Getting higher productivity doesn’t mean working hard, i.e. working for more time with the available resources. It is all about how smart we work. On sewing floor it refers to how efficient we are at doing a piece of work, i.e. opting the best method with the combination of most recent technology available. This not only increases the productivity but also saves money, improves quality by reducing defects.
In this article Kunal Saurabh and Tameem Hussain, students of M.F.Tech, NIFT, Bangalore along with Vasant Kothari, Assistant Professor, Department of Fashion Technology discuss how to de-skill the operation of stitching a Reinforcement Fabric in a Cargo Pocket using better technology.
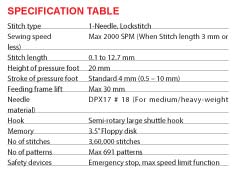
A reinforcement fabric either of the same material or a sheeting material is required while working with delicate fabrics or heavy stitching (more stitches in a small area), i.e. embroidery, bar tacks, snap buttons, etc. to give strength to the fabric.
For stitching a reinforcement fabric in the cargo pant or cargo shorts at the mouth of the cargo pocket, usually 4-6 bar tacks are required. This provides strength to the part of the base fabric. For this operation different levels of technologies are employed.
Basic Level of Technology
The important factor in this operation is the proper placement of pockets which is aided by markings. Also, the stitch appearing on the face of the fabric has an aesthetic look. Therefore, it is important to have it very neat and even. This can be achieved only if the stitching is done with the base fabric on top. But, this creates handling problem if reinforcement fabric is manually fused using double-sided fusing tape.
Juki DDL-9000A and Duerkopp Adler 251-140040 are two most commonly used machines for the purpose.
There are three operational activities in the basic technology which require one operator per operation (a total of 3 operators) as listed below:
Advanced Level of Technology
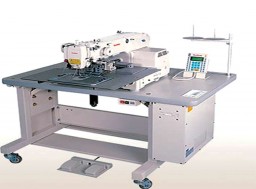
The use of pattern tacking machine for tacking the two panels helps in eliminating a lot of manual operation and errors. It also helps in decreasing the SAM, and thus increasing the productivity.
The new operation sequence becomes:
1. Load both panels on the work clamp
2. Just push the button to start the stitching
3. Reload the tacked panels from the work clamp.
No matter what the size of the pattern is, the clamp can be designed accordingly.
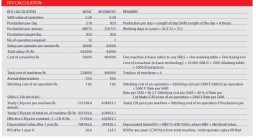
The number of stitches (stitches per inch) and the stitch line, i.e. curves, turns and back tacks, all this information is fed to the machine which is computer programmed and the operator has no hurdles once the machine is set. Even the information can be set by any semi-skilled operator who knows simple English.
There are various machines available in the market which can change (combine and thus simplify) the operation in the desired way. SUNSTAR SPS/A (B)1811/2211 SERIES, Juki AMS 215D and Brother BAS-311 are some of the names. SUNSTAR SPS/A (B)1811/2211 electronic pattern sewing machine has a maximum running speed of 2000 spm at a stitch length of up to 3 mm. It produces lockstitches of size 0.1 mm top 12.7 mm and can lift the stitching frame up to 30 mm. The memory of the machine can be fed with designs via a 1.5” floppy disk (see the Specification Table on the right for more details).