The goal of ergonomics is to create a workforce that is healthy and safe, as well as productive. Effective usage of e(r)gineered workplaces can help you move towards ‘right-tech’ instead of ‘hi-tech’. The need is to apply yourself to effect a comfortable working condition reaping greater rewards than imagined.
“Increased customer satisfaction, speed delivery, reduced lead times, tighter order prices, relationships, stricter human rights laws, world at war, recession, exchange fluctuations, new trade treaties, low productivity, complaining workforce…, all these spin my head; and in addition I have my customers breathing down my neck on my factory efficiency levels. How do I get my factories to work effectively to achieve higher efficiencies with a more pleasant working atmosphere?” asks the managing director of an apparel manufacturing firm.
In return, the production manager of the firm thinks, “How do I get to increase my working efficiency down to the operator level? My operators complain of aching backs and do not agree with time standards set by my engineer. The sewing operators do not feel comfortable in the seating bench provided to them, the bundles are kept in cartons and operators feel they need to bend so many times in a day, leading to backache. Besides, the lighting at needle point is insufficient sometimes while working with dark coloured fabrics; even the label-tagging operators in my packing section complain about pain in wrist at the end of the day. There are so many adverse circumstances under which they have to perform while doing their job. What do I tell my engineer to look into? How do I get my efficiencies up?” This brooding becomes a part and parcel of every production manager’s daily routine.
Optimizing the output to the maximum, with respect to the given input, constitutes the efficiency of any manufacturing process. Many manufacturing companies yearn to achieve excellence in productivity by high efficiencies. In order to affect the maximum out of any machine/operator, it is important that the area of work is planned or engineered. Engineering has been the backbone of almost all manufacturing industries across the globe. To get high efficiency, one also has to make sure that the machine operator is comfortable while on job. Poor design of sewing machine systems, besides reducing productivity, can lead to many health problems for the operators. The angle of the head, lower than its natural position, causes strain on the neck and shoulder muscles, which may lead to headaches and some cumulative trauma disorders (CTDs). Normally in the industry, the operators’ reach are greater than recommended and can lead to backache and strain on the shoulder and elbow joints. Repetitive motion caused by the foot pedal can lead to CTDs in the foot. Excessive noise and poor lighting can also lead to hearing and vision problems.
Proper ergonomics is the solution to these problems. There is an urgent need to address workplace engineering and its relationship with ergonomics. These two concepts go hand-in-hand, and hence I prefer calling the improved operational process as an e(r)gineered operation.
E(r)gineering a workplace
To be able to engineer a workplace, there are some key parameters that an engineer needs to comply with. These parameters deal with the measurement of work content of any operation being carried out in the factory. Any operation, which is being engineered, should be studied in totality in advance. The purpose of studying the operation is to provide a smooth work process for the operator, besides effecting savings in time to do the operation.
For e(r)gineering an operation, the following activities need to be carried out by the engineer:
- SAM (Standard Allowed Minute) of the operation needs to be assessed on the current method and equipment. This would provide us with a target to work upon;
- During this assessment, the engineer should be able to study each element of the operation including the motion of the operator doing the operation; and
- Once analysed and timed, the engineer needs to draw schematic diagrams (preferably visual than mental) to see possible eliminations or combination of motions.
Once the operation is fully analysed, the engineer should look at reducing the work content of the operation by the following effective means:
- Pick and dispose method;
- Material handling support;
- Material positioning and aligning method;
- Sewing technique and burst reduction; and
- Last, but not the least, the working posture of the worker.
The focus under each of these elements would need to be on training the operator to master the right technique to perform the operation.
Method Selection
The ergonomic way identifying the right method greatly depends upon the comfort/ease provided to the operator for performing the operation. The areas which need to be kept in mind should be:
- Workplace positioning with reference to material movement, lighting, impact of natural light etc.;
- Height of the sewing machine with reference to operator seating (in case of seated workplaces) or operator height (in case of standing workplaces);
