Important factors for shirt finishing would be a completely pressed collar, flat-pressed shoulder and armhole seams, at-pressed pockets and a smooth hem without any wrinkles.
However it is important, to distinguish between the finish of a casual shirt with that of a formal dress shirt since a casual shirt can be finished with the help of any basic or advanced level of technology, a formal dress shirt may require part use of basic technology (in touch up operations) over the highest level of technology, viz, tunnel finisher.
Basic Level of Technology
Steam Irons with Vacuum Tables
Typical Work-Cycle Elements of Ironing: Pick up Position > (vacuum on) > Steam (vacuum off) > Iron > Vacuum (remove residual steam) > Dispose off
This is the oldest and popular method for finishing shirts. Steam irons are ergonomically designed to provide effortless operation and superb finish. Steam irons may have several unique features like digital temperature control, detachable heater elements, a hard-coated aluminum base, Teflon shoe and silicon pad. The steam passages allow unilateral flow of steam all over the garment. The hot steam produced at high pressure and temperature helps remove wrinkles easily. Macpi’s ‘precise’ iron and VEIT ‘HP 2003’ offers accurate temperature control [within +/- 20C (+/- 30F)], which aids in the ironing of temperature sensitive fabrics without marks.
Machinery and Equipment Required for Basic Level of Technology (Steam Irons):Steam Iron, Boiler assembly, Power Supply, Vacuum table, Storage rack |
|
Makes and Models | Features and Specification of Machinery and Equipment |
VEIT iron HP 2003 & VEIT table HD 2128, Macpi iron 035.90 & Macpi table 167.701 | Ironing surface: 220 x 105 mm to 200 x 115 mm to 1300 x 700 mm |
Connected Load W/ Volt/ Hz:1250/ 230/ 50-60 | |
Consumption: 1,8/4,65 Kw/h (according to the model) | |
Iron weight : 1.25 to 3.5 Kg | |
Temp: 130 - 2500C |
The vacuum table comes generally in a rectangular shape with pedal controlled air suction. The vacuum helps in retaining the garment flat and wrinkle free in shape during ironing and removing the residual steam after ironing. A good industrial vacuum board may have features like: superior and selective suction, durable components, sound insulation and anti-rust features. The vacuum table also comes with certain additions like inclination (Macpi 17.701), electrically heated buck (Macpi 17.701), height adjustment (Veit HD 2128) with the possibility to be fitted with one or two swing-arms (to facilitate buck ironing).
Vacuum tables are universal and primarily used for ironing woven garments. Upsteam table (for knitwear) and an air blow table (for gathered/frilled garments) are other variations of the ironing table.
Ironing using vacuum tables is characterized by the rubbing of two surfaces (thus altering fabric texture), a small area of contact (thus less productive), batch processing (thus less productive) and lastly, the need for skilled labour, which are the basic disadvantages at this level.
Intermediate Level of Technology:
Buck Presses & Form Finishers
Work-Cycle Elements of Steam Buck Press Operation:
Load & position > Steam > Buck head close (predetermined time) > Vacuum > Buck head open > Unload
Buck Presses
Buck presses are primarily for shaped garments where flat surface ironing is not possible, like suits, dress shirts, etc., as they give faster and superior quality pressing and are less labour intensive. Buck presses for dress shirts are classified by an apparel section name, such as collar, sleeve, front, back or shoulder which describes the basic form and utility of the buck. A typical buck press system for a dress shirt will require an assembly for different bucks for pressing different parts of the garment.
