One of the key factors affecting the sewing line balance is material movement with proper choice of material flow system, not only does efficiency improve and handling time gets reduced, the productivity, and hence, the hourly production also gets better. In this article Peter Pinder discusses the pros and cons of various material movement systems. Peter Pinder Browne worked as a consultant for KSA for 12 years before offering his own consulting services to the apparel industry.
While walking through factories in India, I was surprised to see that almost all factories still use the Central Table System. Some factories have their layouts arranged as in a school classroom, i.e. all operators were faced in the same direction.
When asked why, I received answers like: “The operators don’t talk to each other as much when they have no eye-contact” or “It is important that we can observe the operators from behind.” There were no answers that I could agree with. Operators, who are treated like children, will act like children and will chat when they think that they are not being observed, creating more of a school-type atmosphere.
The major drawback of this positioning is that the operators do not have the same working advantages when the Transport Table is to their right hand side.
The sewing machines are built for right-handed people. Originally, the machine was hand driven with the right hand and the left hand was used to guide the cloth.
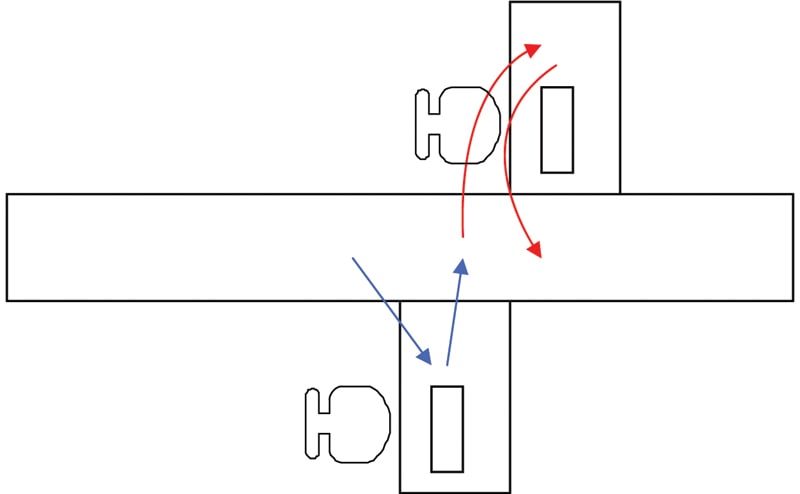
When working on an industrial machine, it is always quicker to pick-up the goods on the left and dispose again on the left. Operators sitting on the left of the transport “Table” have a much longer pick-up and dispose distance and therefore must work harder to achieve the same results.
In most cases, the lighting is positioned above the Transport Table. The light coming from the left of the machine falls on the area around the needle and thus causes no shadow. The light coming directly from the above throws a shadow on the area around the needle, thus making the working conditions worse.
The lighting should not be higher than 7 feet above the ground, or 4 feet above the working surface. This way it gives a more intense light and avoids the shadow of the machine head around the throat-plate of the sewing machine.
Centre Table and its Disadvantages
The Central Transport Table is a relict of the past. This production system was phased out of the production in Germany in the 60’s and 70’s and replaced by a Bundle Trolley.
- The disadvantages of the Transport Table are:
- The table limits the extent of any workplace engineering.
- The workplace table must be adjusted to the standard height of the transport table.
- The space in which the operator can keep the work in process is limited.
- The operators must be positioned in sewing sequence.
A much more flexible solution is to use a bundle trolley on wheels as transport.
Table hinders an effective engineering of workplaces. It further limits the size of a group and the use of sophisticated machines such as pocket welting machines. I experienced a factory where the welting machine was only used to about 20% because only 250 pants were required from the line. The result was that the operation was made complicated to avoid the operator sitting doing nothing till the next single piece arrived. If they had rationalized one pocket away, they would not have saved anything at this operation as the waiting time would have only increased.
