Single needle lockstitch machines with needle positioner and under bed trimmer are commonly known as computerised sewing machines in the industry. Generally around 15-25% of the sewing machines on the sewing floor are computerised. These machines surely possess additional features, thus offering additional benefits over ordinary single needle lockstitch machines. However, there are some common fallacies which need to be demystified.
All sewing machines on my shopfloor should be computerised
Wrong
The computerised sewing machine often represents the so-called ‘state-of-the-art’ sewing machine. During upgradation of facility or in a race to put up ‘state-of-the-art’ sewing floor to impress upon fellow manufacturers or buyers, manufacturers often buy all computerised machines in their shopfloor. A typical computerised single needle lockstitch machine can perform needle positioning, under bed thread trimming, back tack and step programming. We need to analyse all the operations where we require these features. For example where we stitch small parts in chain to maintain the sequence of ticket numbers, we may not require thread trimming facility. Similarly for all those operations where seam end goes inside subsequent seams, may not even require back tack and so on. It is observed that needle positioning is the most wanted feature and step programming is least used feature. A study by a leading sewing machine brand reveals that appropriate selection of computerised sewing machine on the shopfloor can lead to approximately 13% improvement in productivity.
Programming of features in computerised machine is very complex, operators can’t do it
Wrong
The icon based programming is very easy and even operators can do it. Nowadays different settings can be saved and simply called in during change of style.
Computerised lockstitch machines can raise alarm before bobbin thread exhausts
Right
Against common belief that sensor raise alarm when bobbin thread exhausts, these sensors actually raise alarm when a pre-determined amount of thread is left in the bobbin. This is to ensure that existing cycle of sewing is complete and bobbin is replaced before the next cycle starts. Some of the computerised lockstitch machines are equipped with proximity sensors, which can be programmed to sense and raise alarm based on remaining thread in bobbin. The amount of remaining thread can be programmed based on requirement. An operation like shirt front placket stitching requires to be programmed with more amount of remaining thread then an
operation like pocket attaches.
All computerised sewing machines can programme number of stitches
Wrong
Computerised machines may come with only needle positioner and under bed trimmer and may not have step programming facility. It is the step programming facility which can count the number of stitches and which could be pre-programmed based on total length of stitch and SPI (Stitches Per Inch) being set. For example a length of 5 inches seam at 12 SPI theoretically will have 60 stitches. However, as fabric is dimensionally unstable material, operator has to actually stitch, count and programme actual number of stitches. Earlier different models were available with or without step programming facility, however nowadays generally all brands offer computerised sewing machines with all features namely: needle positioned, under bed trimmer, back tack and step programming.
I can easily attach patch pocket using programmable computerised sewing machine
Wrong
This is probably the most difficult and controversial myth in the sewing floor. And unfortunately the machine manufacturers keep fooling around these features. A typical patch pocket (as shown in the figure) will have 4 sides of measurement. The programmable lockstitch machine can easily programme these four steps with given SPI. For example suppose the pocket side A-B is 5 inches, B-C is 3 inches, C-D is 3 inches, and D-E is 5 inches, at 12 SPI, A-B length should contain 60 stitches and similarly 36 stitches in next step and so on. But in reality while creasing the pocket, there may be minor variations of length A-B between pieces to pieces or between A-B and D-E. Suppose the tolerance is 1/8th inches (as such small variation in length will not make the pocket commercially/visually unacceptable). If in A-B length of one pocket is 1/8th inch smaller, then 60 stitches will shoot off the corner and pivot point will be outside the pocket. If the pocket A-B measurement is 1/8th inch longer, then pivot point will not be exactly at the corner and the look will be unacceptable. These problems arise because stitch programming go by exact number of stitches and cannot adjust one or two stitches more or less due to slight variation in measurement which is commercially acceptable.
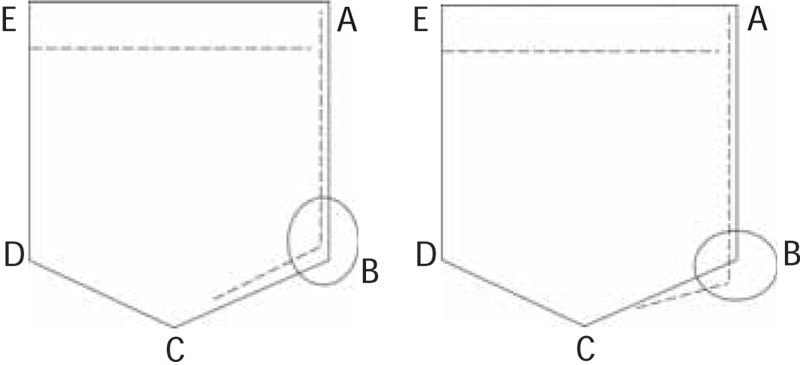
Step programming machine will only work successfully where pocket creasing is consistently accurate to fraction of a millimetre which is generally not possible even using pocket creasing machine. Although all the computerised machines with step programming facilities have an additional stitch button, it is still inconvenient for the operator and may ultimately take longer time than using an ordinary machine.
I can NEVER attach patch pocket using computerised sewing machine
Wrong
Some of the computerised sewing machines come with a feature called ‘ply sensor’. This feature can sense the difference between number of plies through a sensor and stop the machine accurately. While attaching patch pocket, the stitch is given on the edge of pocket fold (three plies), while the body of the fabric is only single ply. The ply sensor can sense the difference between single and three plies and accurately stop at all corners, operator only has to pivot and press the pedal to start sewing. Although ply sensor technology is very useful and practical solution for deskilling the patch pocket attaching operation, the awareness and popularity of these machines are very less. Unfortunately the machine manufacturers do not promote these machines to manufacturers correctly.
Another reason behind non-popularity of ply-sensor technology was frequent malfunction of sensors in dusty and lint-scattered surfaces. But with more and more cleaner factories coming up, the technology is worth considering