Single needle lockstitch machines, which comprise 70-80% of the total number of sewing machines in a factory, have many features and functions which are needed to be understood in detail to witness productivity improvement.
Any sewing operation works in five basic steps: pick, place, align, sew and dispose of. Two or three different plies of same shape or different shapes are picked up one by one by the operator. These plies are then placed on the bed of the machine with end to be sewn near or under the presser foot. Before starting to sew all plies, they are aligned. The sewn plies are then disposed of by the operator for the next operation. To understand the lockstitch sewing process, it is necessary to understand the basics of these five steps, out of which, only ‘sewing’ involves running of sewing machine and consumes a maximum of 20-30% of total operator time; other four movements do not require sewing machine to run.
Sewing Steps
The sewing steps in a lockstitch machine with clutch motor would comprise of – start of seam – pull the thread by bringing presser foot and needle to a position where thread pulling is possible by moving wheel by right hand – pick ply number 1, then ply number 2 or 3 one after the other or simultaneously – start tack by pressing back tack lever – start sewing with start strip – sequence by aligning both plies – stop – control/adjust margins – start sewing – adjust to ease/stretch – end tack – stop – trim thread – dispose of.
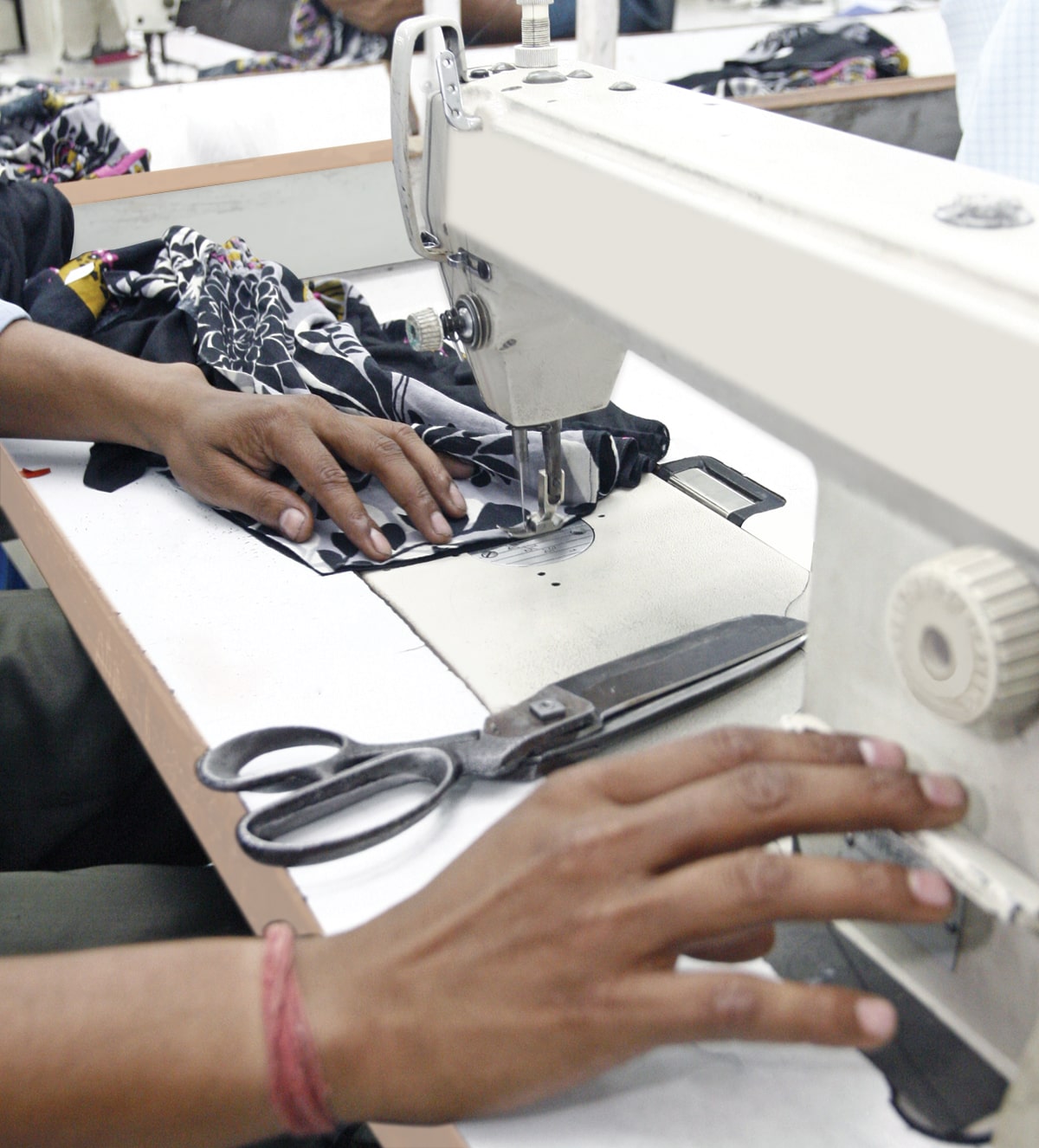
But this is not all, apart from these steps the operator is also required to carry out the following tasks while sewing using lockstitch machine with clutch motor.
