Although the words ironing, pressing and finishing are used interchangeably, these are three different functions that aim to remove the ‘unwanted’ crease and impart ’wanted‘ crease. A crease in a fabric can be removed either by compressing the fabric between two flat surfaces or by stretching the fabric. However, to impart ’wanted‘ crease, fabric plies need to be folded and compressed between two surfaces as stretching is not enough. Moreover, process parameters like use of vacuum, steam, temperature and pressure make each process different from the other.
However, finishing being a continuous process with tremendous possibilities for automation, mass manufacturing is gradually adopting finishing over ironing and pressing to scale up the production. While the technology of buck ironing is giving way to sophisticated buck pressing and non-contact tunnel finishing is giving way to flexible finishing module, the trend is shifting from mass manufacturing to flexible manufacturing.
Ironing involves relative movement or friction between two flat surfaces, while pressing involves compression between two surfaces (but no relative motion between them). Pressing can be done by compressing between either two flat or curved surfaces, e.g., by pressing a convex and a concave surface together, a crease in the fabric can be removed simultaneously while shaping the fabric . Finishing removes the ‘unwanted’ crease by stretching, but cannot impart a ’wanted‘ crease. Both ironing and pressing can remove or impart a crease.
While utility ironing tables should be used in the industry to enable single ply ironing of most of the garments in tubular fashion, in reality, wider width rectangular tables are commonly used in the industry where an operator has no other option but to iron front and back of the garment together, resulting in longer handling time or compromising on quality.
Types of Irons
Traditionally, workers learned the skill of ironing on the job from older generations by using heavyweight electrically heated irons and padded wooden tables. The use of steam and vacuum came later and the correct use was never taught to the iron wielders scientifically, resulting in grossly incorrect methods being followed. The all-steam iron was the first type of iron to be developed, followed by the electric steam iron. While in an all-steam iron, steam is used to heat the iron and discharge a moist spray, a steam electric iron uses a heating element to keep the iron warm (and control the temperature) and a solenoid holds the steam from the iron until called for. This method is safer, as all-steam irons have live steam circulating in the iron and the iron hoses can burst and scald someone. The steam electric iron also has a hose but the electric solenoid keeps the steam out of the hose until the electric micro-switch on the iron is touched. Thus there is no steam under pressure in the iron. In allsteam irons, temperature depends on the pressure of the steam. This limits the working temperature for the irons between 140° and 150° Celsius, whereas a steam electric iron has a thermostat which will allow the temperature to be finely adjusted from 100° to 200° Celsius. Cotton and linen need at least 180° Celsius for ironing. To achieve that temperature, it is necessary that we have electric-heated steam irons.
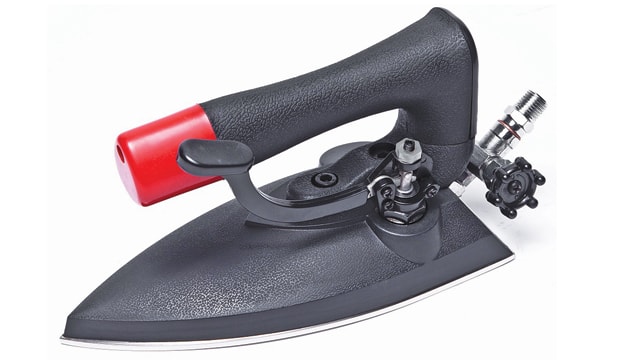
Even today it is a misconception that temperature and weight of an iron are very important parameters as both often compensate the lack of the other, i.e. lesser weight is compensated by setting higher temperature and vice-versa. These wrong notions and practices often resulted in scorching (yellowing/ browning effect) of the garment. In fact it is not the weight but the extra temperature from the mass of the heating element that dries a garment faster. Today vacuum tables are used to remove the heat and moisture, so a lightweight iron is enough. Since we use steam to do the ironing and not the weight or the pressure of the iron, the weight of the iron is not critical any more. It is ergonomically better to have lighter irons as they help the operator do ironing easily. The chambered iron has one electrical connection and a steam inlet.
The steam comes and gets stored in the steam chamber(s) and is released via a steam button, if provided. But this feature also has a disadvantage – if the iron is not in use for some time, steam condenses and water droplets may come out while ironing. The chamber-less variety of irons, removes this deficiency by providing no storage chambers and putting in one steam outlet pipe. Now the steam is kept in continuous circulation back and forth in the hose, so that there is no condensate formation, but this requires more steam. However, it removes the possibility of any cracks in the iron body due to high steam pressure.
