Use of an edge guide or compensating presser feet may deskill the operation substantially and a comparatively low skilled operator is able to sew with consistent quality, thus being able to achieve higher production. There are different folders and attachments for single needle lockstitch machine which can simplify the complex operations to achieve higher productivity while reducing operator skills.
Joining two plies of fabric is a simpler operation and commonly known as superimposed seam, but when it comes to managing small margins and with the shapes which have built in contours (concave, convex, straight and their combinations), it is comparatively difficult operation to manoeuvre without any devices, attachment on work aid. Use of deskilling devices or work aids allow quick, accurate place, align and finally sew at higher speeds with less stops and starts. Sewing operations involving flat seams can be categorized into joining two straight plies at edge and joining of curved plies at edge. Joining of curved plies can be further classified into one straight with one curve, two similar curves and two dissimilar curves, i.e. one concave and another convex plies at edge.
Joining Straight Seams
Joining of two straight plies is one of the easiest operations but managing higher speed with consistent margin is always an issue, even if seams are straight. One good example would be side seam on inseam joint of formal trouser. These seams are generally done with the help of an edge guide usually magnet type or cardboard stuck to base plate of the machine near needle plate, if fabric is slippery or grainy (like georgette or chiffon), then managing two plies at even/uneven margins is very cumbersome. The machine is stopped and started at regular intervals to realign, thus needle running time reduces. Many a times, plies have tendency to stick to each other before stitch formation (in front of presser foot).
With plain device such as even and uneven margin sewing guide (Picture 1A) the operator is able to sew with much lesser stops and can feed continuously because two plies are separated by the transparent plate and having a guiding plate which can be adjusted according to thickness of the fabric.

In the attachment shown in Picture 1A, there are two transparent plastic plates and between these two plates, there are two separator plates (Picture 1B, coloured red) for two plies. These separator plates can be adjusted right or left according to the seam allowance for upper and lower plies separately. But the thickness of the separator plates is according to the thickness of the fabric which means that for a thicker fabric a thicker separator plate is used and vice-versa. Moreover lower and upper separator plates can be adjusted independently for uneven seam allowance. This is otherwise much more difficult to achieve in shaped/contoured plies.
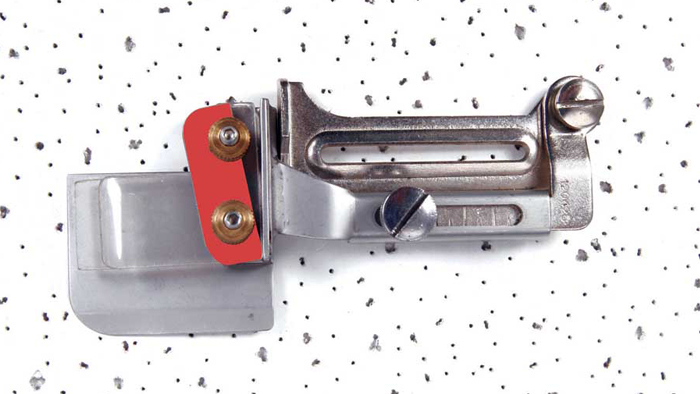
The operator just needs to feed the fabric by making it touch the separator plate at the end near to the operator since the metal plate within the plastic plate is set at an angle, feeding to the needle is not perpendicular but at an angle for manipulating concave and convex curves around the edge of the guide. The thickness of the separator plate has a slight slant from operator side to the needle. This is because at the feeding end (the end towards the operator), there is a chance that fabric may get folded. Even if the ply gets folded at the feeding end, it gets opened due to the reduced gap between two plastic plates. The closer plates do not allow any additional folded thickness to pass through. This raises the degree of confidence and reduces the dependency of the factory on higher skilled operators.
Joining Curved Seams
Joining of two curved plies is done for forming three dimensional effects. Curved shapes can be categorized as either concave or convex. Joining two similar shapes – concave to concave or convex to convex – is easy because the seam allowances also superimpose each other perfectly. But while joining one concave with another convex shape, the circumference of convex and concave at stitch line is required to be equal but the edge circumference (with seam allowance) of the plies are different. The operator has a tendency to visualize the edge, align them and feed the edges of the fabric to be joined which in this case are obviously not equal. In such cases the operator will always encounter problems either with seam allowance or the length of the seam.
Usually in shirt sleeve and princess line dresses such seams are common.
This problem can be easily understood by the following illustration:
In Picture 2, the length of dotted seam line for convex as well as concave is equal AB. However the edge circumference of convex CD is greater than edge circumference of concave EF.
