Most factories manufacturing polo shirts in bulk quantities are observed to utilize slit cutting operation followed by conventional front placket setting operation. This method not only restricts machine productivity but also requires additional manpower for slit cutting and stacking operation. Integrated front placket setting and centre cutting workstation combines the two operations and helps not only to improve the productivity but also to deskill the job by restricting the operator’s task to loading of panels to the feeding clamps. The machine simultaneously performs the placket setting and centre slitting operation on a single workstation thereby eliminating the subsequent centre cutting operation.
Conventional method for front placket setting and centre cutting operation
The conventional front placket setting operation is completely manual, where operator performs all the tasks like panel handling, front panel and placket piece positioning, sewing and disposing. This necessitates use of skilled manpower, thereby increasing human dependency and also increasing the chances of human induced errors. The operation also requires a subsequent centre cutting operation which is manually performed. The observed average cycle time for front placket setting and slit cutting operations on conventional machines is indicated in Exhibit 1.1.
Technology behind automatic sleeve closing
Atlanta Attachment Company, Jack , UZU, JUITA are prominent brands in the market offering integrated front placket setting and centre cutting work stations. The integrated workstations have an extended machine table for placing and positioning the body front and the placket panel. The operators then slide the assembly to the sewing position. The machine is either operated automatically through optical sensors or is operated by pressing the foot pedal.
Atlanta Attachment Company – automatic placket setting machine: model 982
Model 982 from Atlanta Attachment Company is an integrated front placket setting and centre cutting workstation. The machine features the patented bus control system. Operator’s task is limited to placement of shirt front and placket in the clamping position. The machine is equipped with laser guides to assist precise placement and alignment of components. Operators are just required to slide the component assembly to the sewing position and the machine cycle begins automatically. The machine is equipped with automatic thread cutting system and completes the sewing, slit cutting, bartacking and stacking operations automatically. In case of thread break, the machine stops, backtracks to facilitate the repairs and eliminates the need to repair offline. The machine has programmable centre knife, which operates independent of sewing head. The auto stacker also has unloaded features. The machine is equipped with Bobbin monitor system to facilitate instances of mid cycle bobbin run out. The machine is flexible, can accommodate all sizes varying from size Small to XXXL. Productivity of the machine is 410 units per hour and 3,282 units per shift (placket setting + slit cutting + stacking).
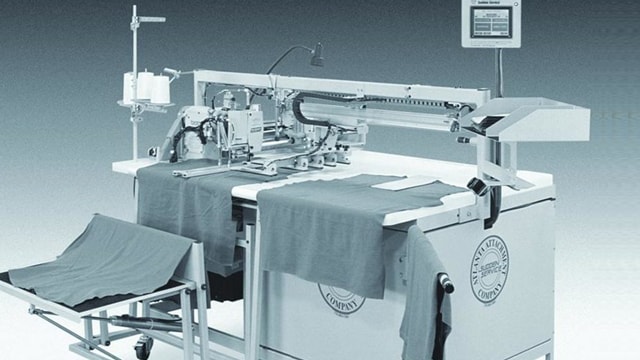
JACK – automatic placket setting machine: model JK-5878-58B
The JK-5878-58B from Jack, an integrated workstation which performs placket setting and centre slit making operation on the same workstation, sews, slits and stacks the panel automatically. Operator’s task is restricted to front shirt and placket panel positioning to the machine clamps. The machine has auto feeding assembly that moves the panels into the sewing position. The machine is microprocessor controlled/ programmable and is equipped with large display panel for ease of operation. The machine has double knife assembly that ensures precise cut. The machine can accommodate different placket sizes ranging from small to XXXL. The machine has needle thread monitoring device to prevent chances of thread run-out during machine cycle. The stacking device automatically stacks the panels with easy unloading feature. The productivity of the machine is around 299 units/ hour or 2,388 pieces/shift (refer Exhibit 1.1).