There are different surfaces for irons like aluminium, aluminium-coated, chrome-plated, stainless steel and Teflon soles. These are recommended based on the product to be ironed. If the iron surface is highly polished during ironing, the small invisible protruding fibres in the fabric surface are aligned in regular fashion, resulting in uniform light reflection and thus shine. Also, a smooth polished surface means increased area of contact, greater heat transfer, burning of the protruding fibres, ultimately resulting in shine on the fabric surface. Teflon coating gives the surface a matte finish, which decreases the area of contact between iron surface and cloth and also aligns the fibres protruding haphazardly. The size and also the shape of the iron is very critical in ironing as sometimes there are points in a garment which can never be reached by an iron. With the new pointed soleplate, complicated ironing of tucks or pleats is no longer a problem. A slightly arched soleplate point enables improved sliding features. The very low weight of only around 1,400g facilitates smooth gliding over the garments. The iron handle is ergonomically shaped with integrated contactor switch to release steam. Fibres like viscose and polyester can react too quickly to the heat and quality problems and brittleness might show up due to the effect of temperature. The latest thermostat provides temperature control of less than ± 2° Celsius to the preset temperature, thereby ensuring quality ironing.
Ironing Tables
There are three types of ironing tables available. Firstly, the universally/commonly used vacuum table, where the suction effect is created through the table surface to lay the garment flat on the surface as well as suck the residual moisture and heat from the garment after ironing. The second type of iron table is the ‘up-steam’ table where steam comes up from table surface through garments thus moistening the garment. This is used for knitted garments, where ironing is not advisable as the movement of the iron deforms the garment. An up-steam table guarantees a complete and even distribution of steam and suction over the whole surface. The surfaces can be inclined at 60°, 90° or 120° angle. All parts contacted by steam are made of stainless steel. This prevents corrosion and guarantees a long working life and trouble-free operation. There is a little known third type: the blow-up table which is unique for any garment pressing, without leaving any marks. In 1969, VEIT invented the blow-up table and also the tubular ironing method that offers cushioning effect to the garments due to the upward thrust of air from the table which prevents ironing marks on the garments. Air blowing is used in combination with vacuum to assist in finishing the garment without leaving marks. When a vacuum is used, the garment is drawn towards the pressing surface. On multiple plies, it leaves impression marks (due to seamlines). Using air blowing, the garment is expanded and pressed on a cushion of air where ironing is possible without putting in marks. This is especially good on lined and silk garments. VEIT Varioset table has in-built suction and blowing functions as standard and all VEIT Uniset tables have the blowing function as an option.
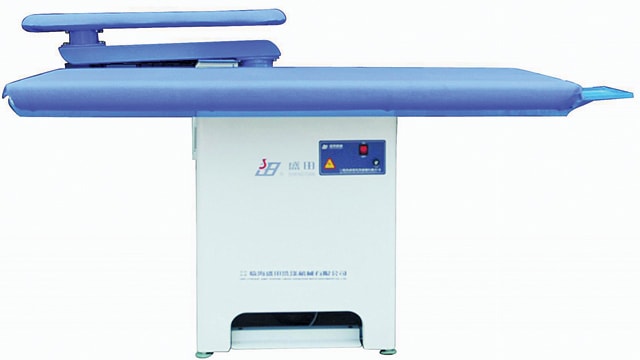
The table surface consists of five layers – top cover, intermediate layer, adjusting fibre, base layer and ironing surface. The top cover may consist of either synthetic fibre, which has long life, short-term heat-resistance up to 190° Celsius, should be slide — resistant (to keep the garment as positioned), should be porous (to be able to draw the vacuum through the garment to dry and cool it) and processed for antistatic electricity. The intermediate layer consists of 5 or 10 mm of foam as cushion for covers. The adjusting fibre guarantees the complete splitting of the condensate drops and reduces the humidity in the cover system. The base layer is generally a patented silicon mat for ensuring consistently good suction/ blowing results and distributing strong airflow evenly over the entire surface/form buck.
The base layer can be cleaned easily by compressed air and ensures unchanged performance during its lifetime. It can also be of polyurethane material of 6 mm thickness, which permits good airflow over the entire surface/ form buck, while being water-resistant for a dry surface/form buck and washable by hand with soap water. This is an economic solution for medium-term good suction/blowing result. The ironing surface of tables and bucks consist of a corrosion-resistant perforated plate or a bored casting mould with an additional light metal grid for an evenly spread suction and blowing airflow (avoids wet covers).