Machinery and Equipment Required for Intermediate Level of Technology (Buck Presses): Buck presses, boiler assembly |
||
Makes and Models | Features and Specification of Machinery and Equipment | |
For Collar and Cuff Buck Press | VEIT – TrioStar, Macpi 209.07.9109 | Dimensions in mm: 1100x1150x1600 approximately |
Working Air Pressure: 6kg/cm2 | ||
Air Consumption in l/min: 31.45 | ||
Connected Load kW/ Volt/ Hz: 2/ 3 x 23 0/ 50-60 | ||
For Front Placket Buck Press | VEIT – FPD Macpi 506.17.9120 | Dimensions mm: 1400x1120x1600 |
Weight kg: 420 | ||
Working Air Pressure bar: 6 | ||
Air Consumption in l/min: 1200 | ||
Connected Load kW/ Volt/ Hz: 2.1/ 400/ 50 | ||
For Sleeve Finishing Buck Press | VEIT – SFD Macpi 506.17.8506 | Dimensions mm: 1350x2540x1900 |
Weight kg: 460 | ||
Working Air Pressure bar: 6 | ||
Air Consumption in l/min: 860 | ||
Connected Load kW/ Volt/ Hz: 10.6/400/50 | ||
For Shirt Body Press | VEIT –VertoStar, HPV2 Macpi - 288.00, Colmac 3-CPU | Dimensions mm: 1800x1300x1810, 2345x113 5x1745 |
Working Air Pressure bar: 4.49-8.63 | ||
Air Consumption in l/min: 120 – 215 | ||
Connected Load kW/Volt/Hz: 12.5/3x400/50-60 | ||
The above specifications are indicative and may vary from company to company. Also the working principle may differ, e.g., while the Veit-Kannegieser machines are actually electric heated and do not consume steam, Macpi machines are steam heated and the utility consumptions are different. |
The various categories of buck presses have been discussed below.
Collar and Cuff Buck Press
This machine has been especially designed for pressing collars and cuffs of both blouses and shirts. It can also be used as a neck press. There are adjustable pressing forms for cuffs to adjust automatically to the shape of the lower form. Flexible heating mats guarantee an even distribution of temperature and pressure over the whole surface. There may be a manual spraying device and a suction unit. The suction unit makes it easier to position collars and cuffs before pressing and optimises cooling down after pressing. The pressure can be adjusted very sensitively for all kinds of fabrics. Features like digital temperature, electric heated mat, adjustable cuff size, vertical closing of the heat mats, mat to take the shape of the lower buck are typical /unique advantages of VEIT-Kannegieser Triostar while Macpi 209.07.9109 scissor press for collar and cuff is supplied with an Air Cushion System and Spray Unit.
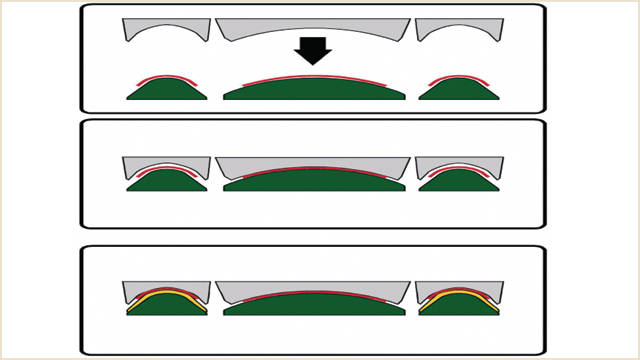
Front Placket Buck Press
A good example is the Veit-Kannegieser FPD, which can combine both the fusing and pressing.
The design of the heating plate is arranged to avoid temperature fluctuations, thus guaranteeing a stable set temperature. Sensitive setting for different materials is possible as pressure is infinitely adjustable. The padding of the bucks assures an ideal fusing and finishing result. The programmer ensures exact adjustment of pressing time, actual and set temperature and suction time. Suction makes it easier to position the garment exactly before pressing and guarantees an optimal cooling down after pressing. A clamp at the front of the machine can hold a number of front plackets in order to work according to the waterfall principle. It also helps to improve workplace design. Apart from the placket, there are also scissor presses for front and back shirt pressing (e.g., Macpi 209.17.9102).
