk manufactured goods such as standard Tee and Polo shirts which permits long continuous runs. In case of small orders and fashion products, line plan can be designed to utilize these machines as an external task rather than an internal task, which can help in minimizing the set-up time.