Exhibit 1.1: Polo Shirt Front Placket setting and cutting operation |
|||||||||||
Machine make | Machine/Operation type | Loading for stitching (with allowance) | Runstitch sewing (with allowance) | Unloading after stitching (with allowance) | Centre cutting | Runstitch sewing (with allowance) | Centre cutting | Stacking | Total average cycle time (in sec.) (with allowance) | Prod./ Machine/Hr. X No. of machines manned (No. of cuffs) | Prod./ shift (cuff units) |
Juki DDL 5550N | Placket attach operation | – | 30 | – | NA | – | 2.5 | 2.5 | 30 | 119 | 948 |
Manual operation | Placket centre cutting | – | NA | – | 27 | 10 | 2 | 2 | 27 | 133 | 1067 |
Atlanta Attachment Company 982 | Automatic | 8.55 | – | – | – | 8.8 | 2.5 | 8.8 | 410 | 3282 | |
Jack JK-5878-58D | Automatic | 12.06 | – | – | – | 10 | 2 | 12.1 | 299 | 2388 | |
UZU UZ-PL33D-ST/PS | Automatic | 13.84 | – | – | – | 12.5 | 2 | 13.8 | 260 | 2081 | |
JUITA JTK2-02C | Automatic | 12.94 | – | – | – | 11.44 | 1.69 | 12.94 | 278 | 2226 |
UZU – automatic placket setting machine: model UZ-PL33D-ST/PS
The sewing and slit cutting operations are performed automatically on UZ-PL33D-ST/ PS – another integrated front placket setting and centre slitting workstation. The knife cutting program can be selected from full-cut or semi-cut. The machine has programmable controls and touch screen monitor for ease of operation. The operator’s task is limited to loading of panels on machine carriage, which is powered by stepping motor for positioning the panels precisely at the sewing position. The sewing head is driven by servo motor thereby ensuring saving of power and reduced vibrations. Alongside a thread break detector sensor, the machine has laser guide system to ensure precise positioning of panels and accurate sewing. The program can be set to select between 5 different shapes for hidden placket. Placket style can be selected from C-CLOSE or C-OPEN shape. Sewing width can be adjusted from 4-40 mm, while the sewing length can be adjusted from 40-300 mm. The machine is equipped with a system to automatically calculate the bobbin thread content, to avoid thread running out during machine cycle. The sewing start and end cycle is selectable for ‘Condense’ and ‘Back Tack’ Stitch. The machine productivity is around 260 units per hour or 2,081 units per shift (refer Exhibit 1.1).
JUITA automatic placket setting machine: model JTK2-02C
JTK2-02C from JUITA is a multifunctional automatic front placket setting and slit cutting workstation. The use of Schneider Electric components (Japan), Panasonic servo motor control system (Japan), SMC pneumatic components and direct-drive system ensures that product quality is reliable and stable. The machine has a powerful CNC operated sewing function. The machine is equipped with automatic thread trimmer, automatic presser foot lifter, automatic backtracking, automatic folding cloth break detection and adjustable needle spacing arrangement. The machine has easy to use control panel operation and uses advanced large colour LCD display with touch operation screen controls. The slit cutter has independent drive motor which ensures improved quality of cut. The machine also features infrared positioning lights that help in precise fabric positioning for accurate sewing. The machine has an automatic stacker for easy disposal of produced shirt plackets. The workstation can be effectively used for sewing unilateral placket (also known as unilateral tube, dark tube) and bilateral placket (also known as bilateral tube, Ming tube or POLO tube). The machine productivity is around 278 units per hour or 2,226 units per shift (refer Exhibit 1.1).
HUACE: model HC-280A-01/02
Apart from established brands, new brands like China-based HUACE provide placket making automat with versatile functionality. HUACE’s HC-28001/02 provides fully automatic operation for sewing and cutting in one progress. The machine is capable of sewing visible, invisible and ornamental T-shirt placket fronts. HC-280A-01 is a single needle single placket computerized machine for sewing single side placket (also called wrap over front, plain front button panel placket). HC-280A-02 is a single needle double blade computerized machine that can conveniently stitch both-side plackets (also called flanged bobbin, visible flanged bobbin or polo flanged bobbin placket). The automat is claimed to give a production rate of 2,000-2,800 pcs./8 hour shift. The machine is fully automatic in function and the operator’s task is restricted to loading the clamping device. The high production rate gives improved machine efficiency and helps deskill the operation.
It should be noted that placket making of polo can be of various styles, viz. single line of slitting and double line of slitting. Automated workstations can be selected as per the style requirement, i.e. single or double slit operation. In the study, except JUITA, all other models offer single line slitting operations.
Conclusion
Use of technology has been successfully demonstrated in improving productivity and enhancing manpower utilization for front placket setting and slit cutting operation. Use of automat in deskilling the job, by minimizing human intervention is also demonstrated. Though the automats are more suitable for bulk manufactured products that offer longer runs, for smaller orders, these machines can be utilized as an external task by designing the line plans accordingly.