Time and Action Calendar or TNA, is a technique for tracking and following up on important milestones in pre-production processes to ensure timely delivery within stipulated delivery date. Despite claims of being practically in use by most buying and manufacturing organizations, the follow-up of orders/styles during the pre-production processes are not foolproof and there are several myths which need to be redressed.
In contract apparel manufacturing scenario work is tracked through the order fulfilment process (OFP) by monitoring at specific order points decided by critical path reporting agreement by buyers on manufacturers in developing countries. However, different terminologies were used by different users like ‘time-and-action’, ‘critical path’, ‘work flow’, merchandising ‘calendar time scale’. Many apparel managers also use project management concept such as Gantt chart, to monitor time and manage employees who work on product development and production.
TNA should be same as critical path
Right
Garment pre-production (also known as merchandising) activities are characterized by people-oriented functions. Interdependent activities are synchronized between succeeding and preceding activities to make a non-linear process network. The longest chain of activities considering task dependencies is called critical path. TNA should have the same activities as critical path derived from PERT (Program Evaluation and Review Technique) network or Gantt chart.

Time is the most critical factor in TNA or critical path
Right
Even though most of the users are aware of the term ‘critical path method’ (or the CPM), surprisingly few know the correct meaning (definition as per operation research) of ‘critical path’. The interpretation of term ‘critical’ by industry executives are varying. While some feel ‘critical’ means ‘possibility of non-conformance is higher’ as per previous experience, others feel ‘critical’ means ‘most time taking’; some even link ‘critical’ with ‘cost involving that activity’. Everybody selects ‘critical’ activities hypothetically based on intuition or previous experience or buyer’s milestones and no one actually makes PERT network of activities and then arrive at CPM.
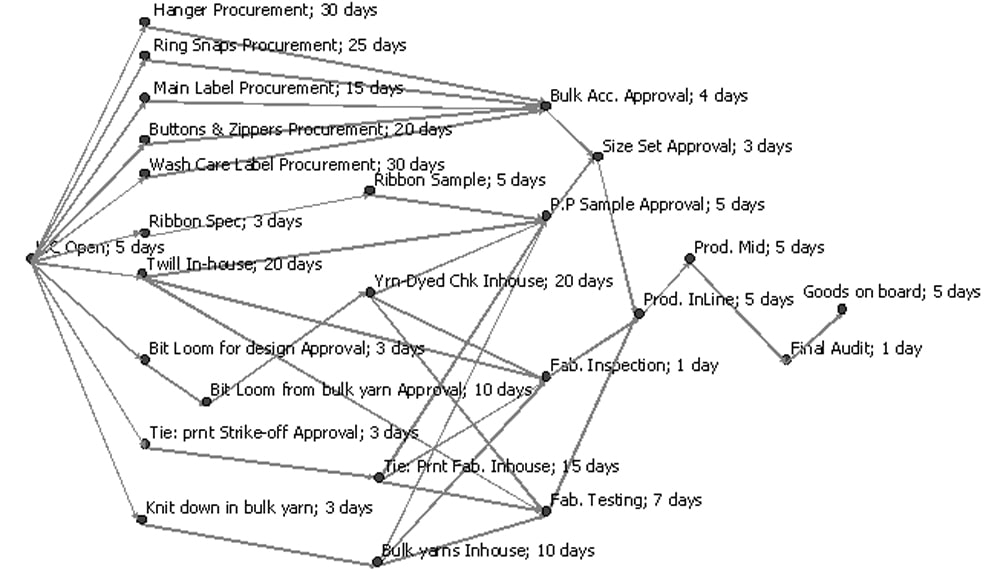
Sequence of activities in garment pre-production are linear
Wrong
It is a common practice to list activities from order receipt to delivery in linear sequence and assigning time duration to each activities by backward planning, which is wrong as the activities are never linear since there are lot of parallel activities. Therefore, the sequence of activities should be drawn either as PERT network or Gantt chart format.
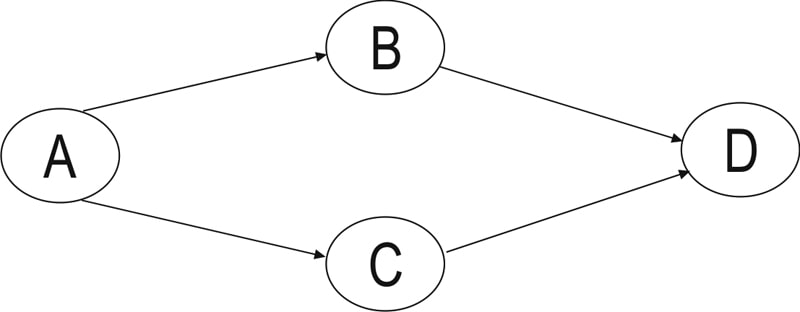
How many and which all activities should be there in TNA depends on the buyer
Wrong
It was found that in majority of the cases the buyer specifies target dates of key activities and based on those target dates the manufacturing organization creates their own TNA adding buffer days (to ensure that buyer target dates are not missed). It was also a common practice to have two TNA: one with few main important activities (also called milestone activities) that are suggested by the buyer, and another one with more number of in-between micro activities (in-house activities) to exercise control over macro activities. To decide upon which all activities should be there in TNA calendar, one must prepare either PERT network or Gantt chart mandatorily and the resultant critical path should be the activity chain for TNA calendar, all activities falling in critical path are critical activities. Critical activities should always be on focus, a single minute delay in any of the critical activities may lead to final shipment delay. In case some of the buyer-suggested milestone activities are part of the critical activities, then well and good; other non-critical activities will have slag time anyway.
