Eliminating extra work and therefore waste to increase production is not the sole preserve of the large exporter with dedicated Industrial Engineering staff. Neither is it only for those fortunate enough to be able to afford expensive garment transportation systems.
Productivity can be improved by utilising even low-cost changes in work content to make the production process more efficient in ways which can be available to the smaller manufacturers.
Examples of poor methods and layouts are again taken from a Gents suit-manufacturing unit but the principles apply to all manufacturing. If the reader thinks I have heard this before, then no apologies are made. It is crucial that cost reductions are made. Production is lost through:
- Low operator performance
- Low operator utilization
- Poor or ineffective methods
And all three are avoidable. If method improvements are not allied to an overall systematic approach to productivity improvement, then utilization can be adversely affected. To increase the ability of both – the operation and the operator – to produce and not to change workflow, will only move a problem but not improve anything.
A simple rule for method improvement in the garment industry is to consider the operation as being made up of two phases:
- Dispose of work and load the machine. Essentially, this is removing a component away from the needlepoint to storage and bringing the next piece to the needle (iron) ready for work to begin. In this phase the transport of work between operations can also be considered.
- The work/sewing method, i.e. when the garment is under the needlepoint. This phase is dependent upon the handling and sewing skills of the operator. Systematic operator training systems have been discussed in previous issues of StitchWorld.
Let us imagine a menswear factory of 300 operators that have been producing garments for its local market but it now wants to expand into supplying the US and EU customers. It has modern machines with labour-saving devices and all necessary specialist machines and presses. Its mind-set is that of a tailoring unit but now needs to become internationally competitive on price and quality and has to implement the management practices that its new customers will expect to see. Accordingly the management orders a major review of manufacturing procedures.
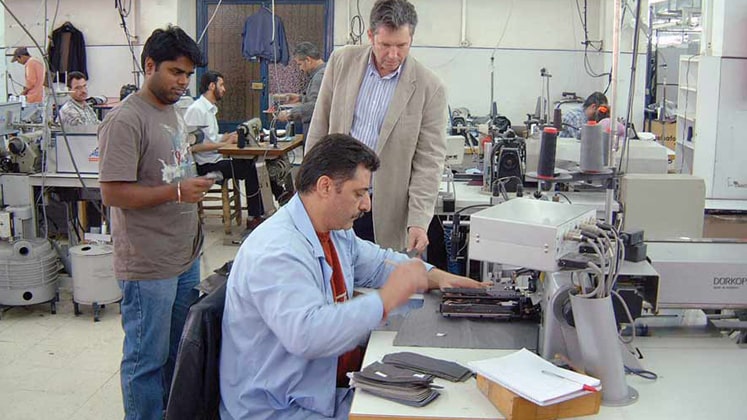
A work-study exercise identifies:
- Poor garment handling. Jackets are initially produced in sections for individual components, i.e. sleeves, fronts, backs, collars, linings, and move from operation to operation in bundles from 2 to 5 pieces at any one time. The pieces are handed from operator to operator without any handling devices. There are no specialist workstations only those devices and worktables that came with machines.
- When jacket fronts, backs, collars and linings have been compiled into single jackets they travel as one item, handed from operator to operator.
- Sleeves are collated to the jackets just prior to insertion.
- Jackets are hung on an overhead transport system when they arrive at the final pressing stage and travel through the department hanging.
- Trousers travel in bundles on specialist trolleys until the fronts and backs are joined at which they are transferred into single garments onto trays, travelling along a central table.
- Trousers are then hung on an overhead transport system as singles through the final pressing areas.
The current transport systems do not allow:
- Operators to work in an uninterrupted rhythm as they are unable to consistently pick up work from the same convenient point but constantly turn and take from the previous operator.
- Effective workstations to be deployed. Again as work travels in singles, preserving pressing quality is impossible and handling contributes to extra pressing being needed to remove unnecessary creasing caused during assembly.
- Producing mens’ jackets is probably the most complex of all garment manufacturings with an average garment taking over 100 standard minutes over numerous operations. Work-study investigation identified that over a period of time extra ironing operations had been included to counteract quality problems, (instead of fixing the problem) and operations had been split for balancing purposes. These changes had then become “custom and practice”. As a result there were extra operations and instances where additional work content had been created by loading and unloading the machine more times than necessary.
Additionally there were no time standards; managers had no means of measuring performance, efficiencies, lost time, or generating meaningful production reports. Without measures operator reward was not based on output except on a few vital operations when salary was a matter of personal negotiation.
Going through the above manufacturing processes, it could be summarily concluded that there is –
- Ineffective work transporting systems
- No bundling systems
- Ineffective work stations
- Extra operations causing additional work
- No measures
- No effective management systems or reporting procedures
- No means of linking output to reward
Does this sound like your factory!
Actions
Any Industrial Engineer will tell you that standard times should be based upon correct methods. However as it was necessary to quantify any reduction in labour content, time standards were initially set, (but not issued to operators), on the existing methods and operations re-measured after improvement. Operations were timed then checked and reviewed by considering:
- Was the operation necessary (primarily ironing)
- Can the workstation or ancillary equipment be improved? (These points have been described in previous editions of StitchWorld)
- If necessary, can operations be combined to reduce handling? Check operations to discover if they are performed on the same machine type, use the same thread, utilize the same skills. If so, then they can be combined?
