Sewing of set-in sleeves in jacket is the most difficult of all sewing processes. Most blouses, jackets and coats have set-in sleeves. To sew set-in sleeves, the shoulder seams and the side seams of the bodice are already sewn and pressed open and the sleeve is also closed in the form of a tube. In this sewing process, circular opening of sleeve tube is set with circular opening at the armhole. As the two circular openings are dissimilar in size, the sewing involves differential easing of one ply of fabric (resulting in fullness in sleeve crown) and that requires skilled operator.
Professor Prabir Jana, Chairperson, Dept. of Fashion Technology, NIFT analyse the operation of dart sewing and the technology involved at the basic and highest levels. and Swasti Arya, MF Tech from NIFT discuss the technology available for the process at different levels.
The perimeter of armhole in jacket body part is bigger than the perimeter of armhole in sleeve. The crown portion of the sleeve armhole is required to be eased into the body part during sewing, which actually results into fullness and the puffed look of the armhole crown. In the sewing process, the body armhole is kept as an outer perimeter of the circle and the sleeve armhole is kept as an inner perimeter. The outer layer is the bottom ply during sewing and in contact with the feed dog; the inner layer is the upper ply and in contact with the presser foot.
Basic level of technology
At basic level of technology, the operator uses single needle drop feed flatbed lockstitch machine with edge guide for setting up of sleeves. As it is a drop feed machine, here the operator manually controls the differential over-feeding of top ply at the crown portion. Moreover, the overfeeding amount varies between front and back portion of sleeve crown. This manual control requires highest level of skill of the sewing operator to maintain uniformity of the fullness between front and back, as well as between right and left sleeves. This is probably the most demanding skill of any sewing operator and acquired over years of experience. One of the reasons behind why tailoring charges of suit is so high!
Some of the machine brands and models in basic level are JUKI DDL-5550N-7 and PFAFF 1053.
Intermediate level of technology
At intermediate level, variable top and bottom feed machines are used. One feeding foot at top (of the machine bed) and one feed dog below the throat plate feed the fabric plies together. The bottom of the feeding foot has a toothed surface. Feeding takes place while needle is outside the fabric plies. Here top feed and bottom feed amount can be independently adjusted to create inter ply slackness or tension in the fabric being sewn.
The presser foot is in two sections – one holding the fabric in position while the stitch is being formed, and the other (the feeding foot) having teeth on the lower side and moving or walking in such a way that the top ply is taken along positively while the needle is out of the material. Positive control of top ply allows for the overfeeding of the top ply, i.e. the sleeve armhole. With a variable top and bottom feed machine, the overfeeding amount between top and bottom ply can be set and does not require operator’s skills.
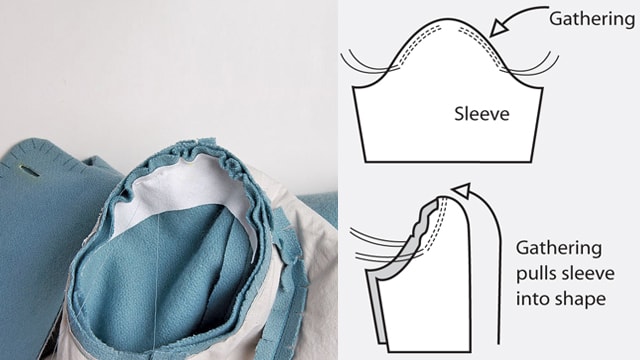
However, the overfeeding amount is not same in front, top and back portion of the crown of the sleeve armhole. The amount of overfeeding needs to be changed during the sewing process. There are still some skills required from the sewing operator to maintain the right amount of ease (by automatic overfeeding of the machine) at right places.
Some of the machine brands and models in intermediate level are JUKI DLU-5490N-7 and Duerkopp Adler 275-142342-01.
Advanced Level of Technology
At advanced level, programmable post bed lockstitch machines are used, which de-skills the operation completely. Post bed is often tilted forward for better visibility. To better handle the jacket body with sleeve, the post bed machines are provided with extended curved support. The feed system is top and bottom belt feed, where top and bottom speed can be independently adjusted. By introducing the belt feed, the machine reduces the teeth mark on the fabric made by the feed dog. These machines are equipped with right-and-left independent belt feed system. Right and left feed amounts can be adjusted separately. This prevents the material from slipping out of position, thereby sewing sleeves with a consistent seam allowance.