Critical activities in any TNA remain unchanged throughout order execution process
Wrong
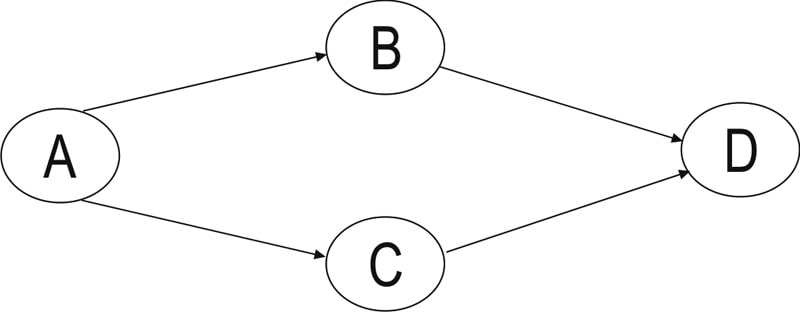
Generally TNA is prepared as proposed plan of execution. The planned duration and sequence of activities decide the critical path. However, during actual execution of order, duration of any activity may stretch beyond planned duration, which may change the critical path. If duration of any non-critical activity extends beyond the slag time then that particular activity may become critical and critical path will change accordingly. This phenomena happens frequently during order execution and therefore specialised software is necessary for tracking TNA which automatically and dynamically changes the critical path during order execution process.
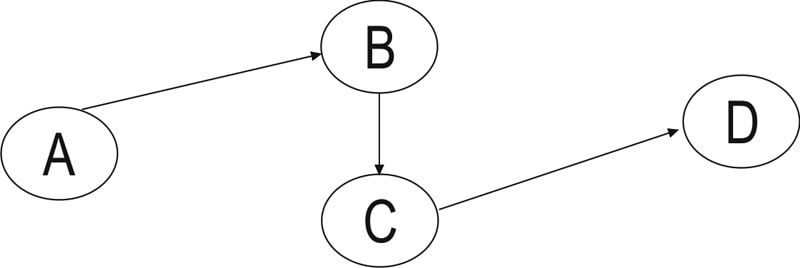
Manpower resource dependency is not so important in preparing critical path or TNA
Wrong
It is a common practice to estimate the duration of activities in days or hours rather than in ‘man-days’ or ‘man-hours’. In the given four task example assignments, both B and C can work concurrently as per dependencies concerned. However, if same manpower are to be used for both B and C, the dependency relation will change accordingly and B and C will become sequential processes.
In a typical scenario, one order may have 40-50 activities to be tracked/followed up/managed (from order receipt to delivery) by 5/6 people, which obviously means one resource person is responsible for more than one activity. Therefore, resource dependency is very important in TNA.
Different orders should be followed up using separate TNA
Wrong
It is common practice to have one merchandiser responsible for multiple orders. Prevalent practice is to prepare separate TNA for different orders and track in isolation. Since resource utilization for more than one order is not synchronized, and since it is calculated separately, situations will arise when same resource is expected to work on more than one place, which is impossible. Therefore, when common resource is to be used for multiple tasks, it is logical to combine all TNA’s into one integrated to avoid confusion of priorities.
Spreadsheet software is enough to manage TNA
Wrong
It was found that majority of the organizations use spreadsheet (e.g. MS Excel) to schedule activities against target date, which they call TNA or critical path. With full potential of spreadsheet being used, all requirements of TNA still cannot be managed. Firstly existing use of spreadsheet is merely typing activities and dates in tabular form. Hardly anyone uses formula, macros or conditional formatting of spreadsheet to calculate variations and get alarms. Therefore, the purpose of using spreadsheet is virtually defeated. Secondly, spreadsheet cannot generate automatic Gantt chart or calculate critical path and many other requirements that are necessary for managing TNA. Spreadsheet when used cleverly can generate linear calendar dates, calculate variance between planned and actual completion date and raise visual alarms.
Specialized softwares are required to manage TNA
Right
Managing TNA requires automatic Gantt chart preparation, automatic critical path preparation, automatic resource utilization calculation, automatic integration of more than two Gantt charts with resource constraints automatically reflected, different options of task relationships like start-start, finish-finish, as well should be able to change all synchronized activities during any change of plan during progress of the order. Further, the software should help or guide the user with several visual/colourful benchmarks and alarm systems. Generally specialized project management software is capable of providing maximum of these features, thus ideal for managing TNA.