The technology of fusing machines has made gigantic strides over past 65 years since the introduction of polymer resin-coated interlinings for the garment industry. While most of the developments are drawn from the advancements in mechatronics and material science, the original three parameters: temperature, pressure and processing time still remain the same. Although the use of soft micro dot non-woven interlining has taken over from stiffer resin-coated woven ‘buckram’, use of electric irons is still prevalent as basic technology for fusing the interlinings to shell fabric. It is well said that both the interlining material and the fusing machines are equally important and neither inferior interlining can give better results by using superior technology nor inferior technology be compensated by superior interlinings.
Fusing is the process of fixing a fusible interlining with the outer fabric through the application of heat and pressure. In this process, the interlining and the outer fabric composite are heated up to a specified temperature (so that the adhesive reaches glue line temperature) as recommended by the manufacturer (depending upon the melting point of adhesive used in the coating). After a few seconds, when the adhesive becomes plastic, it is forced inside the fabric texture by applying pressure. After fusing is complete, the composite has to be gradually cooled down to convert the plastic adhesive into its original solid state to form a strong bonding.
The UK-based company, Stayflex, introduced the world’s first dotcoated resin interlinings in 1954 and invited a local engineering company, Reliant Tooling, to develop a machine suitable to apply this dot-coated resin interlinings and the static tray press was born. There are primarily two types of processes: batch process &continuous process.
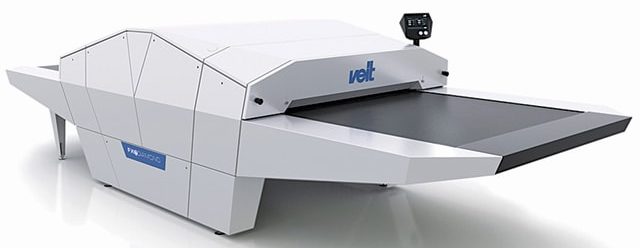
The three parameters — temperature, pressure and processing time — are the primary design criteria for any fusing press. In a typical flatbed press, the upper plate is electrically heated and unpadded, whereas the bottom plate is unheated and padded with a resilient cover of wool, felt or silicone. Top and bottom bucks can be covered with a PTFE (Poly Tetra Fluoro Ethylene) cover to prevent staining, adhesive build–up, adhesion of garment parts to the buck and assist in maintaining a clean surface. Heat is provided by an electric heater element embedded in the pressure plate. The heating element must be such that an accurate and uniform distribution of the temperature is obtained over the plate surface. The flatbed press is a batch process and loading and unloading of materials consume a lot of time in comparison to processing time, making the process very less productive. To improve productivity, factories often use a tray or frame to externalize the loading/unloading process thus improving productivity to a certain extent. Other disadvantages of flatbed fusing press are heat loss to atmosphere, simultaneous application of heat and pressure, and low pressure range. The only advantage of flatbed fusing press is that the material remains static throughout the process and hence gives distortion-free results for dimensionally unstable fabrics.
A double pass process is not necessary any more for KANNEGIESSER Double Pressure System, as the entire fusing good has to be warmed up again. According to all major interlining suppliers, this has to be avoided under all circumstances.
