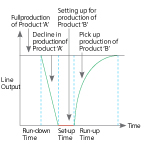
How fast and effectively one can adjust to the requirements of different orders, is one of the keys to success for any organization. With increased competitiveness, lead times are getting shorter and one cannot afford delay in setting up the batch and a slow output. Gone are the days of huge quantity consistent orders with no or minimal style changes. Smaller order quantities with increased variations are flavour of the recent times and the same is expected to continue in future also.
Quick response manufacturing systems which can handle low volume – multistyles with faster throughput time and efficiency – are need of the hour. A number of manufacturers have realized this and geared up to handle such order trends. Logical approach supported by IE may result in quick changeover with minimizing start-up losses. Manoj Tiwari, Associate Professor, NIFT Jodhpur and Dr. Prabir Jana, Professor, NIFT Delhi discuss the mechanism of start-up and suggest logical approach to minimize the start-up losses resulting in faster and effective line output.
Usually, whenever there is a style changeover, a drop in production is observed. The drop is experienced in all the areas of the manufacturing process. However, in the case of small quantities the implications of this dip are wide ranging on the lead time for the buyer and seller. This phenomenon is termed as start-up loss or changeover loss or shift in/shift out loss. Start-up losses have two major components – set-up losses and production losses. A set-up consists of all the activities that are performed after the last product ‘A’ comes out of the machine until the first products ‘B’ is made. The set-up involves adjusting the machine mechanism to the sewability of the style, which is to be fed in the sewing line/batch.
Table 1: Off-line and On-line activities | |
Off-line | On-line activities |
Development and testing of templates, folders and profiles | Demonstration to operators by the supervisors |
Developing machine layout and sequencing of machines | Change in machine setting that is already in the line |
Arrangement of machines, folders, labels, accessories and trims that are required in the line | Rethreading of machines already in line and setting tension adjustment |
Testing/trial runs of new machines that are being brought in the line | Change of needle, presser feet, throat plate, feed dog and other work aids |
Adjustment in setting of machines that are being brought new in the line |
The change in the setting is done gradually as and when the process of the shift out is complete at a particular station. Losses during this phase are mostly related to machine- and material-related issues and referred to as set-up losses. Production losses, on the other hand, are loss in the output as a result of the new style in the line/batch. Such losses are attributed to the time taken by the operators to get accustomed to the new style. It also depends on the style complexity of the previous style which is being run in the line. Such losses are mostly related to manpower and skill-related issues.
Batch setting is defined as the time taken by first piece of a style being fed to the first station till the time it comes out of the last station along with required quality, and takes into consideration machine setting, operator setting and initial line balancing time. Components of start-up and batch setting may be understood from Figure 1.
Table 2: Achieving pick-up (Assembly Line vs. Modular System) | ||
% of target achieved | ||
Day | Assembly Line | Modular System |
1 | 15% | 25% |
2 | 25% | 55% |
3 | 45% | 85% |
4 | 60% | 100% |
5 | 75% | 100% |
6 | 90% | 100% |
7 | 90% | 100% |
8 | 100% | 100% |
Given the large number of products and variants that need to be produced in different quantities, it is feasible to have a dedicated machine or machine line for every product. However, if different products need to be produced using the same production equipment, it implies that every time we change from a product ‘A’ to a product ‘B’, a number of activities need to be performed by other people to prepare the equipment for the new product. These can be activities like exchanging parts, adjusting settings, cleaning and administration on work order documents, getting new raw materials, etc.
Factors affecting Start-up losses and role of IE
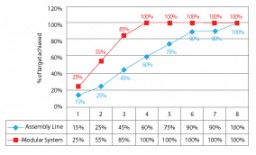
IE plays a critical role in minimizing the start-up losses. A good IE always focuses on saving the productive time and doing preparations in advance. It’s similar to performing a surgery by a team of doctors where some activities or preparations have to be done in advance so that we don’t waste productive time later. IE also selects the activities which can be done without disturbing the setup. Activities may be classified as off-line and on-line as discussed below:
Off-line and on-line activities – All the activities that are involved in batch setting should be divided into off-line (the activities that don’t require the machine to be stopped) and on-line activities (the activities that require to be done on the line and result in downtime of machine). Efforts should be made to convert as many on-line activities as possible into off-line activities. Lean manufacturing tool Single Minute Exchange of Dies (SMED) is also based on similar concept. This results in saving of valuable production time which was wasted earlier in those activities which could have been done in advance at the planning stage.
Managing Start-up losses – Managing the loss of productive time when orders are changed is very challenging and requires a proactive approach in order to minimize the losses; however, a certain degree of start-up loss may be unavoidable. In today’s frequent style changing scenario it is very important to effectively manage the every next style being introduced into the production floor. Failure to managing next introducing style leads to production loss, quality issues, end moment fire-fighting, etc., which ultimately results into financial loss to the company. In order to avoid the adverse effect, it is very important to understand the next introducing style well in advance and assure everything is put in place for better execution of the style.