Sleeve Finishing Buck Press
This machine gives a good pressing result for all kinds of sleeves due to its variable adjustment possibilities. The design of the heating plate is arranged to avoid temperature fluctuations, thus guaranteeing a stable set temperature. Sensitive setting of different materials is possible as the pressure is infinitely adjustable. For example, in the Veit Kannegieser SFD, the lower pressing buck can be moved sideways and oscillated. This guarantees ideal pressing of all kinds of armhole designs without change over. A laser pointer shows the exact position of the sleeve. The programmer ensures an exact adjustment of pressing time, actual and set temperature and suction time. Suction makes it easier to position the garment exactly before pressing and guarantees an optimal cooling down after pressing.
Shirt Body Press
The shirt body press presses the complete back, yoke, shoulders and front part including the breast pocket. Main features are vacuum dummies, double operating dummy for left and right, computerised control, built-in vacuum unit and automatic water spraying unit. The working principle consists on the upwards extension of the dummy after the pressing plates closure. In this way, the fabric is spread perfectly on the shoulder, securing a faultless result. The automatic water spaying unit is also very innovative. While Macpi 288.00 has revolutionary dummies with vacuum and with extensible devices on the sides for different sizes, retractable sleeve supports and pneumatic collar clamp, Veit Kannegieser’s oil heated, stainless steel bucks help to press post cure /vapour phase wrinkle free processed shirts.
The shirt forms are available in different sizes (for wide, standard and narrow shoulders) the shirt forms adjust automatically to every side seam form. Productivity of up to 1900 shirts/ 8 hours can be achieved due to the overlap operation method (simultaneous pressing and loading). Through the extensions like loading systems and transfer systems, up to 2400 shirts/8 hours can be pressed.
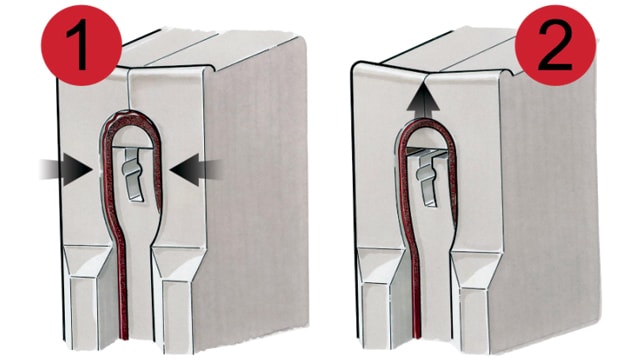
The shirt can also be pressed also by means of a carousel. The Macpi – 506.17.9119 carousels have been designed to grant high productivity and reduced running consumptions, mantaining a high standard quality. Macpi models are 180° and 1200 carousels for small and big shapes. Working on 2 traditional pressing machines the operator moves between both machines for the shirt loading/unloading. With the new carousel, the shapes move and the operator stand still with a considerable reduction of production downtime.
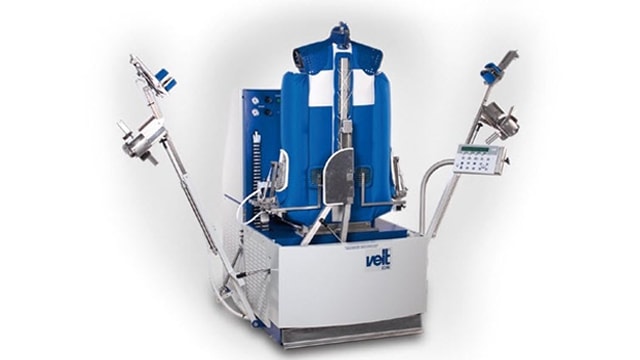
Form Finishers
Form finishers achieve crease free hem finishing and operate on continuous cycles of steam and hot air. It is ideal for achieving final finish of shirts removing all tardy wrinkles. Around 40-160 garments can be form finished in an hour.
