Sewing is the most important activity in garment manufacturing due to the multiplicity of machine types involved and amount of time taken by an operator in a given environment and factory condition, which goes on to define the quality of the garment. Having said that, the 1000 lux required at the needle point for quality work can be achieved using various lighting systems. Various types of lights with different lumens and colours are commonly available in the market but it is the incandescent bulbs and fluorescent tubelights which are most commonly used on the shopfloor, and among them fluorescent lights are used little more extensively in garment factories, giving a much needed clarity to the subject.
Professor Prabir Jana, Chairperson, Dept. of Fashion Technology, NIFT analyse the operation of dart sewing and the technology involved at the basic and highest levels and Kanupriya, an MF Tech from NIFT, New Delhi analyze the different levels of technology in lighting used on sewing floor.
Basic Level of Technology
Fluorescent Tubelights on Lighting Frame and Ceiling
Fluorescent tubelights have been in use in the industry from the very beginning on the ceiling as well as in the lighting frame, typically constructed along the sewing line 8 feet above the floor level. T8 fluorescent tubelights are now commonly used on sewing floor as cool white colour is considered appropriate by apparel manufacturers since it lasts longer than traditional T12 and has greater lumen maintenance over time, besides being manufactured by numerous brands at competitive prices. One primary difference between T8 and T12 fluorescent tubelights is the size of the tubelights and their bases. While both tubelights come in standard lengths, commonly four feet, the number 8 or 12 refers to the difference in the diameter of the tubelights. T8 tubelights are one inch in diameter, while T12 tubelights have a larger diameter of one-and-a-half inch. According to Philips, a maker of light tubelights and lighting equipment, a T8 tubelight produces around 2600 lumens, while the T12 tubelight puts out around 2520 lumens. Over the time the tubelights begin to lose their intensity and brightness while T8 tubelights have a slower period of decrease, losing only 10 per cent of their initial brightness after 7,000 hours of use. In comparison, T12 tubelights can lose 20 per cent, or double the T8 loss, after the same number of hours.
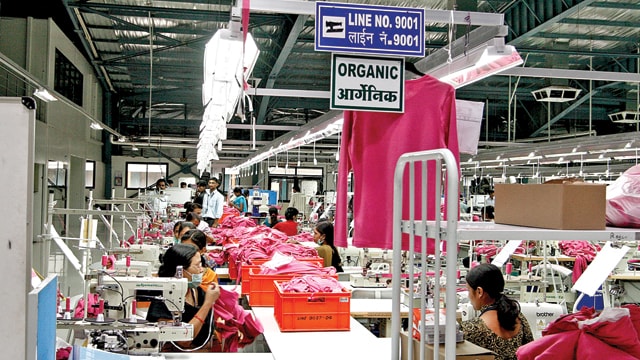
In basic level of technology, the required 1000 lux at needle point is achieved using the combination of lights used in lighting frame and ceiling. T8 fluorescent tubelights are fitted at lighting frame as well as ceiling. Ceiling is at 10 feet (304.8 cm) height and lighting frame is at 8 feet (234.8 cm) above floor level, and height of workstation is approximately 76.5 cm. Taking in consideration the distance of the needles point from the ceiling light source and from the lighting frame light source, the illuminance at the needle point would be 16.38 sq. m due to ceiling light and 8.76 sq. m due to lighting frame light. Hence the lux (lumen per sq. metre) from both the light sources at the needle point would be 296 and 158, respectively.
With 2 tubelights at lighting frame and 2 tubelights at ceiling, total lux generated will be a total of 910 lux. Therefore, 30 T8 fluorescent tubelights at ceiling and 30 T8 fluorescent tubelights at lighting frame will be required for the complete sewing line of 30 machines. The power consumption for one hour of 60 T8 fluorescent tubelights will be 30 x 36 watts, i.e. 2160 watts.
