Operation breakdown and sequence of operations are not important in the Make Through System since one operator sews the complete garment, but they are critically important in an Assembly Line because the construction of a garment is planned in steps where different operators are responsible for sewing different parts of the same garment, and each operator is given a specific task. An Assembly Line work involves preparing a document (called Operation Bulletin or OB) that lists out the total number of components in the garment, and includes a diagram showing the sequence of operations, a table with machineries and equipment required for each operation, needles and threads needed, and the work content of each operation, which is calculated either through Time Study or PMTS. Though it is important to make an OB, it is not without a few pitfalls, explains Dr. Prabir Jana, Professor, NIFT Delhi.
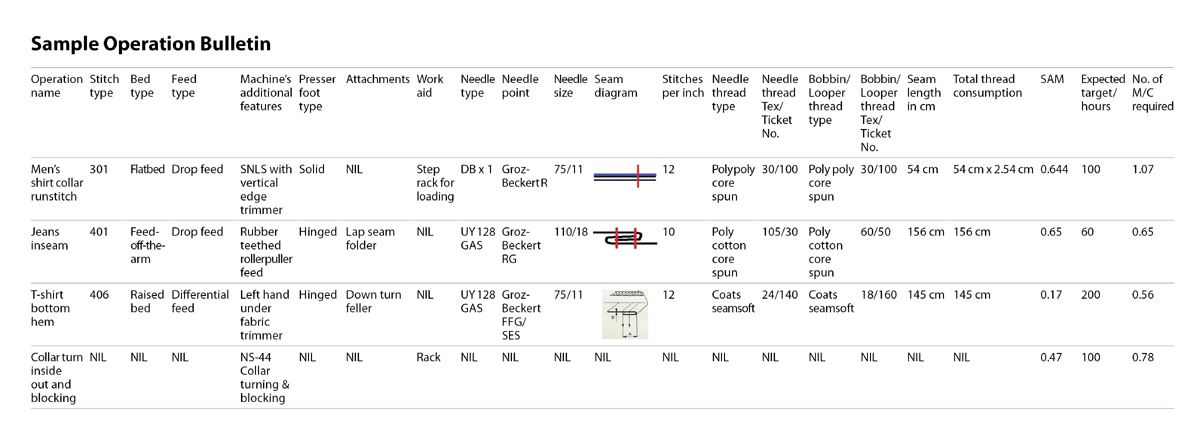
In case of an Assembly Line, the product needs to be broken down into different operations, wherein each and every machining and non-machining operation is identified and documented in a flow chart, and each connected to the preceding and succeeding operation. The same is the case with producing a garment where every sewing operation is characterized by a start and stop action (with or without back tack and except for a burst in a single operation), is considered as a separate operation. For example, collar making in men’s shirts is divided into the following operations that must flow as per the sequence: collar runstitch, collar turn inside out and pressing, collar topstitch, collar centre trimming and notching, band hemming, band and collar joining, and turning the band to finish the collar. These operations determine the machinery and equipment required for each operation. There seems to be a practice of laying more emphasis on sewing operations and ignoring non-sewing operations, but both are equally important, since a bottleneck in either operation will adversely affect the preceding or succeeding operation.
Preparing an Operation Bulletin
The Operation Bulletin (OB) comprises of the operation breakdown sequence and the flow chart. It is a table detailing of the different operations and their machines, the needles and sewing threads required and the work content. Although no definitive format of the OB is available, some organizations prepare a detailed sheet while other companies work with a basic list of the most important processes. The table enclosed here shows a comprehensive Operation Bulletin in which the information under different columns is explained for their importance and usability. While preparing the OB, some information like stitch and seam type, stitches per inch are extracted from the techpack while other details are suggested by the IE. Basically, the techpack lists what all is required/expected (output parameters) in the sample, and the OB lists all the process input parameters to achieve the required output.
