Today, joining of more than one ply of fabric is achieved predominantly by sewing which involves sewing needle and sewing thread as the enablers. The basic kinematics of sewing machine that we use today was developed during the beginning of the 19th century. Over the years, mechatronics and electronics have been added to enable better productivity, repeatability of output and consistency of quality. In the last one-and-a-half decade, the integration of computer and information technology made the machines capable of generating, storing and transmitting data automatically with ease of diagnostics and quick repair. Today, flexibility or multiple modes and materials of usage in one machine, user-friendliness at the operator level and clean output of garments have become the key factors, with an eye on ecological compliance as well as minimum expenditure on energy.
The most significant change that happened over time in the sewing machine today are direct-drive and dry head technology. In direct-drive mechanism, the external motor and belt drive are being replaced with in-built on-shaft motor resulting in reduction in energy usage. The dry head technology eliminated use of open tub lubricants and resulted in stain-free garments. Some of the future development trends are modularization & digitalization. In modularization, the machine head is split into two parts for creating different combinations & of machine head. In digitalization, the feeding of the fabric is de-linked from shaft drive and independently and digitally controlled, enabling a whole lot of possibilities in sewing.
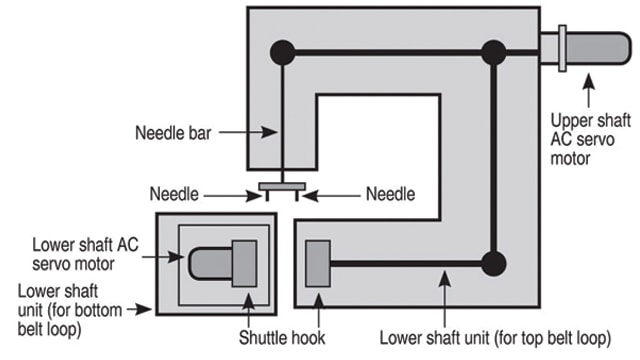
There was a time when increasing sewing machine speed was perceived to be directly related to higher production and hence was a challenge for the machine manufacturer. From a moderate speed of 2,000 SPM (stitches per minute), we have seen the development of 10,000 SPM overlock sewing machines. However, once the human limitation becomes very clear, i.e. whatever be the developments to speed up the stitch formation, there still will be two human hands aligning and adjusting the fabric being sewn together, the focus shifting away from sewing speed to reducing non-sewing elements, i.e. loading and unloading functions, aligning and adjusting, etc. Although basic sewing kinematics remained same over the years, minor characteristic differences between Japanese and German technology have emerged. Japanese preferred gear drive and pump lubrication whereas Germans banked on toothed belt drive and sealed forced lubrication. However, with current convergence in technology, direct-drive and dry head technology may be accepted as worldwide standard.
Traditionally the sewing machine gets single source drive to main shaft, which transfers motion to needles, take up lever, feed dog and hook/looper in a synchronized manner. The only radically different technology that was developed in recent past was from Tice Engineering, USA which delinked the functioning of sewing machine head and bed function. The Tice technology had freed the mechanical linkage to the bobbin, opening the doors for unprecedented versatility in sewing. Tice introduced the industry’s first double needle belt loop tacker and multiple head buttonhole sewer. Although in the past, Brother used this technology in several of its models, the technology was never popularized or commercialized. However, the release of Brother’s 7300 model may be an indicator of breaking the age-old principle of single source drive to multi-source drive sewing machine in future.
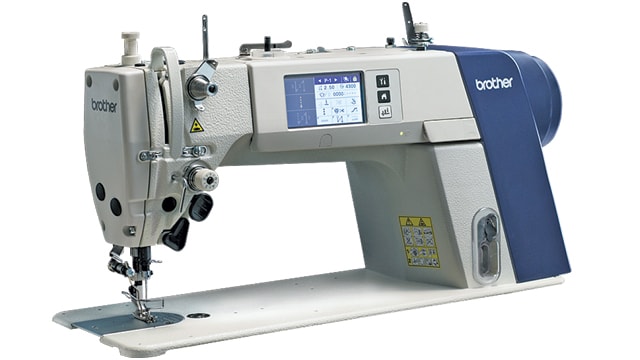
The use of lockstitch in automated workstations and cycle machines was limited due to continuity problem, i.e. frequent and inevitable bobbin changing requirement. Hence, automatic bobbin changer by Juki, Philip Moll and Kinoshita can be categorized as revolutionary developments in sewing machine history. While Juki used two interchangeable bobbins, Philip Moll and Kinoshita used bobbin magazines. Although Juki’s principle of using two interchangeable bobbins was a better option, it was never popularized or commercialized (for reasons known to Juki). However, Philip Moll’s and Kinoshita’s principle of bobbin changers is now becoming a regular feature in many cycle sewing automats.
