Massive changes are taking place in the corporate world, not only for emerging companies but also those with a long tradition. In a very highly competitive world, corporate restructuring is becoming commonplace, resulting in changing roles and responsibilities. In the changing environment, reluctance to change is expected. Change requires energy and fresh ideas. More importantly, when the change is to affect ‘People’, the larger the change, the greater the required energy and conviction to accomplish the change. Despite the increased requirements, Dr Rams explains why they are essential and how they can be fostered by proper initial training.
“If you want to build a ship, don’t gather your people and ask them to provide wood, prepare tools, assign tasks…just call them together and raise in their minds the longing for the endless sea” –Antoine de Saint-Exupery.
In a recent evaluation on the challenges faced by the Manufacturer Exporters, the following were revealed:
- Quality problems (repairs/rectifications/rejections/ delayed shipment, airfreight, etc. are associated with this)
- Low labour productivity
- Lack of trained manpower
- Yawning gap in the supply chain
- Fabric sourcing problems
- Lack of resources to invest in appropriate technology or retraining
- Suppliers’ don’t deliver on time and right quality
- Price competition, etc.
These problems have not appeared suddenly but have been there from time immemorial. The simple reason is that the Industry is not focussed on these issues professionally, due to various other reasons. Similarly, the Industry has not focussed on Human Resources Development and always looks for a short cut method of grabbing manpower from somewhere (wherever) within the Industry. There is no well-established Human Resources Department empowered to get best practices. It is surprising to note that many companies in full fledged operation have not yet established this Department and if at all there, their job is limited to time keeping, payment of wages and submitting reports to the Inspector of Factories. They are not fully empowered and work like puppets.
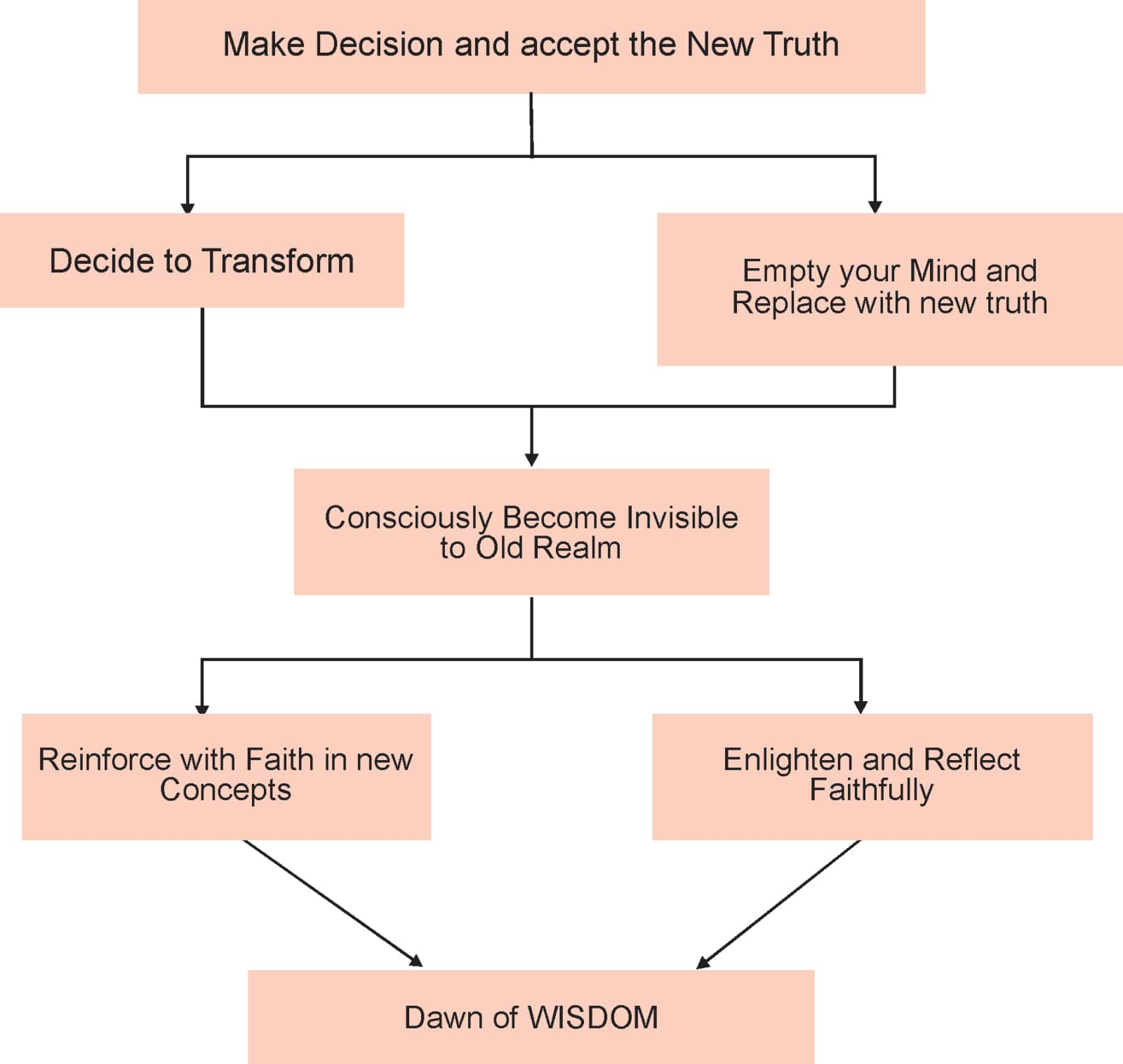
To reach the above level, we must first look into the natural process to wisdom as shown in the chart overleaf.
The configuration of the Industry is around 48% Proprietary, 25% Partnership, 25% Private and 2% Public Limited. Most of the employees are under the lower education level, being a labour intensive industry. These may also be part of the reasons why the industry is at low productivity levels and finds it difficult to evolve to new heights.