- Operator seating or standing comfort
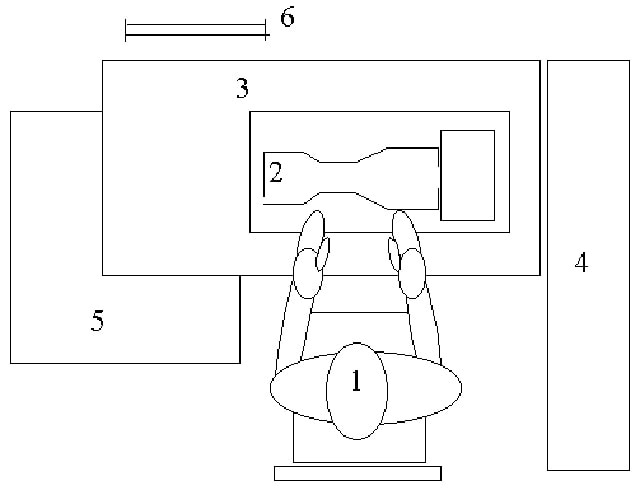
2 Denotes the machine type, folder position, knee lift position, needle positioning.
3 Denotes the machine bed (fat, submerged, raised, width, length, surface).
4 Denotes the centre bench (material pick-up position, distance from operator).
5 Denotes workaid provided (extensions, carousels, trolleys, clamp, stands, trays etc).
6 Denotes disposal equipment (stackers, stands, bins).
- Material pick-up position and distance (bundle pick-up or overhead single piece movers);
- Sewing aid (folder etc.) position;
- Material dispose position; and
- Material handling aid (workaids and attachments).
To plan the sewing workstation, the following could be used by the engineer for an ergonomically correct method. The four main aspects while planning the sewing station are lighting and noise, sewing table, chair and foot pedal.
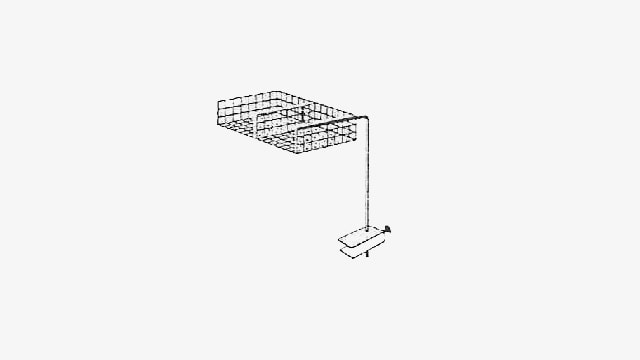
Ergonomic tips
The table should be modified to be adjustable to a height between 26” and 28” and the depth of the table limited to about 21”. All access to and from objects to be placed within 15” to the right or left of the user to limit reach requirements. Also, the sewing machine platform (head) should be at a tilt of 15-20 degrees below the horizon to keep the workpiece in the normal line of sight.
For any seated work, a footrest is recommended. For a traditional sewing station, a double footrest with a foot pedal incorporated for use by either foot could be designed. Users of sewing machines traditionally sit on the front of their chairs to more easily operate the foot pedal. With foot pedal modifications, a full-size seat needs to be provided to the operator. Proper seating requires adjustable height, seat depth, lumbar support and armrests (sewing table suitably modified could be used as armrests). To counter the tendency to lean forward while sewing, an additional posture aid like a front pad attached to the table could be developed to allow the user to lean forward with the workpiece and still maintain a proper posture.
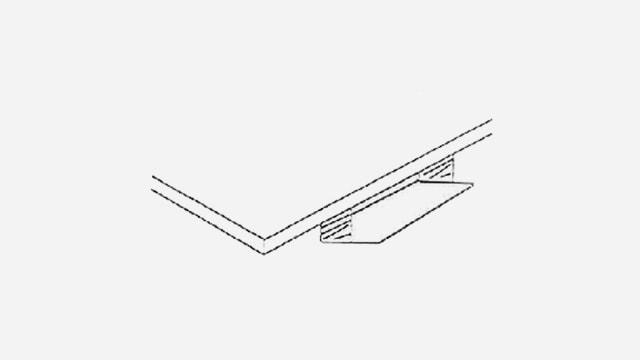
The final consideration needs to be for environmental aspects like lighting and noise. The light should be at about 7-7½ feet from the ground. The centre of optical intensity should be ½” to the left of the needle point. An ideal luminosity index should be 1000 lx. The noise level of industrial sewing machines should be around 90db limit for safe exposure, depending on the type of material and speed of stitching. Hearing protection like earplugs, in case of higher decibel levels, should be put in.
