A good technician is never satisfied with the present achievements and is always striving for the best. One must also keep in mind that the best machines are no guarantee of the best productivity. It’s not what you do, but how you do it and achieve result! These are but some of the basic principles which if followed to the line, can help in running any factory more efficiently. This article is by Peter Pinder-Browne, a sewing and pattern making consultant with more than 12 years of experience in the apparel industry.
The Background Scene
A fairly modern factory with 110 direct employees and 11 indirect employees had a standard minute value 35.6 minutes for the basic classic pants. They produced pants for a large organization, and had a limited number of styles. (A representative style with one back pocket, knee-lining, top-stitched side seams, waistband extension and taped bottom hems was selected with a work content of 35.6 standard minutes for cutting to final inspection and packing).
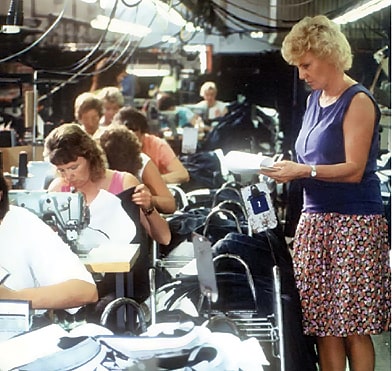
The machines were set up in two groups and all parts were hanging in small clamps on a straight single rail system, about 1.5 metres above the floor.
- Cutting done face up, open spreads and each part numbered size and running number.
- All parts for one pair of pants were clamped and put into production on the hanging rail system.
Improvements Suggested
The senior consultants made a survey of the facilities and suggested that with number of new machines, the standard time for the representative sample pants could be reduced to under 30 standard minutes without affecting the wages earned by the direct employees.
To achieve the results, automated workstation for over-locking back panels, long seamer to close side and in-seams with stackers, top-stitching side seams and stacking, attach endless zipper to left fly, cut and stack, pocket welting with corner notching and stacker, and double leg presses were recommended.
Could the Results be achieved?
Production manager of the company who was also the minority share holder, after a profound discussion with the other owners, committed to achieve 30 minute mark if provided with the requested machines.
The company proceeded to buy the machines and after their integration into the production, the time was reduced to approximately 32 standard minutes, a reduction of 2.5 minutes, two more than calculated for.
Since the exact time of 30 minute was not achieved the consultants were sternly told to “put money where the mouth is!”
The Implementation
Introduction of Trolley
At the first glance it became quite apparent to the consultant that the new machines were all in operation but in the old system. The first thing needed was to change the transport system and the layout. The problem with a bundle of 15 clamped pants was that after unclamping, it was very difficult to put them back into the clamp. Moreover the space was also limited; hence a trolley was designed with a top area of 40 cm X 50 cm which could be stacked for convenient storing and moving back to the beginning of the bundle trolley cycle. The solution was to change the transport system from closing side seams to a simple bundle trolley on 4 wheels. This was then used from close side seams through to pressing.
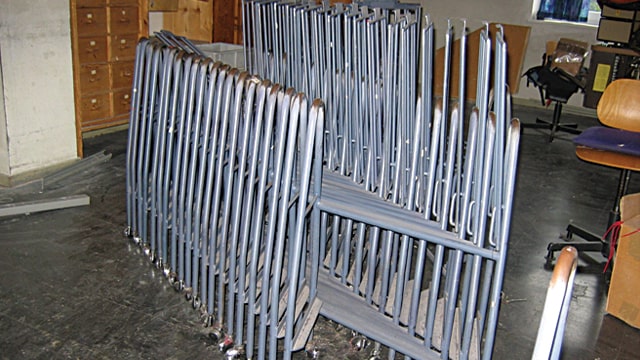
Modified Welders Clamp
Another obstacle was to identify how to clamp 15 pieces in the hanging system; the existing clamps were too weak. Some exploration within the factory threw at us ‘welders clamp’ which were later modified to avoid damaging the material.
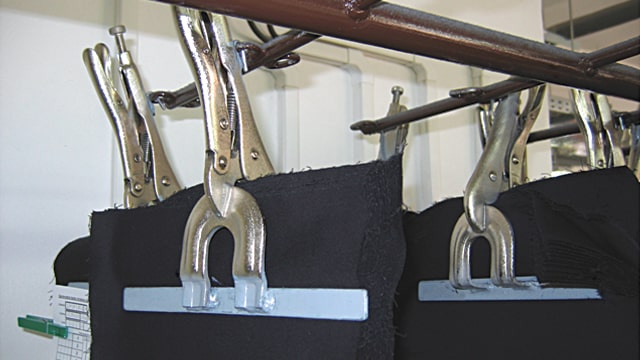
Raising the Podium
The workstations were on the floor, making it difficult to handle the hanging parts, realising that, a 30 cm raised podium was built on which sat the machine and operators. The operators could now be seen above the transport rail, making all very happy.
Redesigned Workplaces
The workplaces in the hanging section were all modified, mostly being cut off on the left side and extended to the front to give a better area for positioning the materials to be sewn. Shelves were made for holding pocket linings etc.
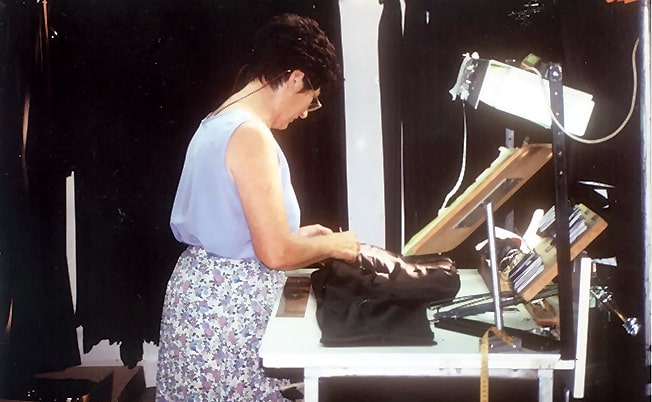
Method Change
At this point a change in the method was initiated. The first task taken up was to train the operators on the revised workstations and make time studies. The use of the stackers was very clearly seen as advantageous with the bundles of 15 pants and the trolley system.
When all systems had been introduced, including quality controls, daily data collection and incentive calculations, the time came under 29 minutes.
Conclusion
The company went on to produce the pants for a long time and further improved the time to achieve 21 minute from cutting to package, unfortunately these styles are no longer in production due to the change in fashion.