Look at the software organisations as to how quickly they evolve through fresh thinking and perspective to tie up with Educational Institutions to meet the future demands of the global customer. They look at the growing opportunities that need to be grabbed through a collaborative effort with the Institutions. They earmark the future employees even when the students are at the third year of graduation and nurture them to be ready on joining the organisation. They don’t dump them straight onto real-time work on finishing their studies but provide a well-structured training program in their own campus before they are enrolled to do the tasks to jell with the Company’s Standing Operating Procedures (SOP). This we call partners in prosperity – the Organisation – the Institution – the Students. Such a vision is needed for this industry if we need to accomplish the US$30 billion mark by 2012.
When fresh thinking is tied up with survival or prosperity, we drive ourselves even more. Is the organisation growing to meet new challenges? Are we equipping ourselves to grab the opportunity if it comes through? Is our vision changing in a positive or negative direction? Are we moving forward to create our own future? How long do we have to live with these problems? When and how can our valuable resources and energy be diverted towards more productive performances? When we will recognise the need of productivity in the cost escalating inflation scenario?
It would be pertinent to mention here the excellent thought process given by Paul Collyer in his article ‘Operator Training – Estimated Costs’ (StitchWorld April 2007), best read with an open mind.
If recruits are to develop skills and speed quickly so as to minimise costs, then a specialist-training programme needs to be available. This programme will need trained instructors operating with designated machines and material. Associated costs will be incurred. Reducing training costs and increasing the effectiveness of operators can be a very effective way of improving profits and productivity. Most importantly, reducing the length of time between a trainee starting and reaching required production targets could minimise cost.
In other words, the industry should not become an out and out training institution but should focus on the highly competitive business opportunities. It should leave the major job of training to the Institutions to develop employees with the required mind and skill set. The Institutions should not churn out run of the mill type of people to the Industry.