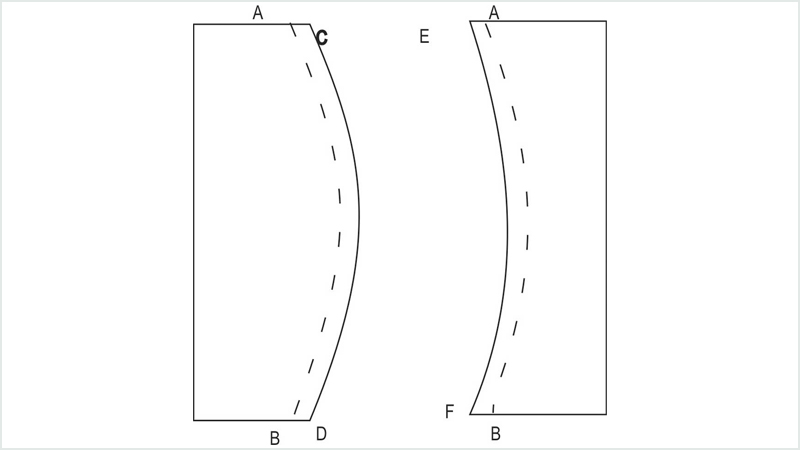
The difference in circumference will vary according to the amount of seam allowance. According to the formulae of circumference for a seam allowance of 1 cm will result difference of total circumference of little over
6 cm. For example, if the length of curvature in one-fourth circumference, then effective difference in edge length during sewing will be 1½ cm.
Since, the operator has the tendency to match the edges and sew, as he can’t align on the dotted lines; the operation becomes complex and he has to stop and start, ease and stretch at regular intervals to align the plies.
To further this, (Picture 3) convex and concave shapes are interchanging at each scallop. In actual working on garments these contours are never going to be semi-circular. They are going to be of different radii at different quadrants.
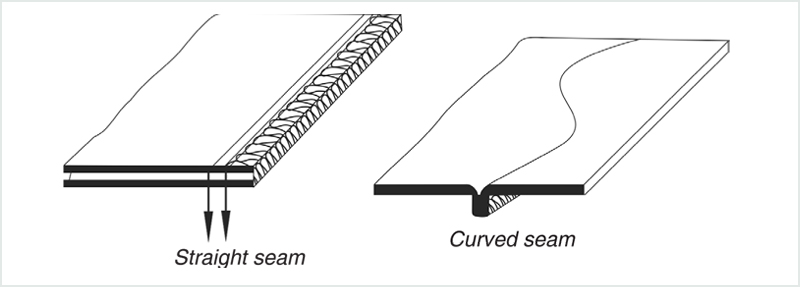
Similarly problems will arise while joining plain and curved plies together. Skill and speed is always a matter of concern for such complex operations but a very simple device almost similar but technically different to the one discussed above helps solve the above problems.
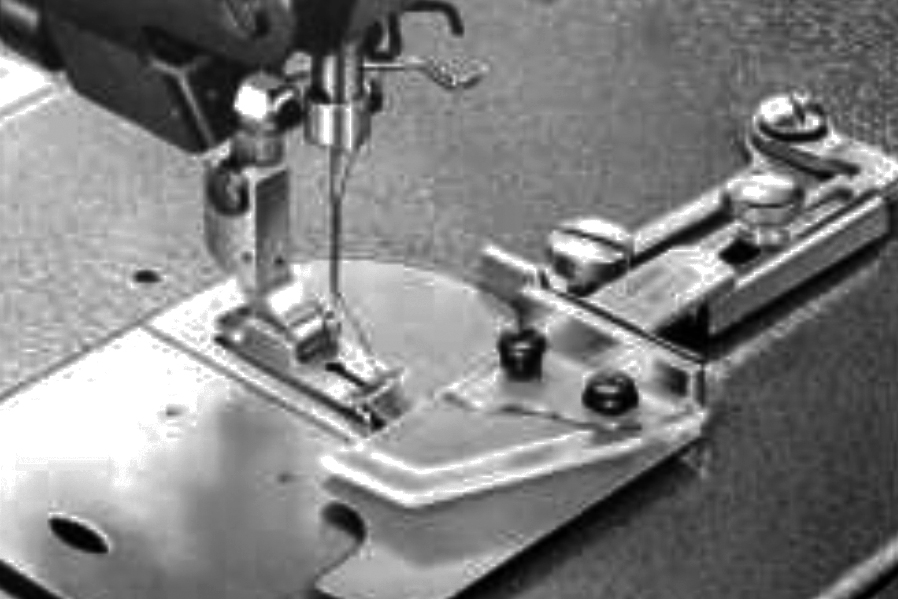
In Picture 4, the separator plate has three curves (or scallops) protruding out towards the presser foot. This is specifically useful for joining curves as discussed above. Here the fabric is in contact with the area near the operator. In case of convex and concave curves, the curves of the separator plate push out the fabric according to the requirement of the seam allowance. The operation becomes much faster than when manually manipulating the seam allowance. Since the two plies to be joined are separated by plastic plates, cohesion or stickiness between the plies is eliminated. Similar devices are available for use with overlock/safety stitch machine; just the holding contraption needs to be changed.
Even this plain device for superimposed seam can enhance productivity with lesser skills and greater accuracy.