Machinery and Equipment Required for Intermediate Level of Technology(Form Finisher): Form finisher, boiler assembly |
|
Makes and Models | Features and Specification of Machinery and Equipment |
VIET- 8346, 8325 Macpi 389.00 | Working Air Pressure bar: 6 |
Air Consumption in l/min: 12 l/cycle | |
Steam consumption: 40 Kg/h | |
Connected Load kW/ Volt/ Hz: Around 2.2/ 400/ 50 and 2.2/ 200-240/ 50-60 |
Basically, form finishers are designed to eliminate positioning and repositioning time in a ironing/pressing work cycle.
Work-Cycle Elements of Steam Bag Form Finishers Without Timers
Loading and Positioning > Steaming (predetermined time) > Hot Air Blowing (predetermined time) > Unloading
The main features of the form finisher are the body, back, shoulders, sleeves and sides locking devices. Other features are automatic clamps adjustable in height, automatic side tensioning – hot and cold air blowing – turning and translating front plate. The pneumatic sleeve tensioners finish the cuffs without leaving marks. All functions are programmable by a Programmable Logic Controller(PLC), but can be manually overridden to obtain the best finish under any conditions and with any kind of fabric. The finisher is equipped with a powerful hot-air fan that reduces fixing and drying time and thus increases productivity. A clearly arranged display panel shows all the important functions at a glance. Tandem processing can increase the productivity.
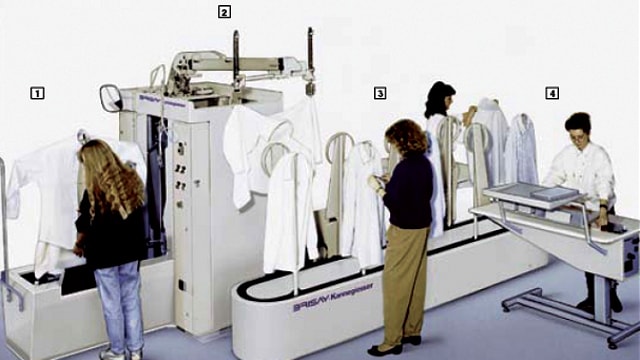
Macpi 389.00 adopts a special plate movement for the pressing of shirt front placket, which allows getting the dummy to a lower position, facilitating the shirt loading operations.
Highest Level of Technology
Steam Tunnel Finishers
This is a finishing process where pressure is not applied to the garments but where handling during the process is reduced. It can be used mainly for casual shirts in man-made fibres and blends. The garments are mounted on hangers and are fed under automatic control through a cabinet on a motorised rail, passed though sections with superheated steam, and dried by air blowing. With these finishers one can achieve high output capacities (up to 3000 garments/h) with consistent high quality.
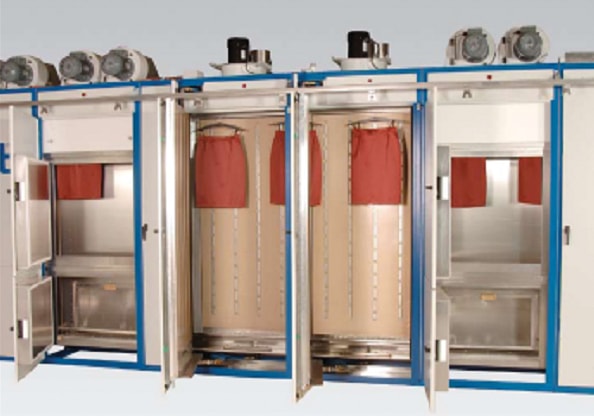
Tunnel finishers usually are made up of modules, which can be combined as per requirement.