A common mistake followed in most of the factories is that of ironers applying steam while the vacuum is on. Such erroneous processes, though not resulting in any quality shortcomings in the garment (and the reason why it goes unnoticed), lead to incorrect motions that hamper productivity and staggering energy bills.
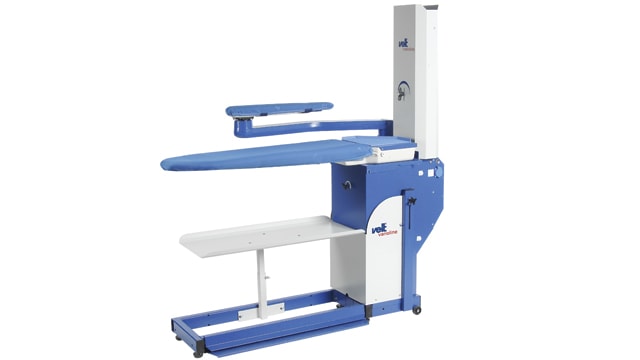
There are two basic shapes of ironing table: narrow width called utility (like a domestic ironing board) and rectangular (commonly used in the industry). The utility variant is best for dresses, bottoms, etc., while the rectangular is used for underpressing (in-line pressing) and flat pressing of children’s garments and shirts. During IMB 1997 exhibition, Electrolux Orton exhibited patented Shape Change iron table capable of ironing varied needs, where the table corner could be expanded to accommodate the garment; however the innovation did not go well with the industry. Although ironing mostly consider garments as being two-dimensional in shape, buck ironing helps to iron garments of 3-dimensional shape. Garment components can be placed on convex-shaped buck (instead of flat table) and hand iron can be used to iron (for example shoulder portion of a blazer). However if the garment portion requires concave shape of the table, it is then impossible to use hand iron. Therefore buck ironing gave way to buck pressing which will be discussed in the next issue.
Conclusion
There are no major improvements in ironing technology since its inception. Over the decades, iron became lighter, the iron plate surface coating improved to become non-sticky, non-glossy; while Teflon is the most common coating, there are several other patented high-performance sole finishings used by leading iron manufacturers such as Tufflon and titanium-plated iron soles. Due to over dependency on manual labour and batch process with low productivity, the ironing process is gradually giving way to faster alternative of pressing and finishing.
Pressing is done by compressing the fabric between either two flat or curved surfaces (no relative motion between the surfaces); and though pressing is also a batch process like ironing, it is mainly used either for large areas (as it is a faster process than ironing) or for 3D shaping of the garment part (e.g., by pressing a convex and a concave surface together). On the other hand, finishing is done to remove the ‘unwanted’ crease by applying stretch. The garment is worn over an inflatable dummy and steam is applied to inflate the dummy, thereby removing the creases; the hot air follows steam to remove the remaining moisture.
Pressing
Initially, the pressing tables were primarily two flat surfaces covering large area and the most popular pressing function was trouser legger press. In a single press, the whole trouser leg, from below crotch to bottom hem portion, was pressed at one go. There were improvised pressing machines for sweater and heavy knitwear as well, where garments were laid flat on an upsteam table and another flat surface (created by tensed fabric) was used to press over the garment in a scissor action. Although pressing of flat surfaces was relatively easy and simple technology was used to make the process faster by covering greater area at one go, the real challenge of pressing came while pressing shaped area of garments.
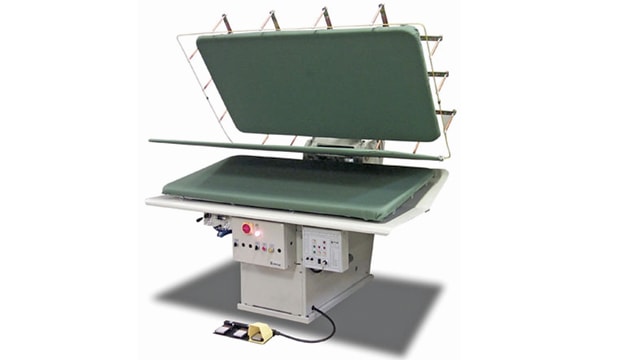
In the past, ironing tables used to have one movable arm and various convex shapes of bucks for ironing shaped garments; the shaped portion of garment parts were placed over the bucks and hand iron was used over the top to iron, remove the creases from the shaped portion of the garment (like shoulder and sleeve crown area of jacket). Initially there were only few generic shapes of bucks available and same buck was used for right and left side of the garment. First of all, the process was extremely slow and as the convex bucks were of approximate shape as the garment area, quality of the process was compromised. Although the process used to be called ‘buck pressing’, it was actually ‘buck ironing’ as the top surface was the same hand iron moving over the buck surface. Generally the convex or male shapes are stationary heads; garments are laid on top of it and concave or female shapes are moving heads that come over it in vertical action to press the garment parts.