If structure is the ‘skeleton’ of the organisation and ‘process’ its infrastructure, then ‘people’ are the blood and guts. The people resource we need to achieve our strategy for change cannot be put in place overnight. It needs required time to build the mind and skill-sets which are critical; therefore, it has to be built through a structured training program before they join the Industry. At the end of the program, we need to develop self-management skills so that it is easier to mesh them into the mainstream with minimal guidelines. We must reinforce in our vision the objective of “Making people Before making Products” (Mp B4 Mp) as a navigator for successful business proposition.
What are the characteristics of self-managed people?
- They will have self-confidence, pride and courage to deal the issues without fear.
- This will give individuals closer control over their destiny; provide major benefits to the organisation and the people around them.
- They will have expertise on the job and address the problems at the source. This will enable them to eliminate colossal waste at the end of the process and will take instant suitable action to rectify flaws to smoothen the flow in the chain of actions.
- As they solve the problem at source, they will have better control on the process and satisfy the next customer in the process and will add value to the process. They become more quality conscious people and nurture the same attitude through out the organisation.
- As self- managed people, they have the responsibility and accountability of their job.
- They will always be in continuous learning mode
- They are self-motivated people organising themselves to always focus on higher performance levels.
When we plan to establish a Manufacturing Facility, it takes a minimum of two to three months as we wait for sanction of financial resources and then indent for machines and organise the infrastructure. All these may take a minimum of 6 months period and in case of owning a building, it will extend another two to three months; this means overall 8 to 9 months duration. It would be ideal that during this time, a tie–up should be made with any institution to start a training program of the employees. We have ATDC, ALT and many private institutions to carry out this job. We may call this an incubation period and need good relations with Institutions to assist and monitor the program periodically. These institutions must have a common curriculum encompassing all required skills and the mind set to develop people fit for the organisation to take up pilot production followed by commercial production.
We will first look into the mind and skill-set required to be developed at the Institution level to make these people fit for the Organisation:
Mind-set:
- There is no end to improvement
- Always think positively
- Always consider the current situation as imperfect
- Do away with a fixed mind-set
- Practice thinking from a broader perspective
- Keep working on improvements so that firefighting will vanish
- Customer satisfaction is the priority
- House keeping and clean environment adds to healthy life
- Empathy is the key to harmonious relationship
Attitudes:
- Find out the root cause and fix it
- Always generate new ideas and innovation
- Respect people for collective wisdom
- Do not waste time in implementing good ideas
- Always work with enthusiasm and do not fear failure
- Always practice discipline with pride
Skill sets:
- Skill related to Job: Exposed to the specific knowledge of the process right from the time the fabric comes in to the execution of finished product. Different fabrics, style-contents, technicalities, accepted quality levels, etc., all need to be integrated here.
- Skill related to Team Performance: Learn effective communication as a team member to contribute new thoughts and ideas; be harmonious with the team for accomplishing the mission. Think about winning teams in sports as an indicator for success.
- Skill related to Individuals: Work for self-improvement even in difficult times, be analytical to improve the skill to match the needs of the organisation, have patience and perseverance. Always believe that you belong to the organisation and not to any individual masters.
- Skill related to maintain Operating Procedures: Skill to maintain standards, follow procedures and operating instructions with discipline, finish the work on time without defects, adhere to safety procedures. Understand problem solving tools.
- Skill related to Collaboration: Coordinate and cooperate with co-workers to get the job done. Do not look at titles but at contributions.
In the institution itself, the people shall get all this training apart from job-oriented training. The industry must, at the end of the program, select the right type of candidates to match their organisation’s requirements and have a short induction program to acquaint the selected people with the new environment where they are going to be positioned. During this induction period, the employee is exposed to the general culture of the organisation and the vision of the company.
If this has to happen then we have to restructure the training program to a broader perspective and for a little more time to cover various important aspects of a growing organisation. If we confine the training only to tailoring with a limited exposure of fabric/style contents/ skill contents, then the organisation has to take a longer time to again train them to fit into their needs. In other words, they come out quickly from the institution with narrow skill sets and without a proper mind-set. In this process, neither the industry nor the new recruits benefit.