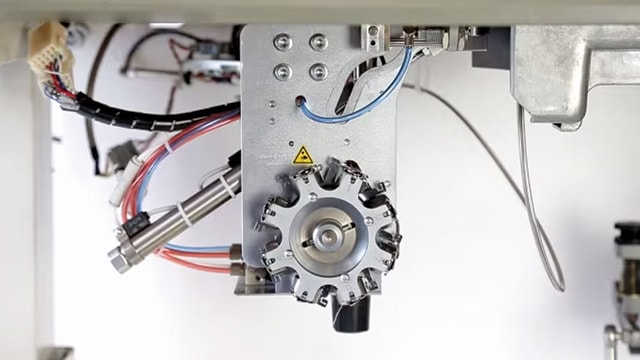
Although Macpi is known for its technology in pre- and post-sewing area, multi-stitch by Macpi was a revolutionary sewing concept developed by the company in the year 2000. For the first time, joining of two plies (by overlocking) and topstitching (double needle chainstitch) was achieved in one single operation. This development could not be popularized further due to the fact that use was limited (only to inseam operation in jeans, leg closing in knitwear) and did not offer any notable aesthetic or functional benefit over conventional lap seam method.
V Sewing machines are now available with drop feed and needle feed, interchangeable in same head, parallel chainstitch and lockstitch at same head (Vibemac and Kansai Special), unison to top and bottom feed convertible (by Typical Inc.), convertible bar tack to button sewing (by Typical Inc.), four needle parallel lockstitch and light to medium duty convertibility (easily switchable needle bar stroke in Yamato).
In the area of bed type, feed type and stitch type, there was no development for a long time. However, last decade has shown signs of change. Newer feed types like X-feed from Typical, Improvised Differential Feed from Megasew and User Defined Digital Feed from Brother are addressing the challenges of fabric feeding at an advanced level. Activeseam by Merrow and Zebra stitch by Pegasus are interesting developments in stitch types. Modular structure of machine head by Typical Corp (Vetron) and Duerkopp Adler (M-Type) will enable the use of exchangeable common parts between different machine types resulting in easy repair, lesser machinery inventory and reduced cost of ownership. Reduction of number of moving parts is another approach (adopted by AMF Reece eyelet buttonhole machine) which will reduce failure rate, help in ease of repair and lesser downtime.
IT Interventions
Since the computer controlled sewing machine hit the market about three decades ago, the urge to “computerize” the sewing machine function became a never ending exercise. It started with application of microchip or PLC (programmable logic controller) in sewing machine which helped to control and diagnose, store and reproduce the sewing machine functions better than manually possible. The following list is only a testimony to that:
- Programming stitch profiles (cross tack, crescent tack, etc.) in pattern tacking machine
- Controlling the speed of the machine (electronic stop motor)
- Programming the number of stitches in sewing bursts
- Controlling the feed dog movements
- Diagnosing the machine malfunction area
- Voice activated start-stop of machine
- Step motor for driving puller
- Computerized thread tension monitoring (active tension control from Juki and Yamato)
- Thread break/exhaust detector for needle, bobbin and looper
- On Line seam quality inspection (Clapp et. al.)
- Speed responsive presser foot pressure
- Elastic metering device
- Ply sensor integration
In the area of computer & IT integration, there are already computer controlled ‘Needle Throw-in’ zigzag machine (SunStar), USB based secure log in (Vetron), touch screen based easy diagnostic module for repair and mobile device integrated sewing machine (Pfaff).
Another example is the seam documentation system for car airbags from Pfaff, Duerkopp Adler and Juki where all stitch parameters are recorded online, while production pieces are sewn.
Different machine settings/ programmes are now transferable through ROM, PDA and other specialized devices. We now have zigzag sewing machine that can be connected to a laptop and any stitch pattern drawn on the computer can be reproduced directly by the sewing machine.
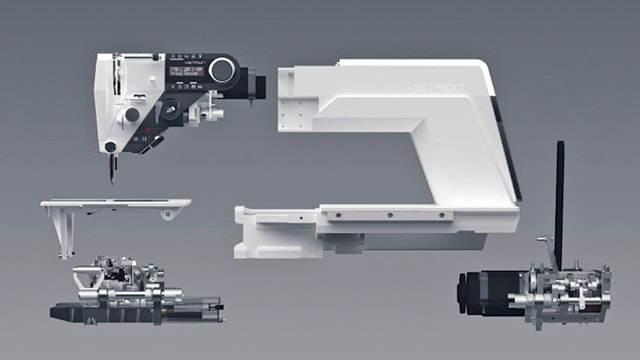
Ever since Efka (a sewing machine motor making company from Germany) showed real-time data capturing from sewing machine motor back in 2003, the market is buzzing with possibilities. The needle point data not only will help in monitoring operator and operation performance but will also help to prevent machine malfunction, preventive maintenance, remote programming, remote problem diagnostic and repair in near future.