To execute next introducing style effectively, some key points need to be taken into consideration such as study of style in terms of machine requirements, work aids requirement and SAM, in-house available capacity, in-house date of raw materials, delivery date, making an action plan to execute the style and preparedness to monitoring the planned action and mechanism of necessary corrective action.
Learning curve – Whenever there is a style change, the set-up takes its time to achieve peak output. The increment in daily output may be gradual and non-linear. The learning curve may vary from product to product and set-up to set-up. There is no such standard learning curve reported, however IE and PPC use their experience in deciding learning curves for different products while planning for orders. Also it may be noted that in a setup, switching over from complex to simple style may have faster learning curve (as operators adapt to easy operations faster) while a learning curve shifting from simple product to complex may take comparatively more days with a slower learning curve.
It has also been observed that different manufacturing setups for the same product in the same organization have different learning curves. Let’s understand this with an example of manufacturing of a 5-pocket jeans, where one product is produced in assembly line as well as in modular system. An assembly line may have a learning curve spanning 7- 8 working days while a module may get its peak production in only 3-4 days. A typical learning curve is shown in Table 2 and Graph 1.
Selection of right line for a new style
Product allocation to a line is a regular activity of IE and PPC. While doing so, efforts should be on achieving faster learning curve and getting quicker output. Consideration of some key factors (as discussed below) may have a positive visible impact on the line performance:
1. Line compatibility to the product – Line compatibility plays a critical role in achieving the desired timely output. A mismatch between line and product may lead to lower productivity. Such issues have a significant impact on the profitability of the organization as delivery deadlines may be missed out.
Whenever there is a new style in the line, operators require time to get familiar with the operations and get settled on the same. Product and line incompatibility further increases this time and slows down the learning curve.
Let’s understand this with a case, assuming a sewing line is suitable for 5-pocket jeans, if there are 2 new product styles, say cargo shorts and 5-pocket jeans with button fly which need to be produced. While selecting the suitable style to be put in the line, one must consider the similarity (or differences) between ongoing style and the style to be put. A line will be more compatible to a similar product (5-pocket jeans with button fly), as operators will pick up faster.
2. Requirement of changes and modifications in setup – In practical work environment, major frequent changes in setup are not advisable. Such changes not only disturb the setup in terms of batch setting and start-up but also make it difficult to handle the work from supervisor’s controlling point of view. Unless there is an emergency, products allocation should be in such a manner that the new order can be executed with minimal changes in machine settings and the layout of the machines. It has been experienced that whereas lines with major changes take 5-6 working days in achieving peak and if the changes are minor the same peak was achieved in 2-3 working days.
3. History of the line – Past record of a particular line is also an important factor while deciding the product to be produced from that line. It has been observed that most of the times line operators with their skill sets are kept intact and are assigned to a particular line. While deciding a product to a particular line, past experience of the same or similar product must be taken into consideration. This definitely helps in faster learning curve and minimum start-up loss as such operators will pick up the efficiency faster than other operators.
4. Attitude while executing new products – Many a times it is observed that a particular set of people under a supervisor or production manager love to take up challenges of producing difficult product styles. Such lines or groups have a proven track record of handling difficult situations and coming out successfully while others are not so good. IE and PPC should have a watchful observation on this and should use such instincts while allocating critical styles.
Key Learnings…
Sewing happens in most cases either in PBU (Progressive Bundle Unit) system or UPS (Unit Production System). Since in PBU the number of parallel operations depend on style to style and the flow of material is converging, the changeover process will require complex co-ordination to minimize idle time, whereas in UPS there is always linear flow and no parallel operations ever happen. The style changeover process in UPS is very simple as first operator completes the last piece (and passes on to 2nd operator) of previous style, he/she starts the first piece of new style. Then the 2nd operator will complete the last piece of previous style and start the first piece of new style, and so on.
The PBU scenario is little different, as there are multiple operators doing part preparation in parallel. Taking the example of shirt making, in PBU the collar runstitch, cuff runstitch, back-yoke join, pocket hemming operation all are happening simultaneously; during style changeover all of these operators will complete the last piece of previous style at different time and will require cut parts of new style. Suppose the new style is half sleeve, therefore there will not be any cuff runstitch operation in new style and supervisor has to give some other operation to cuff runstitch operator and so on. That is also one of the reasons many manufacturers are unconsciously moving towards UPS.
Conclusion
Minimizing start-up losses during style changeover is very important for any manufacturing setup. A day saved or lost in start-up may be very crucial to meet the shipment deadline. In practical environment, a day should be treated in terms of output at peak. For example, mathematically output may be 450 units in start-up on a given day but psychologically its impact on shipment terms may be 1,200 units (which a line may produce at peak). A day saved in start-up may give an advantage of a peak product quantity which may be vital to any shipment. That is the reason it is said that the success or failure of shipment is controlled by start-up not by the later stage. An IE should play a proactive role in style changeover and try to make start-up smooth, efficient and faster. In the initial days of start-up, IE should take a lead and help the line in achieving its peak output. Later, once the line is set, it should be handed over to production personnel to carry the momentum forward.