As we started to engineer the workplaces and rationalize by working in bundles, we discovered that the table between the sewing machines was more of a hindrance than a help. The table must go! But what do we do about transporting the goods from one workplace to the other?
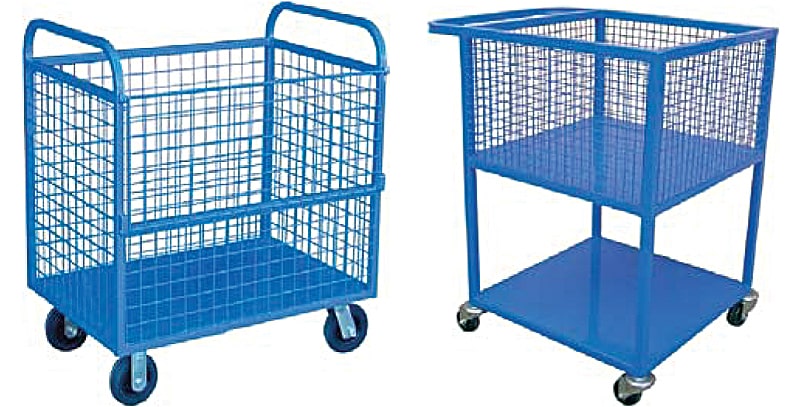
One idea is to put all the pieces into a box and have someone transport them from one operator to the next. The problem is to have the transport worker at the right place at the right time.
The trolley can be used as a pick-up shelf if it is flat or when a clamp is fitted, it can be used as a hanging unit. In this case, the idea is to have an overhead railway system with the pieces clamped into it, either singly or in small bundles. The problem in this system is to have the machines strictly in the right sequence, just as on the Table. The restrictions to workplace engineering are also the same.
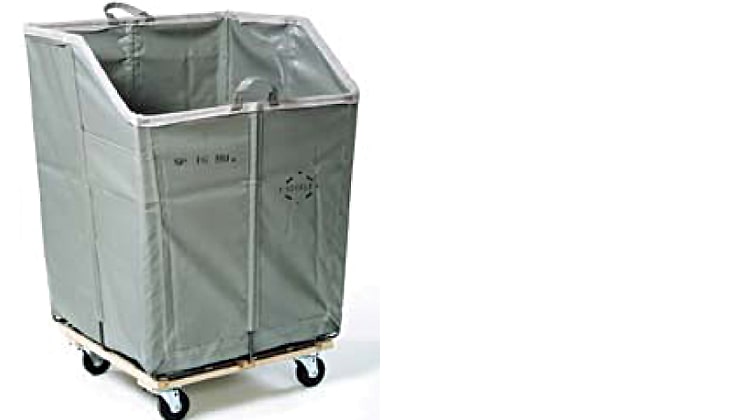
The use of the trolley in this case can be compared to the use of a taxi as opposed to a tram which goes on a rail system. The taxi is much more flexible.
After much thought and many trials, the efficient European factories came out with a bundle trolley on 4 wheels, about 2’ X 1.33’ in size and 3’ in height. This universal trolley can be moved from one workplace to the next without having to visit every station on the way. The trolley replaces the Centre Table and makes the production much more flexible.
The biggest advantage is that one can introduce modern specialized workplaces without having to have one for every line.
Bundle Trolleys and its Usage
Bundle trolleys are of different shapes, sizes and purposes. Common shapes are bin trolleys, bakers’ trolleys, and horse back trolleys. Bin trolleys are either wire frame PVC coated, metal frame cloth bag type, or solid plastic bin type. Wire frame makes the trolley lighter. Bin trolleys can also have provisions for parts segregation or for small parts and/or light fabrics. Sometimes trolleys can be attached and detached to the sewing machine for better working efficiency. Generally, depending on the size of the bin trolleys, they can accommodate 5 bundles of work in progress.