Machinery and Equipment Required for Highest Level of Technology:Tunnel finisher & conveyer system (optional) |
|
Makes and Models | Features and Specification of Machinery and Equipment |
VEIT 8346, VEIT 8656, Macpi 533.01, Macpi 533.02, Colmac CFS1200 | Operating unit: Touch screen |
Distance between hooks (optional) mm: 200-900 | |
Centrifugal fans with electronic control of variable capacity: 2 | |
Heat exchanger: 2 | |
Steam pressure: 7/9 BAR | |
Steam consumption: 75/115 Kg/h to 100/150 Kg/h | |
Length/length with conveyor mm: 2280Height and width mm: 2300x1950/2750, 2280x2700/3500 | |
Connection to compressed air: 4.49-8.63 BAR | |
Installed power: 2.3-4Kw | |
Electric feeding: 3+N~50Hz 400 V |
1. Pre-heating Module
This is optional, to refinish the garments. In this process, the garments are pre-heated with medium temperature and air to ensure better absorption of the steam.
2. Steam Module
The finishing process requires that the garments are sprayed with steam directly or, depending on the length of the fibres, indirectly. The required amount of steam can be regulated infinitely from 0 up to 100%. In each steam module, the amount of steam and the injection can be adjusted individually.
3. Air Module
One or more air modules smooth and dry the garments. In this process the programmed quantity of air with the corresponding temperature flows down the module past the garments.
4. Blow-off funnel
To give the garments the corresponding volume when leaving the Tunnel Finisher (doll effect), the garments are opened from below with the remaining heat to give them the appropriate shape. Each module has its own display with a bar chart and direct input for the parameters to be programmed. The programmed and the actual temperature are displayed in a corresponding colour combination. In Veit Model 8625, it is also possible to activate interface links and program settings via an RFID interface.
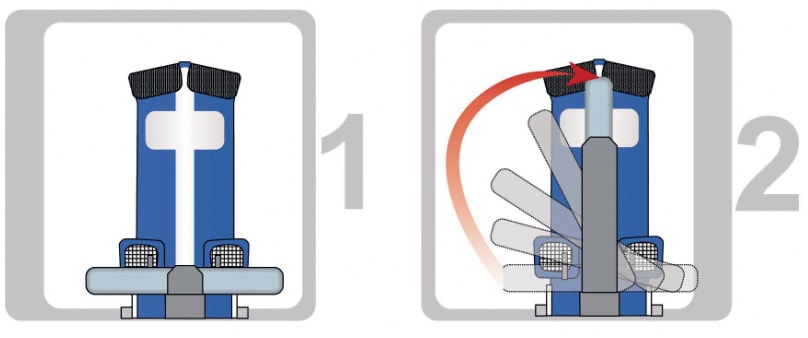
Macpi 533.01/02 introduces a new concept, based on research and tests, providing results which demonstrate significant improvement in efficiency and productivity. The working cycle starts behind closed doors and with stationary garments. The fluids (steam and superheated air) are introduced with a forced circulation in both directions, allowing the garment to be treated effectively, reaching also the most inner fibres. A located airflow allows cooling of the hanger in the most critical point (see picture), avoiding its deformation at high temperatures. The steam humidity level is controlled by an electropneumatic valve managed by PLC through a pressure transmitter and electronic converter.
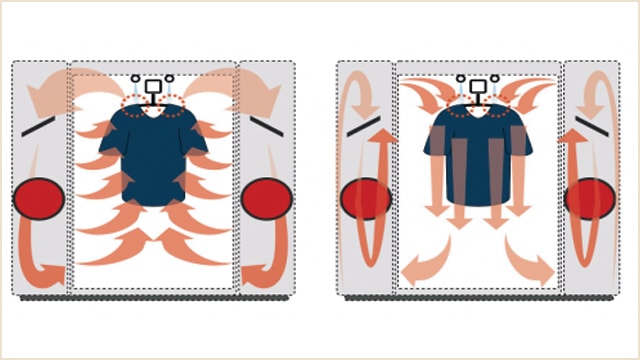
The closed (batch) processing method creates the most versatile finishing system, enabling the economic production of very long or short runs on a Quick Response basis. Furthermore through this system we can obtain total control of any internal parameters: air (quantity, flow, temperature, direction speed) steam (quantity and quality, degree of humidity) and times, giving the best quality results.