Darts are generally featured in ‘A’ zone of the garments and thus require quality sewing. Length and pitch consistency between the left and right components is of utmost importance. Even though sewing of darts is such a small and simple operation, it often irks one’s imagination into analysing machinery and equipments used for the same.
Vasuta Kalra, BF Tech from NIFT (Apparel Production) and Professor Prabir Jana, Chairperson, Dept. of Fashion Technology, NIFT analyse the operation of dart sewing and the technology involved at the basic and highest levels.
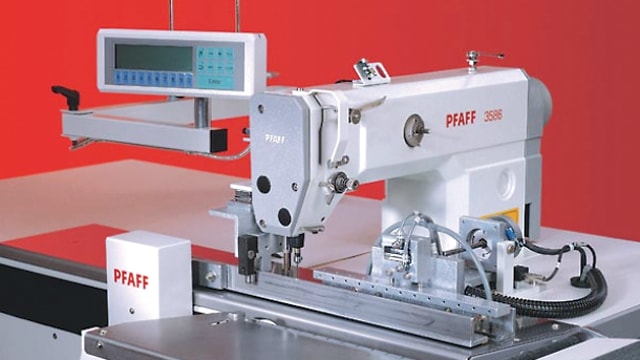
Basic Level of Technology
Darts are of different shapes and sizes and are used in both tops and bottoms. The basic level of technology for Dart Sewing is a programmable Single Needle Lockstitch (SNLS) machine with or without an Under Bed Trimmer (UBT). The operator can be skilled, or at the least, semi skilled. Marking of a dart needs to be correct and consistent. The operator either marks the dart length on the fabric with the help of a ruler, or notches are marked for dart end and a drill mark is there for the dart tip. The operator folds the dart into half matching the notches together and sews straight or in a slightly curved line connecting the notches and dart tip point. Maintaining consistency of the straight or curved profile in every piece is very important and depends solely on the operator’s skill as little is provided to him in the form of sewing aids.
Equipment needed for basic level: Single Needle Lockstitch machine with or without UBT, ruler, marker. |
|
Makes & Models | Features & Specification of Machinery & Equipment |
JUKI DDL5550N-7 Series, Brother S7200 A Series or equivalent | Max. sewing speed: 3,500 spm to 5,500 spm |
Max. Stitch Length: 4 mm to 5 mm | |
Needle bar stroke: 29 mm to 35 mm | |
Lift of presser foot: 6 mm to 16 mm | |
Lubrication Type: Full, Semi or Dry Head |
Intermediate Level of Technology
This level of technology requires a programmable SNLS machine (with UBT) along with a template for dart sewing and a compensating presser foot to sew along the edge of the template. The use of a template ensures consistent quality and saves the time needed for manually marking the dart on the fabric.
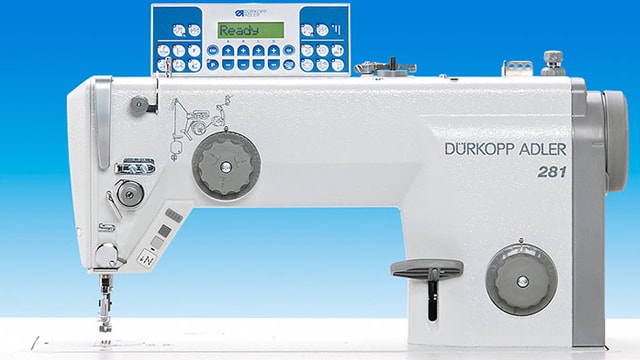
Some machines, like Durkopp Adler 271/271, come with a thread nipper. At the beginning of a seam, a thread nipper pulls the needle thread and holds it underneath the fabric while the first stitch is being formed. This prevents thread cast-off or a skipped stitch and ensures a neat seam beginning.
Equipment needed for intermediate level: Single Needle Lockstitch machine with dart template |
|
Makes & Models | Features & Specification of Machinery & Equipment |
JUKI DDL 9000 Series, DURKOPP ADLER 271 / 272 or equivalent | Max. sewing speed: 3,500 spm to 5,500 spm |
Max. Stitch Length: 4 mm to 6 mm | |
Needle bar stroke: 29 mm to 35 mm | |
Lift of presser foot: 8 mm to 13 mm | |
Lubrication Type: Full, Semi or Dry Head |
Highest Level
The highest level of technology available for dart sewing is an automatic workstation where a required dart template is fixed on the machine. The operator simply places the fabric on the machine, aligns it according to the table or template markings and starts the machine. The dart is automatically sewn in the required shape, size and depth. The thread trimmer trims the threads and the work piece is ready to be manually removed from the machine.