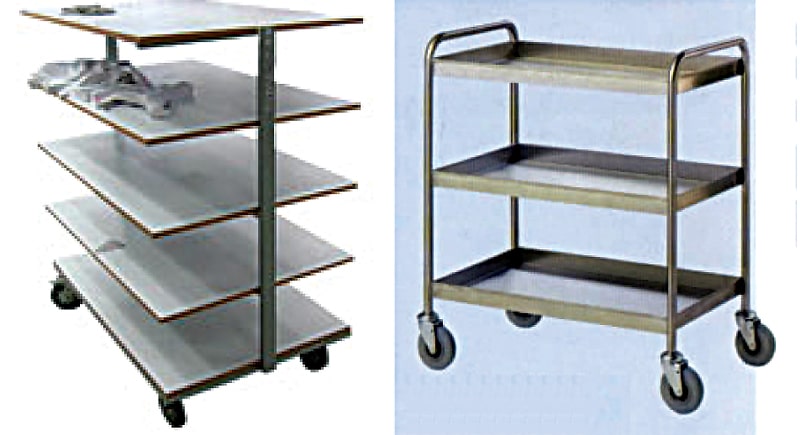
The disadvantages of bin trolleys are distortion of dimensionally unstable fabric components, problems of retrieving parts using first in first out (FIFO) principle. Generally two trolleys are required per sewing workstation – one trolley for pickup and another for disposing of. The trolley can be fitted with a visible card holder in which the bundle number, order number and style can be displayed. The use of a running bundle number in the production helps to ensure that the first trolleys are processed first. The use of the trolley requires a little more space per workplace, approx. 60 sq.ft. but this can be more than compensated by the higher utilisation of new special machines.
The bakers’ trolleys have multiple racks at different heights which are often adjustable. Using this trolley multiple component assembling is easier. Here cut components are transported in nicely stacked manner. A single trolley can be used for both pick up and dispose of.
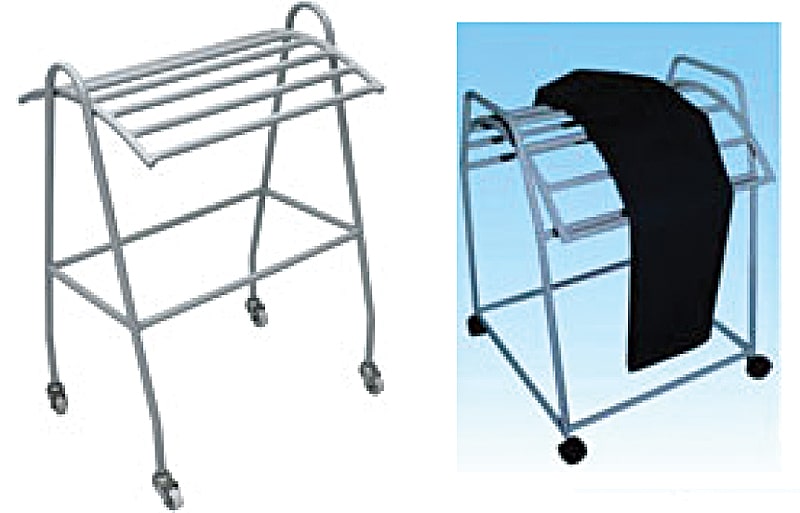
For sewing of long and/or slippery components horse back trolleys are used. Long components can be conveniently stacked on a horse back trolley and can be used for both pick up and disposal. Sometimes these horse back trolleys are improvised to waterfall stacker where components are not picked up, rather sewn while being clamped on to the trolley.
Conclusion
Intelligent use of trolleys can save precious material handling time as well as readily stacked, organized, cut components or half sewn garments. In some operation mix use of trolleys can give better results; for e.g. input trolley may be baker’s trolley but dispose of to a horse back trolley. The changes to the bundle trolley system helps to improve the productivity by up to 30%, when we take into account that the operators were put onto an incentive system and an efficient quality control system, with random checking was also installed.