Rib attaching with the body of sweatshirt is generally perimeter sewing operation. Rib attaching in sweatshirt requires folding of rib into half and closing the rib to band before attaching to bottom. As the rib fabric is having greater elastic behaviour than body fabric, the rib is created as band, loaded to the machine, pre-stretched and then attached to the body of the sweatshirt. Once the rib-band is pre-stretched, the sewing operation basically joins body perimeter with rib perimeter with edge alignment and closes the seam with overlap. As the operation does not require any other alignment/adjustment, the operation can be automated to single burst sewing with pre-defined overlap amount.
Conventional method for bottom rib attach operation
The conventional bottom rib attach operation is completely manual, where the operator performs all the tasks like band and body panel handling, positioning, sewing and disposing. This necessitates use of skilled manpower, thereby increasing human dependency and chances of human induced errors. The observed average cycle time for bottom rib attach operation on conventional machines is indicated in Exhibit 1.1.
Technology behind automatic bottom band attaching operation
Pegasus and Atlanta Attachment Company are prominent brands in the market, offering automatic bottom rib attach workstations. Pegasus model EXT5104/433-4/KS/FR151 is a semi-automatic workstation which assists an operator in guiding and manipulating the tubular panel during the sewing cycle. Operations of band/body panel loading, withdrawal and stacking are manually performed by the operator. Model 1278-6 from Atlanta Attachment Company is an automatic integrated workstation, where operator’s task is limited to loading of panel to the holding clamps. The machine performs material positioning, sewing and stacking operation on its own.
Pegasus – variable top feed cylinder bed overedger: model EXT5104/433-4/ FR151
Model EXT5104/433-4/FR151 from Pegasus is a semi-automatic cylinder bed 3-thread overedger equipped with variable top feed mechanism. The machine can handle light- to medium- to heavyweight fabrics. The differential feed ratio can be adjusted via lever that can be adjusted intermittently during sewing. The machine has a fully automatic lubrication system. The FR in the model number indicates that the machine is equipped with fabric tensioner device which holds the fabric and elastic during sewing cycle of tubular garments. The operator’s task is restricted to folding the bottom band and loading the band and tubular garment panel to the tensioner device. The device expands and assists the operator in manipulating the fabric tube during the sewing cycle, thereby deskilling the job and reducing skilled operator’s dependency. Withdrawal of stitched garment from the tensioning device and stacking is performed manually by the operator. Productivity of the machine is 267 pieces per hour or 2,133 pieces per shift of 8 hours (refer Exhibit 1.1).
Exhibit 1.1: Bottom Rib Attach Operation |
||||||||
Machine Make | Machine Model/Serial No. | Machine/Operation Type | Loading for stitching (with allowance) | Sewing (with allowance) | Unloading after stitching (with allowance) | Total Average Cycle Time (Secs) (with allowance) | Prod./Machine/Hr. X No. of machines manned (Pcs) | Prod./Shift (Pcs) |
Juki | DDL 5550N | Bottom Band Attachment | 31 | 31 | 116 | 929 | ||
Pegasus | EXT5104-04/433-4/KS/FR151 | Semi Automatic | 14 | 14 | 267 | 2133 | ||
Atlanta Attachment Company 1:1 Configuration | 1278-6 | Automatic | 7.65 | 7.2 | 2 | 14.9 | 242 | 1939 |
Atlanta Attachment Company 1:2 Configuration | 1278-6 | Automatic | 7.65 | 7.2 | 2 | 14.9 | 457 | 3657 |
Atlanta Attachment Company – Automatic Rib Knit Band Setting Station: Model 1278-6
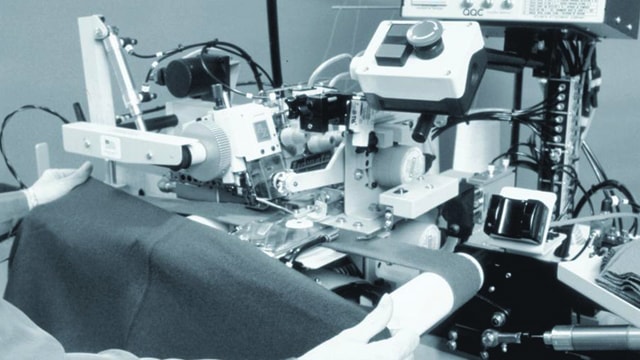
Model 1278-6 from Atlanta Attachment Company is an automatic workstation for sewing circular bottom rib on sweatshirts. This unit incorporates a cylinder arm overlock sewing head with vacuum thread trimmer giving a precise cut. The machine utilizes sewing heads from Pegasus, Juki or Union Special. The workstation has electronic controls with a dual electronic active edge guiding system for band and body panel. It is also equipped with pneumatic expansion rollers that facilitate loading of band and body panel to the sewing head. The machine has automatic stacking device that withdraws the sewn panel from the sewing position and stacks them automatically. The operator’s task is limited to folding the circular rib knit piece in half to form a band and placing it over the expansion guide rollers. The rollers automatically expand to load the body. The body is loaded over the rollers and band, and start sensor expands the rollers to sew position and indexes the parts under the presser foot and the sew cycle begins. The operator is then free to load band and body panel on the second machine. When the finished seam is detected at the needlepoint, the parts are sewn further till a predetermined distance, thread chain is cut, and the part is automatically stacked. The productivity of the machine in 1:1 man to machine configuration is 242 pieces per hour and 1,939 pieces per shift. While in 1:2 configuration, machine productivity is 457 pieces per hour and 3,657 pieces per shift. There is a loss of 27 pieces per hour in 1:2 man to machine configuration as compared to 2:2 configuration (two operators for 2 workstation. refer Exhibit 1.1.
Exhibit 1.2: Production Loss for AAC 1278-6 1:2 and 2:2 configurations |
|||
Time Loss/Cycle (Secs) | Time Loss/Hr. (Secs) | Prod. Loss/Hr. (Pcs) | Prod. Loss/Shift (Pcs) |
0.45000 | 212 | 27 | 221 |
Conclusion
Use of technology has been successfully demonstrated in improving productivity and manpower utilization for bottom rib attach operation. Use of automat in deskilling the job, by minimizing human intervention is also demonstrated. Though the automats are more suitable for bulk manufactured products that offer longer runs for smaller orders, these machines can be utilized as an external task by designing the line plans accordingly