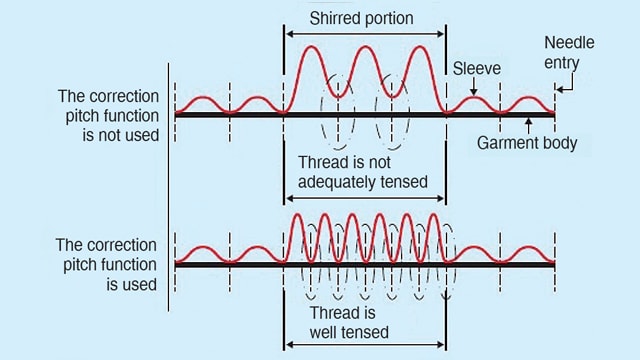
The machine comes with a mechanism provided for moving the belt feed and intermediate presser up and down alternately, enabling it to eliminate tucks produced at the sleep cap as well as irregular puckering produced in the neighbourhood of the sleeve cap. All the machines are equipped with active thread tension system that enables the separate setting of suitable thread tensions for sewing sleeves on a portion-by-portion basis. This prevents an inadequate thread tension at a portion where the shirring amount is large or an excessive thread tension at a portion where the shirring amount is small.
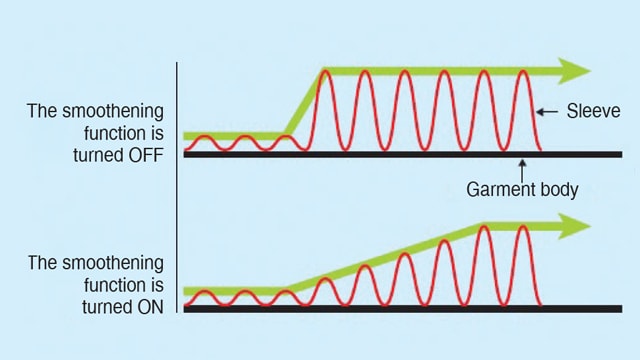
All the machines come with a touch sensitive colour LCD panel, which can visually display the circular sewn path and all the stitching parameters along the sewing path. Operator can easily program the overfeed amount, stitch length, thread tension and decide the starting point in the circular path which resembles the armhole of actual sewing product. Total sewing length is stored in the memory when sewing the portion between notch marks. This enables quick and easy programming of sewing data. When basic data is entered, the data is developed on a size-by-size basis. This helps save the operator from future program entering work. The stitching program can be easily mirrored for right and left sleeve and saved and transferred to other sewing machines through various kinds of media (such as a floppy disk, SmartMedia, CompactFlash and SD card) to enable 100 per cent consistency in quality.
Some of the machine brands and model numbers in advanced level are Juki DP-2100, PFAFF 3834, and 550-16-26-01 from Duerkopp Adler.
Many additional features in the advanced level machines make the job of sleeve setting absolutely de-skilled. Juki DP-2100 comes with smoothening function and correction of pitch setting function. In smoothening function, the machine prevents an abrupt change in the shirring amount at the sewing-step changing point, thereby upgrading the finished quality of seams. In correction of pitch setting, the stitch pitch can be changed on a portion-by-portion basis. Seam grinning can be prevented by decreasing the stitch length at a portion where the shirring amount is large.
550-16-26-01 from Duerkopp Adler has programmable sewing foot alternation to sew over thick crossover seams (epaulettes, etc.). PFAFF 3834 on the other hand uses a puller feed system, which uses the roller presser (running close to the needle) by which the material can be precisely inserted. This guarantees flexible work with an unobstructed view of the work piece. An additional small puller behind the needle ensures optimum material handling. The machine enables a neat seam design and consistent stitch formation, especially when processing delicate fabrics. PFAFF 3834 also offers sewing of pre-gathered sleeves.
Return on Investment for basic and advanced levels of technology is shown below: |
||
Basic Level of Technology | Advanced Level of Technology | |
SAM value for two sleeve setting (min) | 3.16 | 0.70 |
Production per day (shift of 8 hours) | 151.90 | 685.71 |
Working days /month | 26.00 | 26.00 |
No. of months /year | 12.00 | 12.00 |
Production per annum | 47392.41 | 213942.86 |
CM price per pair of sleeve ($) | 0.12 | 0.12 |
Cost output/annum ($) | 5744.53 | 25932.47 |
Production Target (pcs/day) | 685 | 685 |
No of machine required | 5.00 | 1.00 |
Cost of one machine ($) | 750.00 | 13500.00 |
Cost of total machine ($),T | 3750.00 | 13500.00 |
Annual Depreciation (%) | 0.15 | 0.15 |
Depreciated value of m/c after one year (Z) | 3260.87 | 11739.13 |
Salary of one operator p.m ($) | 130.00 | 130.00 |
Total operators salary per annum (Y) | 7800.00 | 1560.00 |
CM price from total m/c (X) | 28722.67 | 25932.47 |
Cash Inflow (X-Y=I) | 20922.67 | 24372.47 |
ROI for the first year (X-Y)/Z in % | 6.42 | 2.08 |
[The ROI calculation is only an indicative figure based on labour cost factor. The actual figure may change based on other savings in terms of space, utilities, etc.] |