Example 1:
An example is the completion of pockets on a jacket front after a Duerkopp Welt machine has formed the pocket. The first operation is the attaching of the pocket bag in the same line of sewing as the pocket form. This was found to need a standard time of 36 seconds per pocket or 72 seconds per jacket. By the addition of an extra clamp to the Duerkopp (manufactured by the maintenance department at minimal cost) this operation was eliminated; adding an extra 5 seconds to the Welt sew operation due to extra loading of the pocket bag. The extra work for the Durkopp reduced capacity by 14% but freed an operator to work elsewhere full-time.
Tacking of the pocket ends with a single needle machine for both fronts was 46 seconds and for the chest front pocket 31 seconds. As the chest and side pockets needed the same skills, they were combined; a total time of 68 seconds was established, a reduction of 12.7%.
In total, the pocket operations described had been reduced by 40 seconds, a saving of 35% for minimal cost.
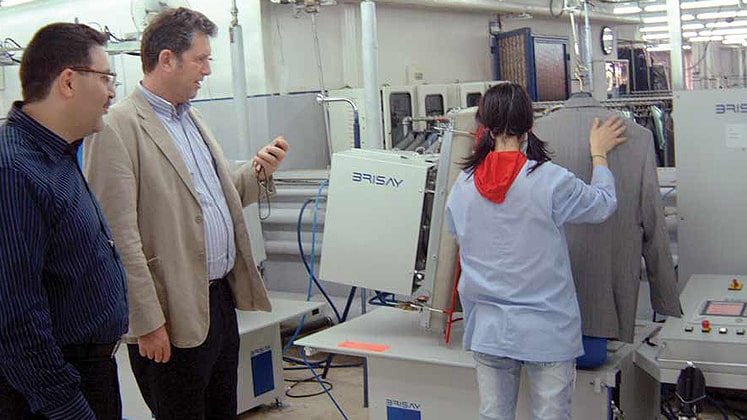
Example 2:
Savings can also be achieved from improving fusible attach on an iron by altering the workstation. Two consecutive ironing operations were combined, removing a load and dispose, and replacing with a reposition on the ironing board. For no outlay, a reduction of 7 seconds was achieved, a modest 3.5% of the total of the two operations.
The ironing operations were at the front of the jacket front’s line. The new work sequence was:
1. Join front seam
2. Iron front seam, attach fusibles (the previously combined operations)
3. Join jacket front side seam (attach side panel)
4. Iron side panel seam. Attach fusible to pocket slit.
This sequence was further modified to:
1. Join front and side panel seams.
2. Iron front and side panel seams. Attach all fusibles.
The combined effects of improving work station layouts and implementing necessary handling by combining operations reduced the ironing times from 200 seconds to 168 and machining from 113 to 102 seconds. Some engineers may comment that the standard times are longer than optimum but it must be remembered that SMVs reflect a single jacket, i.e. 2 fronts and therefore actual cycle times are half the shown times.
Example 3:
By increasing both the length of operations and bundle sizes to 20-25, it is possible to keep the operator working on a single bundle for much longer, thereby allowing more effective balancing and utilization.
For example at a daily targeted throughput of 600 jackets the machine operation of front seam (SM of 50 seconds) needed 500 standard minutes to be produced. At 80% efficiency, this represents 625 minutes of attended time or 1.30 operators. With the previous low W.I.P. and “hand to mouth” working, it was not possible to balance one of the operators onto a second job without running the next operation out of work. Accordingly operator utilization was, at best 65%! The side panels needed 12.35 hours or 1.54 operators. Again two operators were needed with utilization of 77%.
Under the new arrangements, it is possible to deploy three operators (21.25 attended hours needed) with one of these moved to another operation for 3 hours per day. The workflow and balancing now allows the operator to be sensibly moved without running the ironing operation out of work.
Improve productivity without major capital investment – Involve “real experts” the operators
During the review and implementation of new ideas there is no opposition from operators who can see the benefits and adopt new methods as and when they are told to. Their only major concern is “will we be able to earn more money”? Delays are caused by supervisors and managers not wanting to change. They are the people who have introduced or worked with the old methods and see modifications, despite reassurance and training, as direct criticism of them and a threat to their positions.
Method changes have so far been limited to those needing effort and time but little capital expenditure. The management system and payment alterations require specialist knowledge but form part of an overall productivity improvement exercise and should not be beyond the capabilities of a trained production manager or industrial engineer.
The previously described examples are part of the factory wide improvement process. It is a mixture of method study, good production balancing and most importantly a willingness to effect change!
The changes do not involve capital expenditure but making better use of the assets currently available. There is no doubt that wise acquisition of handling systems and equipment such as overhead chain systems will significantly contribute to business improvement. But companies considering such investment should first ask themselves “Are we making optimum use of what we already have?”