In the area of computer & IT integration, there are already computer controlled ‘Needle Throw-in’ zigzag machines (SunStar), USB based secure log in (Vetron) and mobile device integrated sewing machine (Pfaff).
Flexibility
There was a time when the aim of every machine manufacturer was to create super specialization not only from product to product, but also within operations, and such need created sewing automats. For example, stitching a pair of formal trousers may require 5-6 different types of serging automats for inseam, outseam and crotch portions of the panel, apart from combinations. Such specializations improve productivity, but require large orders to justify the initial investment. With the general trend reversing towards small – order quantity and quick response manufacturing, now sewing automats are designed to perform multiple types of operations.
User-friendliness
CAM control to microprocessor control in buttonholing, button attaching and pattern tacking (bartack) machines dispensed with the requirement of a machine mechanic to change the sewing pattern. Now a sewing operator can easily and quickly change from parallel stitch to X-stitch button sewing by just pressing a button. Another technology that has been changed over the time in a button sewing machine is needle bar movement; while German machines used to come with laterally moving needle bar and clamp movement, Japanese machines used to have fixed needle bar with clamp movement. Today, due to the process of simplification and economization, all brands come with fixed needle bar with clamp movement sans the advantage of sewing collar button in a button-down shirt. The new looper thread take-up CAM system from Yamato is devised for quick and easy maintenance. The CAM is installed outside and it simplifies threading. Also, in case the looper thread winds itself on the CAM, the CAM can be removed quickly for unwinding the thread. This feature dramatically decreases the downtime. Besides, exchange of CAM can also be done quickly to meet various sewing conditions. Placing the different button function guides near the needle point is another convenience provided to the operators; the latest is the computerized overlock with touch panel like lockstitch machine.
With online connectivity becoming affordable, machine-to-machine (M2M) communication for all sewing machines and predictive maintenance will become a norm.
Clean Garment
Oil-stained garments were proving to be such a mammoth challenge, for manufacturers and retailers alike, that machine manufacturers were forced to develop dry head sewing machines two decades ago. Sealed upper needle bar from Yamato helps sew garments safely and cleanly. There are no moving parts on top of the machine frame and no oil leakage from the upper section of the needle bar for better working environment. The Juki MO 6000 series of overlock machines incorporates several mechanisms like changed needle bar structure, double gear oil pump, change of metal of upper and lower needle bar, three oil shield plates, changed diameter of oil pin hole, etc. to ensure no oil stain on the garment. Selfcleaning or lint collector system is another such hot selling feature in overlock and interlock sewing machine. Lint accumulation in and around the needle not only makes the garments dirty but also affects machine functioning. Lint accumulation in moving parts affects their movement as well as re-threading of the machine. Almost all specialized chainstitch, overlock and interlock sewing machine manufacturers like Yamato, Pegasus, Kansai are incorporating this feature in their machine.
Environment-friendly
Energy efficiency is a major concern for sewing machine manufacturers. The journey from clutch motor to servo motor to direct-drive was aimed towards minimizing energy loss. Lowering noise level and vibration not only reduces sound pollution, but also ensures increase in productivity. For example, in Brother 7200A, the brand new built-in direct-drive motor has an optimized design that utilizes magnetic field analysis and is the most compact motor of its type in the industry. Instead of using a V-belt, the drive power is transmitted directly to the mechanisms resulting in reduced energy loss to an absolute minimum.
It is interesting to note that all above developmental trends are interlinked. For example, a microprocessor controlled button sewing machine makes the machine flexible, as different types of button sewing may now be possible on a single machine. It also becomes user-friendly, as it is now possible for the operator to change the stitch type without any assistance from a mechanic. This also makes the machine IT-enabled, as any stitch program may be saved in a removable floppy/PDA device and copied to other machines.
Conclusion
With online connectivity becoming affordable, machine-to-machine (M2M) communication for all sewing machines and predictive maintenance will become a norm.
The development of near-endcontour manufacturing, i.e. three dimensional manufacturing in connection with robot technology and single arm stitching systems, is already well advanced and is taking definitive step towards 3D Sewing Technology.
Sewing with needle and thread, once considered the only means of joining components is giving away market share to unconventional technologies like welding, bonding and ultrasonic welding. Ultrasonic welding has a special niche since it welds, unlike those depending on heat, can be “adjusted” according to application. Since welded joints can be airtight, watertight and dust-tight, they are highly sought-after for biomedical application, extreme weather clothing and protective clothing.