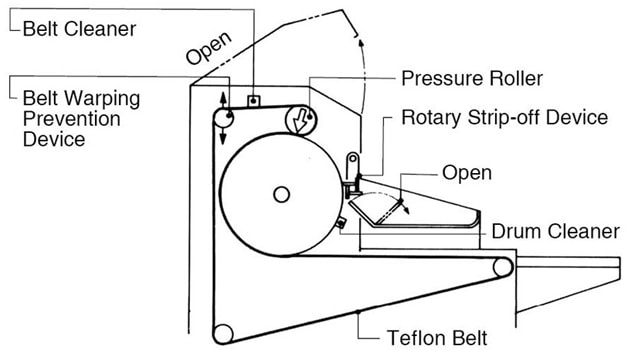
To solve the heat loss problem and separate out the pressure application from heat application, continuous fusing press was developed. There are two types of continuous fusing press: return feed conveyor system (also called drum continuous) and end-to-end conveyor system (also called flat continuous). In return feed conveyor system, one conveyor belt is wrapped partially around a drum surface where the drum is positively driven; the fusible composite is transported while being sandwiched between the drum surface and conveyor. The drum surface is heated through heating elements inside the drum. The fusible composite gets heated while being carried along the drum surface and the pressure is applied at the end while the composite is about to exit the drum surface. The cylinder consists of two parts: the inner cylinder, a stationary assembly in which the heating element are mounted; and the outer cylinder, which rotates around the inner cylinder. This principle ensures that the heat generated by the inner core is evenly distributed all over the cylinder mantle. Since approximately half of the cylinder-mantle surface area is in the actual heating zone at any given moment, the remaining area regains the heat lost through transference. The whole system is housed inside an insulated casing with two opening slits for entry and exit of fusible composite. While the drum is positively driven, the speed of both (the drum and the conveyor) must be synchronized in order to prevent the compression or extension of the materials. Since the composite goes around the drum surface and exits from the same side as the entry, these are called ‘return feed’. The limitations of these are slow conveyor speed (as the fusible interlining has to reach the glue line temperature during the traverse time around the arc of the drum surface), single stage heating and chances of distortion (due to arc travel path) of dimensionally unstable fabric.
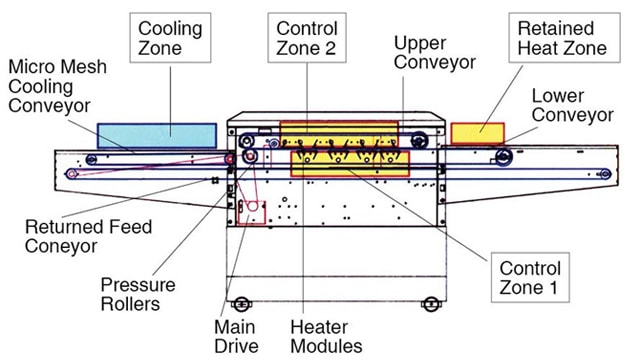
In 1970, Reliant introduced the first twin belt, continuous, straight-through fusing press utilizing PTFE-coated conveyor belts, also called end-to-end conveyor fusing press. Here the fusible composite could be transported continuously in volume through a heated tunnel with triple output. The tunnel which is terminated with a pair of silicon rubber nip rollers is able to deliver strong uniform pressure to the fused parts across the full width of the belt. The longer tunnel enables faster output in spite of achieving the glue line temperature. The end-to-end conveyor fusing press can accommodate multiple heating zones, enabling gradual heating which was a limitation in return feed. The heating systems generally used for end-to-end continuous fusing press consist of two heating surfaces that are positioned apart, with one above the conveyor belt and one below the conveyor belt. The surfaces are slightly arched to intensify heat diffusion. The lower heating surface is usually longer than the upper, and in relation to the conveyor direction, the lower heating source is positioned after the higher one. Both the panels can be separately controlled, which enables any temperature profile to be achieved. There can be a series of upper and lower heaters, which can create different heat zones.
Here the loading and the take-off areas are at the opposite end of the machine, thus allowing numerous opportunities to improve productivity. The use of separate loading and unloading conveyor, forces air cooling at the unloading end enables these fusing presses to be super productive. These fusing presses have numerous advantages such as gradual heating zones inside and pre-heater outside the fusing area ensuring that heat shock does not happen to sensitive fabrics during fusing (which is a common problem with viscose rayon, resulting in brittleness and texture change). This type of press can be of narrow width with one side open, thus enabling part fusing of shell fabric while maintaining the fabric texture and effective utilization of belt’s width.
As the technology has evolved over the course of time, control over achieving accurate temperature, pressure application and time for which the composite is fused has also improved.
Temperature
As the adhesives have a narrow melting range, temperature controlling was a perennial problem in old fusing presses due to inaccuracy of standard bi-metal thermostats, as they resulted in wider range of temperature variation which led to strike back and strike through in fused components. Use of Proportional Integral Derivative (PID) controlled thermostats improved the scenario as these devices not only measure temperature at source but also memorize the heat-loss cycle within the fusing press environment. These thermostats detect the drop in the press temperature at the exact millisecond-level and immediately electricity is supplied to the heaters to maintain the set temperature. The heaters continue to be powered until a stable temperature environment is re-established and then the electricity is terminated. These advanced systems not only ensure temperature accuracy in the order of +/- 0.5% of various machine settings but also offer the added advantage of minimal power consumption. It is also essential that modern fusing presses be efficiently insulated to maintain a constant heating environment within the press. If insulation is poor and/or there is heat loss, then the heaters would be in a constant state of operation and the power consumption will be high. It also makes the working environment uncomfortable and reduces productivity.