Realizing that actual 3D shaping of any symmetric garment part is mirror image of each other; the pressing machine suppliers started manufacturing mirror shaped bucks for alternately pressing left and right side of the garment. Formal jacket offers the maximum challenge as different parts have different 3D shaping. The press manufacturers very painstakingly created exact replica of different sections of jacket shapes to offer the best possible quality appearance while the process remains fast. Initially, all buck shapes were horizontal and operator had to place the garment horizontally over it and the motion of head was vertical downwards. Then came vertical buck pressing, which can be used for smaller units and helps loading the garment better and quicker due to gravity assist. These types of machines use a combination of oscillating front and back forms, where shirts can be simultaneously loaded and pressed. This method achieves optimal handling and machine time with remarkably good results. A plus for some of the vertical presses is that they have sensors to determine if the waist and inseam are of correct size. Additionally, if the measurements are close, but not quite within tolerance, the machines can be programmed to stretch the garment to the correct size. Obviously, there is a limit to which the garments can be stretched, but safe tolerances have been established.
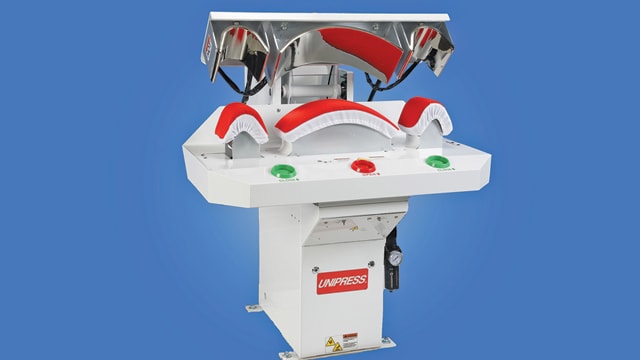
Formal jacket offers the maximum challenge as different parts have different 3D shaping. The press manufacturers very painstakingly created exact replica of different sections of jacket shapes to offer the best possible quality appearance while the process remains fast.
During pressing, steam and heat are applied from both top and bottom surfaces. Bottom steam is only used prior to pressing to help condition the garment, whereas top steam is used in the pressing operation to penetrate the garment and also act as a pressing force, reducing the need for pressure pressing. Vacuum at the buck draws steam through the garment to avoid condensation while the head acts as an iron and helps set the crease. Normally, heads either use Teflon-coated or fabric-covered aluminium or steel to help spread the top steam evenly over the entire garment. Buck pads and covers are porous so that the vacuum can dry and set the garment. The main purpose of the cover system is to help build good vacuum force during pressing, for good transfer of heat. Very high quality cover systems are generally made with the use of Kevlar/Nomexfibres to achieve good heat and pressure resistance, so that the cover itself is not deformed when heat and pressure are being applied. Generally vacuum is applied from the buck. In certain instances in jacket pressing, the head vacuum is also used to separate the plies to eliminate marks. Most automated pressing machines these days are fitted with an integrated suction on the steam head for some of the operations, because the head and buck are partially enclosed at the rear of the machine and if one does not extract the excess steam, then one may have moisture droplets or overspray of steam may hit the garment.
Most automated pressing machines these days are fitted with an integrated suction on the steam head for some of the operations, because the head and buck are partially enclosed at the rear of the machine and if one does not extract the excess steam, then one may have moisture droplets or overspray of steam may hit the garment.