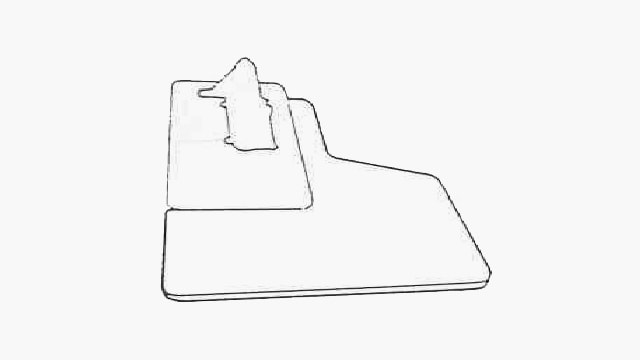
Based on the above, the engineer needs to plan the method to comfort the operator. A well thought-out and documented operation leads to better workplace engineering. To elaborate on each of the following, the following diagram schematics could explain these better.
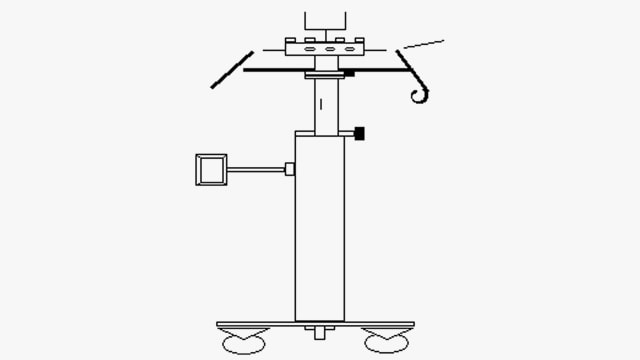
Let’s take the example of a workplace which uses a conventional centre bench for material movement.
In the above example, the focus of engineering the workplace would lead from an ‘ergonomic’ analyses and subsequent planning of the aids provided to the operator. In this case, based on all the above, the engineer plans the workplace engineering in such a way that the operator is provided with maximum ease, minimum displacement and focused operating technique (maximizing needle time). When the e(r)gineered method is compared to the old method, an improved work technique along with definitive savings in operation time would be noticed. Across the factory, this makes a huge opportunity for overall efficiency build-up.
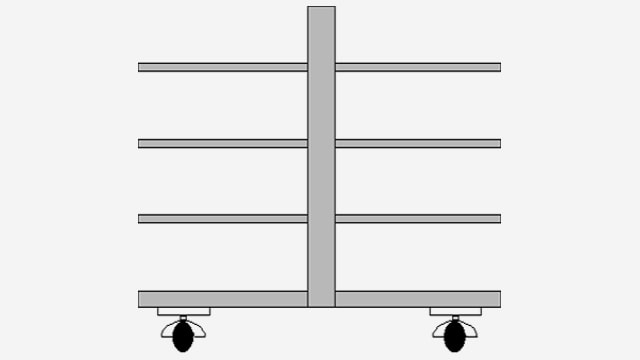
To analyse motion movement and subsequent e(r)gineered techniques, there are various softwares available online as well as mobile apps to guide the engineers to assess the risk and decide the most appropriate option.
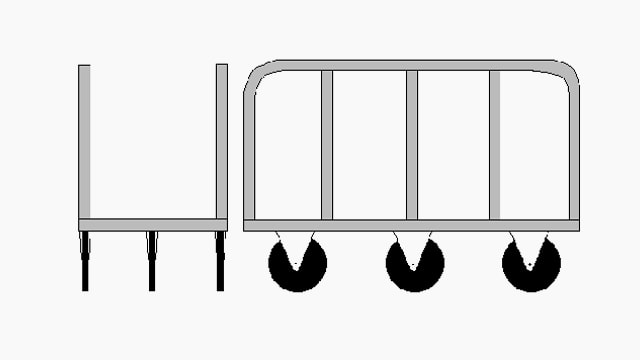
Besides the above, there are several other options for material movement across the operational floor in a factory. These could be various modes of Unit Production Systems (UPS) like ETON, SwitchTrak etc. Even in those, engineering of the workplace would constitute the crux for operator comfort and efficiency build-up.
Examples
Some of the proven work aids which affect a lot of ergonomic comfort and greatly contribute to operator performance are illustrated below. Some of these work aids have been able to cut down the operator fatigue level, measured by distance moved up to 18%.
These work aids have proven to be widely used throughout the industry effecting savings in material handling reduction and minimum operator displacement. There are NO work aids which fit well under all conditions. They need to be e(r)gineered to suit the purpose.