• Slow down to approximate stop (example – Attaching sleeve to armhole and stopping to match the notch)
• Slow down to accurate stop (example pocket attaching and stopping at corners to pivot)
• Manually rotate handwheel to bring down the needle (for pivoting)
• Manually rotate handwheel to bring up the needle (at end of stitch)
• Rock the handwheel to release thread
• Pick the scissor/trimmer to cut the thread
Nuances in the ‘Sew’ Step
Workplace Engineering
In cases where factories do not have effectively engineered workplace, operators may have to ‘turn’, ‘rotate’ and ‘twist’ the fabric plies before finally bringing them under presser foot to align. If the piece to be sewn is long, then it will hang out of the table making it difficult to align and sew due to unbalanced weight. In the first half of the seam when the weight of the fabric is towards the operator, the fabric will resist feeding. While in the second half of the seam, when most of the fabric is hanging on the other side of the machine, it will be overfed. In both the cases the operator will have to handle the situation and compensate for this. When the fabric is hanging on the operator’s side, she will have to assist in feeding the fabric, while when the fabric is hanging on the far end from the operator, she will have to prevent overfeeding by controlling the fabric. As the garments become bigger because the number of components increase after every operation, not to mention that the garment is getting more and more three-dimensional after every operation, the stacking of the garment pieces get more complex. Moreover the garments get crushed needing flattening at seam area, either by stretch or better handling at time of joining. This adds to increased handling of the garment by the operator.
As is the practice, small parts/components are sewn in a chain formation. After completing the bundle, each piece in the chain to be worked upon is pulled and then cut. This involves three sets of operations – pulling the chain by one hand; cutting the chain with the other hand by using a scissor or a cutter; and holding the chain otherwise cutpieces will fall. The small components in the chain are free to rotate around the seam and when these parts are cut from the chain and stacked, at times sequence of ply number is lost. If the cut and stacked pieces are jumbled up, the next operator will waste a lot of time in picking, flipping, turning and matching with other ply or piece. If the picked up piece is to be sewn with another ply or part, which is also disposed of in chain, then the entire process adds to many unwanted movements.
Complexity of seam shapes
The plies to be sewn might be in a straight grain/cross grain, plain to bias, and bias to plain (Diagram 1). Not only this, they could be curved but of same shape, contoured of different shapes, like plain to concave, plain to convex, concave to convex and vice versa may be different fabrics are of two different dimensions. The objective of sewing is to convert these geometrical shapes from flat patterns (two dimensions) to three dimensions. In this process pleats, darts, ruffles and cross seams are to be handled which involves lot of pivoting and turning, not to mention keeping in mind even and/or uneven margins. While sewing darts, the seam allowance has to be turned towards a particular direction and if that direction is towards the operator, then sewing of dart is easy, but if the seam allowance of the dart has to be folded away from the operator, then the machine has to be stopped near the dart for the operator to shift the seam allowance and start again (see pictures below).

Another complexity comes while attaching collar to neckhole in a shirt. Usually collar is kept on top of the neckhole (see diagram 2 below). And the precise matching of notches at the centre and edges is required. As the shape of neck is curved, it is highly biased; therefore, chances of it getting stretched while sewing are very high whereas the collar band is straight with least possible stretch potential. The operator has to align the neck step by step to the straight collar in such a way so as not to put pressure while sewing on either ply otherwise the uneven stretch in both the plies will increase the complexity.