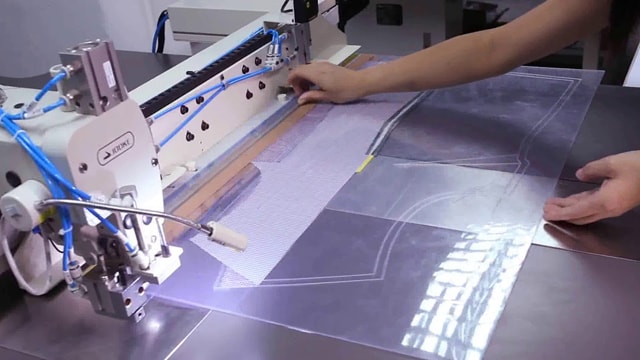
Equipment needed for highest level: Automatic dart sewing machine, machine templates or sewing programs. |
|
Makes & Models | Features & Specification of Machinery & Equipment |
PFAFF 3586 - 2/ 01, 3586 - 2/ /02, DURKOPP ADLER 743-221 or equivalent | Single needle lockstitch or chainstitch with UBT |
Max. sewing speed: 4,500 spm to 4,800 spm | |
Dart Length: Up to 250 mm | |
Dart Depth: Up to 30 mm | |
May use Computer Programming or Dart Templates |
The advantages of an automatic dart seamer are:
- Constant quality of darts and due to accurate repetition
- Constant sewing results in different materials
- Short cycle times
- Precise and quick adjustment for various types of darts
Various types of darts, like curved and straight, can all be sewn on a single machine. There are two different technologies available in the market for this:
1. Using Machine Templates
The machine comes with a set of dart templates. There are different sets for different types of darts. To stitch a particular type of dart, the corresponding dart template has to be fixed onto the machine. The dart length and other specifications are fed into the software program. The needle moves along the template to make the dart. The Durkopp Adler 743-221 works on this principle. The machine comes with a set of patented templates.
1. Dart sewing Template
2. Operator loads fabric on the machine
3. Machine automatically sews the dart along the template
2. Using Computer Programming
The machine comes loaded with programming software. The length, depth, and curve angle of the dart are entered into the software by the operator into the graphics control panel. The required dart is stitched without any need for rail guides. The machine manufacturer usually provides built in programs for basic shapes. Specific requirements can be entered and stored in the program memory. An example of such a machine is the PFAFF 3586 machine. This machine has an integrated disk drive using which program data can be transferred to/from another machine, or saved on a disk. In addition, the machine’s operating software can be up-dated at any time.
The machines in this category are well equipped with features that make the task extremely simple. A single operator can easily perform the operation. The productivity of automatic machines is much higher compared to the lower levels of technology. In some models, productivity is further increased as the operator can load the next work piece on the machine on the platform while one dart is being stitched.
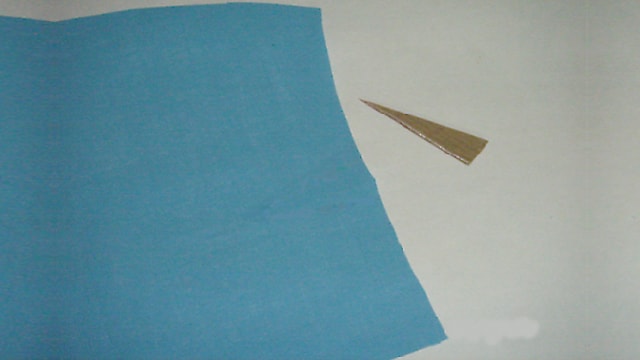
A further enhancement, available in some models, is a reflecting light fabric end detector. This detector senses the edge of the fabric due to change in light reflection and stops the machine at the correct position where the fabric ends.