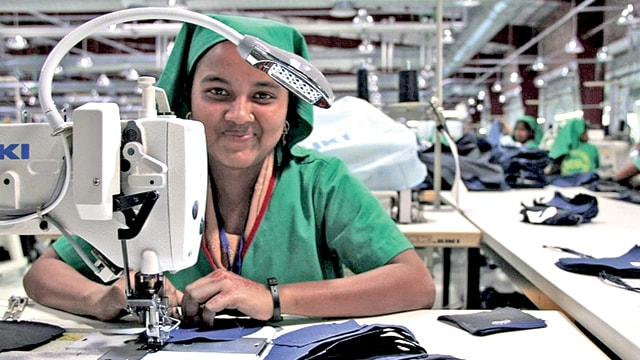
Advanced Level of Technology Combination of LED Needle Point Lights & CFLs at ceiling
In comparison to CFL, LED lights consume 15-30 times less power (<0.5 watt) and offer wider range of lux from 800~1600 lux.
Again in the same setup of a 30 sewing machine line, lights are removed from the lighting frame, along with the frame itself. The LED based needle lights at each sewing machine are the only source of light, which is complimented by CFL at the ceiling, 10 feet above the floor. CFL at ceiling is providing the ambient lighting at the shopfloor and LED needle lights are providing work lights at the sewing machine. Considering the distance from the needle point, the CFL lights of 50 watt each at the ceiling operating at 47% efficiency will produce approximately 80 lux, one LED needle light will produce 920 lux. So, the total lux generated at the needle point with the LED needle light and ceiling CFL lights would be 1000 lux. Therefore, 30 needle lights at the sewing machines and 15 CFL lights at ceiling will be required, and the power consumption for one hour would be a total of 765 watts, with each needle light consuming 0.5 watts and each CFL light consuming 50 watts.
Assumptions
• There are 30 sewing machines (15 machines in each row).
• Length of lighting frame is assumed 60 feet for the whole line.
• There are 26 working days in a month and 12 working months in a year.
• 20 garments are produced per machine per day and Rs. 40 is the CM per garment.
So total annual CM per line is 20 x 40 x 26 x 12= Rs. 2,49,600
Return on Investment
Another way to calculate ROI in above case, and which is more realistic is:
Total cost of electricity savings per year = (35043.84 – 12411.36) = Rs. 22,632.48
If we take a company currently in basic level of technology switching to advanced level, then it will make additional investment of Rs. 24,600
Payback period is Rs. 24,600/Rs. 22,632.48 = Rs. 1.08 year
Payback period considering depreciation = Rs. 21,391/
Rs. 22,632.48 = Rs. 0.95 year
[Standard Service Illumination in different work areas. Source: ILO Manual]
Table 1 - Return on Investment |
||
Basic Level of Technology | Advanced Level of Technology | |
Wattage consumed per hour | 2160 | 765 |
Working months/year | 12 | 12 |
No. of days/month | 26 | 26 |
No. of working hours | 8 | 8 |
Light consumption per annum(w/h) | 5391360 | 1909440 |
Light consumption per annum (kw/h) | 5391.36 | 1909.44 |
Cost of electricity per kw/h | 6.5 | 6.5 |
Cost of single unit of light | 1400 | Needle light @ 420 and CFL @ 800 |
Number of units | 30 | 30 needle light & 15 CFL |
Cost of all lights | 42000 | 24600 |
Cost of false ceiling @ 1000 per running ft. | 60000 | 0 |
Cost of electricity per year(x) | 35043.84 | 12411.36 |
Total cost of light + peripherals | 102000 | 24600 |
Annual depreciation (%) | 0.15 | 0.15 |
Depreciated value of light after one year (Z) | 88696 | 21391 |
CM price from total line (X) | 249600 | 249600 |
Total cost of electricity per year (Y) | 35043.84 | 12411.36 |
Cash inflow (i) | 214556 | 237189 |
ROI for the first year,(X-Y)/Z | 241.90% | 1108.81% |
Payback period (t/i) | 0.48 | 0.1 |
Table 2 - Lighting Standards |
|
Work Area | Standard Service illumination (Lux) |
Storage area and plant room with no continuous work | 150 |
Casual work | 200 |
Rough work: rough machining and assembly | 300 |
Routine work: offices, control room, medium machining and assembly | 500 |
Demanding work: inspection of medium machining | 750 |
Fine work: colour discrimination, textile processing, fine machining and assembly (sewing) | 1000 |
Very fine work: hand engravings, inspection of fine machining and assembly | 1500 |
Minute work: inspection of very fine assembly | 3000 |