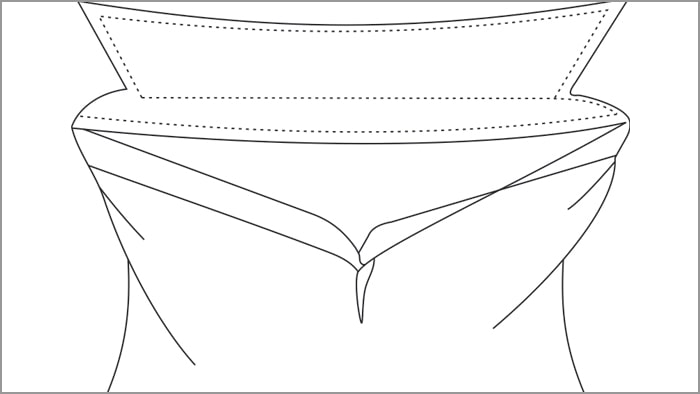
Complexity in the behaviour of fabric
The behaviour of fabric is very complex and many a times unpredictable. Fabrics are finished to have stretch, smoothness (which makes it slippery), they are sometimes chemically coated, have raised piles and ribbed which changes the handling requirements of the finished fabric and that too from grain to grain. Even the warp, weft, bias and curved shapes of the pattern pieces put additional demands on the skill levels of the operator. He is expected to develop extraordinary skills to feed with ease, handle stretch, properly align the notches and precisely follow the seam path, where slight distortion can cause quality problems. This is commonly seen while attaching bias binding on the armhole, the armhole de-shapes at the curves.
Problems due to the clutch motor
As and when the treadle is pressed which is at the start and stop of each and every operation (and even during the operation), the machine gives jerk (sudden start/stop) because operator requires quite high skill to accelerate and decelerate the machine gradually. This results in the operator stopping the machine much earlier to avoid over-sewing without controlling plies. Every time the machine is stopped, the wheel has to be moved by hand for last few stitches. Moreover, the operator also performs other activities during the sewing cycle like thread pulling, back tack lever pressing, adjusting the wheel to pivot the needle. Thus, the operator’s right hand is mostly busy in handling the machine whereas, it should be busy handling the fabric for better quality. In an 8-hour shift, an operator has to lift the presser foot almost 1000 times. How strenuous that can be! Moreover, the operator cannot run the machine at slow sewing speed without experience. Even if he has a high degree of experience, then also running at low speed and simultaneously manipulating fabric is quite a task.
Machine usually has to accelerate/decelerate slowly to avoid unstable stitch*, distortion, ensuring needle to be in fabric (pivot) for every stop to avoid shifting of plies. In all such cases, the operator has to move the machine wheel with his right hand.
Overall, this entire sequence of sewing allows the operator to use right hand to assist fabric feeding and control for only 30-40% of the actual needle time. The rest of the time is either lost in moving hand-wheel, adjusting needle up/down position or back tacking, cutting and pulling of thread.
Technological features that improve quality and productivity
Computerized sewing machine or a machine fitted with a servo motor eliminates the common irritants which makes operator not to think about hand-wheel, pulling thread, reaching out for a scissor, cutter, back tacking and many such unwanted movements, thus freeing the right hand for controlling fabric during the operation. Even though the servo motor consumes 500W of electricity which is double than clutch motor, even then the power saving is more than 60%.
Now that the right hand of the operator is free to handle the fabric, his confidence increases tremendously and he is able to focus on different elements of operation. Moreover, due to auto-trimmer, there is no 6-8” long thread tangled on the piece for next operator.
Accuracy at start and end of the seam is of utmost importance, by automatically setting up back tack of 3-5 stitch at both ends (starting and finishing point of the seam) clean, neat and hassle free back tacking can be achieved.
In any sewing cycle, the operation begins with pressing of treadle. At first, 3 forward and backward stitches (for start tacking) are done, which is followed by 40 forward stitches till the first stoppage point. This entire step takes around 1 second at the machine running speed of 2000-2500 RPM. Moreover, at such a fast movement (forward, backward and seam length) the operator tends to lose control on plies due to the jerk. The advantage of using a computerized servo motor machine is that the control can be set in a way that the speed during the back tack (end tack and start tack) is acceptable/controllable with slow acceleration and deceleration.
Besides this, the very fact that this machine can be made to run at slow speed and can be controlled by a normal operator with ordinary reflexes is reflected in the increased confidence in the operator, delivering higher efficiency at improved quality. Besides offering comfort, far lesser vibrations and sound and other problems like entangling of 4” to 6” of hanging thread, increase productivity also allow easier manoeuvrability for stacking and disposal after completion of operation, thus maintaining sequence which has direct impact on quality.
Additional features
There are many other such features or programmes which do facilitate productivity/quality and lowers the skill requirements. Many features of a machine which were both optional and expensive are now standard and readily available without really spending too much money or influencing in any way the financial projection (investment) of the project.
a) Auto back tack – Start tacking and end tacking number of stitches can be pre-programmed. It can be automatic, can be treadle controlled or can be hand switch controlled.
b) Thread trimmer – It again can be automatic/programmed (after fixed number of stitches) or switch/treadle controlled.
c) Needle positioner – Needle can be programmed to position either inside the fabric or outside the fabric (as required) whenever the machine is stopped right between the operations.
d) Thread wiper – A thread wiper brings the nest of the thread, cut under the bed on to the front side of the top ply so that it is not visible on the lower ply. This is required in certain cases where the stitching is done on the back side of the garment like collar band stitch on the neck.