Finishing
A standard form finisher for tops and bottoms is an automated way to apply steam and air to certain garments and is normally used in conjunction with hand pressing. A garment is placed on a dummy where it is steamed and blown out, thus eliminating 25-30% of the hand pressing. There are two different kinds of form finishers available, viz. the 2D and the 3D form finishers. 2D form finisher machines are used for shirts, sports jackets, casual jackets and dresses without inner linings, etc. whereas the 3D finishers are used for all kinds of formal jackets with or without the inner lining. The 2D style machine only steams and dries the garment; then one has to either press or touch up the garment. The 3D style machine steams, tensions and then dries, actually eliminating the entire touch-up process. 3D finishers for Jeans and casual trousers do not use inflatable dummy; the trouser itself is blown out, the steam passes through the densely woven fabric, removing the creases. 3D finishers for tops generally use inflatable fabric sacks of variable sizes which inflate by steam. The styles with centre open generally are not buttoned and centre plackets are kept overlapped and pressed by one vertical plate while garment is blown out.
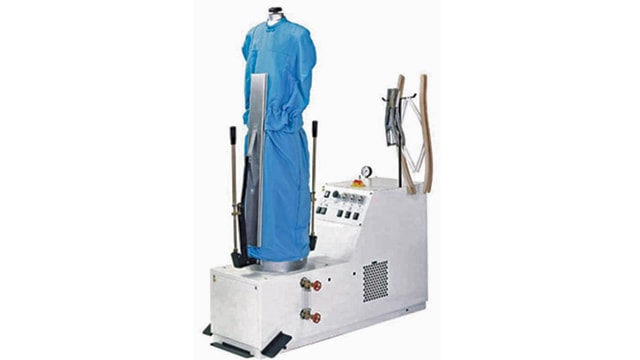
Form finishers come with two options: with or without hot air, which gives a high output of approximately 70-100 pieces per hour, at a low-cost and a rapid payback or cold air (warm air) to set the shape of the garment and give high finish quality. The two basic functions can be easily programmed as either ‘steam – hot air – cold air’ to start one after the other or, steam followed by hot air. Functions for both options can be timed to suit the type of garment to be finished. The extremely powerful blower is adjustable for all fabrics, from extremely light-weight to very heavy. Precise repetition of programme sequences is possible with microprocessor control. The special-purpose steaming dome includes a built-in dryer, which ensures uniform steam quality. A single operator can operate two such form finishers in tandem thereby creating continuous process from otherwise batch processes. This reduces the waiting time to increase productivity by around 50%. The individual dress forms turn through 360 degrees and can be exchanged within seconds.
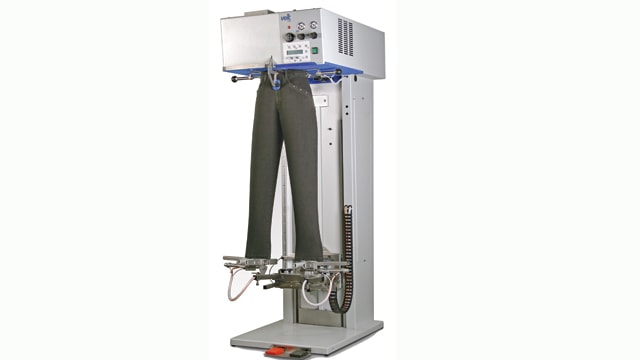
Tunnel finishing makes form finishing a continuous process, resulting in higher productivity and volume finishing. A tunnel finisher is an automated system where 90% or more of the hand finishing is done automatically. In tunnel finishing, the material is continuously moved in and out of the steam and air tunnel with the help of conveyors. These finishers are mostly used in refinishing the garments (taking out unwanted creases). Synthetic garments like polyester and nylon or blended fabrics are well finished with the help of tunnels since there are no contact surfaces. There are some garments that can be processed in a tunnel finisher without touch up, for example, T-shirts, some polos, lingerie and some types of dresses.
Conclusion
Form or tunnel finishers can also be used in combination with ironing. For example, when we dye garments or heavy wash in a garment is followed by tumble drying, we get severely creased garments. It is preferable to run the garments through a form finisher, tunnel or blower topper first and then follow it by pressing or ironing touch-up. In fact, there are quite a few examples of fabrics like casual shirts (seersuckers), fleeces, knitwear and also fabrics that have some special feel. Nowadays, with highly fashionable garments evolving day-to-day – most of which require good feel and handle – it is always better to finish them using a form finisher that helps in enhancing the finish of the garments. Companies these days also offer excellent shaping operations with the use of digital distance control systems (microprocessors) to cater to different thickness of the fabric to forestall excessive pressures due to contact, as contact and subsequent pressing may crush/damage the fabric texture in the garment. These microprocessors have programmable cycles for pressing, steaming, vacuum and retouch. Computer controls can be set to work with a variety of different fabrics to help remove shine or overpressing, also eliminating the risk of human error.