Machine Selection
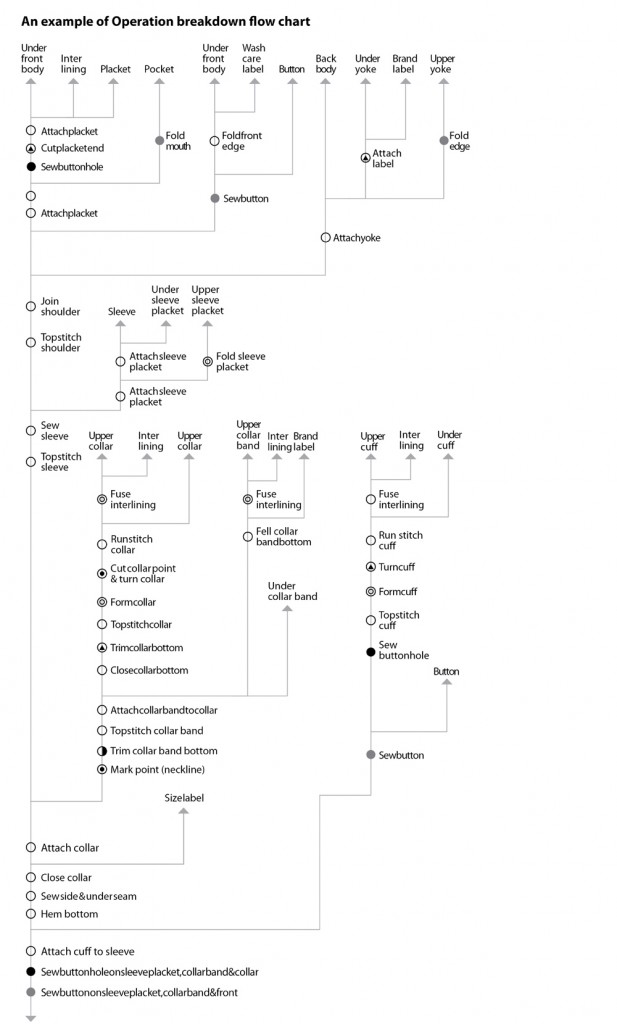
The sewing machine has three distinct features that characterize the bed type, stitch type and feed type, but it is a common practice in the industry while preparing the OB to make a single column giving either the generic specifications like ‘flatbed SNLS’ or the machine brand with its model number (like Juki DDL 9000). However, while writing in a single column, one tends to misgive some key information like the feed type or bed type; so it is important that all mandatory information be provided in separate columns. If the organization is large and has a centralized IE preparing the OB, it is quite likely that the machine brand and model number details may not be known to the IE; in this case, the generic specification is acceptable. But in a smaller organization, where the machine brand and model number is available, the IE should prepare the OB by writing the machine’s model number in a single column, which would automatically indicate the bed, stitch and feed type, along with any other additional features, for example, JUKI DLM 5400N indicates that it is a flatbed lockstitch drop feed machine with vertical edge trimmer. It is advisable that engineers of the IE department should be conversant with all machine types and their features, and should mention the appropriate machine model number for each operation.
It was often noticed that appropriate machines were not used as suggested by the IE, resulting in additional operation(s) and increase in SAM value. For example, if IE has recommended JUKI DLM 5400N machine for collar runstitch operation, then the collar edge is simultaneously trimmed during the runstitch and can be taken for collar turn inside out operation. But, suppose the factory did not have JUKI DLM 5400N in working condition, and instead is using DDL 8700 for collar runstitch, and followed by the trimming operation to be done after runstitch by a helper using a scissor or by an overlock machine without thread before the piece can be taken for collar turning. As the additional trimming work content was not a part of the original SAM, the production department should immediately inform IE for amendment of SAM. However, in practice such incidences are often not reported, with the result that the actual production will be lesser than the target and lead to a misunderstanding between the IE and production department.
To avoid any such misunderstandings, the IE department could give different options and corresponding SAM value. Probably, some of you may have noticed that some machine brands like Duerkopp Adler often mention two alternative machine types for every operation with variable expected output. The IE department has to be sensitive about the possible constraints that the production department may face, and accordingly create options with clear ranking as per most preferred and least preferred such that the production department will choose the best option in any given circumstances. If the best options are not followed for any reason, the production department will be answerable with appropriate reasons. This may result in differential SAM value being applied to the same garment on different days because one particular machine may not be working on one day, but the next day the same machine may be working.
Gauge Parts changes, Attachments and Work Aids
Folders, edge guides and hemmers to be used in an operation are generally mentioned in the OB, but gauge parts (such as presser foot, feed dog and throat plate) that may change as per the attachment being used, are usually not mentioned. Using attachments without gauge parts can impact the quality and performance of the work aids and lead to rejection/failure of the attachment. The throat plate specification is synchronized with the needle size where the ratio between the needle diameter and needle-hole diameter in the throat plate is maintained to ensure that there is no needle-cut or fabric dip-in. The presser foot can be solid or hinged, single or double leg, narrow or wide, normal or compensating, metal or teflon. Although there is a separate column in the OB for presser foot, it is often noticed that the word ‘standard’ is mentioned against every operation. The IE should have a thorough idea of the different types of presser foot and their use, and be able to recommend the most appropriate one. For example, shirt front placket sewing should use the solid presser foot, yoke topstitch should use the left compensating presser foot, and so on.
