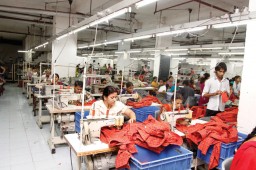
Maintaining defined quality standards and first-time right in a predetermined time has always been the forte of exporters with deep pockets… But, the commitment to achieve ‘zero’ defect garments is not the proprietary of only the big players… presented is a success story of a 100-machine manufacturer catering to domestic brands like Blackberrys, Cantabil and John Player, and that too in a niche non-Delhi product like basic formal shirts. Driving success is a well managed IE department; Gaursons Exim in Sahibabad has a gross turnover of Rs. 8.5 crores within a time period of just one year after its commencement with capacities booked for the whole year! The man behind this venture is Vikas Shandilya, Director of the manufacturing facility. He has undertaken the critical aspects of production planning, time & motion study and operator training under his portfolio which has resulted in the upward growth of this unit. The Technical team of SW recently visited the factory to validate the claims…
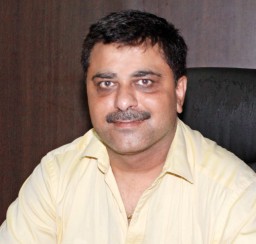
With eleven years of shop floor experience under Korean technicians, Vikas is a hands-on person, who believes that keeping things simple helps to achieve productivity.
Of course, a major advantage that the unit has is the product which they manufacture – formal shirts – which is basic and has very few changes in styling. “It’s the product that has given us the edge in terms of productivity.
Due to a fixed product we have saved upon style changeover times, pattern engineering and the operators too have acquired ‘speed skills’ in various aspects of shirt manufacturing,” says Vikas.
- “Doing a time study is easy but to follow those times is most difficult. We don’t have to follow these times while sewing rather it’s the sewing operator who needs to understand its importance and stick to it,” Sunil Khanna, Head of Production, Gaursons Exim
- Before commencing the production in the manufacturing facility in Sahibabad Vikas Shandilya, Director, conducted an extensive time & motion study of various sewing operation and related aspects of shirt manufacturing. “I have worked under the Koreans at Toy’n’Toy International, Sonepat for a period of 11 years and acquired the knowledge which today has helped me in gaining these heights,” says Vikas. After starting out as a sampling tailor and moving on to the ranks of a supervisor, Vikas has done it all on a production floor in real time and apart from the knowledge of Industrial Engineering, he also makes various folders and attachments in-house, which are being successfully used in his unit.
Additionally, high investment departments like merchandising, which in an export house doing high fashion garments is the backbone of business, have requirement of minimal manpower and operations. The manufacturing starts straightaway after getting the approval of the pre-production sample, for that a single merchandiser is enough. “With little variation in the design, fabric is the only major change encountered for product differentiation and that also is usually provided by nominated suppliers of the brands we cater to. Thus reducing the time wasted in pre-production activities involving numerous approvals,” avers Vikas.
Time & Motion Study
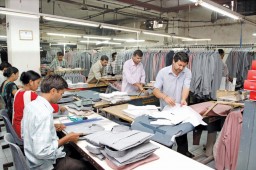
The manufacturing capacity of the unit is 50,000 shirts per month, with 60 shirts produced every hour in an eight hour shift by a single line. The unit has 2 sewing lines of 45 machines each with auxiliary lines for collar, cuffs, placket, button-holing and attaching. The operation breakdown followed in the company is quit unique from the standard practise and has been broken down into many simpler operations resulting in deskilling of the manufacturing process. “We might have lengthened the operation breakdown but we also have reduced the amount of skill required by an operator to execute a process,” reasons Sunil Khanna, Head of Production. It has been claimed that a single line produces a shirt every one minute. The 350 strong workforce at the company contributes to the high man-machines ratio of 3.5:1. However, Vikas justifies the ratio saying it adds to the productivity. “Major portion of our workforce is involved as helpers for the sewing operators. From the aspect of in-line material handling to providing water to operators while stitching, all is undertaken by them and they ensure smooth operations, without undue stoppages,” he says.
Operator Training & Management
Gaursons Exim undertakes operator training programs not only to skill them, but also to make them understand the importance of quality and then grading them. Besides the usual standard procedure for operator training, the training also involves stamina building activities, which involves methods to increase an operators sewing capacity by increasing the sewing duration steady over a period of time. “Training of an unskilled labour is conducted for a week before being induced in the sewing line and goes on up till a period of three months, after which the operator is graded into three categories, namely A, B or C. All the operators being on payroll, we have a negligible attrition rate with 15-16% monthly absenteeism,” says Vikas.
It’s the relation that the company has nurtured with its operators that has paid in the longer run. The incentive system followed in the unit is individual-based. The lines are balanced in such a way that every operator is given a target of 60 pieces per hour. “Few operators do overshoot their targets and get adequate compensation for that. But we cannot increase the target as not all can achieve it and higher production targets become very operator-oriented. Thus if an operator performing more than the standard target quits the job or is absent, we would not have to re-balance the line all over again,” argues Sunil.
With a strong IE input all effort is made in the pre-production stage to iron out any possible loophole, and the traditional ‘jugad’ is used extensively to achieve results without compromising on quality, for example fixed-width edge stitching is not done with any attachment or folder but with the help of a thick tape that has been stuck at the required distance from the needle for indication.
Another interesting innovation is the use of cardboard folder for the purpose of folding the shirts and imparting the diamond shape to the sleeve placket, all being cost saving and efficient. Indeed Gaursons Exim has combined the latest technology with traditional entrepreneurial acumen for a very profitable manufacturing unit. Now the company is setting up the second factory to manufacture formal trousers, on demand from its regular buyers..