Glass-wool was traditionally used as an insulating material and nowadays Stonewool is being used by certain press manufacturers. While the source of heating is primarily electric, Macpi used to have fusing press heated by steam.
Stonewool was first identified on the islands of Hawaii. It comes from volcanic lava, which under special circumstances, produces fibrelike strands similar to wool in consistency. Today the process has been commercialized and Stonewool is produced on an industrial scale from abundant natural sources of lava rock. Its insulating properties are four times more efficient than fibreglass and it is much lighter than most of the equivalent products.
Pressure
The action of applying pressure in the fusing process is sensitive and precise as too much pressure will induce the evil strike-back or strikethrough and too little pressure will limit the penetration of the adhesive into the outer fabric. Pressure should be applied only after the adhesive has reached glue line temperature and should be uniform throughout. The very reason that heat and pressure is applied together in an iron or flatbed fusing machine, will be flattening of adhesive dots resulting in stiffening of fused components and inferior peel bond strength. In case of continuous fusing press, there are rollers which apply pressure on the composite. As the width of fusing presses increase, length, diameter and weight of pressure roller also increase, resulting in unequal pressure and inconsistent bond strengths. Computer–aided profiling of roller is done these days to achieve better accuracy. The pressure application can be mechanical, pneumatic or hydraulic.
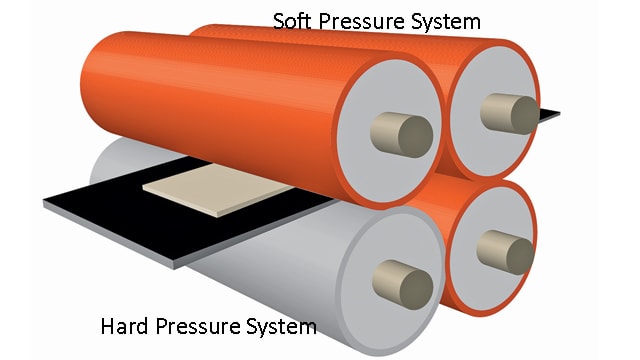
Through a unique technology used for the pressure system, KANNEGIESSER Double Pressure System offers a wide range of pressures applied to the fabric. The Double Pressure System consists of two separate pressure systems: first roller system with a relatively high line pressure (for formal shirts made of poplin); the second pressure system can be activated in case of soft fabric (silk and all casual fabrics) with more soft line pressure leading to a softer handle. In some cases, it is recommended to use both the systems at the same time. By this system, the glue dot is not squeezed and does not lose its dimension for an optimal fusing operation. The glue dot is not enlarged and remains small and compact. As a result, there is a good bonding and no strike through or strike back. This system can be adapted for a wide range of different combinations of interlining and fabrics. As both the pressure systems are independent from each other, they can be used individually or in combination in order to apply double pressure.
Processing Time
Processing Time is the time that composite spends inside the machine. In case of flatbed fusing press, it is either an analogue or digital timer, and for continuous fusing, it depends on the speed at which the belt moves through the conveyor press. Another important development is the inverter motor, which is now a standard component in most modern fusing presses. It safeguards the press from unreliable and fluctuating power supplies and permits the equipment to work under the most stressful of conditions. Most importantly, it ensures that the heaters are receiving the correct wattage of power.
The conveyor belts tend to shift laterally (called tracking) in most continuous machines. Earlier models employed a variety of simple devices to prevent the belts moving offline. The most popular mechanisms were pneumatic arrangements that kept the belt in a constant state of movement. Some technology relied on eyelets inserted in both edges of the belt connected to a pair of moving chains. Yet none of these methods could provide the reliability demanded of the industry that had such high productive dependability. Today, most machines use more reliable electronic tracking methods, whereby a sensor detects belt movement and an impulse is passed to the tracking roller motor moving the roller in a counter direction to the belt movement.