It is a common practice to fix the attachment in a sewing machine without changing the gauge parts as changing parts take time. Though often written as ‘Attachment and Work Aid’ within one column in the OB, the IE should in fact mention them separately. For instance, the presser foot and the throat plate are machine parts, while a folder and a waterfall stacker are separate devices. Also, an edge guide used for collar tip stitch is an attachment, and the step rack used to store the pre-sewn and post-sewn piece is a work aid used in an operation.
Needle Type
The OB should mention the three different characteristics of the needle: First, what type of needle should be used (e.g. DBX1 for lockstitch, DCX1 for overlock, or UY 128 GAS for flatlock); Second, what point type (e.g. ‘R’, SES, RG, etc.); and Third, what size (e.g. 90/14 or 75/11). Although in most of the situations, the needle type is specific for a particular machine type and even if not mentioned in OB, there is very less chance of fixing a wrong type in production. In very rare cases like DAX1 and DBX1, both can be used for single-needle lockstitch and appropriate needle type may be mentioned based on fabric type. Most OBs have one column that mentions the model number of the brand. For example, Groz-Beckert SAN 10 only states that Groz-Beckert is a brand and SAN 10 is the model number, and does not give any information about the needle type, point type and size. The complete information should read as Groz-Beckert SAN 10, DBX1, SES, 75/11. So it is advisable that these three important points be mentioned in three different columns.
Normally, for one type of fabric or garment, a single point type of needle is used, but for certain operations different point styles can be applied, depending on the seam thickness and construction, which will decide the variable. A denim jean for instance should be stitched using a light point needle to avoid any visible material damage after washing, but for operations like Bar-Tacking and Eyelet Button Hole, a sharp point or special ball point like RG should be used to avoid needle buckling and breaking on heavier seams like Bar-Tacking.
While IE professionals have sufficient knowledge of management, manufacturing companies should ensure that they are also trained to acquire a complete understanding of the machines and of the garment assembling processes as these are the areas in which they are lacking. It is often seen that when there is incomplete and incorrect information given in the OB, or the information filled up is not comprehensive, it can lead to inefficiencies in operations and cause disruptions in the smooth flow of work. The importance of a well-planned OB is also compromised which can result in the IE personnel losing the respect of the production department in case of any deviation from the documented work plan. To prepare the OB, the industrial engineers should have knowledge about sewing machines as well as the garment assembly processes. In a large organization, there can be multiple team members with varied expertise in the IE team, so while one takes care of the methods, the other can take care of the machine type.
Seam Type
The seam type used in certain operations is an important specification in the construction of a garment. Words like ‘superimposed seam’ and ‘flat & fell seam’ are common, but the nomenclature is not standardized across companies and countries. Therefore, instead of using names, either seam codes like SSa-1 or seam diagram are used. Although the seam codes are internationally standardized, but seam diagrams are more commonly used for making representations since they are easy to visually communicate with the sewing operator, and are therefore the most common methods of representation.
Sewing Thread
Although it is the buyer who often mentions the thread type to be used, the buyer will rarely mention the different thread types and the thickness that can be used in different operations and also in upper and lower threads of the seam. The IE is required to suggest the most technically appropriate threads for different operations in the OB, for any specific style without changing the aesthetics and commercial value of the product. The selection of thread (for any uncommon style) can often be done in consultation with thread suppliers.
Providing information on thread type and thread count is important as they can change from one operation to another. Nowadays, thread consumption for different operations can be calculated accurately, and are indicated for controlling/checking the consumption pattern. The thread type and its consumption in different operations determine its quality and procurement for the shopfloor. While the upper thread type (needle) and lower thread type (bobbin/looper) generally remain the same in almost every operation, some specific operations may require different threads, in that case it should be clearly mentioned in the OB. The buyer may simply mention the thread type as ‘100% polyester’ in the techpack; it is the industrial engineers who should add value to the product and process by specifying PPC in needle and TXP in the looper.
Depending on the technical expertise available with the buyer, these changes often require buyer’s approval, but sometimes the buyer may simply trust the manufacturer to use the right threads type. For example, the most suitable and recommended thread combination for knitted T-shirts is a polycore (PPC) spun thread in the needle and texturized polyester (TXP) thread in the looper for the overlock (e.g. Coats Epic is a polycore spun thread, and Gramax is a texturized polyester thread). Another important parameter is determining the thread package size; a common practice in the purchase department is to buy the largest package size, which results in rewinding the thread on smaller packages during production. IE should indicate in the OB the package size that should be procured, keeping in mind the operation breakdown and machine layout to avoid excessive rewinding operation.