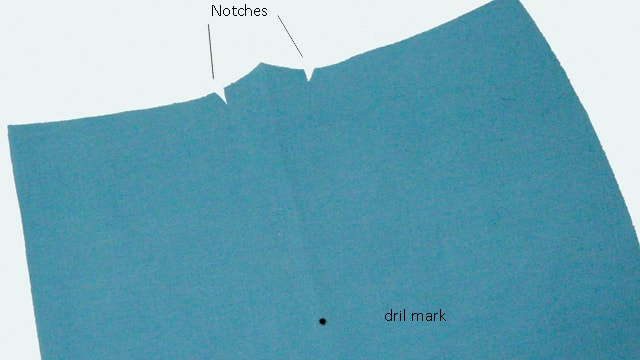
Calculate the ROI for Basic and Highest Level of Technology
The decision of which machine to purchase depends on the size of orders that a manufacturer gets and the kind of labour that is available. The higher we move up in the levels of technology for any operation, greater is the productivity and consistency of quality. Using advanced machinery also results in deskilling of labour; more is the automation, lesser is the skill required by an operator.
Keeping all this in mind, we can calculate the ROI for the highest level of technology and find out how effective it is for an industry.
Basic Level of Technology
Cost of labour = Rs 3000 per month
SAM value for a single dart = 0.36 min
Production = 1333 darts per day (shift of 480 mins.)
Labour cost per day = 3000/ 26 = Rs 115.40 (month of 26 working days)
Labour cost per dart = 115.40/ 1333 = Rs 0.09
Cost of SNLS machine without UBT = $ 635 (list price in US Dollars)
Highest Level of Technology
(for Durkopp Adler 743-121)
Cost of labour = Rs 3500 per month
SAM value for a single dart = 0.074 min
Production = 6500 darts par day (shift of 480 mins.)
Labour cost per day = 3500/ 26 = Rs 134.60 (month of 26 working days)
ROI for Basic and Highest Level of Technology |
||
Depreciated Value (DV) = NBV/{1+DR/100}n, where NBV = Net Book Value; DR = Depreciation rate & n = Number of years |
||
ROI for any year= [CM Price from total machine - total operator salary till that year] ÷ Depreciated value of total machine, expressed as a percentage | ||
The cost of the basic machine is Rs 27,300 whereas it is Rs 9.0 Lakh for the advanced machine. 5 number of basic machine are required to match the output of only one fully automatic dart making machine. | ||
Basic level of Technology | Highest level of Technology | |
SAM value for a single dart | 0.36 min | 0.075 min |
SAM value of per trouser/shirt (assuming 4 darts per garment) | 1.44 min | 0.30 min |
Production per day (shift of 8 hrs.) | 1333/4=333.3 garments | 1600 garments |
Production (No. of darts per annum) | 1333/4 x 26 x 12= 103974 | 1600 x 26 x 12=4,99,200 |
Production Target | 1600 garments/day | 1600 garments/day |
Number of machines required to meet target production of 1600 garments | 4.8 ~ 5 | 1 |
Salary per operator per annum | 36,000 pa | 42,000 pa |
Total salary ( A ) | 36,000 x 5 operators =1,80,000 | 42,000 pa |
Cost of Machine | 27,300 x 5 machine = 1,36,500 | 9,00,000 |
Annual Depreciation | 15% | 15% |
CM Price per dart | Rs 0.36 | Rs 0.36 |
Yearly CM Price per machine | 103974x 0.36= Rs 37,340 | Rs 2,25,000 |
Yearly CM Price ( B ) | 37,340 x 5 machine =1,86,700 | Rs 2,25,000 |
Effective CM Price Constant | [37340]x5-[36,000]x5 =Rs 6,700 | Rs 2,25,000/- 42,000=1,83,000 |
CALCULATION OF ROI | ||
Year 1 Depreciated value ( C ) | 1,18,700 | 7,82,608 |
ROI (B A) /C | 5.60% | 23.40% |
Cumulative ROI for 5 years | 28.20% | 112.30% |
(using above formula) | ||
PAYBACK | FOURTEENTH YEAR | FIFTH YEAR |
It is clear from the above chart that after 4.5 years (approx), the highest level of technology pays back completely. The basic level of technology will pay off completely only in the 14th year! |