Initially, the machine used to come with many optional features which are almost standard with most of the machine manufacturers.
a) Auto presser foot lifter – The auto presser foot lifter lifts the needle too on pressing the treadle. It can also be programmed to lift/bring down the presser foot automatically after certain number of stitches at a set speed or after a time delay. This feature is particularly handy while sewing a patch pocket on a shirt (Diagram 3). After a fixed number of stitches, the presser foot lifts up while the needle is pivoted (inside thefabric plies so that the operator can rotate the material around the needle). The operators turn the panel and the presser foot comes down after a set time.
b) Stitch condensation at start/end – Back tack usually gives a feel of bunch formation at under side, giving it a look of cluttered work (which is very prominent at areas which are visible on top of the garments such as finishing stitch on collar and cuff at start and end (on the backside). With stitch condensation feature, the stitch length at start becomes smaller (Approx. one-third of the set stitch length) in areas where clarities of stitch are required to give a tidy look to the seam. It also gives a better resistance against opening of seam. This feature is usually applied while stitching a garment with contrasted colour thread commonly seen in blue denims with white/yellow thread, the back tack in the seam is clearly visible.
c) Microlifter – In case of spongy, elastic or piled fabric like velvet, the microlifter lifts the presser foot by a few microns giving a better flow and floating movement to the upper ply without stretching the fabric or distorting the piles.
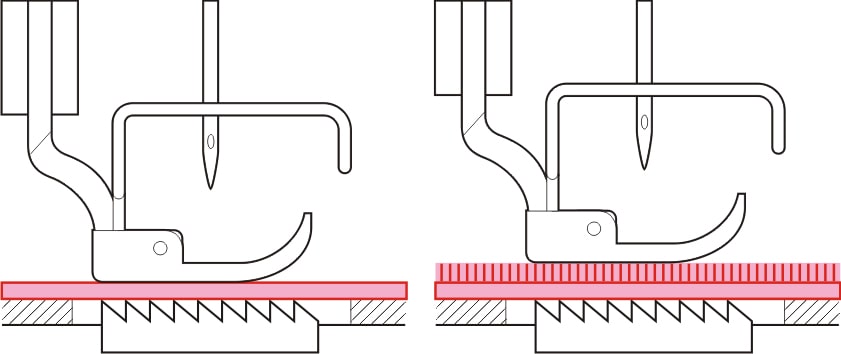
d) Half stitch correction – In case of top stitching where turning is required for example, a patch pocket/collar point/cuff in a shirt, manipulation might be required as the pivot point is half a stitch (less than a stitch) away and adding one more stitch would cause the stitch to run off the fabric edge. In this case one needs to take the needle near to the fabric to manually manipulate the fabric so that the needle falls on the required point. This can be achieved in the computerized machines. The needle can be programmed to nearly touch the fabric to facilitate approximation of the real position of pivoting. Half stitch correction would also mean that the needle moved by a certain distance by pressing a programmed button in the panelwhenever required.
e) Stacker syncronization – Additional devices such as chopper (used to chop rolls of placket or any long continuous taped pattern after they are attached to shirt or any other panel); stacker requires synchronization with needle movement, presser foot lift and thread cutting. With a clutch motor such synchronization is not possible but with a computerized servo motor, timing and delay can be programmed.
f) Treadle presser/degree at heal for actuating pressure for lifts or thread trimmer and even delay time of drop of pressure by operators’ feet after stop and for starts can be programmed.
Besides above features, there are more than 130 to 140 standard functions in almost all good brands of sewing machines. Out of these, 50% are applicable to specific operation requirements which when used increase control and decrease the skill levels of an operator. It is possible because of eliminating certain elements of operator intervention by automating the controls on the machine. Balance 50% of the programmes/features can be implemented to reduce motions in an operation for achieving greater degree of accuracy and reducing damages/bad quality as achieving high degree of skills perhaps is a very difficult task for any factory. What is required is awareness of these features and establishing a relation of these features/programmes with specific operations to achieve the desired result. The need is to understand the possibilities that the machine features can offer.
This is not all. There is much more…
The job of the sewing machine is to feed the fabric and form a neat and stable stitch. While, stitch formation depends on needle, thread take-up lever, bobbin and hook, the right feeding for right stitch formation is done by presser foot, needle plate and feed dog. These parts do vary and are available with different features having specific functions in line with specific requirement of the product. They too are responsible for quality and lowering the operator skills on a specific operation. Besides, folders/attachments, devices and material handling systems also help reduce skills and produce quality with greater efficiency. Not to forget workplace engineering when incorporated for specific operation, enhance productivity with quality.